Le moulage par injection et le moulage par insertion sont deux procédés de fabrication distincts utilisés pour créer des pièces en plastique, chacun ayant ses propres applications et avantages.Le moulage par injection consiste à injecter du plastique fondu dans la cavité d'un moule pour former une pièce, tandis que le moulage par insertion consiste à placer un insert préformé (souvent en métal) dans le moule avant d'injecter du plastique autour de lui.La principale différence réside dans la présence d'un insert dans le moulage par insertion, qui n'est pas utilisé dans le moulage par injection standard.Le surmoulage, un procédé apparenté, consiste à injecter deux doses de matériau pour créer un substrat et un surmoulage, mais il diffère du moulage par insertion en ce qu'il utilise plusieurs matériaux en un seul processus.
Explication des points clés :
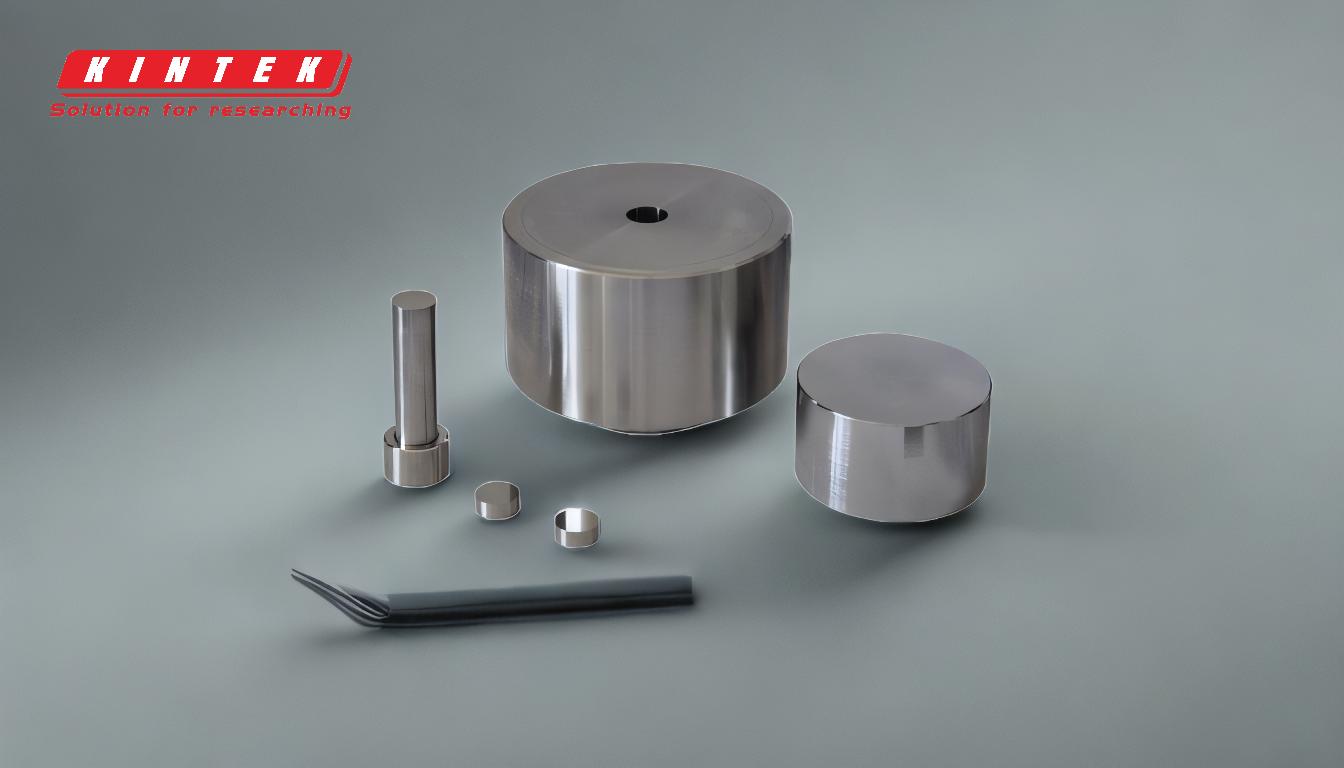
-
Définition et processus:
- Moulage par injection:Il s'agit d'un processus de fabrication dans lequel le plastique fondu est injecté sous haute pression dans la cavité d'un moule.Une fois le plastique refroidi et solidifié, le moule est ouvert et la pièce est éjectée.Il s'agit d'un procédé mono-matériau largement utilisé pour la production d'une grande variété de pièces en plastique.
- Moulage par insertion:Dans ce processus, un insert préformé (souvent en métal) est placé dans le moule avant l'injection du plastique.Le plastique en fusion s'écoule alors autour de l'insert et se lie à lui en refroidissant.Ce procédé est utilisé pour créer des pièces qui combinent les propriétés du plastique et du métal, telles que des inserts filetés ou des connecteurs électriques.
