Introduction à la pulvérisation cathodique magnétron
Aperçu du processus de pulvérisation magnétron
La pulvérisation magnétron est une technologie sophistiquée de dépôt physique en phase vapeur (PVD) qui implique le dépôt d'un film mince sur un substrat. Ce processus se déroule dans une chambre à vide, où un matériau cible est soumis à un plasma à haute énergie. Le plasma, généré par la combinaison d'un gaz de pulvérisation et d'un champ magnétique puissant à proximité de la cible, provoque l'éjection d'atomes ou de molécules du matériau cible, qui se déposent ensuite sur le substrat.
Le champ magnétique joue un rôle crucial dans la pulvérisation magnétron, car il confine le plasma dans une région proche de la cible. Ce confinement garantit que les ions énergétiques du plasma interagissent principalement avec le matériau cible, minimisant ainsi les dommages causés au film mince en croissance sur le substrat. Le processus commence par l'évacuation de la chambre pour atteindre des conditions de vide élevé, ce qui réduit les pressions de gaz de fond et les contaminants potentiels. Ensuite, le gaz de pulvérisation est introduit dans la chambre et la pression est régulée au niveau du milliTorr à l'aide d'un système de contrôle de précision.
Essentiellement, la pulvérisation magnétron est un processus de dépôt basé sur le plasma où les ions frappent la cible, provoquant l'éjection d'atomes. Ces atomes se déplacent ensuite dans l'environnement sous vide et s'intègrent dans le film qui se développe sur le substrat. L'interaction complexe entre le champ magnétique, le plasma et le vide garantit la formation précise et efficace de couches minces, ce qui fait de la pulvérisation magnétron une technique polyvalente et largement utilisée dans diverses applications industrielles.
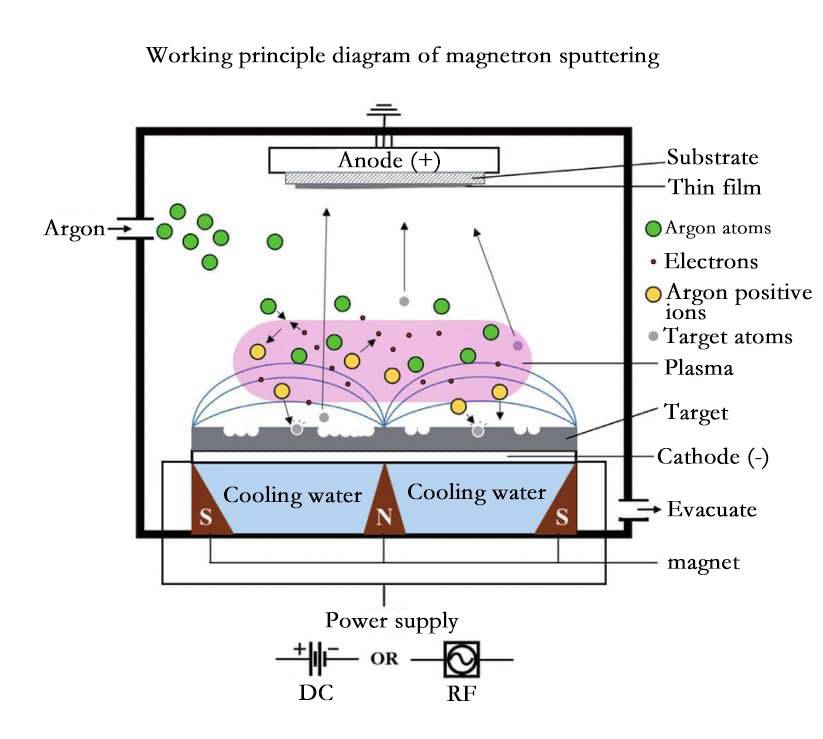
Causes de l'étincelage du matériau cible
Oxydation de la surface du matériau cible
L'interaction entre le matériau cible et les molécules d'oxygène dans la chambre à vide est un facteur critique dans le processus de pulvérisation. Lorsque le matériau cible est exposé à l'oxygène, il peut subir une réaction chimique qui entraîne la formation d'oxydes à sa surface. Ces oxydes, bien qu'initialement stables, peuvent ensuite se décomposer dans les conditions de haute énergie du processus de pulvérisation.
