Le recuit est un processus de traitement thermique critique utilisé pour modifier les propriétés physiques et mécaniques des matériaux, principalement des métaux. Il est nécessaire dans des conditions spécifiques où le matériau doit être ramolli, rendu plus ductile ou débarrassé de ses contraintes internes. Ce processus est essentiel pour améliorer l'usinabilité, faciliter le travail à froid, améliorer les propriétés mécaniques ou électriques et assurer la stabilité dimensionnelle. Le recuit est particulièrement utile après les processus de fabrication tels que le moulage ou le travail à froid, où les contraintes internes et la dureté peuvent compromettre les performances du matériau. En chauffant le matériau jusqu'à sa température de recristallisation, en le maintenant à cette température, puis en le refroidissant à une vitesse contrôlée, le recuit permet d'obtenir une structure plus uniforme et plus facile à travailler.
Explication des points clés :
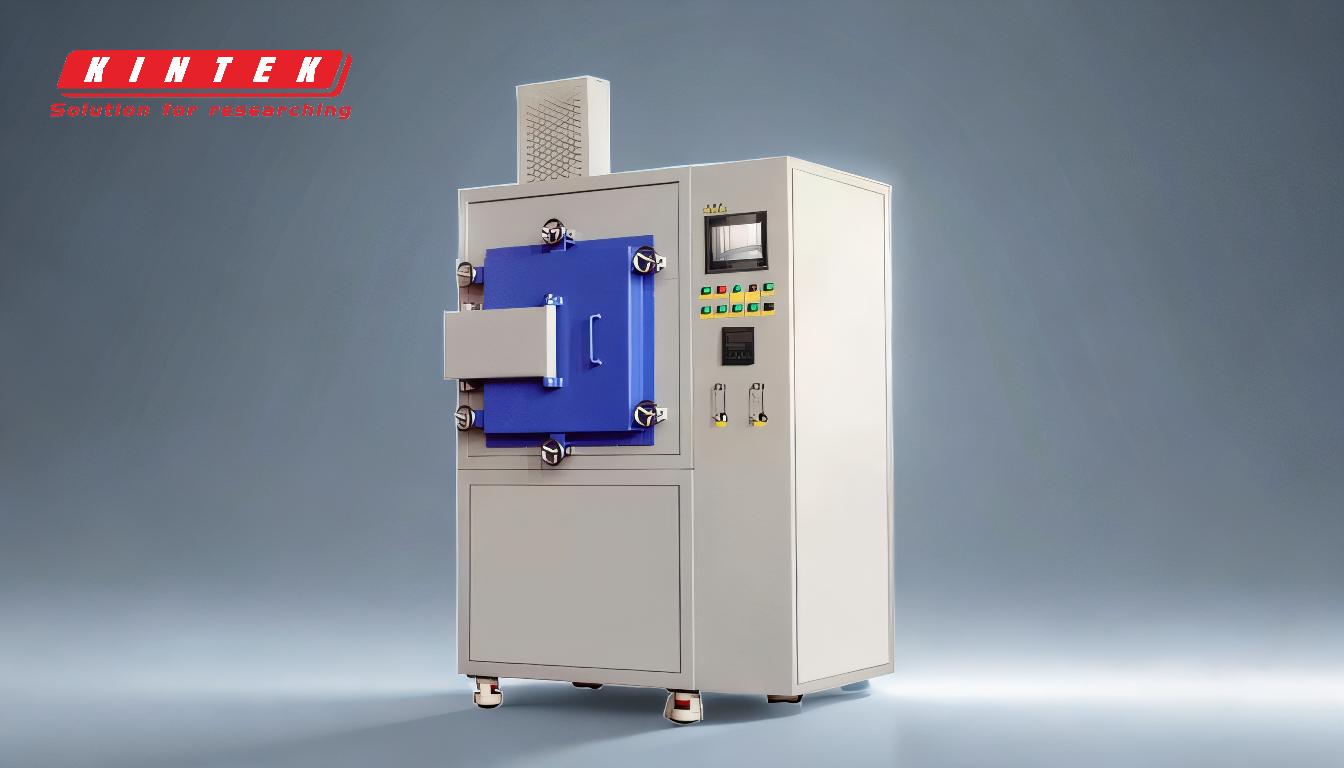
-
Réduction de la dureté et augmentation de la ductilité:
- Le recuit est principalement utilisé pour réduire la dureté d'un matériau, le rendant plus souple et plus ductile. Pour ce faire, le matériau est chauffé à une température spécifique (généralement sa température de recristallisation), puis il est lentement refroidi. Ce processus réduit le nombre de dislocations dans la structure cristalline, ce qui diminue la dureté et augmente la ductilité. Le matériau est ainsi plus facile à usiner, à travailler à froid ou à façonner sans risque de fissure ou de rupture sous contrainte.
