Les fours à induction, bien que très efficaces et polyvalents pour la fusion des métaux, présentent plusieurs inconvénients notables.L'un des principaux inconvénients est leur manque de capacité d'affinage, ce qui signifie que les matériaux de charge doivent déjà être exempts d'oxydes et avoir une composition connue.En outre, certains éléments d'alliage peuvent être perdus en raison de l'oxydation au cours du processus de fusion, ce qui nécessite de les ajouter à nouveau.Ces limitations peuvent accroître la complexité et les coûts des opérations.Nous examinons ci-dessous ces inconvénients et d'autres en détail.
Explication des principaux points :
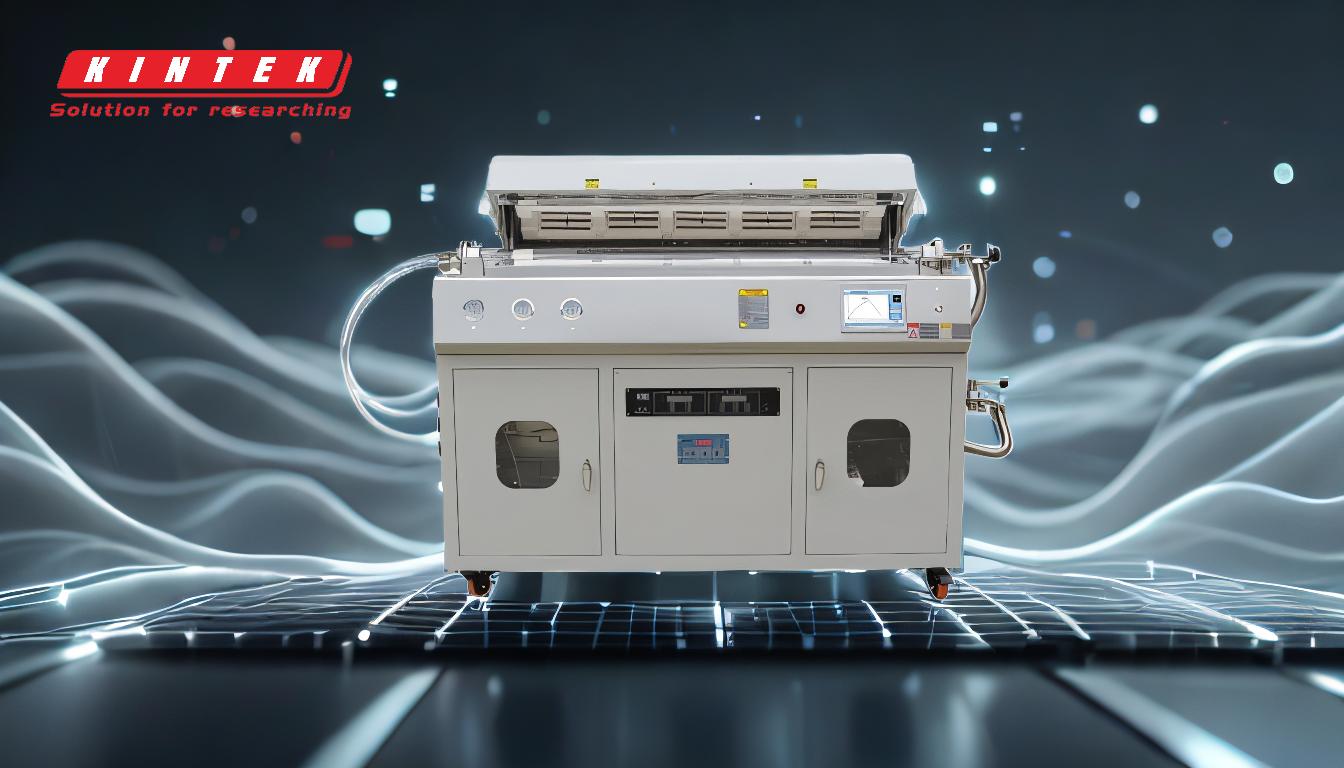
-
Absence de capacité d'affinage
- Les fours à induction n'ont pas la capacité d'affiner le métal pendant le processus de fusion.Cela signifie que les matériaux de charge doivent être propres, exempts d'oxydes et d'une composition connue avant d'être introduits dans le four.
- Pour les industries nécessitant des métaux de haute pureté, cette limitation peut constituer un inconvénient important, car elle nécessite des étapes de prétraitement supplémentaires pour garantir la qualité des matériaux de charge.
-
Oxydation et perte d'éléments d'alliage
- Au cours du processus de fusion, certains éléments d'alliage, tels que le magnésium, l'aluminium et le silicium, peuvent s'oxyder et se perdre dans la masse fondue.
- Les opérateurs doivent alors surveiller attentivement la composition de la matière fondue et ajouter à nouveau ces éléments, ce qui peut augmenter à la fois les coûts des matériaux et le temps de traitement.