La décomposition de ces oxydes libère des gaz qui peuvent s'accumuler dans la chambre à vide. Cette accumulation peut entraîner des changements de pression localisés et, dans les cas extrêmes, provoquer des étincelles. Les étincelles résultent de la libération soudaine d'énergie par le processus de décomposition, ce qui peut perturber l'environnement de pulvérisation et potentiellement endommager l'équipement.
Pour atténuer ce problème, il est essentiel de contrôler l'atmosphère à l'intérieur de la chambre à vide. Cela implique de maintenir une faible concentration de gaz réactifs tels que l'oxygène, afin que l'environnement reste stable et propice au processus de pulvérisation. En outre, un nettoyage régulier de la surface du matériau cible peut empêcher l'accumulation d'oxydes, réduisant ainsi le risque de formation d'étincelles.
Défauts de surface sur le matériau cible
Les défauts de surface du matériau cible, tels que de minuscules fissures ou trous, peuvent avoir un impact significatif sur le processus de pulvérisation. Ces imperfections agissent comme des points de faiblesse localisés, où la décharge électrique pendant la pulvérisation se concentre. Cette concentration de la décharge peut conduire à la formation d'arcs électriques locaux puissants, qui sont des décharges électriques intenses susceptibles d'enflammer le matériau cible.
La présence de tels défauts est particulièrement problématique car ils perturbent la distribution uniforme du processus de pulvérisation. Au lieu d'un revêtement lisse et uniforme, les défauts provoquent une concentration de l'énergie dans des zones spécifiques, ce qui entraîne une surchauffe localisée et un risque d'inflammation. Cela compromet non seulement la qualité du revêtement, mais pose également un risque pour la sécurité de l'équipement et des opérateurs.
Pour réduire le risque d'étincelles dues à des défauts de surface, il est essentiel d'inspecter et de préparer soigneusement le matériau cible avant le début du processus de pulvérisation. Il s'agit notamment d'identifier et de corriger toutes les imperfections de surface, afin de s'assurer que le matériau est dans un état optimal pour l'application du revêtement.
Mauvaises conditions de pulvérisation
De mauvaises conditions de pulvérisation peuvent contribuer de manière significative à l'inflammation de la cible au cours du processus de pulvérisation magnétron. Ces conditions résultent souvent d'une combinaison de réglages de puissance élevés ou faibles pendant le chauffage de la cible et de champs magnétiques inégaux. Des réglages de puissance élevés peuvent provoquer un chauffage excessif, entraînant une vaporisation rapide et l'inflammation subséquente du matériau de la cible. Inversement, un réglage de puissance faible peut entraîner un chauffage insuffisant, provoquant une surchauffe localisée et des étincelles en raison d'une distribution inégale de l'énergie.
En outre, un champ magnétique inégal peut perturber la distribution uniforme du plasma dans la chambre à vide, entraînant des décharges concentrées en des points spécifiques de la surface de la cible. Cette concentration d'énergie peut créer des arcs locaux puissants, susceptibles de s'enflammer. Le tableau ci-dessous résume les effets de ces conditions inappropriées :
Condition | Effet |
---|---|
Réglage de la puissance élevée | Chauffage excessif, vaporisation rapide et inflammation de la cible |
Réglage à faible puissance | Chauffage insuffisant, surchauffe localisée et formation d'étincelles |
Champ magnétique inégal | Distribution perturbée du plasma, décharges concentrées et inflammation |
Pour résoudre ces problèmes, il faut adopter une approche méticuleuse du réglage et du maintien des paramètres de pulvérisation, en veillant à ce que la puissance et le champ magnétique soient à la fois stables et uniformément répartis.
