Le revêtement réfractaire des fours est un élément essentiel conçu pour résister aux températures élevées, fournir une isolation thermique et protéger la structure du four.Les matériaux utilisés dans ces revêtements varient en fonction de l'application spécifique et des exigences du processus.Les matériaux courants comprennent l'alumine à haute résistance, le carbure de silicium, la fibre d'alumine de haute pureté, les matériaux fibreux formés sous vide, les plaques creuses et légères d'oxyde d'aluminium et les briques spécialisées comme l'alumine à faible teneur en fer, l'étain de magnésium et la magnésite.Ces matériaux sont choisis pour leur capacité à offrir des températures de service élevées, une résistance rapide à la chaleur et au froid, un faible stockage de la chaleur et une excellente isolation thermique, garantissant ainsi un fonctionnement efficace et durable du four.
Explication des points clés :
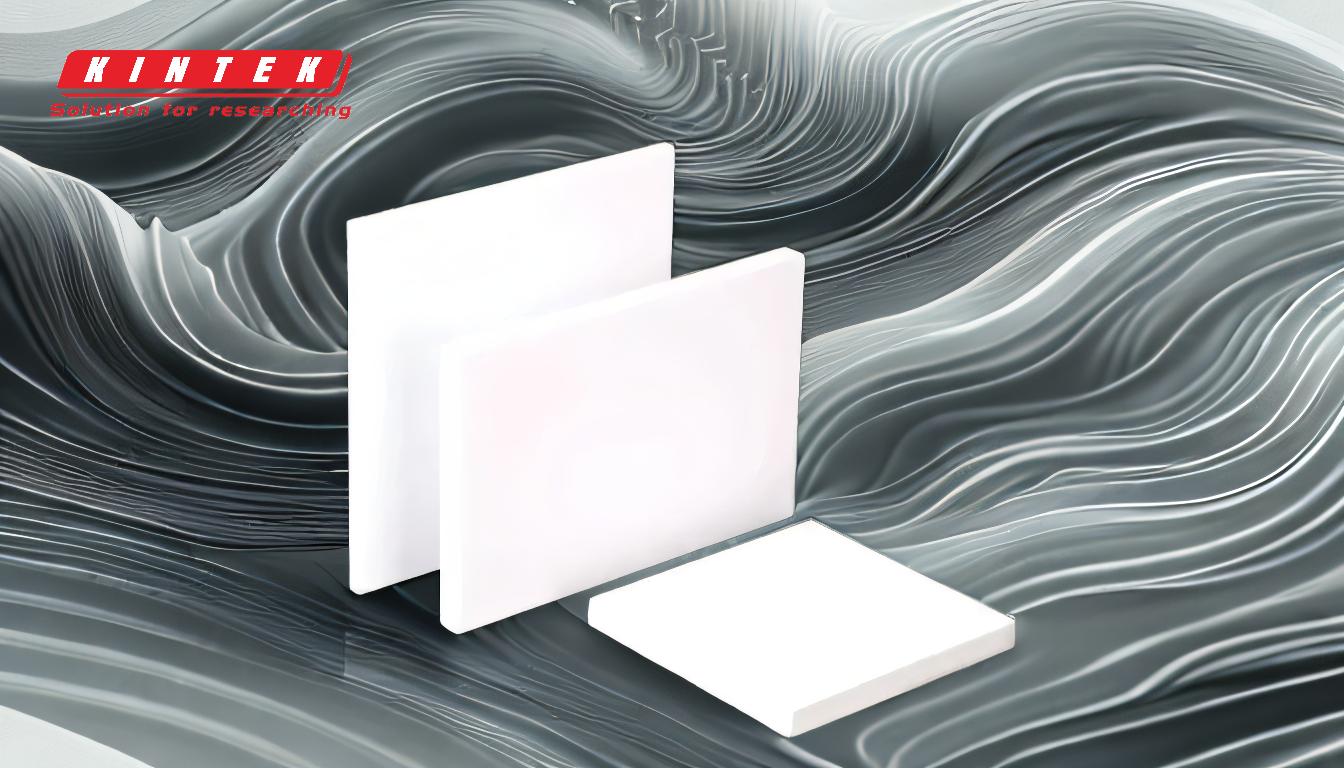
-
Alumine à haute résistance (Al₂O₃) :
- L'alumine haute résistance est un matériau largement utilisé dans les revêtements réfractaires en raison de son excellente stabilité thermique, de sa résistance mécanique et de sa résistance à la corrosion chimique.
- Elle est particulièrement efficace dans les fours à moufle, où elle garantit des conditions de traitement précises et uniformes en maintenant des températures constantes.
- Le point de fusion élevé de l'alumine (plus de 2000°C) la rend adaptée aux applications impliquant une chaleur extrême.
-
Carbure de silicium (SiC) :
- Le carbure de silicium est un autre matériau clé utilisé dans les revêtements réfractaires, en particulier dans les briques réfractaires isolantes.
- Il offre une conductivité thermique supérieure, une résistance élevée aux chocs thermiques et une excellente résistance mécanique, ce qui le rend idéal pour les fours qui subissent des changements de température rapides.
