Comprendre le four de fusion à induction par lévitation sous vide
Découvrez les composants d'un four de fusion par induction à lévitation sous vide, notamment le corps du four, la puissance à moyenne fréquence, le système de vide, le système de refroidissement et le système de commande électrique. Découvrez comment chaque élément contribue à l'efficacité et à la précision des processus de fusion des métaux.
Les fours de fusion par induction sous vide (VIM) sont passés du traitement spécialisé des alliages exotiques à une utilisation plus courante dans diverses industries, notamment pour la production d'aciers inoxydables et d'autres métaux. Ces fours fonctionnent sous vide, ce qui permet un contrôle précis du processus de fusion.
Comment fonctionne un four à induction sous vide ?
Le matériau est chargé dans le four à induction sous vide, où la puissance est appliquée pour amorcer la fusion. Des charges supplémentaires sont ajoutées pour obtenir la capacité de fusion souhaitée. Le métal fondu subit un affinage sous vide, avec des ajustements pour obtenir une chimie de fusion précise.
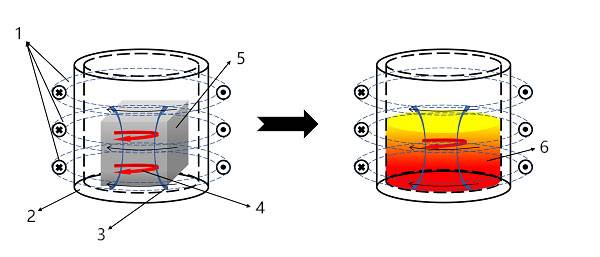
Composants et fonctions clés
Outre le corps du four et le système de vide, un four de fusion par induction sous vide est équipé de composants essentiels tels qu'une alimentation électrique à moyenne fréquence, un système de commande électrique et un système de refroidissement. Ces composants travaillent ensemble pour fournir l'énergie nécessaire à la fusion tout en évitant la surchauffe et en garantissant l'intégrité de la structure.
Des composants auxiliaires tels que des chariots de transmission, des mécanismes de porte de four et des fenêtres d'observation peuvent être ajoutés en fonction des exigences spécifiques du processus. Pour les applications présentant des niveaux élevés d'impuretés, un système de filtrage des gaz est essentiel pour maintenir la pureté du métal.
Avantages des fours de fusion à induction sous vide
La structure compacte des fours VIM, où seule la partie de fusion est enfermée dans la chambre à vide, permet de mieux contrôler les niveaux de vide et d'accélérer les temps d'évacuation. Des caractéristiques telles que l'agitation électromagnétique garantissent un mélange uniforme des éléments ajoutés dans l'ensemble du bain de fusion, ce qui permet de maintenir une température constante.
L'inclusion de chicanes filtrantes et d'autres mesures améliore la pureté du métal en atténuant l'impact des impuretés. La détection et la réparation des fuites de vide sont simplifiées grâce au volume réduit du four, ce qui réduit les temps d'arrêt pour la maintenance.
Précision et contrôle
Les fours de fusion par induction sous vide offrent un contrôle précis de la température grâce à des systèmes de contrôle électrique avancés. Les utilisateurs peuvent surveiller le processus de fusion en temps réel, ce qui garantit la précision et la cohérence. Le système de refroidissement centralisé régule les températures de fusion, améliorant ainsi le contrôle du processus et la qualité du produit.
Applications et flexibilité
Les fours VIM sont disponibles dans une large gamme de tailles, des petites unités adaptées aux expériences à l'échelle du gramme aux modèles plus grands pour la production industrielle. Cette polyvalence permet aux utilisateurs d'ajuster la taille des lots en fonction de leurs besoins spécifiques.
Élimination des gaz et prévention de l'oxydation
L'un des principaux avantages de la fusion par induction sous vide est l'élimination des gaz présents dans les métaux en fusion. Ce processus empêche l'oxydation rapide, garantissant ainsi la pureté et la qualité du produit final.
En conclusion, les fours de fusion par induction sous vide jouent un rôle essentiel dans les processus modernes de fusion des métaux, en offrant un contrôle précis, une pureté accrue et une grande souplesse de production.
