L'effet de la pression dans la pulvérisation est un facteur critique qui influence le comportement des ions pulvérisés, la distribution de l'énergie des atomes sources et la qualité globale du film déposé.À des pressions plus élevées, les ions entrent en collision avec les atomes de gaz, ce qui entraîne un mouvement diffusif et une marche aléatoire, qui affectent l'uniformité et la couverture du dépôt.Les pressions plus faibles, en revanche, permettent des impacts balistiques à haute énergie, ce qui se traduit par un dépôt plus direct et plus énergique.La pression régit également le libre parcours moyen des ions, ce qui a un impact sur leur distribution d'énergie et sur le rendement de la pulvérisation, qui varie en fonction des matériaux cibles et des conditions de pulvérisation.Il est essentiel de comprendre cette dynamique pour optimiser les processus de dépôt par pulvérisation.
Explication des points clés :
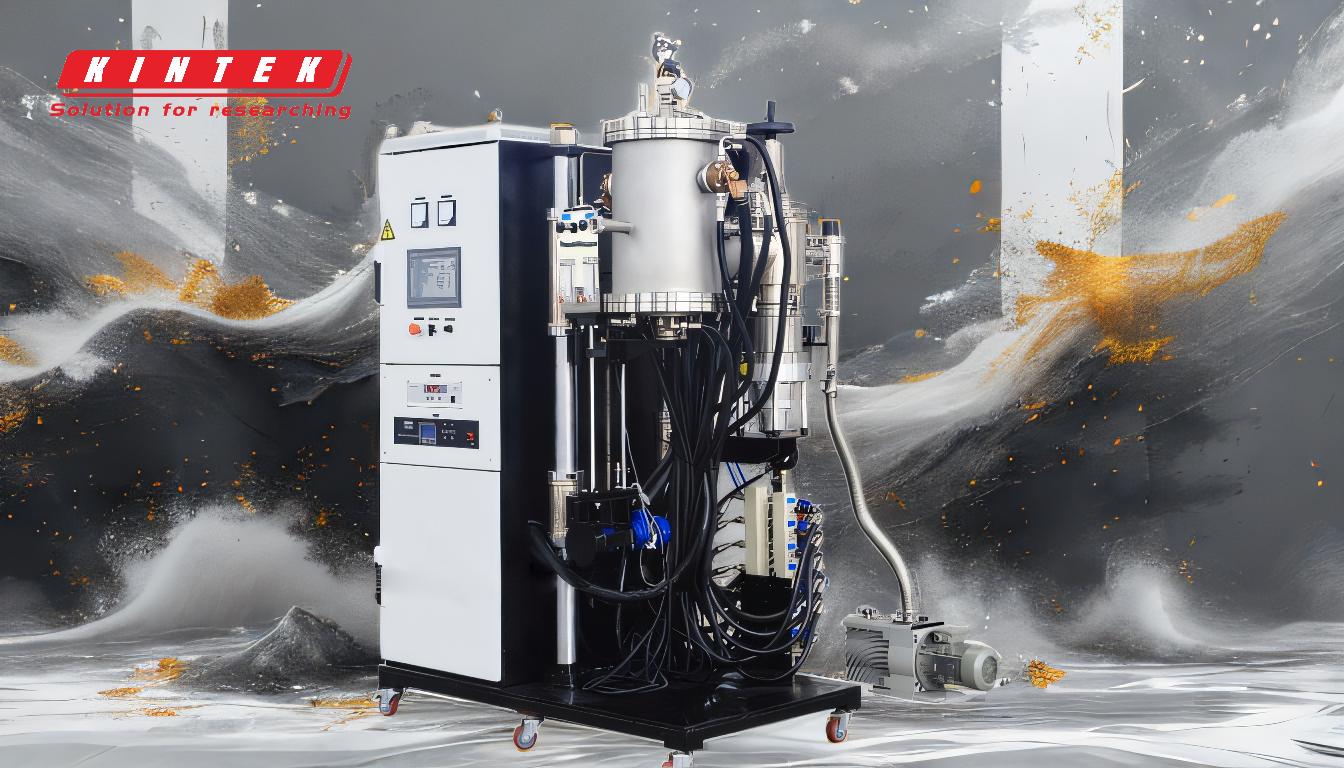
-
Influence de la pression sur le mouvement des ions :
- Pressions plus élevées : À des pressions de gaz élevées, les ions pulvérisés entrent fréquemment en collision avec les atomes du gaz.Ces collisions agissent comme un modérateur, provoquant le déplacement diffusif des ions.Il en résulte une marche aléatoire, où les ions empruntent un chemin plus long et moins direct pour atteindre le substrat ou les parois de la chambre.Ce mouvement diffusif peut améliorer l'uniformité de la couverture mais peut réduire l'énergie des particules déposées.
- Pressions plus faibles : En revanche, des pressions plus faibles réduisent le nombre de collisions entre les ions et les atomes de gaz.Cela permet aux ions de se déplacer de manière plus balistique, de maintenir des niveaux d'énergie plus élevés et d'avoir des impacts plus directs sur le substrat.Cela peut conduire à des films plus denses et plus adhérents, mais peut réduire l'uniformité de la couverture.
