La calcination et la fusion sont des processus à haute température qui nécessitent des fours spécialisés pour réaliser les transformations chimiques et physiques souhaitées.La calcination consiste à chauffer des matériaux à des températures élevées en l'absence ou en présence limitée d'air afin d'induire une décomposition thermique, tandis que la fusion consiste à faire fondre des minerais pour en extraire des métaux.Les types de fours utilisés pour ces processus comprennent les fours à moufle, les fours à réverbère, les fours à cuve et les fours rotatifs.Ces fours sont conçus pour fournir un chauffage uniforme, un contrôle précis de la température et la capacité de traiter de grands volumes de matériaux.Les applications industrielles utilisent souvent des fours à combustion ou des fours électriques, en fonction des coûts et des considérations environnementales.Nous examinons ci-dessous les principaux types de fours utilisés pour la calcination et la fusion, leurs configurations et leurs applications.
Explication des points clés :
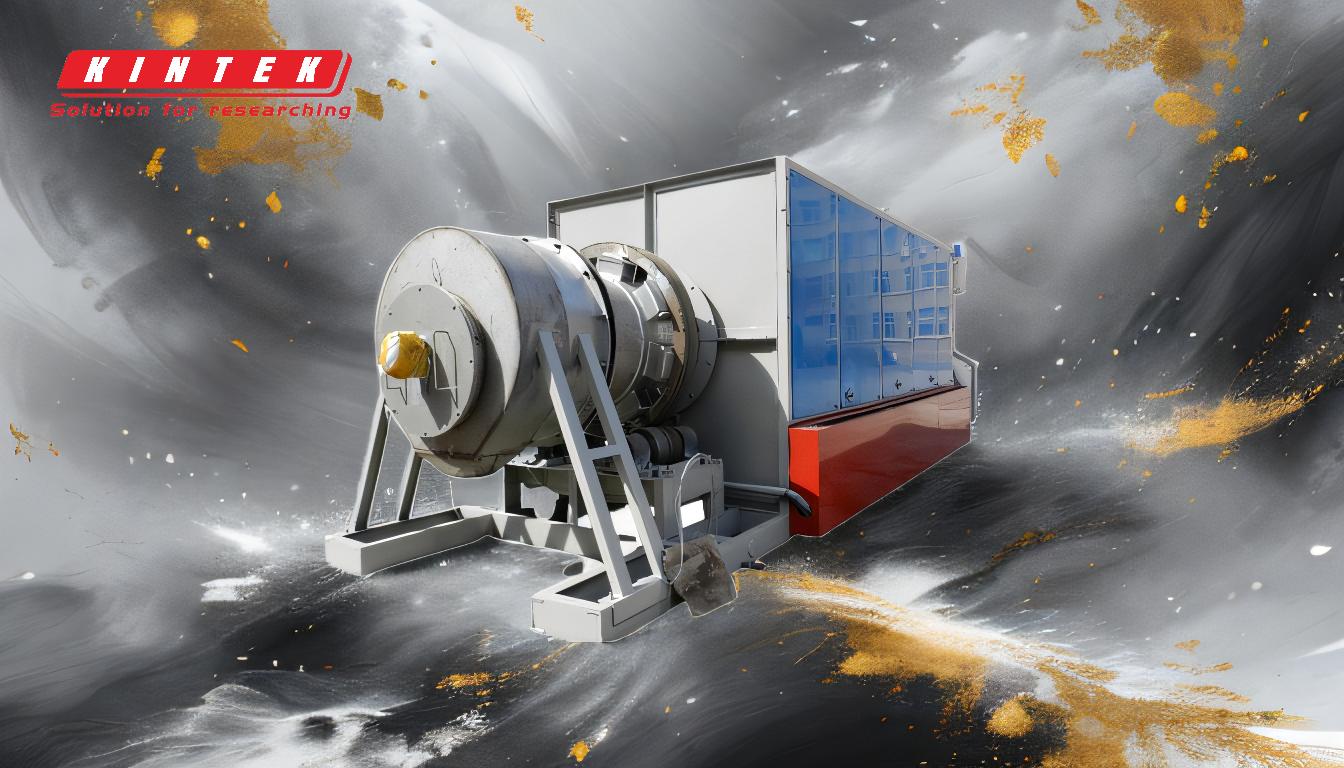
-
Fours à moufle:
- Les fours à moufle sont largement utilisés pour la calcination en raison de leur capacité à fournir un chauffage uniforme et à isoler le matériau des gaz de combustion.Ils sont équipés d'éléments chauffants entourant une chambre, ce qui permet un contrôle précis de la température.