- Le SiC est souvent utilisé en combinaison avec d'autres matériaux pour améliorer les performances globales du revêtement réfractaire.
-
Fibre d'alumine de haute pureté :
- La fibre d'alumine de haute pureté est un matériau léger et résistant aux températures élevées, utilisé pour le revêtement des fours.
- Elle offre une excellente isolation thermique, réduit la capacité de stockage de la chaleur et permet un chauffage et un refroidissement rapides sans fissuration ni scories.
- Ce matériau est souvent utilisé dans les revêtements en fibres formées sous vide, qui sont connus pour leur durabilité et leur efficacité.
-
Matériaux à base de fibres formées sous vide :
- Ces matériaux sont créés en formant des fibres sous vide, ce qui permet d'obtenir un revêtement réfractaire léger et hautement isolant.
- Ils sont composés de fibres d'alumine de haute pureté et d'autres composants, offrant une combinaison de température de service élevée et de faible perte de chaleur.
- Les revêtements formés sous vide sont particulièrement efficaces pour réduire la consommation d'énergie et améliorer l'efficacité des fours.
-
Plaques creuses légères d'oxyde d'aluminium :
- Les plaques creuses légères d'oxyde d'aluminium sont utilisées dans les revêtements de four pour leurs excellentes propriétés d'isolation thermique et leur faible capacité de stockage de la chaleur.
- Ces plaques sont conçues pour résister à des températures élevées et à des cycles thermiques rapides sans se fissurer ni se dégrader.
- Elles sont souvent utilisées dans les conceptions d'isolation multicouche pour améliorer les performances thermiques globales du four.
-
Briques spécialisées (alumine à faible teneur en fer, magnésium-épingle, magnésite) :
-
Le choix des briques spécialisées dépend du processus spécifique réalisé dans le four.Par exemple, les briques d'alumine à faible teneur en fer
- Briques d'alumine à faible teneur en fer : Utilisées dans les fours de réduction du minerai de fer en raison de leur grande pureté et de leur résistance aux attaques chimiques.
- Briques de magnésium et d'épingle : Connues pour leur excellente résistance aux chocs thermiques et leur stabilité à haute température, elles conviennent aux environnements difficiles.
- Briques de magnésite : Couramment utilisées dans les fours à ciment pour leur capacité à résister aux températures élevées et à la corrosion chimique.
-
Le choix des briques spécialisées dépend du processus spécifique réalisé dans le four.Par exemple, les briques d'alumine à faible teneur en fer
-
Isolation multicouche :
- Les revêtements réfractaires utilisent souvent une conception d'isolation multicouche, combinant des fibres céramiques d'alumine légères avec des panneaux d'isolation de haute qualité.
- Cette conception garantit une faible perte de chaleur, une faible consommation d'énergie et une meilleure efficacité thermique.
- L'absence de composants en amiante dans ces modèles les rend plus sûrs et plus respectueux de l'environnement.
-
Avantages fonctionnels des revêtements réfractaires :
- Isolation thermique : Les matériaux réfractaires offrent une excellente isolation, réduisant les pertes de chaleur et améliorant l'efficacité énergétique.
- Protection mécanique : Ils protègent l'enveloppe du four des températures élevées et de l'usure mécanique, prolongeant ainsi la durée de vie du four.
- Résistance chimique : Les revêtements réfractaires résistent aux réactions chimiques avec les matériaux traités, ce qui garantit des performances constantes.
- Résistance aux chocs thermiques : Les matériaux tels que le carbure de silicium et la fibre d'alumine de haute pureté peuvent supporter des changements de température rapides sans se fissurer ni se dégrader.
En sélectionnant et en combinant soigneusement ces matériaux, les fabricants de fours peuvent créer des revêtements réfractaires qui répondent aux besoins spécifiques de leurs processus, garantissant des performances, une durabilité et une efficacité optimales.
Tableau récapitulatif :
Matériau | Propriétés principales | Applications |
---|---|---|
Alumine à haute résistance | Stabilité thermique, résistance mécanique, résistance à la corrosion chimique | Fours à moufle, environnements de chaleur extrême |
Carbure de silicium | Conductivité thermique, résistance aux chocs thermiques, résistance mécanique | Fours avec changements rapides de température |
Fibre d'alumine de haute pureté | Légèreté, résistance aux hautes températures, isolation thermique | Revêtements en fibres formées sous vide |
Fibre formée sous vide | Légèreté, haute isolation, faible perte de chaleur | Revêtements de four à haut rendement énergétique |
Plaques creuses légères d'oxyde d'aluminium | Isolation thermique, faible accumulation de chaleur, résistance aux cycles thermiques rapides | Conceptions d'isolation multicouches |
Briques spécialisées | Grande pureté, résistance chimique, résistance aux chocs thermiques | Réduction du minerai de fer, fours à ciment, environnements difficiles |
Optimisez les performances de votre four avec le revêtement réfractaire adéquat... contactez nos experts dès aujourd'hui !