Le recuit à l'hydrogène est un processus de traitement thermique spécialisé effectué dans une atmosphère d'hydrogène contrôlée afin d'obtenir des propriétés matérielles spécifiques, telles que la réduction des contraintes, le nettoyage de la surface et la prévention de l'oxydation.Ce processus est particulièrement bénéfique pour les matériaux tels que l'acier, les alliages durs, les matériaux céramiques et les métaux réfractaires rares.Le recuit à l'hydrogène est souvent appelé "recuit brillant" en raison de sa capacité à produire une finition de surface brillante et propre en réduisant les oxydes sur le matériau.Des précautions sont toutefois nécessaires pour éviter la décarburation des pièces en acier.Le processus est généralement réalisé à des températures élevées, souvent entre 200 et 300°C, et peut être plus efficace en raison du coefficient de transfert thermique plus élevé de l'hydrogène par rapport à d'autres gaz.Si le recuit à l'hydrogène est efficace, il est aussi plus coûteux, ce qui fait des mélanges azote-hydrogène une alternative rentable dans certains cas.
Explication des points clés :
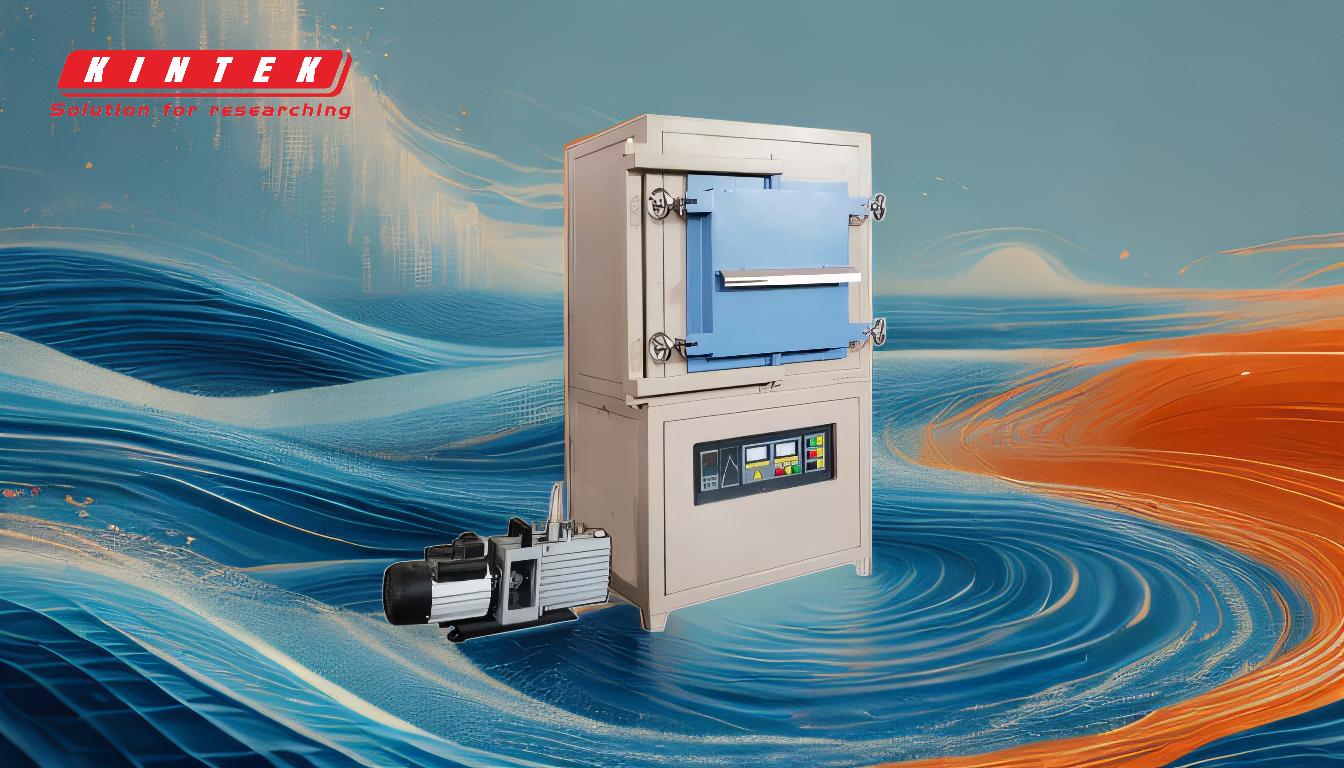
-
Définition et objectif du recuit à l'hydrogène:
- Le recuit à l'hydrogène est un processus de traitement thermique effectué dans une atmosphère composée à 100 % d'hydrogène afin de soulager les contraintes internes, de nettoyer les surfaces et de prévenir l'oxydation.
