La température d'un four de craquage, également connu sous le nom de four de pyrolyse, est un paramètre critique qui a un impact direct sur l'efficacité et les performances du processus de craquage.Les fours de craquage sont utilisés dans des industries telles que la pétrochimie pour décomposer les grosses molécules d'hydrocarbures en molécules plus petites et plus précieuses.La température de ces fours est généralement comprise entre 750°C et 900°C en fonction du processus spécifique et de la matière première utilisée.Des facteurs tels que le temps de séjour, la pression et un entretien adéquat jouent également un rôle important pour garantir des performances et une sécurité optimales.Nous examinons ci-dessous les principaux aspects des températures des fours de craquage et leurs implications.
Explication des points clés :
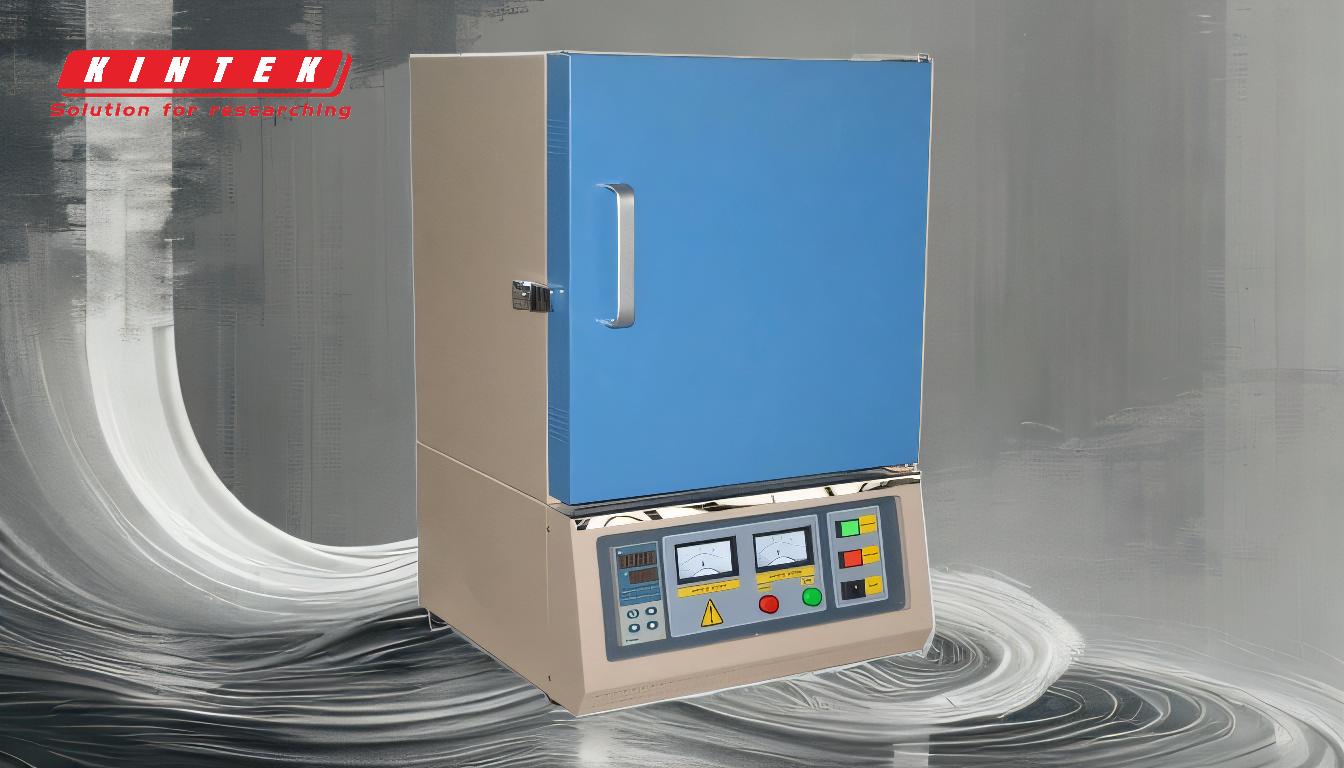
-
Plage de température typique d'un four de craquage
- La température d'un four de craquage est généralement comprise entre 750°C et 900°C .
- Cette température élevée est nécessaire pour fournir l'énergie nécessaire à la rupture des liaisons chimiques dans les grosses molécules d'hydrocarbures, un processus connu sous le nom de craquage thermique.
