Les fours à induction et les fours à arc sont tous deux largement utilisés pour la fusion et l'affinage des métaux, mais ils diffèrent considérablement dans leurs principes de fonctionnement, leurs applications et leurs résultats. Les fours à induction utilisent l'induction électromagnétique pour générer de la chaleur à l'intérieur du métal lui-même, ce qui les rend adaptés à un contrôle précis de la température et à une production d'acier propre, en particulier pour les alliages à faible teneur en carbone. Les fours à arc, quant à eux, s'appuient sur des arcs électriques entre des électrodes en graphite et le métal pour générer de la chaleur, ce qui les rend plus polyvalents pour la manipulation d'une large gamme de matériaux et capables d'une déphosphoration plus forte. Les fours à induction sont plus rentables pour les petits lots et offrent de meilleurs taux de récupération des métaux, tandis que les fours à arc sont mieux adaptés aux opérations à grande échelle et aux processus métallurgiques complexes.
Explication des points clés :
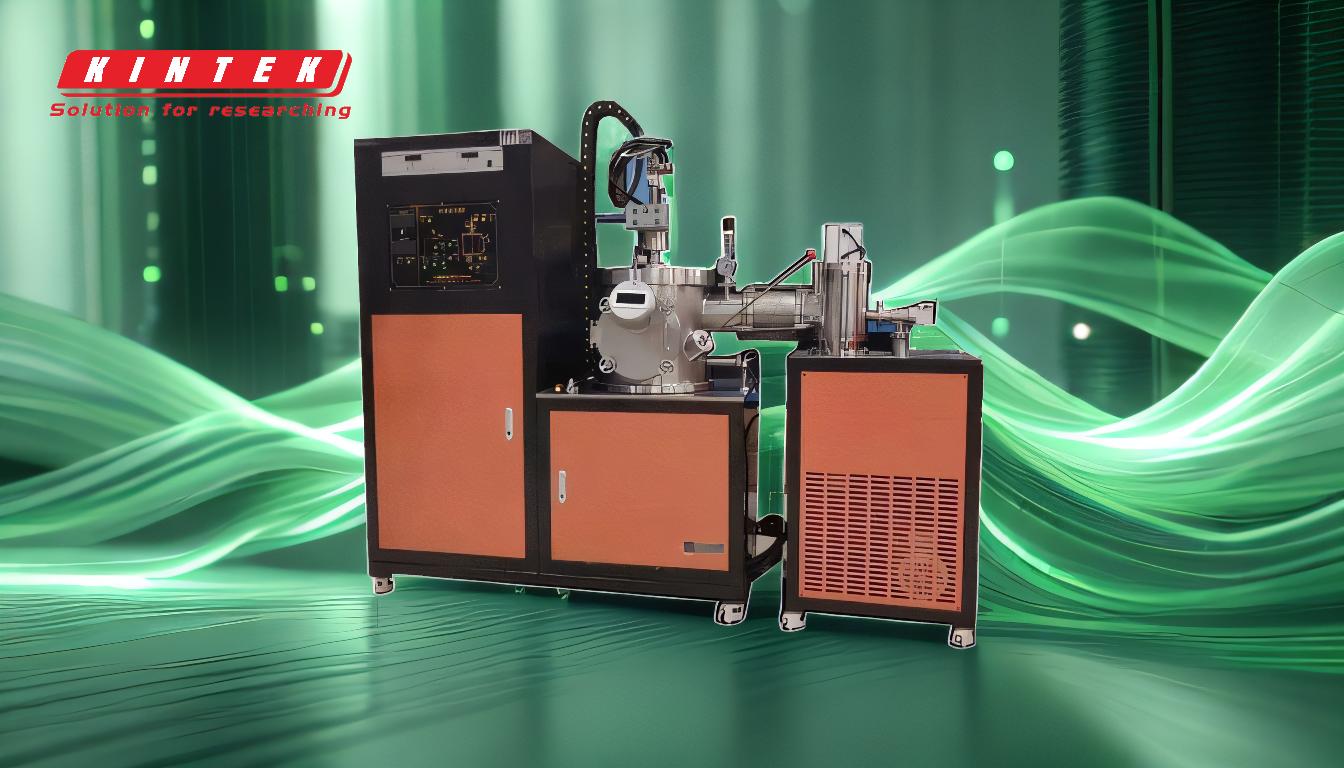
-
Mécanisme de chauffage:
- Four à induction: Cette méthode utilise l'induction électromagnétique pour générer de la chaleur directement à l'intérieur du métal. Cette méthode ne nécessite pas d'électrodes en graphite, ce qui élimine l'accumulation de carbone et permet la production d'aciers à faible et très faible teneur en carbone.
