La cémentation est un processus de traitement thermique qui améliore la dureté de surface de l'acier à faible teneur en carbone en introduisant des atomes de carbone supplémentaires dans ses couches superficielles et souterraines. Ce processus améliore la résistance à l'usure, la résistance à la fatigue et les propriétés mécaniques globales tout en conservant un noyau souple et ductile. Cependant, il présente également des limites, telles qu'une distorsion potentielle, une consommation d'énergie élevée et la nécessité d'un contrôle précis du processus. Ci-dessous, nous explorons en détail les avantages et les inconvénients de la carburation, en tenant compte de ses applications, des variations de processus et des défis opérationnels.
Points clés expliqués :
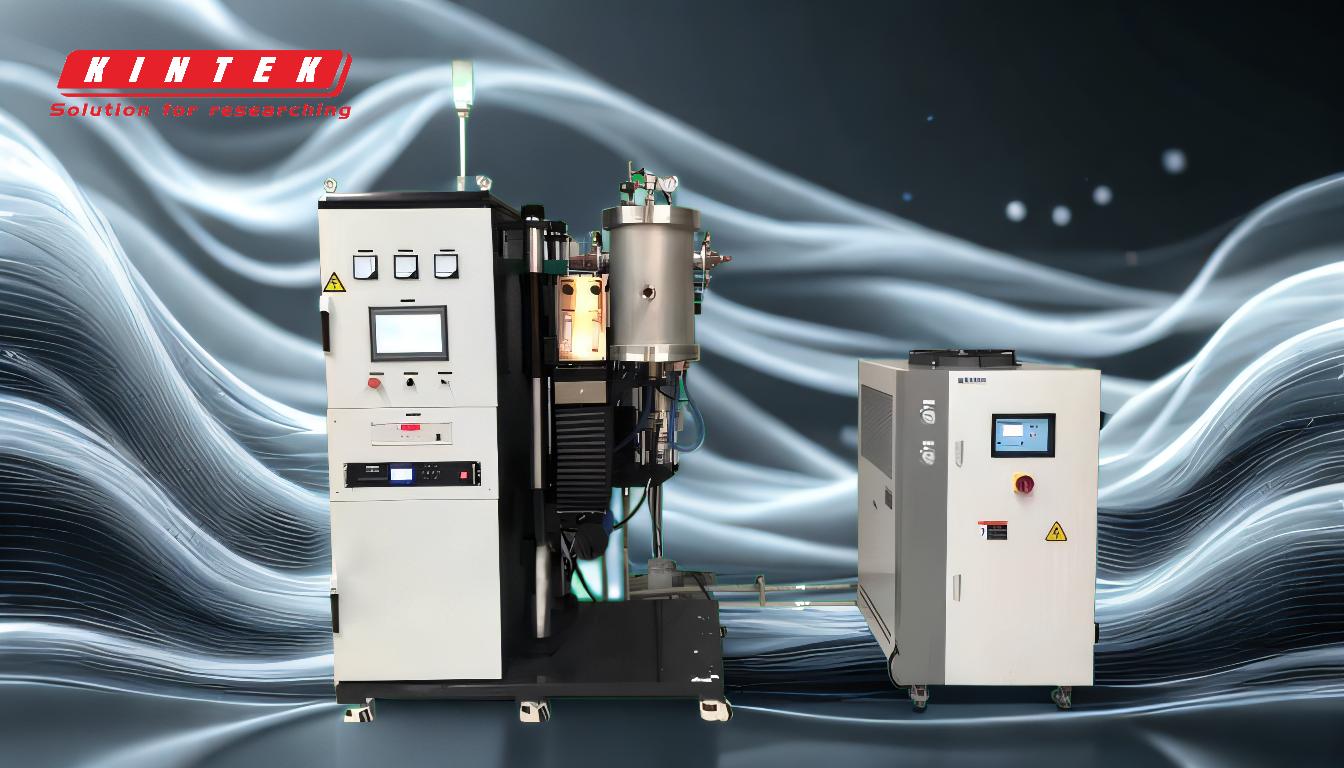
-
Avantages de la carburation
-
Dureté de surface accrue:
La cémentation améliore considérablement la dureté de surface de l'acier à faible teneur en carbone, ce qui le rend adapté aux applications nécessitant une résistance élevée à l'usure. Le processus diffuse du carbone dans la surface de l'acier, créant une couche durcie tout en conservant un noyau plus souple et plus ductile. -
Résistance à l'usure améliorée:
La couche de surface durcie résiste à l'abrasion et à l'usure, prolongeant ainsi la durée de vie des composants soumis au frottement et aux contraintes mécaniques. -
Résistance à la fatigue améliorée:
La cémentation améliore la résistance à la fatigue des pièces en acier, leur permettant de résister aux charges et contraintes cycliques sans rupture. -
Polyvalence dans l'application:
Le processus peut être appliqué à des pièces entières ou à des zones spécifiques en masquant les zones non durcies avec une peinture anti-carbone. Cette flexibilité le rend adapté aux géométries complexes et au durcissement sélectif. -
Rentable pour la production en grand volume:
La cémentation sous atmosphère, en particulier, offre un faible investissement initial en capital et une capacité de production de gros volumes, ce qui la rend économique pour la fabrication à grande échelle. -
Automatisation et contrôle des processus:
Les méthodes de cémentation modernes, telles que la cémentation sous vide, permettent une automatisation complète, un contrôle précis du processus et des ajustements flexibles du cycle, améliorant ainsi l'efficacité et la cohérence.