- Il est particulièrement utile pour les matériaux tels que l'acier, les alliages durs, les matériaux céramiques et les métaux réfractaires rares.
- Ce procédé est souvent appelé "recuit brillant", car il permet d'obtenir une finition de surface brillante et propre en réduisant les oxydes présents sur le matériau.
-
Conditions du processus:
- Le processus de recuit est généralement mené à des températures élevées, généralement entre 200 et 300°C. Le matériau est maintenu dans un four à hydrogène pendant plusieurs heures pour assurer un traitement efficace.
- Le matériau est maintenu dans un four de recuit à l'hydrogène pendant plusieurs heures pour garantir l'efficacité du traitement.
- Le coefficient élevé de transfert de chaleur de l'hydrogène rend le processus plus efficace par rapport à l'utilisation de l'air ou d'un mélange gazeux traditionnel d'hydrogène et d'azote.
-
Avantages du recuit à l'hydrogène:
- Nettoyage de surface:L'hydrogène agit comme un gaz fortement réducteur, qui aide à éliminer les oxydes de la surface du matériau, ce qui permet d'obtenir une finition brillante.
- Soulagement du stress:Le processus permet de soulager les contraintes internes induites pendant les processus de fabrication tels que le moulage, le soudage ou le revêtement.
- Prévention de l'oxydation:L'atmosphère d'hydrogène empêche l'oxydation et la décoloration du matériau.
-
Défis et précautions:
- Décarburation:L'hydrogène peut décarburer les pièces en acier, ce qui peut affaiblir le matériau.Des précautions sont nécessaires pour atténuer cet effet.
- Le coût:Le recuit à l'hydrogène est plus coûteux en raison du coût du maintien d'une atmosphère d'hydrogène pur.Les mélanges d'azote et d'hydrogène sont souvent utilisés comme alternative économique.
-
Les applications:
- Le recuit à l'hydrogène est utilisé dans diverses industries pour la réduction, le frittage, le recuit et le traitement de surface des matériaux.
- Il est particulièrement utile pour le traitement thermique des pièces moulées et soudées, ainsi que pour les matériaux qui nécessitent une finition de surface de haute qualité.
-
L'équipement:
- Un four de recuit à l'hydrogène est spécialement conçu pour ce processus, utilisant de l'hydrogène ou un mélange d'hydrogène et d'azote (avec une teneur en hydrogène supérieure à 5 %) comme atmosphère protectrice.
- Le four assure un environnement contrôlé pour le processus de recuit, en maintenant les conditions de température et d'atmosphère nécessaires.
-
Post-traitement:
- Le recuit à l'hydrogène est souvent utilisé immédiatement après des processus tels que le soudage, le revêtement ou la galvanisation pour éliminer les atomes d'hydrogène enfermés responsables de la fragilisation par l'hydrogène.
- Ce procédé permet d'améliorer les propriétés mécaniques et la durabilité globale du matériau.
En comprenant ces points clés, on peut apprécier l'importance et la complexité du recuit à l'hydrogène dans le traitement des matériaux, en particulier lorsqu'une finition de surface de haute qualité et une réduction des contraintes sont essentielles.
Tableau récapitulatif :
Aspect | Détails |
---|---|
Objectif | Soulager les contraintes internes, nettoyer les surfaces, prévenir l'oxydation et améliorer l'état de surface. |
Plage de température | 200-300°C |
Principaux avantages | Nettoyage de la surface, réduction des tensions, prévention de l'oxydation, finition brillante. |
Défis | Risque de décarburation, coût plus élevé que les mélanges azote-hydrogène. |
Applications | Acier, alliages durs, céramiques, métaux réfractaires rares, composants coulés/soudés. |
Équipement | Four de recuit à l'hydrogène avec atmosphère contrôlée d'hydrogène ou d'azote-hydrogène. |
Optimisez votre traitement des matériaux avec le recuit à l'hydrogène. contactez nos experts dès aujourd'hui pour en savoir plus !