- Applications :Calcination de matériaux tels que le calcaire (pour produire de la chaux), les céramiques et les catalyseurs.
- Avantages :Homogénéité de la température, isolation des contaminants et possibilité d'utilisation à petite échelle en laboratoire ou dans l'industrie.
-
Fours à réverbère:
- Les fours à réverbère sont de grands fours industriels utilisés pour la fusion et la calcination.Ils sont dotés d'une sole peu profonde et d'un toit qui réfléchit la chaleur sur le matériau, assurant ainsi un transfert de chaleur efficace.
- Applications :Fusion de métaux tels que le cuivre et le plomb, ainsi que calcination de minerais.
- Avantages :Capacité élevée, capacité à traiter de grands volumes et aptitude au fonctionnement en continu.
-
Fours à arbre:
- Les fours à cuve sont des fours verticaux utilisés pour la calcination et la fusion.Ils fonctionnent en alimentant les matériaux par le haut et en les laissant descendre à travers une chambre chauffée, où ils subissent un traitement thermique.
- Applications :Calcination du calcaire et de la dolomie, ainsi que fonte des minerais de fer dans les hauts fourneaux.
- Avantages :Utilisation efficace de la chaleur, fonctionnement continu et débit élevé.
-
Fours rotatifs:
- Les fours rotatifs sont des fours cylindriques qui tournent pour assurer un chauffage uniforme des matériaux.Ils sont couramment utilisés pour les processus de calcination et de fusion.
- Applications :Calcination du clinker, de l'alumine et d'autres minéraux industriels, ainsi que fusion de minerais.
- Avantages :Rendement thermique élevé, capacité à traiter une large gamme de matériaux et traitement en continu.
-
Fours électriques ou chauffés:
- Les fours électriques sont utilisés pour la calcination et la fusion dans les applications où le contrôle de la pollution est essentiel.Ils sont plus coûteux mais offrent un contrôle précis de la température et ne produisent pas d'émissions.
- Les fours industriels à combustion utilisent des combustibles (par exemple, le gaz ou le pétrole) pour produire de la chaleur et sont largement utilisés dans l'industrie en raison de leurs faibles coûts d'exploitation.
- Applications :Les fours électriques sont préférés pour les matériaux de haute pureté, tandis que les fours à feu sont utilisés dans les raffineries, les usines pétrochimiques et les fonderies de métaux.
-
Fours spécialisés pour les applications industrielles:
- Les fours à tambour rotatif, les fours à sole roulante, les fours à plaques poussantes et les fours à fond ouvrant sont des fours spécialisés utilisés pour le frittage et la fusion de produits industriels.
- Applications :Frittage de céramiques, de métaux et d'autres matériaux, ainsi que fusion de minerais.
- Avantages :Débit élevé, contrôle précis de la température et adaptation aux opérations industrielles à grande échelle.
En comprenant les exigences spécifiques des processus de calcination et de fusion, telles que la plage de température, le volume de matière et les considérations environnementales, le type de four approprié peut être sélectionné pour garantir des performances et une efficacité optimales.
Tableau récapitulatif :
Type de four | Applications | Avantages des fours à moufle |
---|---|---|
Fours à moufle | Calcination du calcaire, des céramiques, des catalyseurs | Homogénéité de la température, isolation des contaminants, utilisation à petite échelle |
Fours à réverbère | Fusion du cuivre et du plomb ; calcination des minerais | Capacité élevée, traitement de grands volumes, fonctionnement continu |
Fours à cuve | Calcination du calcaire, de la dolomie ; fusion des minerais de fer | Utilisation efficace de la chaleur, fonctionnement continu, débit élevé |
Fours rotatifs | Calcination du clinker, de l'alumine ; fusion de minerais | Rendement thermique élevé, traitement d'une large gamme de matériaux, traitement en continu |
Fours électriques de traitement | Matériaux de haute pureté, applications sensibles à la pollution | Contrôle précis de la température, pas d'émissions |
Fours de traitement chauffés | Raffineries, usines pétrochimiques, fonderies de métaux | Coûts d'exploitation réduits, largement utilisés dans l'industrie |
Fours spécialisés | Frittage de céramiques, de métaux ; fusion de minerais | Débit élevé, contrôle précis de la température, opérations industrielles à grande échelle |
Vous avez besoin d'aide pour choisir le bon four pour votre processus de calcination ou de fusion ? Contactez nos experts dès aujourd'hui !