La modélisation par dépôt de matière fondue (FDM) est un procédé de fabrication additive très répandu dans lequel une matière thermoplastique est extrudée à travers une buse chauffée et déposée couche par couche pour créer un objet tridimensionnel. Le processus implique un mouvement horizontal précis de la buse et un mouvement vertical de la plate-forme de construction, ce qui permet de créer des géométries complexes. La FDM est connue pour sa simplicité, sa rentabilité et sa polyvalence dans l'utilisation des matériaux, ce qui en fait un choix populaire pour le prototypage, les essais fonctionnels et la production de pièces d'utilisation finale.
Explication des points clés :
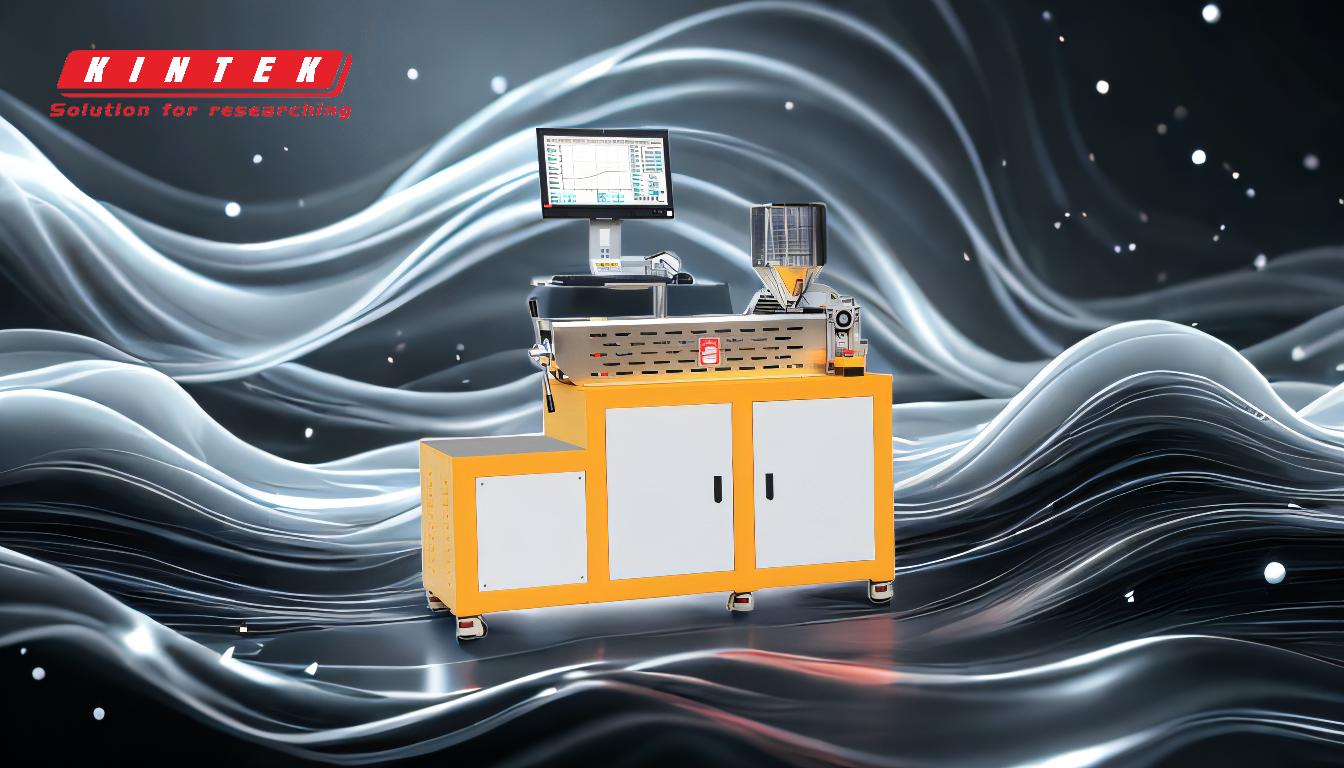
-
Définition et vue d'ensemble du FDM:
- La modélisation par dépôt en fusion (FDM) est un type de procédé de fabrication additive qui permet de construire des objets couche par couche à l'aide de matériaux thermoplastiques.
- Il s'agit d'une marque déposée par Stratasys, mais le terme est souvent utilisé de manière générique pour décrire des technologies d'impression 3D similaires basées sur l'extrusion.
-
Processus d'extrusion de matériaux:
- Le processus commence par un filament thermoplastique qui est introduit dans une buse chauffée.
- La buse chauffe le matériau jusqu'à son point de fusion, ce qui permet de l'extruder à l'état semi-liquide.
- Le matériau extrudé est déposé sur une plate-forme de construction de manière contrôlée, en suivant une trajectoire prédéfinie basée sur le modèle 3D.
-
Dépôt couche par couche:
- La buse se déplace horizontalement pour déposer le matériau dans la forme de la couche en cours.
- Une fois chaque couche terminée, la plate-forme de construction descend (ou la buse remonte) pour permettre le dépôt de la couche suivante.