-
Allègement des contraintes internes:
- Des contraintes internes peuvent se développer dans les matériaux au cours des processus de fabrication tels que le moulage, le soudage ou le travail à froid. Ces contraintes peuvent entraîner une défaillance ou une déformation du matériau au fil du temps. Le recuit aide à soulager ces contraintes en permettant au matériau d'atteindre une structure interne plus stable et plus uniforme. Ceci est particulièrement important pour les composants qui seront soumis à des charges mécaniques ou à des cycles thermiques en service.
-
Amélioration de l'usinabilité:
- Les matériaux trop durs peuvent être difficiles à usiner, ce qui entraîne une usure accrue des outils et de mauvais états de surface. Le recuit ramollit le matériau, ce qui le rend plus facile à couper, à percer ou à façonner. Cette opération est particulièrement bénéfique pour les métaux qui doivent subir des opérations d'usinage importantes, car elle réduit le risque de bris d'outil et améliore l'efficacité du processus d'usinage.
-
Facilitation du travail à froid:
- Les procédés d'usinage à froid, tels que le laminage, l'étirage ou le forgeage, peuvent augmenter considérablement la dureté et la résistance d'un matériau, mais aussi le rendre plus fragile. Le recuit est souvent effectué entre les étapes du travail à froid pour restaurer la ductilité et réduire la fragilité, ce qui permet de poursuivre le traitement sans risque de fissuration. Cette opération est cruciale pour la production de formes complexes ou de sections minces qui nécessitent plusieurs étapes de formage.
-
Amélioration des propriétés mécaniques et électriques:
- Le recuit peut améliorer les propriétés mécaniques d'un matériau, telles que sa résistance à la traction, sa ténacité et sa résistance à la fatigue, en affinant sa structure granulaire. En outre, pour les matériaux électriques comme le cuivre ou l'aluminium, le recuit peut améliorer la conductivité électrique en réduisant les défauts dans le réseau cristallin. Le matériau est ainsi mieux adapté aux applications où la résistance mécanique et les performances électriques sont essentielles.
-
Production d'une structure uniforme et homogène:
- Au cours de la fabrication, les matériaux peuvent développer des microstructures non uniformes en raison d'un refroidissement inégal ou d'une déformation mécanique. Le recuit permet de produire une structure interne plus uniforme et homogène en permettant au matériau de recristalliser et de former des grains équiaxes. Cette uniformité améliore les performances globales et la fiabilité du matériau, en particulier dans les applications où l'uniformité est essentielle.
-
Remise en état des matériaux à l'état "mou":
- Après des processus tels que le travail à froid ou le traitement thermique, les matériaux peuvent devenir trop durs ou trop fragiles pour être traités ultérieurement. Le recuit ramène le matériau à un état plus souple, ce qui facilite les opérations supplémentaires d'usinage, de formage ou de traitement thermique. Ceci est particulièrement important pour les matériaux qui doivent subir plusieurs étapes de traitement pour obtenir les propriétés finales souhaitées.
-
Stabilité dimensionnelle:
- Le recuit peut contribuer à améliorer la stabilité dimensionnelle d'un matériau en réduisant les contraintes résiduelles qui peuvent provoquer des déformations ou des distorsions au fil du temps. Ceci est particulièrement important pour les composants de précision qui doivent maintenir des tolérances serrées pendant leur durée de vie.
En résumé, le recuit est nécessaire dans les cas où les matériaux doivent être ramollis, rendus plus ductiles ou débarrassés de leurs contraintes internes. Il s'agit d'un processus polyvalent qui améliore l'usinabilité, facilite le travail à froid, améliore les propriétés mécaniques et électriques et garantit la stabilité dimensionnelle, ce qui le rend indispensable dans diverses applications de fabrication et d'ingénierie.
Tableau récapitulatif :
Principaux avantages du recuit | Description |
---|---|
Réduction de la dureté | Ramollit les matériaux, les rendant plus ductiles et plus faciles à usiner ou à façonner. |
Allègement des contraintes internes | Réduit les contraintes internes causées par les processus de fabrication tels que le moulage ou le soudage. |
Amélioration de l'usinabilité | Facilite la coupe, le perçage ou le façonnage et réduit l'usure de l'outil. |
Facilitation du travail à froid | Restaure la ductilité entre les étapes de l'usinage à froid, évitant ainsi les fissures. |
Propriétés mécaniques améliorées | Améliore la résistance à la traction, la ténacité et la résistance à la fatigue. |
Microstructure uniforme | Produit une structure interne homogène pour une meilleure cohérence. |
Remise en état à l'état souple | Préparer les matériaux pour un traitement ultérieur après le durcissement. |
Stabilité dimensionnelle | Réduit le gauchissement ou la distorsion, garantissant des tolérances serrées. |
Besoin de solutions de recuit pour vos matériaux ? Contactez nos experts dès aujourd'hui pour en savoir plus !