Le procédé de trempe, bien qu'essentiel pour améliorer les propriétés mécaniques des métaux, présente plusieurs inconvénients. Ceux-ci incluent le potentiel d’une dureté et d’une résistance à l’usure réduites, une fragilité accrue si elle n’est pas correctement contrôlée et le risque de distorsion ou de fissuration due aux contraintes thermiques. De plus, la trempe nécessite un contrôle précis de la température et peut prendre du temps, ce qui la rend moins efficace pour une production en grand volume. Le processus peut également introduire une oxydation ou une décarburation de la surface, affectant la qualité de la surface du matériau. Malgré ces inconvénients, le revenu reste une étape cruciale pour atteindre l’équilibre souhaité entre dureté et ténacité dans de nombreuses applications industrielles.
Points clés expliqués :
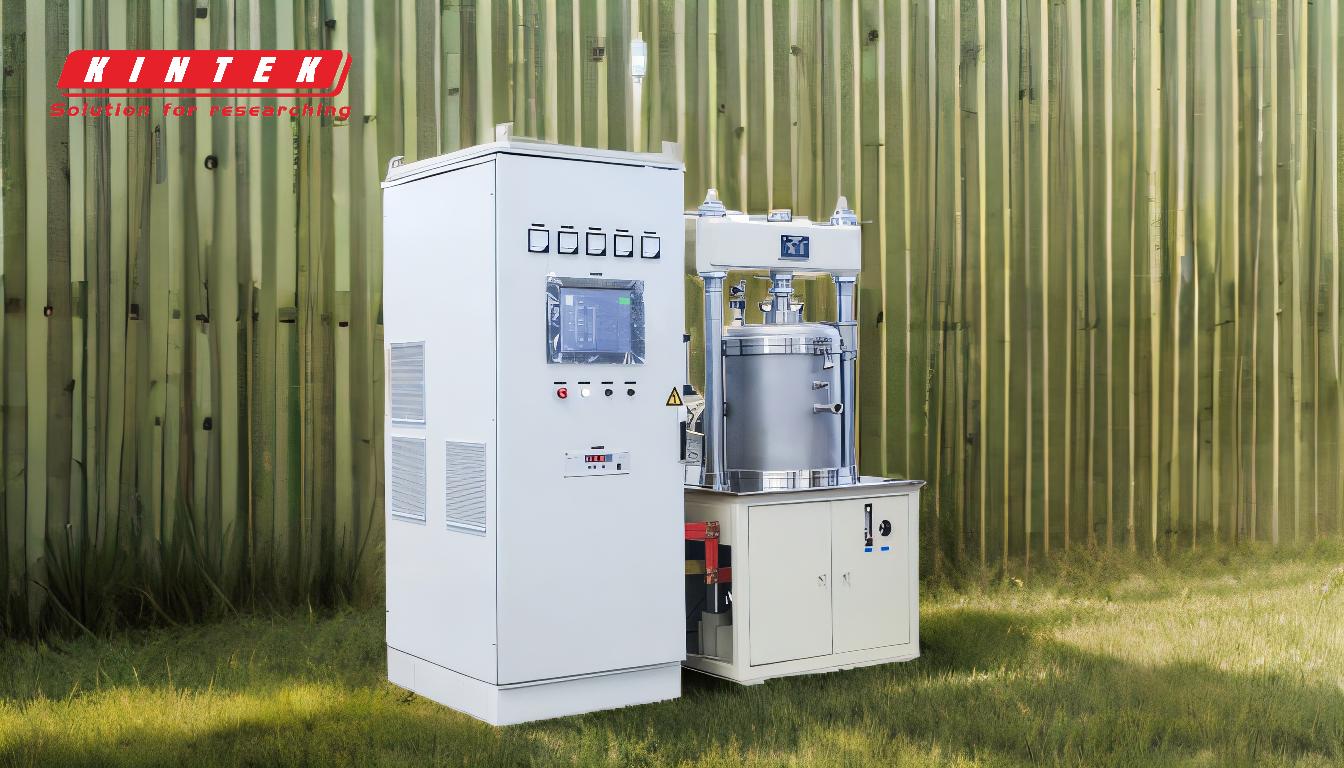
-
Réduction de la dureté et de la résistance à l'usure
- La trempe consiste à chauffer le métal à une température spécifique inférieure à son point critique, puis à le refroidir. Ce processus réduit la dureté obtenue lors de la trempe, à mesure que la microstructure passe de la martensite à la martensite revenue ou à d'autres phases plus molles.
- Bien que cette réduction de la dureté améliore la ténacité, elle peut constituer un inconvénient pour les applications nécessitant une résistance à l'usure ou une dureté de surface élevée.