Efficacité et flexibilité
Découvrez la gamme de fours à vide disponibles, des petites unités adaptées aux lots de quelques grammes aux fours plus grands pouvant accueillir des lots de différentes tailles. Comprenez comment cette polyvalence permet aux utilisateurs d'optimiser les processus de production.
Automatisation et contrôle avancés :
Nos fours à vide sont équipés de systèmes d'automatisation et de contrôle avancés, qui vous permettent de gérer et de contrôler les processus avec précision. Notre interface conviviale vous permet de programmer et d'ajuster sans effort divers paramètres, garantissant ainsi des performances et une efficacité optimales. Grâce aux données et aux diagnostics en temps réel, vous pouvez prendre des décisions éclairées, détecter les anomalies et optimiser vos processus de production pour un rendement maximal.
Efficacité énergétique et durabilité :
Conceptions sous vide
Les fours à vide pour le traitement à basse température peuvent être discontinus ou continus, autonomes, intégrés dans des systèmes de fours à vide continus ou constituer un "module" distinct incorporé dans un système cellulaire. Par exemple, le fonctionnement de base d'un four à vide discontinu est le suivant :
- Des pompes à vide mécaniques, éventuellement équipées de soufflantes, produisent des niveaux de vide allant jusqu'à 1,3 x 10-3 mbar (0,001 torr) avec 6,7 x 10-3 mbar (0,005 torr) en général. Ce résultat est normalement atteint dans les 10 à 30 minutes suivant le début du cycle, en fonction de la taille des systèmes de pompage et de la nature des contaminants présents dans la charge de travail.
- L'unité est ensuite remplie d'un gaz inerte tel que l'azote, l'argon ou un mélange d'azote et d'hydrogène (3 % maximum), dans une plage de pression négative de 66,7 x 101 mbar (500 torr) à une pression positive de 0,10 bar (1,5 psig), et le chauffage commence.
- Les cycles de pompage doubles sont souvent avantageux pour accélérer la durée totale du cycle. Après avoir atteint le point de consigne et trempé à la température, le cycle de refroidissement est lancé.
Caractéristiques des fours à vide
Les fours à vide KinTek offrent un contrôle précis de la température, une excellente uniformité de la température et une large gamme d'applications pour les laboratoires, les universités et toute application de production à petite échelle utilisant des modèles de fours industriels.
Chaque four à vide standard et personnalisé offre les caractéristiques et avantages suivants :
- Excellente précision et uniformité de la température
- Isolation en fibre céramique à haut rendement énergétique
- Dispositif de sécurité à arrêt automatique
Fours sous vide personnalisés
Obtenez un four sous vide à haute température construit spécifiquement pour répondre aux besoins de votre application. Les représentants expérimentés et compétents de KinTek peuvent vous aider à concevoir ou à construire un four personnalisé pour répondre à vos spécifications exactes ou aux besoins de votre application.
Cette gamme complète de caractéristiques et d'options garantit que nos fours à vide offrent l'efficacité et la flexibilité requises pour une grande variété d'applications de laboratoire et de production à petite échelle.
Contrôle précis de la température
Découvrez comment le système de commande électrique des fours de fusion à induction sous vide assure un contrôle précis de la température tout au long du processus de fusion. Explorez le rôle du système de refroidissement dans le maintien de températures de fusion optimales et la prévention de l'oxydation.
Le chauffage par induction est un processus par lequel des courants de Foucault induits chauffent des matériaux conducteurs. Ce chauffage peut être utilisé pour faire fondre des métaux et fabriquer des alliages. La fusion par induction sous vide offre une combinaison intéressante d'atmosphère contrôlée (vide ou gaz inerte) et de contrôle précis du processus de fusion.
Description du four de frittage sous vide
Un four de frittage sous vide est un type de four dans lequel des articles chauffés subissent un frittage dans un environnement sous vide. Ce four est essentiel dans divers processus industriels, en particulier dans la métallurgie des poudres.
Le processus de frittage est très sensible aux variations de température. Un écart de quelques degrés Celsius seulement peut avoir un impact significatif sur la qualité du produit final. Il est donc impératif de contrôler strictement la température de frittage, les écarts ne dépassant généralement pas une plage spécifiée de ±3℃ à ±5℃.