- La température exacte dépend du type de matière première (naphta, éthane ou propane) et des produits finis souhaités (éthylène, propylène).
-
Facteurs influençant la température du four
- Composition de la matière première:Des hydrocarbures différents nécessitent des températures différentes pour un craquage optimal.Par exemple, les charges d'alimentation plus légères comme l'éthane peuvent nécessiter des températures plus basses que les charges d'alimentation plus lourdes comme le naphta.
- Temps de séjour:Le temps passé par la matière première dans le four influe sur l'efficacité du craquage.Des temps de séjour plus longs à des températures plus basses permettent d'obtenir des résultats similaires à des temps plus courts à des températures plus élevées.
- La pression:La pression de fonctionnement peut influencer la température de fissuration.Des pressions plus basses favorisent souvent les réactions de craquage, ce qui permet d'obtenir des températures légèrement plus basses.
- Conception du four:La conception du four, y compris la configuration du brûleur et la distribution de la chaleur, joue un rôle dans le maintien de températures constantes.
-
Importance du contrôle de la température
- Efficacité optimale du craquage:Le maintien d'une température correcte garantit que la matière première est craquée efficacement, maximisant ainsi le rendement de produits précieux tels que l'éthylène et le propylène.
- La sécurité:Des températures excessives peuvent entraîner des réactions secondaires indésirables, telles que la cokéfaction, qui peuvent endommager le four et réduire sa durée de vie.
- Consommation d'énergie:Un contrôle adéquat de la température minimise le gaspillage d'énergie, réduisant ainsi les coûts d'exploitation et l'impact sur l'environnement.
-
Les défis de la gestion de la température
- Fluctuations de la température:Les variations de la composition des matières premières ou des débits peuvent entraîner des fluctuations de température, ce qui nécessite des systèmes de contrôle précis.
- Cokéfaction et dépôts:Les températures élevées peuvent entraîner la formation de dépôts de coke sur les parois des fours et les tubes, ce qui réduit l'efficacité du transfert de chaleur et augmente le risque de surchauffe.
- Vieillissement de l'équipement:Avec le temps, les composants du four peuvent se dégrader, ce qui rend plus difficile le maintien de températures constantes.Un entretien régulier est essentiel pour remédier à ces problèmes.
-
Comparaison avec d'autres types de fours
- Contrairement aux fours continus utilisés pour les processus de traitement thermique (par exemple, le recuit ou la trempe), les fours de craquage fonctionnent à des températures beaucoup plus élevées et sont conçus pour des réactions chimiques spécifiques.
- Les fours dentaires, par exemple, fonctionnent à des températures beaucoup plus basses (généralement inférieures à 1500°C) et sont influencés par différents facteurs, tels que le type de matériaux à cuire (par exemple, céramiques ou alliages).
-
Considérations relatives à l'exploitation et à la maintenance
- Systèmes de surveillance:Des systèmes avancés de surveillance et de contrôle de la température sont essentiels pour maintenir des conditions optimales dans un four de craquage.
- Entretien régulier:Le nettoyage des tubes des fours pour éliminer les dépôts de coke et l'inspection des brûleurs et des échangeurs de chaleur peuvent prévenir les problèmes liés à la température.
- Efficacité énergétique:Un bon réglage des brûleurs et de la conception du four permet de réduire la consommation d'énergie tout en maintenant la température souhaitée.
En résumé, la température d'un four de craquage est un paramètre critique qui doit être soigneusement contrôlé pour garantir un fonctionnement efficace et sûr.En comprenant les facteurs qui influencent la température et en mettant en œuvre des pratiques de maintenance appropriées, les opérateurs peuvent optimiser les performances de leurs fours de craquage et obtenir les rendements souhaités.
Tableau récapitulatif :
Aspect clé | Détails |
---|---|
Plage de température | 750°C-900°C, en fonction de la matière première et du processus. |
Facteurs clés | Matière première, temps de séjour, pression et conception du four. |
Importance du contrôle | Garantit l'efficacité, la sécurité et les économies d'énergie. |
Défis | Fluctuations de température, cokéfaction et vieillissement des équipements. |
Conseils d'entretien | Nettoyage régulier, surveillance avancée et réglages éco-énergétiques. |
Besoin de conseils d'experts sur le contrôle de la température des fours à cracking ? Contactez nous dès aujourd'hui pour des solutions sur mesure !