-
Matériaux utilisés:
- Moulage par injection:La plupart du temps, un seul type de matière plastique est utilisé.Le matériau est choisi en fonction des propriétés souhaitées de la pièce finale, telles que la solidité, la flexibilité ou la résistance à la chaleur.
- Moulage par insertion:Il s'agit de plastique et d'un insert préformé, qui peut être fait de métal, de céramique ou d'un autre matériau.Le plastique est choisi pour bien adhérer à l'insert, ce qui garantit un produit final solide et durable.
-
Les applications:
- Moulage par injection:Il est couramment utilisé pour la production d'une large gamme de pièces en plastique, y compris les biens de consommation, les composants automobiles et les appareils médicaux.Il est idéal pour la production de gros volumes en raison de son efficacité et de sa répétabilité.
- Moulage par insertion:Utilisé dans des applications où une combinaison de matériaux est nécessaire, comme dans la production de composants électroniques, d'appareils médicaux et de pièces automobiles.Il est particulièrement utile pour créer des pièces qui nécessitent un renforcement métallique ou des propriétés mécaniques spécifiques.
-
Les avantages:
-
Moulage par injection:
- Efficacité et répétabilité élevées de la production.
- Capacité à produire des formes complexes avec une grande précision.
- Rentabilité pour les grandes séries.
-
Moulage par insertion:
- Combine les avantages du plastique et du métal, ce qui permet d'obtenir des pièces plus résistantes et plus durables.
- Réduit le besoin d'opérations d'assemblage secondaires, car l'insert est moulé directement dans la pièce.
- Peut améliorer les performances globales de la pièce en intégrant différents matériaux.
-
Moulage par injection:
-
Défis:
-
Moulage par injection:
- Limitation aux pièces monomatériaux, qui peuvent ne pas répondre aux exigences de certaines applications.
- Coûts d'outillage initiaux élevés, ce qui peut constituer un obstacle pour les petites séries.
-
Moulage par insertion:
- Nécessite une mise en place précise de l'insert, ce qui peut compliquer le processus de moulage.
- L'insert doit être compatible avec la matière plastique pour garantir une bonne adhérence.
- Peut entraîner des coûts supplémentaires pour les inserts et une conception plus complexe du moule.
-
Moulage par injection:
-
Comparaison avec le surmoulage:
- Surmoulage:Ce procédé consiste à injecter deux doses de matériau pour créer un substrat et un surmoulage.Il est similaire au moulage par insertion en ce sens qu'il combine différents matériaux, mais il le fait en moulant un matériau sur un autre en un seul processus.Le surmoulage est souvent utilisé pour créer des pièces avec des poignées souples, des composants multicolores ou des pièces dont les propriétés matérielles varient.
- Moulage par insertion:Contrairement au surmoulage, le moulage par insertion implique une seule injection de matière plastique et un insert préformé.L'insert n'est pas moulé mais placé dans le moule avant l'injection du plastique.Ce processus est plus axé sur la combinaison du plastique avec d'autres matériaux, tels que le métal, que sur la superposition de différents plastiques.
-
Considérations relatives à la conception:
- Moulage par injection:Les concepteurs doivent tenir compte de facteurs tels que l'épaisseur de la paroi, l'emplacement de la porte et les angles de dépouille pour assurer un remplissage correct du moule et l'éjection de la pièce.
- Moulage par insertion:D'autres considérations concernent l'emplacement et la conception de l'insert, ainsi que la liaison entre l'insert et la matière plastique.L'insert doit être conçu pour résister au processus de moulage et offrir les propriétés mécaniques souhaitées.
En résumé, si le moulage par injection et le moulage par insertion sont tous deux utilisés pour créer des pièces en plastique, ils ont des objectifs différents et conviennent à des applications différentes.Le moulage par injection est idéal pour les pièces mono-matériau produites en grandes quantités, tandis que le moulage par insertion est utilisé pour créer des pièces qui combinent le plastique avec d'autres matériaux, tels que le métal, afin d'améliorer les performances.Il est essentiel de comprendre les différences entre ces procédés pour choisir la méthode de fabrication adaptée à une application donnée.
Tableau récapitulatif :
Aspect | Moulage par injection | Moulage par insertion |
---|---|---|
Procédé | Le plastique fondu est injecté dans la cavité d'un moule. | Un insert préformé est placé dans le moule avant que le plastique ne soit injecté autour de lui. |
Matériaux | Matière plastique unique. | Plastique combiné à un insert préformé (par exemple, métal). |
Applications | Biens de consommation, pièces automobiles, appareils médicaux. | Composants électroniques, dispositifs médicaux, pièces automobiles avec renforcement métallique. |
Avantages | Efficacité élevée, précision, rentabilité pour les grandes séries. | Combine le plastique et le métal, réduit l'assemblage, améliore les performances des pièces. |
Défis | Limité aux pièces monomatériaux, coûts d'outillage élevés. | Placement précis des inserts, compatibilité et coûts supplémentaires. |
Vous avez besoin d'aide pour choisir le bon procédé de moulage pour votre projet ? Contactez nos experts dès aujourd'hui !