Solutions pour éviter l'allumage de la cible
Assurer la propreté de la surface de la cible
Le nettoyage de la surface de la cible avant le processus de pulvérisation est une étape essentielle pour éviter l'apparition d'étincelles. Cette procédure consiste à éliminer méticuleusement toute saleté, tout contaminant, et en particulier les oxydes qui peuvent s'être formés à la surface du matériau cible. Les oxydes sont particulièrement problématiques car ils peuvent se décomposer dans les conditions de pulvérisation à haute énergie, libérant des gaz qui peuvent provoquer des arcs localisés et l'inflammation.
Plusieurs méthodes peuvent être employées pour garantir une propreté parfaite :
- Nettoyage mécanique: Utilisation de brosses ou de matériaux abrasifs pour éliminer physiquement les contaminants de surface.
- Nettoyage chimique: L'immersion de la cible dans des solvants ou des acides spécifiques qui peuvent dissoudre les oxydes et autres impuretés.
- Nettoyage par ultrasons: Utilisation d'ondes ultrasoniques pour déloger et éliminer les particules incrustées dans la surface.
- Nettoyage par faisceau d'ions: Bombardement de la surface de la cible avec un faisceau d'ions pour éliminer les contaminants au niveau atomique.
Le choix de la méthode de nettoyage dépend de la nature des contaminants et des exigences spécifiques du processus de pulvérisation. Quelle que soit la méthode utilisée, l'objectif est d'obtenir une surface vierge de toute substance susceptible d'interférer avec le processus de pulvérisation ou de provoquer des étincelles indésirables. Cette préparation méticuleuse garantit que le matériau cible est dans des conditions optimales pour le dépôt d'un film mince de haute qualité.
Contrôle de l'atmosphère de la chambre à vide
Il est essentiel de maintenir l'atmosphère dans une plage contrôlable afin d'éviter que la concentration d'oxygène et d'autres gaz n'atteigne un niveau inflammable. Il s'agit de créer et de maintenir une atmosphère modifiée dans la chambre à vide, ce qui peut réduire considérablement le risque d'étincelles dans le matériau cible pendant la pulvérisation magnétron.
Pour ce faire, il est essentiel de disposer d'un récipient étanche. Il peut s'agir d'un tube de travail avec des joints d'extrémité spécialisés conçus pour les fours tubulaires, ou d'une cornue couramment utilisée dans les fours à chambre. Ces récipients permettent d'isoler l'environnement interne des influences extérieures, ce qui permet un contrôle précis des conditions atmosphériques.
Le processus de mise sous vide d'un récipient réduit le nombre d'atomes et de molécules à l'intérieur. Toutefois, il est pratiquement impossible d'obtenir un vide parfait ; même dans un vide inférieur à 10-7 mbar, il reste environ 109 particules par centimètre cube. Cette présence résiduelle de gaz doit être gérée avec soin pour éviter toute accumulation de gaz inflammables.
KINTEK propose une gamme d'ensembles de gaz standard et d'équipements associés conçus pour aider à créer et à maintenir ces atmosphères modifiées. Ces produits sont non seulement polyvalents mais aussi adaptables, ce qui permet une plus grande flexibilité opérationnelle. Par exemple, l'équipement et les accessoires optionnels pour les atmosphères modifiées permettent d'utiliser les mêmes produits pour de multiples applications impliquant différents gaz, niveaux de vide ou même aucune atmosphère modifiée.
En contrôlant méticuleusement l'atmosphère de la chambre à vide, la probabilité d'inflammation du matériau cible pendant la pulvérisation magnétron peut être considérablement réduite, ce qui garantit un processus de revêtement plus sûr et plus efficace.