- Four à arc: Ce procédé repose sur la formation d'arcs électriques entre des électrodes en graphite et le métal pour générer de la chaleur. Ce procédé peut entraîner une accumulation de carbone, ce qui le rend moins adapté aux alliages à faible teneur en carbone, mais efficace pour la déphosphoration.
-
Contrôle de la teneur en carbone:
- Four à induction: Idéal pour la fusion d'acier et d'alliages à très faible teneur en carbone, car il évite l'utilisation d'électrodes en graphite, qui peuvent introduire du carbone dans la matière fondue.
- Four à arc: L'utilisation d'électrodes en graphite peut entraîner une accumulation de carbone, ce qui complique la production d'aciers à faible teneur en carbone. Toutefois, cette caractéristique est bénéfique pour les processus nécessitant une teneur en carbone plus élevée.
-
Capacités métallurgiques:
- Four à induction: Historiquement, les fours à induction avaient des fonctions métallurgiques limitées, mais les progrès réalisés depuis les années 1980 ont permis d'améliorer leurs capacités. Ils sont désormais utilisés pour produire des aciers faiblement alliés, des aciers fortement alliés et même des aciers inoxydables à très faible teneur en carbone et des superalliages de haute qualité.
- Four à arc: Il a généralement des fonctions métallurgiques plus importantes, en particulier en ce qui concerne la déphosphoration. Il peut traiter une plus grande variété de matériaux chargés et convient aux opérations à grande échelle.
-
Taille des lots et rentabilité:
- Four à induction: Plus rentable pour les lots de petite taille en raison des coûts opérationnels plus faibles et des taux de récupération des métaux plus élevés. Il est également plus respectueux de l'environnement.
- Four à arc: Mieux adapté aux opérations à grande échelle, il peut traiter une gamme plus large de matériaux, ce qui le rend plus polyvalent pour les processus métallurgiques complexes.
-
Impact sur l'environnement:
- Four à induction: Plus respectueux de l'environnement grâce à l'absence d'électrodes en graphite, ce qui réduit les émissions de carbone et la contamination.
- Four à arc: L'utilisation d'électrodes en graphite peut entraîner une augmentation des émissions de carbone et de l'impact sur l'environnement, bien qu'elle reste un choix populaire pour la production d'acier à grande échelle.
-
Qualité et homogénéité des produits:
- Four à induction: Garantit une qualité de produit homogène grâce à l'agitation électromagnétique, qui favorise un mélange uniforme de la matière fondue.
- Four à arc: Bien qu'il puisse produire de l'acier de haute qualité, l'homogénéité du produit peut ne pas être aussi constante que celle produite par les fours à induction en raison de la nature du processus de chauffage à l'arc.
-
Applications:
- Four à induction: Utilisé couramment pour les petites pièces moulées en acier et les alliages spécialisés, en particulier lorsqu'une faible teneur en carbone et une grande pureté sont requises.
- Four à arc: Largement utilisé dans la production d'acier à grande échelle, y compris la fabrication d'aciers de construction, d'aciers à outils et d'autres applications à grand volume.
En résumé, le choix entre les fours à induction et les fours à arc dépend des exigences spécifiques du processus de production de métal, notamment la teneur en carbone souhaitée, la taille du lot, les capacités métallurgiques et les considérations environnementales. Les fours à induction se distinguent par leur précision et leur propreté, tandis que les fours à arc offrent polyvalence et robustesse pour les opérations à grande échelle.
Tableau récapitulatif :
Fonctionnalité | Four à induction | Four à arc |
---|---|---|
Mécanisme de chauffage | Induction électromagnétique | Arcs électriques entre les électrodes et le métal |
Contrôle du carbone | Idéal pour les alliages à faible teneur en carbone | Meilleur pour une teneur en carbone plus élevée |
Capacités métallurgiques | Amélioré pour les alliages faibles et les superalliages | Déphosphoration plus forte |
Taille du lot | Rentable pour les petits lots | Adapté aux opérations à grande échelle |
Impact sur l'environnement | Plus écologique (pas d'électrodes en graphite) | Des émissions de carbone plus élevées |
Homogénéité des produits | Grande uniformité | Moins cohérent |
Applications | Petites pièces moulées, alliages à faible teneur en carbone | Production d'acier à grande échelle |
Vous ne savez toujours pas quel four est le mieux adapté à vos besoins ? Contactez nos experts dès aujourd'hui pour des conseils personnalisés !