Avantages de l'équipement d'induction sous vide
Par rapport aux méthodes de fusion traditionnelles, l'équipement d'induction sous vide offre des avantages substantiels en matière de contrôle des processus. Grâce aux progrès de la technologie informatique, les fours à induction sous vide modernes intègrent des systèmes de contrôle intelligents qui rationalisent les opérations, réduisent les coûts de main-d'œuvre et améliorent la précision.
Les développements futurs des systèmes de contrôle intelligents amélioreront encore les capacités de l'équipement d'induction sous vide. Ces systèmes permettront un contrôle précis des températures de fusion, faciliteront l'ajout automatisé d'alliages à des intervalles prédéterminés et rationaliseront l'ensemble du processus de fusion. En outre, l'intégration de la collecte de données complètes et de l'analyse en temps réel permettra aux opérateurs de prendre des décisions éclairées et d'optimiser les paramètres du processus pendant la fusion.
Composants du four de fusion à induction sous vide
Le four de fusion par induction sous vide comprend plusieurs composants essentiels, notamment
- Corps du four à vide: Fournit la chambre où la fusion se produit dans des conditions de vide ou d'atmosphère contrôlée.
- Puissance à moyenne fréquence: Fournit l'énergie nécessaire au chauffage par induction.
- Système de vide: Maintient le niveau de vide souhaité dans la chambre du four.
- Système de refroidissement: Empêche la surchauffe et maintient des températures de fusion optimales.
- Système de commande électrique: Permet un contrôle précis de la température et du fonctionnement général du four.
Principales caractéristiques et avantages
- Contrôle précis de la température: Le système de contrôle électrique assure une régulation précise des températures de fusion, améliorant ainsi la qualité et la cohérence du produit final.
- Élimination des gaz: L'environnement sous vide élimine les gaz des métaux fondus, empêchant une oxydation rapide et préservant l'intégrité de l'alliage.
- Tailles de lots flexibles: Les fours à vide sont disponibles en différentes tailles, s'adaptant à une gamme de tailles de lots allant de la petite échelle aux applications industrielles plus importantes.
- Système de refroidissement centralisé: Le système de refroidissement dissipe efficacement la chaleur, ce qui permet de maintenir des températures de fonctionnement stables et de prolonger la durée de vie de l'équipement.
En conclusion, les fours de fusion par induction sous vide offrent une précision et un contrôle inégalés dans les processus de fusion des métaux. En s'appuyant sur des technologies de pointe et des systèmes de contrôle intelligents, ces fours facilitent une production efficace, garantissent la qualité des produits et ouvrent la voie à de futures avancées dans le domaine du traitement métallurgique.
Principe de fonctionnement et importance historique
Découvrez les racines historiques de la technologie de fusion par induction sous vide, en remontant jusqu'aux industries aérospatiale et métallurgique. Découvrez comment cette technologie a évolué pour devenir une pierre angulaire de la production d'alliages à hautes performances pour diverses applications.
La fusion par induction sous vide : Une voie vers les matériaux avancés
La fusion par induction sous vide (FIV) est une technologie essentielle dans le domaine de la métallurgie, en particulier pour la production d'alliages spécialisés et exotiques. Initialement développé pour le traitement des superalliages, son spectre d'application s'est élargi pour englober les aciers inoxydables et divers autres métaux. Cette expansion est due en grande partie à l'escalade de la demande de matériaux avancés dans diverses industries.
Le processus de fusion par induction sous vide
Au cœur du procédé VIM se trouve le principe de la fusion des métaux sous vide, l'induction électromagnétique servant de source d'énergie principale. Le processus implique la génération de courants de Foucault électriques dans le métal, facilitée par une bobine d'induction transportant un courant alternatif. Ces courants induisent à leur tour des effets de chauffage, qui aboutissent finalement à la fusion de la charge métallique.
L'évolution rapide de la technologie VIM trouve ses racines dans la quête de l'industrie aérospatiale pour des matériaux d'alliage à haute température. Ces matériaux, essentiels pour les équipements de l'aérospatiale, des missiles, des fusées et de l'énergie atomique, ont nécessité des innovations dans les processus de fusion. Les fours VIM sont apparus comme une solution, permettant la fusion d'alliages à base de nickel, de fer et de cobalt dans des conditions de vide. Cet environnement réduit efficacement la présence d'éléments d'interstice tels que O2, N2 et H2, garantissant l'élimination des inclusions non métalliques et des impuretés nocives telles que Pb, Bi, Sb, Cu, Sn et Te.