Définir des conditions de pulvérisation raisonnables
L'ajustement des conditions de pulvérisation est crucial pour prévenir l'inflammation et garantir les performances optimales du processus de pulvérisation magnétron. Les réglages spécifiques doivent être méticuleusement adaptés aux caractéristiques du matériau cible et aux spécifications de l'équipement. Il s'agit de régler avec précision des paramètres tels que les niveaux de puissance, les configurations du champ magnétique et les pressions de la chambre à vide.
Voici quelques exemples,niveaux de puissance doivent être soigneusement calibrés pour correspondre aux propriétés thermiques du matériau cible. Une puissance excessive peut provoquer une surchauffe, entraînant des arcs localisés et une inflammation, tandis qu'une puissance insuffisante peut ne pas vaporiser efficacement le matériau, ce qui se traduit par une mauvaise qualité du revêtement. De même,configurations du champ magnétique doivent être équilibrées pour créer une distribution uniforme du plasma, en évitant les décharges concentrées qui peuvent provoquer des étincelles.
En outre, le maintien d'unepression de la chambre à vide est essentielle. Une pression trop élevée peut permettre aux gaz résiduels d'interagir avec le matériau cible, provoquant des réactions indésirables et une inflammation potentielle. Inversement, une pression trop basse peut entraîner une formation inefficace du plasma, ce qui affecte le processus de pulvérisation.
En ajustant systématiquement ces conditions, les opérateurs peuvent réduire de manière significative le risque d'inflammation du matériau cible, garantissant ainsi un processus de pulvérisation stable et efficace.
Inspection régulière de l'équipement
L'inspection régulière de l'équipement est une pratique essentielle dans le contexte de la pulvérisation cathodique magnétron pour garantir la longévité et l'efficacité du processus. Cette maintenance de routine implique un examen approfondi de tous les composants, de la chambre à vide aux unités d'alimentation, afin d'identifier tout signe d'usure ou de dysfonctionnement. En respectant un calendrier d'inspection strict, les opérateurs peuvent détecter et traiter les problèmes potentiels avant qu'ils ne se transforment en problèmes plus importants.
L'un des principaux objectifs de ces inspections est de vérifier que toutes les pièces mécaniques fonctionnent correctement. Il s'agit notamment de vérifier qu'il n'y a pas de connexions desserrées, de composants mal alignés ou de signes de dommages physiques. En outre, les systèmes électriques doivent être examinés de près pour s'assurer qu'ils fonctionnent selon des paramètres sûrs, afin d'éviter tout court-circuit ou surtension susceptible d'entraîner une défaillance de l'équipement ou, pire encore, des risques pour la sécurité.
En outre, des inspections régulières permettent de maintenir l'intégrité de l'environnement sous vide à l'intérieur de la chambre. Toute fuite ou dégradation des joints de vide peut compromettre le processus de pulvérisation, entraînant un dépôt de film sous-optimal et des étincelles potentielles dans le matériau cible. En identifiant et en rectifiant rapidement ces problèmes, les opérateurs peuvent maintenir une atmosphère stable et contrôlée nécessaire à des applications de revêtement de haute qualité.
En résumé, l'inspection régulière de l'équipement n'est pas simplement une mesure préventive, mais un aspect essentiel pour assurer le fonctionnement continu et sûr de l'équipement de pulvérisation cathodique magnétron. Elle comprend une évaluation complète des composants mécaniques et électriques, garantissant que l'ensemble du système fonctionne comme prévu, minimisant ainsi le risque de formation d'étincelles dans le matériau cible et d'autres problèmes connexes.
CONTACTEZ-NOUS POUR UNE CONSULTATION GRATUITE
Les produits et services de KINTEK LAB SOLUTION ont été reconnus par des clients du monde entier. Notre personnel se fera un plaisir de répondre à toute demande que vous pourriez avoir. Contactez-nous pour une consultation gratuite et parlez à un spécialiste produit pour trouver la solution la plus adaptée aux besoins de votre application !