Le procédé de revêtement PVD (Physical Vapor Deposition) est une méthode sophistiquée utilisée pour appliquer des revêtements minces, durables et très adhérents sur divers substrats.Le processus comprend généralement plusieurs étapes critiques, notamment la préparation du substrat, la création d'un environnement sous vide poussé, la vaporisation du matériau cible, le transport des atomes vaporisés, la réaction avec des gaz si nécessaire et le dépôt sur le substrat.Ces étapes garantissent la formation d'un revêtement uniforme et de haute qualité qui améliore les propriétés du substrat, telles que la résistance à l'usure, la résistance à la corrosion et l'attrait esthétique.Les étapes clés et leur importance sont expliquées en détail ci-dessous.
Explication des points clés :
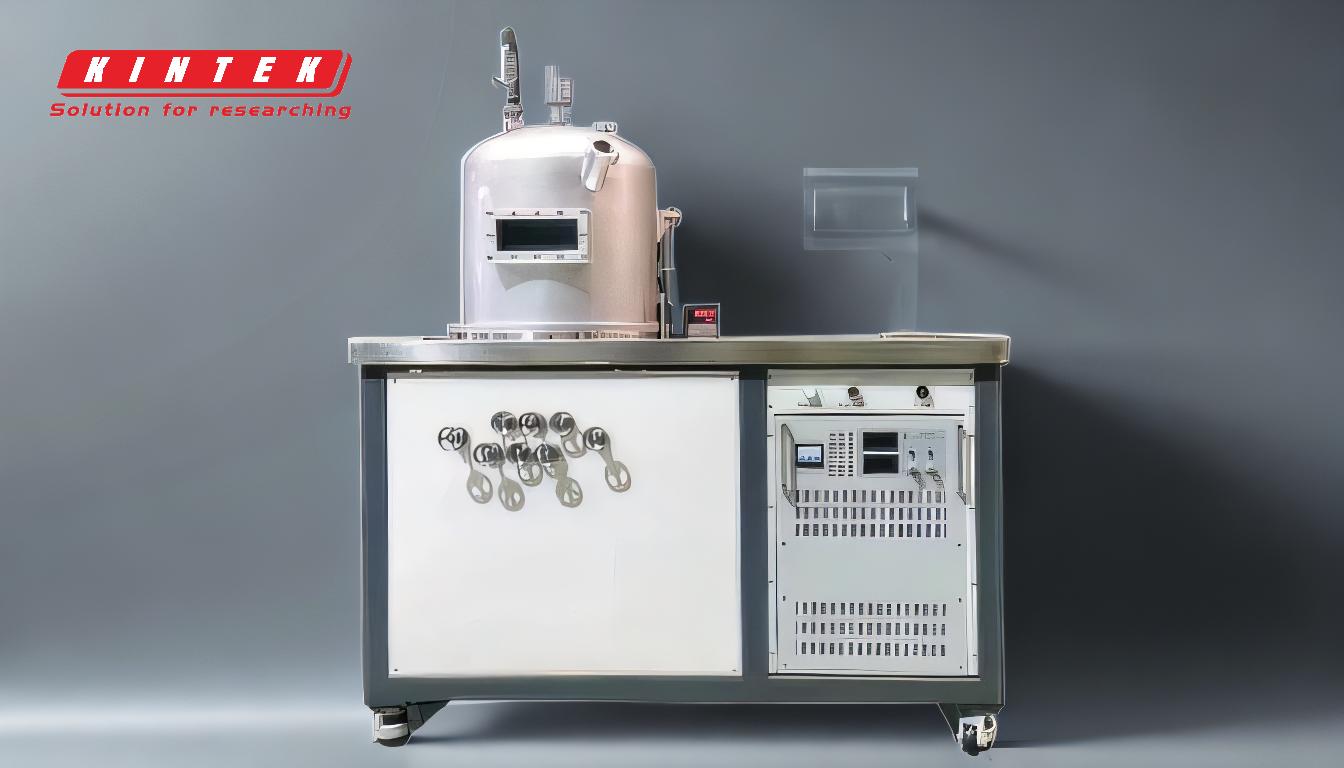
-
Préparation du support
- Nettoyage:Le substrat doit être soigneusement nettoyé afin d'éliminer tous les contaminants, tels que les huiles, la poussière ou les oxydes, qui pourraient nuire à l'adhérence du revêtement.Cette opération est généralement réalisée à l'aide d'un nettoyage chimique, d'un nettoyage par ultrasons ou d'un nettoyage au plasma.