Applications de la fusion par induction sous vide
La polyvalence de la FIV s'étend à diverses applications dans le paysage métallurgique :
- Affinage de métaux et d'alliages de haute pureté.
- Production d'électrodes pour les processus de refonte.
- Fabrication de bâtonnets d'alliages maîtres, essentiels dans des procédures telles que le moulage à la cire perdue.
- Moulage de composants critiques pour les moteurs d'avion.
Évolution historique
La genèse de la fusion par induction sous vide remonte à 1920, lorsque le premier prototype a vu le jour. Par essence, la fusion par induction sous vide exploite l'induction électromagnétique pour induire des courants de Foucault dans les conducteurs, ce qui permet de chauffer et de faire fondre le métal. Au fil des décennies, cette technologie a trouvé une utilité indispensable dans les secteurs de l'aérospatiale et du nucléaire, entraînant des progrès dans la science et l'ingénierie des matériaux.
En résumé, la fusion par induction sous vide témoigne de l'ingéniosité humaine, facilitant la production de matériaux qui alimentent les merveilles technologiques modernes. De ses origines modestes à son statut actuel de pierre angulaire de l'innovation métallurgique, la FIV continue de façonner le paysage de la fabrication de matériaux avancés.
Applications dans tous les secteurs
Explorez le large éventail d'applications de la technologie de fusion par induction sous vide dans l'aérospatiale, l'électronique, l'énergie, etc. Comprenez comment cette technologie améliore les propriétés et la qualité des matériaux essentiels à l'ingénierie et à la fabrication de pointe.
La technologie de fusion par induction sous vide (VIM) a considérablement évolué. Développée à l'origine pour le traitement d'alliages spécialisés et exotiques, elle est aujourd'hui de plus en plus répandue, car les matériaux avancés trouvent des applications plus larges. Utilisée à l'origine pour des matériaux tels que les superalliages, la technologie VIM a élargi son champ d'application aux aciers inoxydables et à divers autres métaux.
Le développement rapide de la technologie VIM est étroitement lié à la demande de matériaux d'alliage à haute température dans des industries telles que l'aérospatiale, les missiles, les fusées et les équipements d'énergie atomique. Les superalliages, essentiels pour ces applications, bénéficient grandement des capacités des fours VIM.
Fonctionnement des fours à induction sous vide
Dans un four à induction sous vide, le matériau est chargé sous vide et la puissance est appliquée pour faire fondre la charge. Des charges supplémentaires sont effectuées pour atteindre la capacité de fusion souhaitée, et le métal fondu est affiné sous vide. Ce processus permet un ajustement précis de la chimie de la fusion jusqu'à l'obtention de la composition souhaitée.
Avantages de la fusion par induction sous vide
-
Pureté et qualité élevées : La FIV excelle dans la production de matériaux de haute pureté et de haute qualité. L'environnement sous vide élimine le risque de contamination par l'oxygène, l'azote et les autres gaz présents dans l'atmosphère. Il en résulte une fusion plus propre et plus homogène, dépourvue d'inclusions et d'impuretés nocives susceptibles de compromettre les propriétés mécaniques.
-
Atmosphère contrôlée : Dans la chambre à vide, l'atmosphère est étroitement contrôlée, seuls des gaz spécifiques étant introduits à des pressions précises. Ce niveau de contrôle permet une gestion précise de la composition chimique du matériau fondu et empêche toute oxydation ou réaction indésirable avec les gaz ambiants.
Les fours de fusion par induction sous vide sont essentiels dans le domaine de la métallurgie sous vide, car ils jouent un rôle important dans la production d'alliages et d'aciers spéciaux essentiels pour l'aérospatiale, les missiles, les fusées, les équipements d'énergie atomique et l'industrie électronique. Notamment, une proportion considérable de produits dans ces secteurs est fabriquée à l'aide de la technologie VIM.
