Les chambres de revêtement, en particulier celles utilisées dans les processus de dépôt sous vide, sont des systèmes sophistiqués conçus pour appliquer des couches minces, durables et protectrices sur diverses surfaces.Ces chambres fonctionnent sous vide pour vaporiser des matériaux métalliques solides, ce qui permet aux atomes vaporisés de pénétrer et de se lier à la surface du produit, formant ainsi un revêtement protecteur.Le processus comprend plusieurs éléments clés, chacun contribuant à la fonctionnalité et à l'efficacité globales du processus de revêtement.Comprendre comment ces composants fonctionnent ensemble permet d'appréhender la nature complexe mais précise de la technologie du revêtement sous vide.
Explication des points clés :
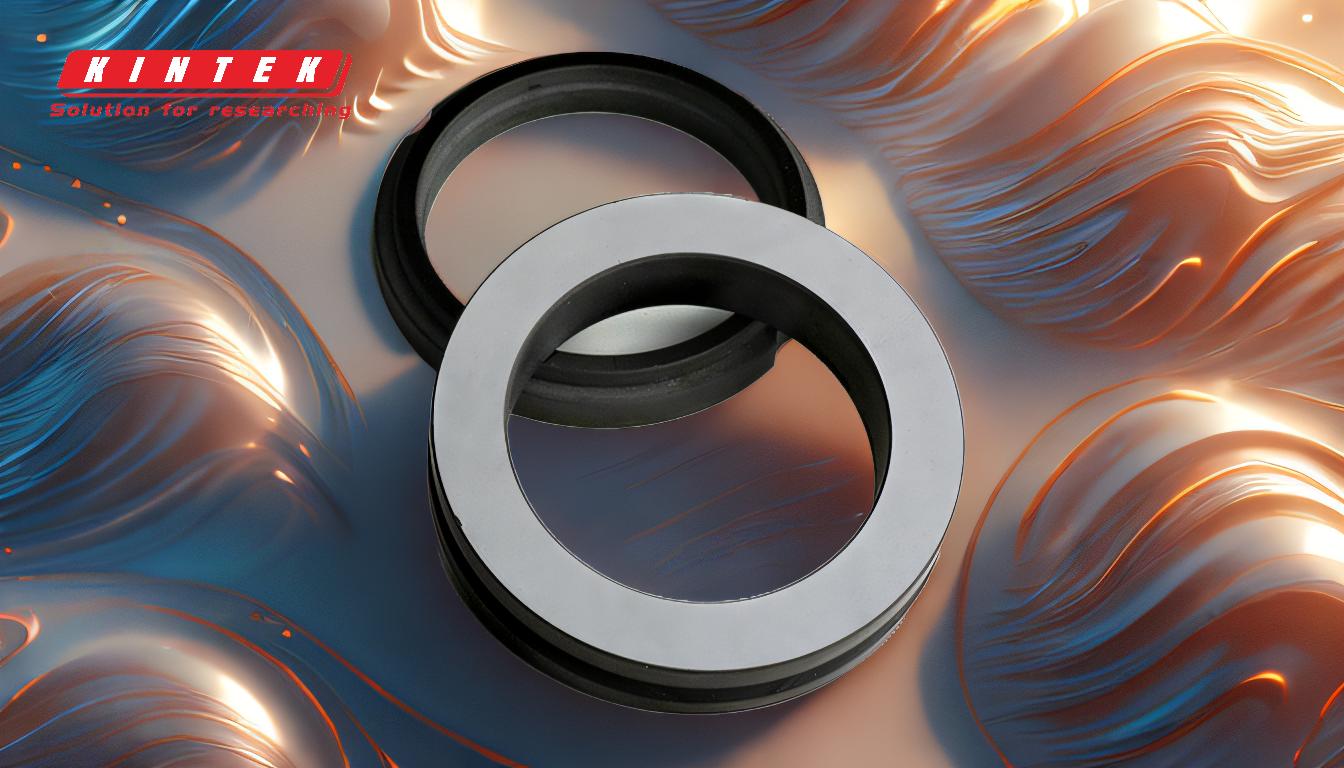
-
Chambre à vide et équipement de revêtement:
- La chambre à vide est l'élément central du processus de revêtement.Elle est conçue pour maintenir un vide poussé, essentiel à la vaporisation et au dépôt des matériaux.
- La chambre est généralement fabriquée dans des matériaux capables de résister à des températures et à des pressions élevées, ce qui garantit un environnement stable pour le processus de revêtement.
- À l'intérieur de la chambre, le produit à revêtir est placé et le matériau vaporisé est dirigé vers lui pour former la couche protectrice.
