La fusion de l'aluminium nécessite des fours spécialisés conçus pour gérer les propriétés uniques du métal, telles que sa faible densité et sa conductivité thermique élevée.Les fours les plus couramment utilisés pour la fusion de l'aluminium sont les fours à induction et les fours de fusion rotatifs.Les fours à induction sont très efficaces, ils réduisent les pertes par oxydation et produisent de l'aluminium de grande pureté, tandis que les fours rotatifs sont polyvalents et idéaux pour le recyclage des déchets d'aluminium.Le choix du four dépend de facteurs tels que la capacité de production, le type d'énergie et les exigences opérationnelles.Les deux types de fours offrent des avantages distincts, tels qu'un contrôle précis de la température, une réduction des émissions et une flexibilité dans le traitement de différents alliages d'aluminium ou de différentes formes de déchets.
Explication des points clés :
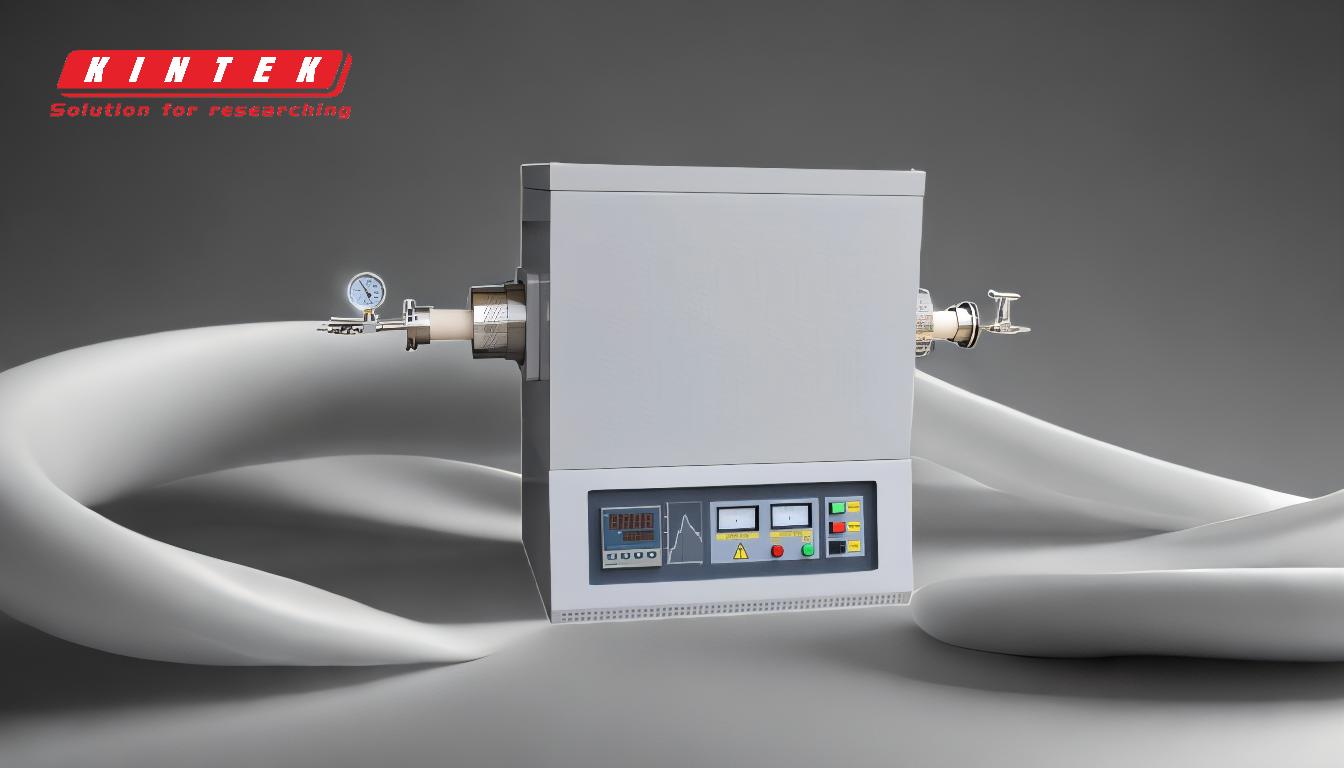
-
Fours à induction pour la fusion de l'aluminium:
- Les fours à induction sont largement utilisés pour la fusion de l'aluminium en raison de leur efficacité, qui varie de 60 à 75 %.Ils minimisent les pertes dues à l'oxydation et produisent un aluminium d'une grande pureté et d'une grande uniformité.