- Cette approche couche par couche se poursuit jusqu'à ce que l'objet soit entièrement formé.
-
Mouvement et précision:
- La buse est capable d'un mouvement horizontal précis, contrôlé par des moteurs pas à pas ou des servomoteurs, garantissant un placement précis du matériau.
- Le mouvement vertical de la plate-forme de fabrication est tout aussi précis, ce qui permet d'obtenir une épaisseur de couche constante et une précision dimensionnelle globale.
-
Matériaux utilisés en FDM:
- Les matériaux courants sont l'ABS (Acrylonitrile Butadiène Styrène), le PLA (Acide Polylactique), le PETG (Polyéthylène Téréphtalate Glycol) et divers thermoplastiques de qualité technique.
- Ces matériaux sont choisis en fonction de leurs propriétés mécaniques, de leur stabilité thermique et de leur facilité d'extrusion.
-
Applications du FDM:
- Prototypage: Le FDM est largement utilisé pour la création de prototypes en raison de sa rapidité et de sa rentabilité.
- Essais fonctionnels: Les pièces produites par FDM peuvent être utilisées pour des essais fonctionnels, car les matériaux peuvent imiter les propriétés des pièces de production finales.
- Pièces d'utilisation finale: Dans certains cas, la technologie FDM est utilisée pour produire des pièces finales, en particulier lorsqu'il s'agit d'une production sur mesure ou en faible volume.
-
Avantages de la FDM:
- Rentabilité: La FDM est l'une des technologies d'impression 3D les plus abordables, ce qui la rend accessible aux petites entreprises et aux amateurs.
- Polyvalence des matériaux: Une large gamme de matériaux thermoplastiques peut être utilisée, ce qui permet une grande flexibilité dans les propriétés des matériaux.
- Facilité d'utilisation: Les imprimantes FDM sont relativement faciles à utiliser et à entretenir, ce qui les rend adaptées à des utilisateurs ayant des niveaux d'expertise variés.
-
Limites de la FDM:
- Finition de la surface: Les pièces produites par FDM ont souvent un fini de surface rugueux, qui peut nécessiter un post-traitement à des fins esthétiques ou fonctionnelles.
- Adhésion des couches: La résistance des pièces FDM peut être limitée par l'adhérence entre les couches, ce qui peut affecter les performances mécaniques globales.
- Vitesse: Bien que la FDM soit plus rapide que d'autres méthodes d'impression 3D, elle peut être plus lente que les procédés de fabrication traditionnels pour les pièces complexes ou de grande taille.
-
Post-traitement:
- Ponçage et polissage: Pour améliorer la finition de la surface, les pièces FDM peuvent être poncées et polies.
- Peinture et revêtement: Les pièces peuvent être peintes ou revêtues afin d'améliorer leur apparence ou d'assurer une protection supplémentaire.
- Recuit: Certains matériaux peuvent bénéficier d'un recuit, un processus de traitement thermique qui peut améliorer les propriétés mécaniques.
-
Développements futurs dans le domaine du FDM:
- Innovations en matière de matériaux: Les recherches en cours se concentrent sur le développement de nouveaux matériaux dotés de propriétés améliorées, telles qu'une plus grande solidité, une meilleure résistance thermique et une meilleure biocompatibilité.
- Impression multi-matériaux: Les progrès de la technologie FDM permettent d'utiliser plusieurs matériaux dans une seule impression, ce qui permet de créer des pièces plus complexes et plus fonctionnelles.
- Automatisation accrue: Les futurs systèmes FDM pourraient intégrer davantage d'automatisation, comme le changement automatique de matériau et l'enlèvement des pièces, afin de rationaliser davantage le processus de fabrication.
En résumé, la modélisation par dépôt en fusion (FDM) est une technologie d'impression 3D polyvalente et rentable qui utilise l'extrusion de thermoplastiques pour construire des objets couche par couche. Sa simplicité, la polyvalence de ses matériaux et son large éventail d'applications en font un choix populaire pour le prototypage et la production de pièces d'usage final. Elle présente toutefois des limites, telles que la qualité de la finition de la surface et l'adhérence des couches, qui peuvent être résolues grâce au post-traitement et aux progrès technologiques continus.
Tableau récapitulatif :
Aspect | Détails |
---|---|
Procédé | Extrusion thermoplastique couche par couche à l'aide d'une buse chauffée. |
Matériaux | ABS, PLA, PETG et thermoplastiques de qualité technique. |
Applications | Prototypage, essais fonctionnels et production de pièces finales. |
Avantages | Rentabilité, polyvalence des matériaux et facilité d'utilisation. |
Limites | Finition de surface grossière, problèmes d'adhérence des couches et vitesse plus lente pour les pièces de grande taille. |
Post-traitement | Ponçage, polissage, peinture, revêtement et recuit. |
Développements futurs | Nouveaux matériaux, impression multi-matériaux et automatisation accrue. |
Découvrez comment la FDM peut transformer votre processus de prototypage. contactez-nous dès aujourd'hui pour obtenir des conseils d'experts !