Divers matériaux, dont l'acier inoxydable, l'acier résistant à la chaleur, l'acier à très haute résistance, l'acier à outils, l'acier à roulements, les matériaux magnétiques, les alliages élastiques et les alliages d'expansion, sont fondus dans des fours de fusion à induction sous vide afin de garantir des performances et une qualité optimales. Ces fours améliorent l'aptitude au travail à chaud et les propriétés mécaniques des superalliages à base de nickel, de cobalt et de fer, ce qui les rend indispensables dans les processus d'ingénierie et de fabrication de pointe.
Avantages par rapport aux méthodes traditionnelles
La technologie de fusion par induction sous vide s'impose comme une méthode de premier plan pour la fusion des métaux en raison des nombreux avantages qu'elle présente par rapport aux approches traditionnelles. En comparant son efficacité, sa durabilité et la pureté de ses matériaux avec les méthodes conventionnelles, on comprend pourquoi la fusion par induction sous vide est de plus en plus prisée dans diverses industries.
Efficacité énergétique et durabilité environnementale
La technologie de fusion par induction sous vide (VIM) représente une avancée significative en termes d'efficacité énergétique et de durabilité environnementale par rapport aux méthodes de fusion traditionnelles. Contrairement aux approches conventionnelles, la fusion par induction sous vide fonctionne dans un environnement sous vide, ce qui minimise les pertes de chaleur et réduit la consommation d'énergie. Cette utilisation efficace de l'énergie permet non seulement de réduire les coûts de production, mais contribue également à un processus de fabrication plus écologique en réduisant les émissions de carbone et le gaspillage d'énergie.
Pureté et qualité des matériaux
L'un des principaux avantages du VIM est sa capacité à produire des matériaux d'une pureté et d'une qualité exceptionnelles. L'environnement sous vide élimine la présence d'oxygène, d'azote et d'autres gaz susceptibles de contaminer le métal en fusion. Par conséquent, le VIM produit des fusions plus propres et plus homogènes, dépourvues d'impuretés et d'inclusions nocives. Cette pureté améliore les propriétés mécaniques et les performances globales des matériaux obtenus, ce qui les rend très intéressants pour diverses applications.
Atmosphère contrôlée
Dans la chambre à vide de l'équipement VIM, l'atmosphère est méticuleusement contrôlée, ce qui permet une régulation précise de la composition et de la pression des gaz. En n'introduisant que des gaz spécifiques à des pressions précises, VIM assure un contrôle étroit de la composition chimique du matériau fondu, minimisant ainsi le risque d'oxydation ou de réactions indésirables avec les gaz ambiants. Ce niveau de contrôle est essentiel pour produire des alliages aux propriétés constantes et minimiser les pertes de matière.
Efficacité et flexibilité des procédés
Au-delà de ses avantages en termes d'environnement et de qualité, le VIM offre une efficacité et une flexibilité de procédé inégalées. Ses cycles de chauffage rapides et le chauffage uniforme des charges métalliques augmentent considérablement les taux de production tout en réduisant les taux de défauts. En outre, la polyvalence du VIM permet de fondre facilement divers métaux et alliages, ce qui facilite le passage rapide d'un matériau à l'autre et permet un arrêt immédiat en cas de besoin. Cette souplesse de production améliore l'efficacité opérationnelle et l'adaptabilité à l'évolution des exigences de fabrication.
Applications et perspectives d'avenir
L'adoption généralisée de la technologie de fusion par induction sous vide dans toutes les industries souligne son immense potentiel et sa polyvalence. De la recherche expérimentale à petite échelle à la production industrielle à grande échelle, le VIM a prouvé son efficacité et sa fiabilité. Son fonctionnement simple et ses températures de fusion rapides en font un choix privilégié pour les fabricants qui recherchent la précision et la cohérence dans leurs processus de production. Au fur et à mesure que la technologie progresse, l'application du VIM devrait encore s'étendre, favorisant l'innovation et l'efficacité dans les processus de fusion et d'affinage des métaux.
