La défaillance des revêtements de four est principalement due à la dilatation et à l'écaillage thermiques, qui se produisent en raison des taux différentiels de dilatation et de contraction des matériaux réfractaires dans des conditions thermiques variables.Ce phénomène entraîne des fissures et des écaillages qui, s'ils ne sont pas traités, peuvent entraîner une défaillance structurelle du revêtement du four.Il est essentiel de comprendre les mécanismes à l'origine de ces défaillances pour sélectionner les matériaux appropriés et mettre en œuvre des stratégies d'entretien afin de prolonger la durée de vie des revêtements de four.
Les points clés expliqués :
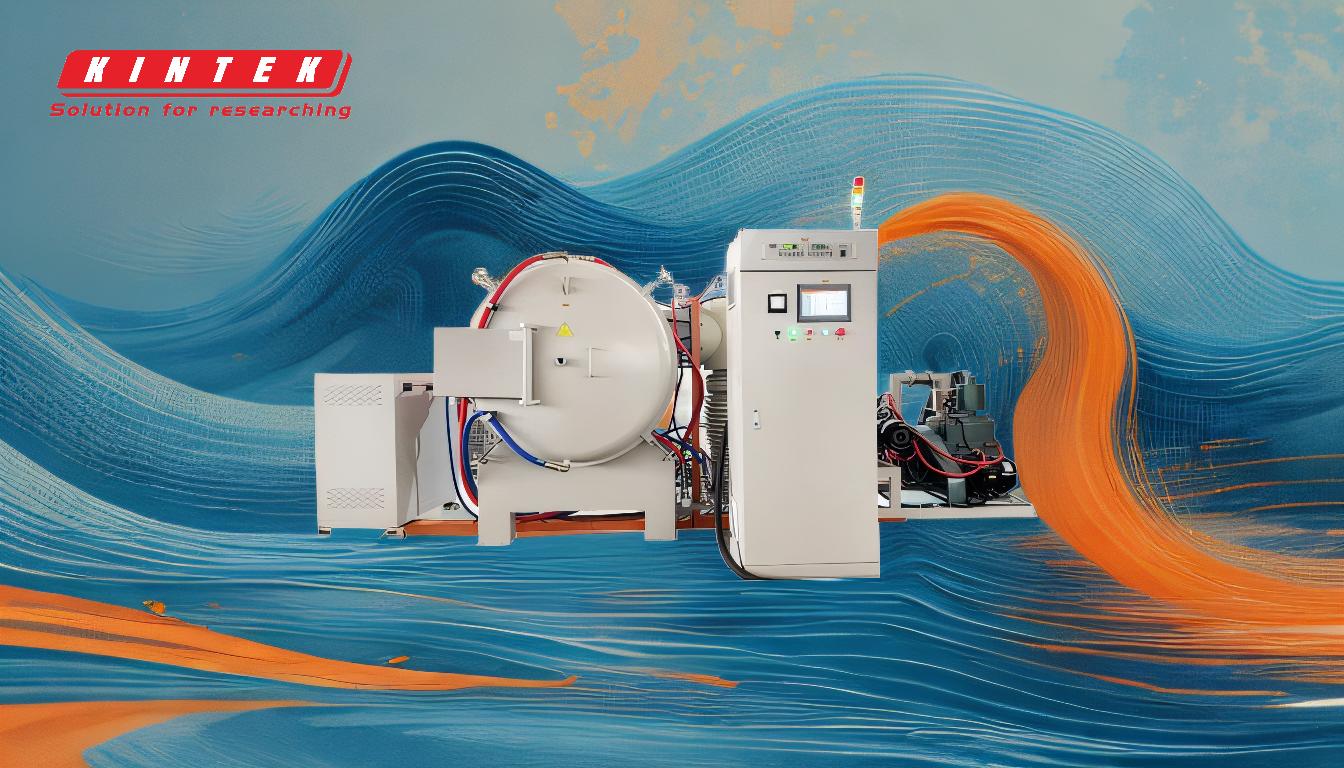
-
Expansion et contraction thermiques :
- Mécanisme : Les matériaux réfractaires se dilatent lorsqu'ils sont chauffés et se contractent lorsqu'ils sont refroidis.Les coefficients de dilatation thermique varient d'un matériau à l'autre, ce qui signifie qu'ils se dilatent et se contractent à des rythmes différents.