-
Dépendance à l'égard de la qualité des matériaux de charge
- Comme les fours à induction dépendent de la qualité des matériaux de charge, toute impureté ou incohérence dans la matière première peut avoir une incidence directe sur le produit final.
- Il est donc difficile d'utiliser des matériaux de rebut ou recyclés sans un tri et une préparation minutieux, ce qui peut augmenter les coûts d'exploitation.
-
Investissement initial et coûts d'exploitation élevés
- Les fours à induction, en particulier ceux qui utilisent des technologies avancées telles que les fours à induction à fours à induction IGBT Les fours à induction IGBT nécessitent un investissement initial important.
- En outre, les coûts d'exploitation, y compris la consommation d'électricité et la maintenance, peuvent être plus élevés que pour d'autres types de fours.
-
Capacité limitée pour la production à grande échelle
- Les fours à induction sont généralement mieux adaptés aux opérations à petite échelle ou à la production par lots.Pour une production continue à grande échelle, d'autres types de fours, tels que les fours à arc, peuvent être plus efficaces.
- Cette limitation peut rendre les fours à induction moins adaptés aux industries nécessitant une production en grande quantité.
-
Complexité du contrôle de la température
- Bien que les fours à induction permettent un contrôle précis de la température, il peut être difficile de maintenir des températures constantes tout au long de la fusion, en particulier pour les fours de grande taille.
- Les variations de température peuvent entraîner des incohérences dans le produit final, ce qui nécessite une surveillance et un ajustement minutieux.
-
Susceptibilité aux problèmes d'alimentation électrique
- Les fours à induction dépendent fortement d'une alimentation électrique stable et fiable.Toute fluctuation ou interruption de l'alimentation peut perturber le processus de fusion et potentiellement endommager le four.
- Ils sont donc moins adaptés aux régions où l'infrastructure électrique n'est pas fiable.
-
Flexibilité limitée pour certains métaux
- Bien que les fours à induction soient polyvalents, ils peuvent ne pas être idéaux pour la fusion de certains métaux ou alliages qui nécessitent des processus d'affinage ou des atmosphères spécifiques.
- Par exemple, les métaux qui nécessitent un environnement sous vide ou sous gaz inerte peuvent ne pas convenir aux fours à induction standard.
-
Entretien et usure des composants
- Les composants d'un four à induction, tels que le creuset et les bobines, sont sujets à l'usure au fil du temps.
- Un entretien régulier est nécessaire pour garantir des performances optimales, et le remplacement de ces composants peut s'avérer coûteux.
-
Problèmes d'environnement et de sécurité
- Les fours à induction génèrent des champs électromagnétiques qui peuvent présenter des risques pour la sécurité des opérateurs s'ils ne sont pas correctement protégés.
- En outre, le processus de fusion peut produire des fumées et des émissions, ce qui nécessite une ventilation et des contrôles environnementaux adéquats.
En résumé, si les fours à induction offrent de nombreux avantages, tels que l'efficacité énergétique et le contrôle précis de la température, leurs inconvénients - notamment le manque de capacité d'affinage, l'oxydation des éléments d'alliage et les coûts opérationnels élevés - doivent être soigneusement pris en compte lors de la sélection d'un four pour des applications spécifiques.Pour les industries nécessitant des métaux de grande pureté ou une production à grande échelle, d'autres types de fours peuvent être plus appropriés.
Tableau récapitulatif :
Inconvénient | Description de la situation |
---|---|
Manque de capacité d'affinage | Ne peut pas affiner les métaux ; nécessite des matériaux de charge propres et exempts d'oxyde. |
Oxydation des éléments d'alliage | Perte d'éléments tels que le magnésium, l'aluminium et le silicium pendant la fusion. |
Dépendance à l'égard de la qualité de la charge | Les impuretés dans les matières premières affectent la qualité du produit final. |
Coûts initiaux et opérationnels élevés | Investissement important et coûts d'électricité et de maintenance plus élevés. |
Capacité limitée à grande échelle | Mieux adapté à la production à petite échelle ou par lots, et non à la production continue à grande échelle. |
Contrôle complexe de la température | Il est difficile de maintenir des températures constantes dans les grands fours. |
Sensibilité à l'alimentation électrique | Nécessite une alimentation stable ; les interruptions peuvent perturber les opérations. |
Flexibilité limitée des métaux | Pas idéal pour les métaux nécessitant un affinage spécifique ou des atmosphères contrôlées. |
Usure et entretien des composants | Un entretien régulier et des remplacements de composants coûteux sont nécessaires. |
Risques pour l'environnement et la sécurité | Les champs électromagnétiques et les fumées nécessitent un blindage et une ventilation appropriés. |
Vous avez besoin d'aide pour choisir le four le mieux adapté à vos besoins ? Contactez nos experts dès aujourd'hui pour des conseils personnalisés !