-
Dureté de surface accrue:
-
Inconvénients de la carburation
-
Potentiel de distorsion:
Les températures élevées impliquées dans la cémentation peuvent provoquer des changements dimensionnels et des déformations dans les pièces traitées, nécessitant des processus de finition supplémentaires. -
Consommation d'énergie:
La cémentation est gourmande en énergie, en particulier dans la cémentation sous atmosphère, où les fours fonctionnent en continu à des températures élevées. -
Complexité du processus:
L’obtention de résultats cohérents nécessite un contrôle précis de la température, de la concentration en carbone et du temps de diffusion. Tout écart peut entraîner un durcissement inégal ou une pénétration insuffisante du carbone. -
Limité aux aciers à faible teneur en carbone:
La carburation est principalement efficace pour les aciers à faible teneur en carbone. Les aciers ou alliages à haute teneur en carbone peuvent ne pas bénéficier autant du processus. -
Préoccupations environnementales:
La cémentation atmosphérique implique l'utilisation de gaz riches en carbone, qui peuvent présenter des risques pour l'environnement et la sécurité s'ils ne sont pas correctement gérés. -
Coût des méthodes avancées:
Bien que la cémentation sous vide offre un contrôle et une flexibilité supérieurs, elle implique des coûts d'équipement et d'exploitation plus élevés que les méthodes traditionnelles.
-
Potentiel de distorsion:
-
Comparaison des méthodes de carburation
-
Carburation en atmosphère:
- Avantages : Faible investissement initial, capacité de volume élevé et connaissance bien établie des processus.
- Inconvénients : consommation d'énergie plus élevée, risque potentiel pour l'environnement et contrôle moins précis par rapport à la cémentation sous vide.
-
Cémentation sous vide:
- Avantages : Contrôle précis du processus, efficacité énergétique (consommation uniquement en cas de besoin) et compatibilité avec des températures plus élevées et des cycles flexibles.
- Inconvénients : coûts d’équipement et complexité plus élevés, ce qui le rend moins adapté aux opérations à petite échelle.
-
Carburation en atmosphère:
-
Applications de la cémentation
-
Industrie automobile:
Utilisé pour les engrenages, les arbres et autres composants nécessitant une résistance élevée à l’usure et à la fatigue. -
Industrie aérospatiale:
Critique pour les pièces soumises à des contraintes mécaniques et à l’abrasion extrêmes. -
Fabrication d'outils:
Améliore la durabilité des outils de coupe et des matrices. -
Machines industrielles:
Améliore les performances des composants tels que les roulements, les rouleaux et les arbres à cames.
-
Industrie automobile:
-
Considérations pour les acheteurs d’équipements et de consommables
-
Exigences du processus:
Évaluez si la cémentation sous atmosphère ou sous vide correspond mieux au volume de production, à la complexité des pièces et aux contraintes budgétaires. -
Efficacité énergétique:
Tenez compte des coûts énergétiques à long terme et de l’impact environnemental de la méthode choisie. -
Besoins d'automatisation:
Pour une production en grand volume, donnez la priorité aux systèmes dotés de capacités d’automatisation complètes pour garantir la cohérence et réduire les coûts de main-d’œuvre. -
Entretien et dépannage:
Choisissez des équipements dotés de dispositifs de contrôle fiables et d’un support de dépannage établi pour minimiser les temps d’arrêt. -
Compatibilité des matériaux:
Assurez-vous que le processus de cémentation est adapté aux nuances d'acier spécifiques utilisées dans vos applications.
-
Exigences du processus:
En résumé, la cémentation est une méthode très efficace pour améliorer les propriétés de surface de l'acier à faible teneur en carbone, offrant des avantages significatifs en termes de dureté, de résistance à l'usure et de résistance à la fatigue. Cependant, cela présente également des défis tels qu'une distorsion potentielle, une consommation d'énergie élevée et une complexité de processus. En sélectionnant soigneusement la méthode et l'équipement de carburation appropriés, les fabricants peuvent optimiser le processus pour répondre à leurs besoins spécifiques tout en minimisant les inconvénients.
Tableau récapitulatif :
Aspect | Avantages | Inconvénients |
---|---|---|
Dureté superficielle | Améliore la dureté de la surface pour la résistance à l'usure | Distorsion potentielle due aux températures élevées |
Résistance à l'usure | Prolonge la durée de vie des composants sous friction et contrainte | Consommation d'énergie élevée, notamment en cémentation atmosphérique |
Résistance à la fatigue | Améliore la résistance aux charges cycliques et aux contraintes | Nécessite un contrôle précis de la température, de la concentration en carbone et du temps de diffusion |
Versatilité | Convient aux géométries complexes et au durcissement sélectif | Limité aux aciers à faible teneur en carbone |
Rentabilité | Économique pour une production en grand volume avec un faible investissement initial | Préoccupations environnementales liées aux gaz riches en carbone |
Contrôle des processus | Automatisation et contrôle précis dans les méthodes modernes comme la cémentation sous vide | Coûts d’équipement plus élevés pour les méthodes avancées |
Optimisez votre processus de carburation pour des résultats supérieurs : contactez nos experts dès aujourd'hui !