Les fours discontinus et les fours continus diffèrent considérablement par leur fonctionnement, leur conception et leurs applications. Les fours discontinus sont des systèmes fermés qui traitent les matériaux en groupes, ce qui les rend adaptés aux environnements de salles blanches et aux atmosphères inertes. Ils sont plus simples, plus faciles à entretenir et ont des coûts initiaux et opérationnels inférieurs. Cependant, ils nécessitent plus de préparation pour le chargement et ont souvent besoin d'accessoires tels que des paniers ou des étagères. En revanche, les fours continus fonctionnent à température constante et les matériaux se déplacent à travers le four à une vitesse constante. Cette conception élimine le besoin de racks ou de paniers, réduit la consommation d'énergie et est idéale pour la production en grand volume. Cependant, ils sont plus complexes, plus coûteux et nécessitent un entretien fréquent. Le choix entre les deux dépend du volume de production, du type de matériau et des exigences spécifiques du traitement.
Points clés expliqués :
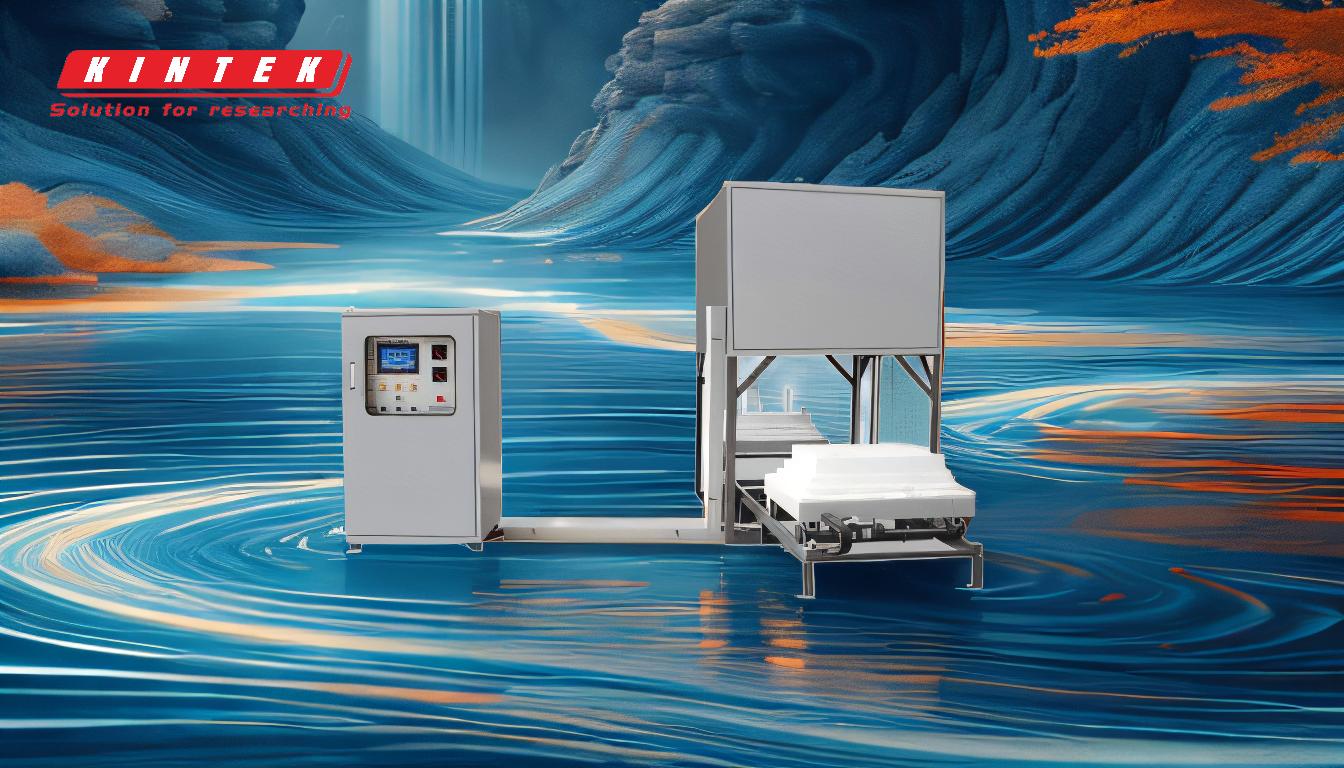
-
Fonctionnement et conception:
- Fours discontinus: Il s'agit de systèmes fermés où les matériaux sont traités par lots. Ils sont conçus pour gérer plusieurs rouleaux ou groupes de matériaux à la fois, nécessitant souvent des accessoires tels que des paniers ou des racks pour le chargement. Cette conception est idéale pour les applications nécessitant des normes de salle blanche ou des atmosphères inertes.