- Impact : Lorsque le four subit des cycles thermiques (chauffage et refroidissement), les taux différentiels d'expansion et de contraction peuvent provoquer des tensions dans le revêtement.Ces contraintes peuvent entraîner la formation de fissures au fil du temps.
-
Écaillage :
- Définition : L'écaillage désigne la rupture de fragments ou de couches de la surface du revêtement réfractaire.
- Causes : L'écaillage est souvent le résultat direct des contraintes causées par la dilatation et la contraction thermiques.Il peut également être exacerbé par l'usure mécanique, les attaques chimiques ou une mauvaise installation des matériaux réfractaires.
- Conséquences : L'écaillage expose les couches sous-jacentes du revêtement réfractaire à des températures plus élevées et à des conditions thermiques et chimiques plus sévères, ce qui accélère la dégradation et peut conduire à une défaillance catastrophique.
-
Fissuration :
- Formation : Des fissures peuvent se former en raison des cycles thermiques répétés du four.Ces fissures peuvent commencer par des microfissures et s'agrandir avec le temps.
- Conséquences : Les fissures permettent à la chaleur et aux gaz corrosifs de pénétrer plus profondément dans le revêtement réfractaire, ce qui aggrave la détérioration.Elles affaiblissent également l'intégrité structurelle du revêtement, le rendant plus vulnérable aux défaillances mécaniques.
-
Mesures préventives :
- Sélection des matériaux : Le choix de matériaux réfractaires ayant des coefficients de dilatation thermique compatibles peut minimiser les contraintes causées par les cycles thermiques.
- Considérations relatives à la conception : Une bonne conception du revêtement du four, y compris l'utilisation de joints de dilatation et d'épaisseurs appropriées, peut aider à tenir compte de la dilatation et de la contraction thermiques.
- Entretien : Une inspection régulière et la réparation rapide des fissures et des zones écaillées peuvent éviter que des problèmes mineurs ne se transforment en défaillances majeures.
-
Réparation et entretien :
- Importance : La détection précoce et la réparation des fissures et des zones écaillées sont cruciales pour maintenir l'intégrité du revêtement du four.
- Techniques : Des techniques telles que le rapiéçage, le gunitage et l'application de revêtements protecteurs peuvent être utilisées pour réparer les zones endommagées et prolonger la durée de vie du revêtement.
En résumé, la défaillance des revêtements de four est principalement due à la dilatation thermique et à l'écaillage, qui entraînent des fissures et une dégradation structurelle.La compréhension de ces mécanismes et la mise en œuvre de mesures de prévention et de maintenance appropriées sont essentielles pour garantir la longévité et la fiabilité des revêtements de four.
Tableau récapitulatif :
Facteur clé | Description de l'impact | Impact |
---|---|---|
Expansion thermique | Les matériaux réfractaires se dilatent et se contractent à des vitesses différentes sous l'effet des cycles thermiques. | Cela provoque des tensions qui entraînent des fissures et affaiblissent la structure du revêtement. |
Écaillage | Des fragments se détachent sous l'effet de la contrainte, de l'usure ou d'une attaque chimique. | Ils exposent les couches sous-jacentes, ce qui accélère la dégradation et risque d'entraîner une défaillance catastrophique. |
Fissuration | Les cycles thermiques répétés provoquent l'agrandissement des microfissures. | Elles laissent pénétrer la chaleur et les gaz corrosifs, ce qui détériore davantage le revêtement. |
Mesures préventives | Sélection des matériaux, conception et stratégies d'entretien appropriées. | Minimise les contraintes, s'adapte aux changements thermiques et empêche les problèmes mineurs de s'aggraver. |
Techniques de réparation | Rattrapage, gunitage et revêtements protecteurs. | Prolonge la durée de vie du revêtement en réparant les zones endommagées. |
Protège le revêtement de votre four contre les défaillances... contactez nos experts pour des solutions sur mesure et des stratégies de maintenance !