Le recuit, bien que bénéfique pour améliorer les propriétés des matériaux telles que la ductilité et réduire les contraintes internes, présente certains inconvénients. Un inconvénient majeur est son impact sur les propriétés mécaniques, en particulier dans des matériaux comme l'acier pour pipelines X80. Par exemple, un recuit à faible teneur en hydrogène à 200 °C pendant 12 heures modifie la courbe contrainte-déformation, entraînant une augmentation de la limite d'élasticité mais un allongement réduit. Cela se produit en raison de la diffusion d'atomes de carbone dans les sites interstitiels de dislocations, formant une atmosphère de Cottrell qui fixe les dislocations, réduisant ainsi la densité des dislocations mobiles. De tels changements peuvent compromettre les performances du matériau dans des applications spécifiques, soulignant la nécessité d'un examen attentif des paramètres de recuit.
Points clés expliqués :
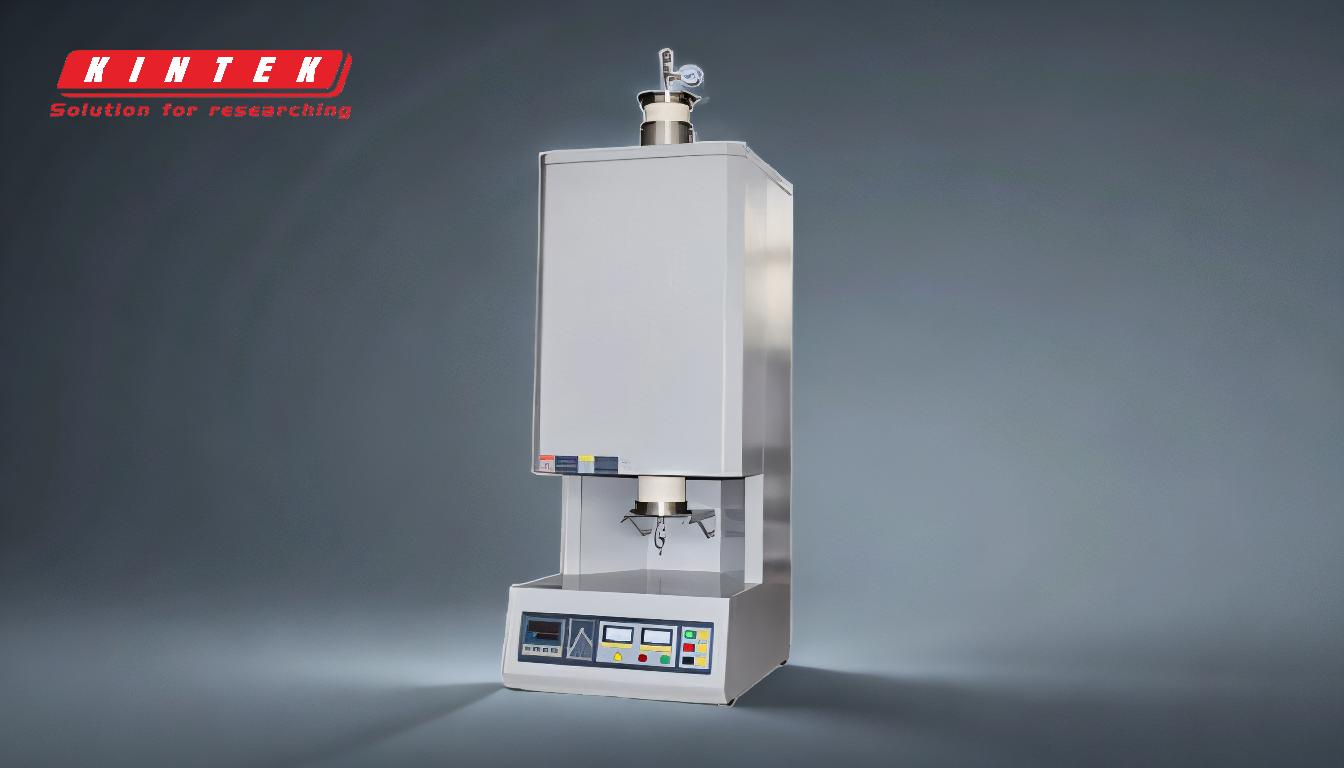
-
Modification des propriétés mécaniques:
- Augmentation de la limite d'élasticité: Le recuit peut conduire à une augmentation de la limite d'élasticité, comme on le voit dans l'acier pour pipelines X80, où elle augmente d'environ 10 %. Cela peut sembler bénéfique, mais cela peut aussi rendre le matériau plus cassant.
- Réduction de l'allongement: L'allongement du matériau diminue d'environ 20%, indiquant une perte de ductilité. Cette réduction peut être préjudiciable dans les applications nécessitant une flexibilité matérielle.
-
Formation de l'atmosphère de Cottrell:
- Diffusion d'atomes de carbone: Lors du recuit, les atomes de carbone diffusent dans les sites interstitiels des dislocations. Ce processus forme ce que l'on appelle une atmosphère de Cottrell.
- Épinglage des luxations: L'atmosphère de Cottrell fixe les dislocations en place, ce qui réduit la densité des dislocations mobiles. Cet effet d'épinglage est responsable des changements observés dans les propriétés mécaniques.
-
Impact sur les performances des matériaux:
- Ductilité réduite: La diminution de l'allongement signifie une réduction de la capacité du matériau à se déformer plastiquement avant la fracture, ce qui peut constituer un inconvénient critique dans de nombreuses applications d'ingénierie.
- Fragilité potentielle: Même si une limite d'élasticité accrue peut être souhaitable dans certains contextes, cela se fait souvent au prix d'une fragilité accrue, rendant le matériau plus sujet à la fissuration sous contrainte.
-
Considérations relatives à la candidature:
- Exigences spécifiques à l'application: Les inconvénients du recuit doivent être mis en balance avec les exigences spécifiques de l'application. Par exemple, dans les applications où la ductilité est cruciale, la réduction de l’allongement peut s’avérer inacceptable.
- Optimisation des paramètres de recuit: Pour pallier ces inconvénients, il est essentiel d'optimiser les paramètres de recuit tels que la température et la durée. Cette optimisation peut aider à atteindre un équilibre entre des propriétés mécaniques améliorées et des effets indésirables minimes.
En résumé, si le recuit peut améliorer certaines propriétés des matériaux, il présente également des inconvénients importants, notamment concernant les performances mécaniques. Comprendre ces inconvénients est crucial pour prendre des décisions éclairées en matière de traitement et d’application des matériaux.
Tableau récapitulatif :
Inconvénient | Description |
---|---|
Force d'élasticité accrue | La limite d'élasticité augmente d'environ 10 %, mais peut conduire à une fragilité. |
Allongement réduit | L'allongement diminue d'environ 20 %, réduisant ainsi la ductilité et la flexibilité. |
Ambiance Cottrell | Les atomes de carbone épinglent les luxations, réduisant les luxations mobiles et modifiant les propriétés. |
Fragilité potentielle | Une limite d'élasticité plus élevée peut rendre les matériaux sujets à la fissuration sous contrainte. |
Limites des applications | Une ductilité réduite peut ne pas convenir aux applications nécessitant une flexibilité matérielle. |
Besoin d'aide pour optimiser les processus de recuit de vos matériaux ? Contactez nos experts dès aujourd'hui pour des solutions sur mesure !