-
Distribution de l'énergie et parcours libre moyen :
- Le libre parcours moyen : Le libre parcours moyen des ions est la distance moyenne qu'ils parcourent entre les collisions.La pression influe directement sur ce paramètre : les pressions élevées raccourcissent le trajet libre moyen, tandis que les pressions faibles l'allongent.Un trajet libre moyen plus court à des pressions plus élevées entraîne des collisions plus fréquentes et une perte d'énergie, tandis qu'un trajet libre moyen plus long à des pressions plus basses permet aux ions de conserver plus d'énergie jusqu'à ce qu'ils atteignent le substrat.
- Distribution de l'énergie : La distribution de l'énergie des atomes de la source est régie par la pression.Dans les techniques hyperthermiques telles que la pulvérisation, la pression joue un rôle décisif en déterminant la manière dont l'énergie est répartie entre les atomes pulvérisés.Cela affecte le rendement de la pulvérisation et la qualité du film déposé.
-
Rendement de la pulvérisation et dépendance à l'égard du matériau :
- Rendement de pulvérisation : Le rendement de pulvérisation, défini comme le nombre d'atomes cibles éjectés par ion incident, est influencé par la pression.Des pressions plus élevées peuvent réduire le rendement de la pulvérisation en raison de la perte d'énergie due aux collisions, tandis que des pressions plus faibles peuvent l'augmenter en permettant aux ions de conserver plus d'énergie.Le rendement varie également en fonction du matériau cible et des conditions spécifiques de pulvérisation.
- Compatibilité des matériaux : Les matériaux réagissent différemment aux changements de pression.Par exemple, certains matériaux peuvent nécessiter des pressions plus élevées pour obtenir des rendements de pulvérisation optimaux, tandis que d'autres peuvent être plus performants à des pressions plus faibles.La compréhension de ces comportements spécifiques aux matériaux est cruciale pour l'optimisation du processus de pulvérisation.
-
Qualité du dépôt et propriétés du film :
- Densité et adhérence du film : L'énergie cinétique des particules émises, qui est influencée par la pression, détermine leur direction et leur dépôt sur le substrat.Des pressions plus faibles se traduisent généralement par une énergie cinétique plus élevée, conduisant à des films plus denses et plus adhérents.Des pressions plus élevées peuvent entraîner des films moins denses en raison de la perte d'énergie due aux collisions.
- Mobilité de la surface : L'énergie excédentaire des ions métalliques peut augmenter la mobilité de la surface pendant le processus de dépôt.Cela peut avoir un impact sur la qualité du film déposé, car une mobilité de surface plus élevée peut conduire à des films plus lisses et plus uniformes.La pression joue un rôle dans la détermination de l'étendue de cette mobilité de surface.
-
Optimisation du processus et considérations pratiques :
- Pression et température : La pression doit toujours être prise en compte avec la température de dépôt lors de l'optimisation du processus de pulvérisation.L'interaction entre ces deux paramètres peut affecter de manière significative le résultat du dépôt.
- Source d'énergie : Le type de source d'énergie (DC ou RF) utilisé pour la pulvérisation interagit également avec la pression.Par exemple, la pulvérisation RF peut être plus efficace à des pressions plus basses, tandis que la pulvérisation DC peut être plus performante à des pressions plus élevées.Le choix de la source d'énergie, ainsi que de la pression, affecte la vitesse de dépôt, la compatibilité des matériaux et le coût global du processus.
En résumé, la pression est un paramètre fondamental de la pulvérisation qui affecte le mouvement des ions, la distribution de l'énergie, le rendement de la pulvérisation et la qualité du film déposé.En contrôlant soigneusement la pression, ainsi que d'autres paramètres tels que la température et la source d'énergie, il est possible d'optimiser le processus de pulvérisation pour obtenir les propriétés de film et les résultats de dépôt souhaités.
Tableau récapitulatif :
Aspect | Pression plus élevée | Pression plus faible |
---|---|---|
Mouvement des ions | Mouvement diffusif, marche aléatoire, meilleure uniformité de la couverture, énergie réduite | Mouvement balistique, impacts directs, énergie plus élevée, films plus denses |
Trajet libre moyen | Plus court, collisions fréquentes, perte d'énergie | Plus long, moins de collisions, énergie conservée |
Rendement de la pulvérisation | Réduit en raison de la perte d'énergie | Amélioration grâce à l'énergie conservée |
Densité et adhésion du film | Films moins denses en raison de la perte d'énergie | Films plus denses et plus adhérents |
Mobilité de surface | Mobilité de surface plus faible, films moins uniformes | Mobilité de surface plus élevée, films plus lisses et plus uniformes |
Optimisation du processus | Meilleure uniformité de la couverture, réduction de l'énergie | Énergie plus élevée, films plus denses, possibilité de réduction de l'uniformité de la couverture |
Vous avez besoin d'aide pour optimiser votre processus de pulvérisation ? Contactez nos experts dès aujourd'hui pour des solutions sur mesure !