-
Pièce d'obtention du vide:
- Ce composant est responsable de la création et du maintien du vide à l'intérieur de la chambre.Il comprend des pompes et des vannes qui éliminent l'air et les autres gaz de la chambre.
- Le vide est crucial car il empêche la contamination et permet à la matière vaporisée de se déplacer sans entrave jusqu'à la surface du produit.
-
Mesure du vide:
- La mesure précise du niveau de vide est essentielle pour contrôler le processus de revêtement.Cette partie comprend des jauges et des capteurs qui surveillent la pression à l'intérieur de la chambre.
- Le maintien d'un niveau de vide correct garantit la qualité et l'homogénéité du revêtement.
-
Alimentation électrique:
- L'alimentation électrique fournit l'énergie nécessaire pour vaporiser le matériau métallique solide.Il peut s'agir d'alimentations haute tension pour les sources de pulvérisation ou d'évaporation.
- L'alimentation doit être stable et contrôlable pour garantir un dépôt précis du matériau de revêtement.
-
Système d'alimentation en gaz de procédé:
- Dans certains procédés de revêtement, des gaz spécifiques sont introduits dans la chambre pour améliorer le processus de dépôt ou modifier les propriétés du revêtement.
- Le système d'introduction des gaz contrôle le débit et la composition de ces gaz, qui peuvent influencer l'adhérence, la densité et d'autres caractéristiques du revêtement.
-
Transmission mécanique:
- Cette partie comprend les mécanismes permettant de déplacer et de positionner le produit dans la chambre.Elle garantit que le produit est enrobé de manière uniforme et que le matériau vaporisé est uniformément réparti.
- La précision du mouvement est cruciale pour obtenir une épaisseur et une qualité de revêtement constantes.
-
Équipement de chauffage et de mesure de la température:
- Le contrôle de la température est essentiel dans le processus de revêtement.Les éléments chauffants et les capteurs de température garantissent que la chambre et le produit sont maintenus à la température optimale pour le dépôt.
- Une bonne gestion de la température affecte le taux de vaporisation et la qualité du revêtement.
-
Source d'évaporation et de pulvérisation ionique:
- Ces sources sont utilisées pour vaporiser le matériau solide.L'évaporation ionique consiste à chauffer le matériau jusqu'à ce qu'il se vaporise, tandis que la pulvérisation cathodique utilise des ions à haute énergie pour arracher des atomes au matériau cible.
- Le choix de la source dépend du matériau utilisé et des propriétés souhaitées du revêtement.
-
Système de refroidissement à l'eau:
- Le processus de revêtement génère une chaleur importante, qui doit être gérée pour éviter d'endommager l'équipement et garantir des conditions de processus constantes.
- Le système de refroidissement à eau fait circuler de l'eau dans la chambre et les autres composants pour dissiper la chaleur et maintenir une température de fonctionnement stable.
En résumé, les chambres de revêtement sont des systèmes complexes qui intègrent divers composants pour obtenir des revêtements précis et de haute qualité.Chaque composant joue un rôle spécifique dans la création de l'environnement sous vide, la vaporisation du matériau de revêtement et la garantie d'un dépôt uniforme sur la surface du produit.Il est essentiel de comprendre ces composants et leurs fonctions pour optimiser le processus de revêtement et obtenir les propriétés protectrices et fonctionnelles souhaitées du revêtement.
Tableau récapitulatif :
Composant | Fonction |
---|---|
Chambre à vide et équipement de revêtement | Maintient un environnement sous vide poussé pour la vaporisation et le dépôt de matériaux. |
Pièce d'obtention du vide | Crée et maintient des conditions de vide pour éviter la contamination. |
Partie relative à la mesure du vide | Surveille et contrôle les niveaux de vide pour une qualité de revêtement constante. |
Partie alimentation | Fournit l'énergie nécessaire à la vaporisation des matériaux solides. |
Système d'alimentation en gaz de procédé | Introduit des gaz pour améliorer le dépôt ou modifier les propriétés du revêtement. |
Pièce de transmission mécanique | Assure un revêtement uniforme en positionnant le produit avec précision. |
Chauffage et mesure de la température | Maintient des températures optimales pour la vaporisation et la qualité du revêtement. |
Source d'évaporation et de pulvérisation ionique | Vaporise les matériaux pour le dépôt en utilisant la chaleur ou des ions à haute énergie. |
Système de refroidissement par eau | Dissipe la chaleur pour maintenir des conditions de fonctionnement stables. |
Optimisez votre processus de revêtement avec des systèmes de dépôt sous vide avancés. contactez nos experts dès aujourd'hui !