- Fours continus: Ceux-ci fonctionnent en déplaçant les matériaux à travers le four à une vitesse constante. Le four maintient une température constante et les matériaux sont traités en une seule couche, éliminant ainsi le besoin de supports ou de paniers. Cette conception est plus efficace pour la production en grand volume.
-
Complexité et maintenance:
- Fours discontinus: Ils sont moins complexes, ce qui les rend plus faciles à entretenir et à réparer. Leur conception plus simple contribue également à réduire les coûts initiaux et opérationnels.
- Fours continus: Ceux-ci sont plus complexes en raison de leur fonctionnement continu et de leur maintien à température constante. Cette complexité entraîne des exigences et des coûts de maintenance plus élevés.
-
Considérations relatives aux coûts:
- Fours discontinus: Généralement, les fours discontinus ont des coûts initiaux inférieurs et sont moins coûteux à exploiter au fil du temps. Cependant, ils nécessitent davantage de travail en cours pour préparer les matériaux au chargement.
- Fours continus: Ceux-ci ont des coûts initiaux et opérationnels plus élevés en raison de leur complexité et de la nécessité d’une maintenance fréquente. Cependant, ils peuvent être plus rentables pour la production en grand volume grâce à une consommation d’énergie réduite et à des temps de traitement plus rapides.
-
Efficacité énergétique:
- Fours discontinus: Bien qu'ils soient moins économes en énergie que les fours continus, leur simplicité et leurs coûts d'exploitation inférieurs peuvent compenser cet inconvénient dans certaines applications.
- Fours continus: Ceux-ci sont plus économes en énergie grâce à leur fonctionnement constant et à l'élimination du besoin de grilles ou de paniers, ce qui réduit les pertes de chaleur et la consommation d'énergie.
-
Adéquation des applications:
- Fours discontinus: Idéal pour les applications nécessitant un contrôle précis de l’environnement de traitement, telles que les normes de salle blanche ou les atmosphères inertes. Ils conviennent également aux petites séries de production ou au traitement de matériaux nécessitant une manipulation spécifique.
- Fours continus: Idéal pour la production en grand volume où les matériaux doivent être traités rapidement et efficacement. Ils sont couramment utilisés dans les industries où un traitement continu est essentiel, comme dans la production de treillis métalliques ou d'autres matériaux continus.
-
Manutention des matériaux:
- Fours discontinus: Nécessitent plus de préparation pour le chargement, nécessitant souvent des accessoires comme des paniers ou des supports. Cela peut augmenter le temps de traitement global et les coûts de main-d’œuvre.
- Fours continus: Éliminez le besoin de racks ou de paniers, car les matériaux sont traités en une seule couche à une vitesse constante. Cela réduit le temps de manutention et les coûts de main-d'œuvre, ce qui les rend plus efficaces pour une production à grande échelle.
En résumé, le choix entre les fours discontinus et continus dépend des besoins spécifiques du processus de production, notamment du volume de matériaux, du type de matériaux traités et de l'environnement de traitement requis. Les fours discontinus offrent simplicité et coûts réduits mais nécessitent plus de préparation et de manipulation, tandis que les fours continus offrent une efficacité et des économies d'énergie au détriment d'une complexité et de coûts de maintenance plus élevés.
Tableau récapitulatif :
Aspect | Fours discontinus | Fours continus |
---|---|---|
Opération | Traite les matériaux par lots ; nécessite des supports ou des paniers pour le chargement. | Traite les matériaux en continu à une vitesse constante ; aucun support ou panier n'est nécessaire. |
Complexité | Conception plus simple ; plus facile à entretenir et à réparer. | Plus complexe ; nécessite un entretien fréquent. |
Coût | Coûts initiaux et opérationnels réduits. | Coûts initiaux et opérationnels plus élevés. |
Efficacité énergétique | Moins économe en énergie mais compensé par des coûts opérationnels inférieurs. | Plus économe en énergie grâce à un fonctionnement constant. |
Applications | Idéal pour les environnements de salles blanches, les atmosphères inertes et les petites séries de production. | Idéal pour la production en grand volume et le traitement continu. |
Manutention des matériaux | Nécessite plus de préparation et de montages pour le chargement. | Élimine le besoin de supports ou de paniers ; réduit le temps de manutention et les coûts de main d’œuvre. |
Besoin d’aide pour choisir le four adapté à vos besoins de production ? Contactez nos experts dès aujourd'hui pour des conseils personnalisés !