-
Risque de fragilité accrue
- Si la trempe n’est pas effectuée à la bonne température ou pendant la durée appropriée, le matériau peut devenir trop cassant. Ceci est particulièrement problématique pour les aciers à haute teneur en carbone, où un revenu inapproprié peut conduire à une défaillance catastrophique sous contrainte.
- La fragilité peut également résulter de la fragilisation par revenu, un phénomène qui se produit lorsque certains aciers sont trempés dans des plages de températures spécifiques, entraînant une résistance aux chocs réduite.
-
Contraintes thermiques et distorsion
- Le processus de trempe implique des cycles de chauffage et de refroidissement, qui peuvent introduire des contraintes thermiques dans le matériau. Ces contraintes peuvent provoquer des déformations, des déformations, voire des fissures, notamment dans les géométries complexes ou les sections minces.
- La distorsion peut entraîner des imprécisions dimensionnelles, nécessitant un usinage supplémentaire ou des mesures correctives, ce qui augmente les coûts de production.
-
Oxydation de surface et décarburation
- Pendant le revenu, l’exposition à l’air à des températures élevées peut provoquer une oxydation de la surface, entraînant la formation de tartre ou une décoloration. Cela affecte la finition de surface du matériau et peut nécessiter un post-traitement pour restaurer l'apparence souhaitée.
- La décarburation, c'est-à-dire la perte de carbone de la couche superficielle, peut également se produire, réduisant la dureté et la résistance du matériau près de la surface. Ceci est particulièrement préjudiciable pour les composants soumis à des contraintes superficielles.
-
Exigences de précision et de temps
- La trempe nécessite un contrôle précis de la température et du temps pour obtenir les propriétés mécaniques souhaitées. Les variations de ces paramètres peuvent conduire à des résultats incohérents, affectant les performances du produit final.
- Le processus peut prendre du temps, en particulier pour les composants volumineux ou épais, car il faut suffisamment de temps pour que la chaleur pénètre uniformément. Cela peut réduire l’efficacité de la production et augmenter les coûts.
-
Applicabilité limitée pour la production en grand volume
- En raison du temps et de la précision requis, la trempe peut ne pas convenir aux processus de fabrication à grand volume où la vitesse et l'efficacité sont essentielles. Des méthodes alternatives de traitement thermique, telles que le durcissement par induction, peuvent être préférées dans de tels cas.
-
Considérations environnementales et énergétiques
- La trempe implique une consommation d’énergie importante, notamment pour les opérations à grande échelle. Cela peut entraîner des coûts opérationnels plus élevés et une empreinte environnementale plus importante.
- Des mesures de ventilation et de sécurité appropriées sont également nécessaires pour gérer la chaleur et les fumées générées pendant le processus, ce qui ajoute à la complexité et au coût de mise en œuvre.
-
Limites spécifiques au matériau
- Tous les matériaux ne réagissent pas bien au revenu. Par exemple, certains aciers inoxydables et alliages non ferreux peuvent ne pas bénéficier de manière significative du revenu, ou le processus peut introduire des propriétés indésirables.
- L'efficacité du revenu dépend également du traitement thermique initial (par exemple, trempe) et de la composition de l'alliage, ce qui le rend moins polyvalent pour certaines applications.
En résumé, bien que la trempe soit un processus précieux pour améliorer les propriétés mécaniques des métaux, elle présente plusieurs inconvénients, notamment une dureté, une fragilité, une distorsion et une dégradation de surface réduites. Ces défis doivent être soigneusement gérés pour garantir les performances et la qualité souhaitées du produit final.
Tableau récapitulatif :
Inconvénient | Description |
---|---|
Dureté et résistance à l'usure réduites | La trempe réduit la dureté, ce qui a un impact sur la résistance à l'usure et la dureté de la surface. |
Risque de fragilité accrue | Un revenu inapproprié peut conduire à une fragilité et à une défaillance catastrophique. |
Contraintes thermiques et distorsion | Les cycles de chauffage et de refroidissement peuvent provoquer une déformation, une déformation ou des fissures. |
Oxydation de surface et décarburation | L'exposition à l'air peut provoquer une oxydation et une perte de carbone, affectant la qualité de la surface. |
Exigences de précision et de temps | Nécessite un contrôle précis de la température et peut prendre beaucoup de temps. |
Applicabilité limitée à haut volume | Moins efficace pour la production en grand volume en raison des besoins de temps et de précision. |
Préoccupations environnementales et énergétiques | Consommation d’énergie élevée et impact environnemental dans les opérations à grande échelle. |
Limites spécifiques au matériau | Tous les matériaux ne bénéficient pas du revenu et l'efficacité varie selon l'alliage. |
Besoin d’aide pour optimiser votre processus de trempe ? Contactez nos experts dès aujourd'hui pour des solutions sur mesure !