- Prétraitement:Les processus de prétraitement, tels que la gravure ionique ou l'activation de surface, sont souvent employés pour améliorer l'énergie de surface du substrat et renforcer l'adhérence du revêtement.
-
Création d'un environnement sous vide poussé
- Le substrat et le matériau cible sont placés dans une chambre à vide, qui est ensuite évacuée pour créer un environnement sous vide poussé.Cette étape est cruciale pour éviter la contamination par les gaz atmosphériques et garantir un processus de dépôt propre.
- La pression du vide est soigneusement contrôlée et maintenue tout au long du processus afin d'optimiser les conditions de vaporisation et de dépôt.
-
Vaporisation du matériau cible
- Le matériau cible (par exemple, le titane, le chrome ou l'aluminium) est bombardé par des sources de haute énergie, telles que des électrons, des ions ou des photons, afin de déloger les atomes de sa surface.Ce processus est connu sous le nom d'évaporation ou d'ablation.
- Les atomes vaporisés forment un nuage de matière dans la chambre à vide, prêt à être transporté vers le substrat.
-
Transport des atomes vaporisés
- Les atomes vaporisés sont transportés du matériau cible au substrat à travers la chambre à vide.Cette étape est essentielle pour assurer une distribution uniforme du matériau de revêtement.
- Le processus de transport est influencé par des facteurs tels que la géométrie de la chambre, la distance entre la cible et le substrat et l'énergie des atomes vaporisés.
-
Réaction avec les gaz (facultatif)
- Dans certains cas, les atomes de métal vaporisés réagissent avec des gaz introduits, tels que l'azote, l'oxygène ou l'acétylène, pour former des composés tels que des nitrures, des oxydes ou des carbures métalliques.Cette étape est essentielle pour créer des propriétés de revêtement spécifiques, telles que la dureté ou la couleur.
- La réaction est soigneusement contrôlée pour obtenir la composition chimique et les caractéristiques de revêtement souhaitées.
-
Dépôt sur le substrat
- Les atomes ou composés vaporisés se condensent sur le substrat, formant un film mince et uniforme.Le processus de dépôt est influencé par des facteurs tels que la température du substrat, la vitesse de dépôt et l'énergie des atomes entrants.
- Le revêtement se lie fortement au substrat, créant une couche durable et adhérente qui améliore les performances du substrat.
-
Procédés de post-dépôt
- Purge:Après le dépôt, la chambre est purgée avec des gaz inertes, tels que l'argon, afin d'éliminer toute vapeur résiduelle et d'éviter toute contamination.
- Finition:Des procédés de finition supplémentaires, tels que le polissage ou le recuit, peuvent être appliqués pour améliorer l'aspect ou les performances du revêtement.
- Contrôle de la qualité:Le substrat revêtu est soumis à des contrôles de qualité rigoureux pour s'assurer que le revêtement répond aux spécifications en matière d'épaisseur, d'adhérence et d'autres propriétés.
En suivant ces étapes, le procédé de revêtement PVD produit des revêtements de haute qualité qui sont largement utilisés dans des secteurs tels que l'aérospatiale, l'automobile, les appareils médicaux et l'électronique grand public.La précision et la polyvalence de ce procédé en font une méthode privilégiée pour appliquer des revêtements fonctionnels et décoratifs sur une large gamme de matériaux.
Tableau récapitulatif :
Étape | Description de l'étape |
---|---|
1.Préparation du substrat | - Nettoyage :Élimine les contaminants pour une meilleure adhérence. |
- Prétraitement :Améliore l'énergie de surface pour une meilleure adhérence du revêtement. | |
2.Environnement à vide poussé | - Crée un environnement sans contamination pour le dépôt. |
3.Vaporisation | - Le matériau cible est vaporisé à l'aide de sources à haute énergie. |
4.Transport | - Les atomes vaporisés sont transportés vers le substrat pour une distribution uniforme. |
5.Réaction avec les gaz | - Étape facultative pour créer des propriétés de revêtement spécifiques (par exemple, dureté, couleur). |
6.Dépôt | - Les atomes se condensent sur le substrat, formant un revêtement durable et adhérent. |
7.Post-dépôt | - La purge, la finition et le contrôle de la qualité garantissent que le revêtement est conforme aux spécifications. |
Découvrez comment le procédé de revêtement PVD peut améliorer les performances de votre produit. contactez-nous dès aujourd'hui pour obtenir des conseils d'experts !