Frittage sous vide : Améliorer l'efficacité et la qualité
Outre la fusion par induction sous vide, le frittage sous vide apparaît comme un autre procédé essentiel pour améliorer l'efficacité et la qualité des produits dans la fabrication des métaux. En frittant des poudres métalliques à des températures inférieures au point de fusion dans un environnement sous vide, le frittage sous vide offre plusieurs avantages. Il élimine les réactions entre les métaux et les gaz, améliore la densification et réduit les températures de frittage, ce qui permet d'économiser de l'énergie et de prolonger la durée de vie des fours de frittage. Le résultat est la production de produits métalliques de haute qualité avec des propriétés mécaniques améliorées et une consommation d'énergie réduite.
En conclusion, la fusion par induction sous vide et le frittage sous vide sont des technologies de pointe qui offrent de nombreux avantages par rapport aux méthodes de fusion traditionnelles. Qu'il s'agisse de l'efficacité énergétique, de la pureté des matériaux, de la flexibilité des processus ou de la durabilité environnementale, ces techniques avancées stimulent l'innovation et redessinent le paysage de la fabrication des métaux. Alors que les industries continuent de donner la priorité à la durabilité et à la qualité, l'adoption de procédés basés sur le vide tels que la fusion par induction sous vide et le frittage sous vide devrait s'accélérer, ouvrant la voie à une nouvelle ère d'efficacité et d'excellence dans la production de métaux.
Principales caractéristiques des fours de fusion à induction sous vide
Les fours de fusion par induction sous vide jouent un rôle essentiel dans les processus métallurgiques, car ils offrent un éventail de caractéristiques adaptées à un contrôle précis et à une productivité accrue. Voici une exploration complète de leurs composants clés et de leurs avancées :
Composants structurels
Le four est constitué d'une enveloppe en acier étanche refroidie à l'eau, conçue pour maintenir les conditions de vide requises pendant le traitement. Dans cette enceinte, le métal est fondu dans un creuset niché dans une bobine d'induction refroidie à l'eau. En outre, l'intérieur du four est généralement revêtu de réfractaires capables de résister à des températures extrêmes.
Améliorations du processus
1. Contrôle environnemental
- La coulée de métal en fusion peut être réalisée sous vide ou sous gaz inerte, ce qui garantit des conditions optimales pour la formation d'alliages et le maintien de la pureté.
2. Caractéristiques supplémentaires
- Les fours peuvent intégrer des mécanismes d'inclinaison et de coulée, des chambres de coulée et des orifices d'échantillonnage pour répondre à des besoins de production variés.
- Les installations de manutention des moules permettent un traitement automatisé ou semi-automatisé, et intègrent parfois des systèmes de verrouillage du vide pour un fonctionnement sans faille.
Tendances futures du développement
L'évolution de l'équipement de fusion par induction sous vide reflète une transition vers des structures multifonctionnelles capables de s'adapter à divers processus technologiques. Les configurations modulaires devraient dominer, permettant des combinaisons personnalisées de composants pour répondre efficacement aux exigences de processus spécifiques.
Contrôle de précision et automatisation
L'intégration de technologies avancées telles que les systèmes informatiques et l'acquisition intelligente de signaux permet un contrôle précis des processus. Des interfaces homme-machine conviviales rationalisent les opérations, réduisant les coûts de main-d'œuvre et améliorant la simplicité opérationnelle.
Systèmes auxiliaires
Outre les composants de base, les systèmes auxiliaires tels que les alimentations électriques, les unités de contrôle et les systèmes de refroidissement jouent un rôle essentiel. Ces systèmes garantissent l'apport d'énergie pour la fusion et empêchent la surchauffe des composants critiques.
Considérations structurelles
L'attention portée à la conception des structures est primordiale pour éviter les décharges de vide. L'isolation de tous les corps chargés à l'intérieur de la coquille du four et l'élimination des arêtes vives dans la conception de l'inducteur sont essentielles pour garantir un fonctionnement ininterrompu.
Principaux avantages
- Fusion de certains alliages de titane : Les conditions de vide permettent la fusion d'alliages de titane, ce qui élargit les possibilités d'application du four.
- Prévention des réactions chimiques : Les environnements sous vide protègent les métaux et les alliages fondus des réactions chimiques indésirables avec les inclusions non métalliques.
- Élimination des gaz nocifs : L'état de vide facilite l'élimination des gaz dissous nocifs et des polluants du métal liquide en fusion, ce qui garantit la pureté du matériau.