- La source de chaleur d'un four à induction n'entre pas directement en contact avec l'aluminium, ce qui permet la fusion mixte d'alliages d'aluminium.
- Ces fours utilisent un courant alternatif triphasé, un dispositif de conversion de fréquence et une charge de bobine pour faire fondre l'aluminium.Les impuretés remontent à la surface et sont éliminées, tandis que l'aluminium pur descend.
- Les fours à induction sont plus silencieux, produisent moins de fumée et de poussière et sont plus efficaces que les fours à résistance ou les fours à fréquence industrielle.
-
Fours de fusion rotatifs:
- Les fours rotatifs sont très polyvalents et conçus pour le recyclage des déchets d'aluminium.Ils sont excellents pour récupérer toutes les formes de déchets, ce qui les rend idéaux pour les industries axées sur le développement durable.
- Ces fours tournent à l'aide de systèmes tels que des roues d'entraînement à friction, des crémaillères ou des chaînes, en fonction des dimensions et des exigences de production.
- Les fours rotatifs sont équipés de systèmes efficaces d'extraction des fumées, qui peuvent être fixes ou inclinés avec le four.Ils peuvent être alimentés par des sources d'énergie telles que le gaz, le diesel ou l'huile de chauffage.
- Ils sont revêtus de matériaux réfractaires et de matières coulées pour des performances et une efficacité supérieures, ce qui les rend adaptés aux industries de la forge et de la fusion de l'aluminium.
-
Facteurs à prendre en compte lors du choix d'un four:
- Capacité:Les petits fours (5-10 tonnes) conviennent aux petites entreprises, tandis que les grands fours (25 tonnes ou plus) sont rentables pour une utilisation industrielle.
- Livraison de la production:Certains fours exigent une taille de lot minimale, par exemple 20 tonnes, avec tout le métal provenant de la même chaleur.
- Commodité du service:L'accumulation de crasse réduit l'efficacité du four, d'où la nécessité d'un nettoyage périodique.La facilité d'entretien doit être prise en compte.
- Type d'énergie:Le choix de l'énergie (gaz naturel, mazout, diesel ou électricité) dépend de sa disponibilité et de son coût.Les fours à induction utilisent généralement l'électricité, tandis que les fours rotatifs peuvent utiliser le gaz ou le pétrole.
-
Avantages des fours à induction et des fours rotatifs:
-
Fours à induction:
- Rendement élevé et pertes d'oxydation réduites.
- Contrôle précis de la température et répartition uniforme de la chaleur.
- Idéal pour la production d'aluminium et d'alliages de haute pureté.
-
Fours rotatifs:
- Polyvalence dans le traitement de diverses formes de déchets d'aluminium.
- Extraction efficace des fumées et options énergétiques.
- Convient aux opérations industrielles à grande échelle.
-
Fours à induction:
-
Considérations spécifiques à l'application:
- Le choix entre les fours à induction et les fours rotatifs dépend de la cadence de production souhaitée, de la qualité et de la composition de la ferraille d'aluminium, et de la nécessité d'un mode de fonctionnement discontinu ou continu.
- Pour la production d'aluminium de haute pureté, les fours à induction sont préférables, tandis que les fours rotatifs conviennent mieux au recyclage de la ferraille et aux opérations à grande échelle.
-
Fours de fusion sous vide:
- Bien qu'ils ne soient pas explicitement mentionnés dans les références, les fours de fusion sous vide constituent une autre option pour la fusion de l'aluminium, en particulier lorsqu'une pureté élevée et une oxydation minimale sont essentielles.Ces fours fonctionnent dans un environnement sous vide, ce qui empêche la contamination et l'oxydation.Pour plus de détails, vous pouvez explorer le sujet des four de fusion sous vide .
En comprenant les caractéristiques et les avantages uniques de chaque type de four, les acheteurs peuvent prendre des décisions éclairées en fonction de leurs besoins spécifiques, tels que la capacité de production, l'efficacité énergétique et la flexibilité opérationnelle.
Tableau récapitulatif :
Type de four | Caractéristiques principales | Applications |
---|---|---|
Four à induction | Rendement élevé (60-75%), contrôle précis de la température, pertes d'oxydation minimales | Production d'aluminium de haute pureté, fusion d'alliages |
Four rotatif | Polyvalent, extraction efficace des fumées, traitement de diverses formes de ferraille | Recyclage des déchets d'aluminium, opérations à grande échelle |
Vous avez besoin d'aide pour choisir le bon four pour vos besoins en fusion d'aluminium ? Contactez nos experts dès aujourd'hui !