En conclusion, les fours de fusion par induction sous vide incarnent la polyvalence et la précision, et font progresser les procédés métallurgiques grâce à une conception innovante et à l'intégration technologique.
Avantages pour l'environnement et les performances
La fusion par induction sous vide (FIV) offre des avantages significatifs en termes d'environnement et de performances, ce qui en fait une méthode privilégiée pour la production de matériaux de haute pureté aux propriétés supérieures.
Pureté et qualité élevées
La FIV excelle dans la production de matériaux d'une pureté et d'une qualité exceptionnelles. En opérant dans un environnement sous vide, le VIM élimine le risque de contamination par les gaz atmosphériques tels que l'oxygène et l'azote. Cela garantit une fusion plus propre et plus homogène, dépourvue d'inclusions et d'impuretés nuisibles qui pourraient compromettre l'intégrité mécanique du matériau. Par conséquent, les alliages obtenus présentent des propriétés mécaniques et des caractéristiques de performance améliorées.
Atmosphère contrôlée
Dans la chambre à vide, l'atmosphère est méticuleusement contrôlée, ce qui permet une régulation précise de la composition et de la pression des gaz. Ce niveau de contrôle est primordial pour obtenir la composition chimique souhaitée du matériau fondu tout en évitant une oxydation ou des réactions indésirables avec les gaz ambiants. Le VIM permet donc de produire des matériaux aux propriétés chimiques constantes et à la réactivité minimale, ce qui garantit des performances supérieures dans diverses applications.
Résumé des avantages
Les avantages de l'utilisation d'un four de fusion par induction sous vide sont multiples :
-
Élimination des gaz : Le VIM fonctionne sous des pressions extrêmement basses, généralement autour de 0,000001 atmosphère. Cet environnement facilite l'élimination des gaz indésirables et des éléments volatils des matières premières au cours du processus de fusion, ce qui garantit la production d'alliages d'une grande pureté.
-
Analyse chimique précise : L'absence d'atmosphère dans la chambre à vide permet un contrôle exceptionnel et reproductible de la composition chimique des matériaux fondus. Cette précision permet de produire des alliages avec des compositions sur mesure et des propriétés souhaitées, ce qui améliore l'efficacité globale du processus et la qualité du produit.
-
Contrôle supérieur du processus : Le VIM offre un contrôle indépendant de la pression, de la température et de l'agitation inductive, ce qui permet un contrôle inégalé du processus. Cette flexibilité permet de développer des pratiques de fusion optimisées spécifiques à chaque composition d'alliage, ce qui améliore encore les performances et la cohérence des matériaux produits.
Outre les avantages environnementaux, les avantages d'un four à induction sous vide s'étendent au traitement de divers métaux et alliages :
- Amélioration de la pureté : L'absence de pollution de l'air et des scories dans les fours à induction sous vide contribue à la production d'alliages relativement purs avec des niveaux de performance élevés.
- Élimination des gaz : Le fonctionnement sous vide permet de réduire la teneur en gaz de l'acier et des alliages fondus, ce qui permet d'obtenir des matériaux présentant des concentrations de gaz plus faibles et des propriétés améliorées.
- Prévention de l'oxydation : Le traitement des métaux dans un environnement sous vide réduit le risque d'oxydation, préservant ainsi l'intégrité du matériau traité.
- Évaporation des impuretés : Les impuretés telles que le plomb (Pb) et le bismuth (Bi) peuvent s'évaporer plus facilement dans un environnement sous vide, ce qui facilite la purification du matériau au cours du processus de fusion.
En conclusion,les fours de fusion par induction sous vide offrent une solution complète pour la production de matériaux de haute pureté présentant des caractéristiques de performance supérieures, tout en atténuant la pollution de l'environnement et en garantissant l'efficacité du processus.
CONTACTEZ-NOUS POUR UNE CONSULTATION GRATUITE
Les produits et services de KINTEK LAB SOLUTION ont été reconnus par des clients du monde entier. Notre personnel se fera un plaisir de répondre à toute demande que vous pourriez avoir. Contactez-nous pour une consultation gratuite et parlez à un spécialiste produit pour trouver la solution la plus adaptée aux besoins de votre application !