Introduction aux fours de frittage par plasma à étincelles (SPS)
Les fours de frittage par plasma étincelant (SPS) représentent une technologie de pointe dans le domaine de la science des matériaux, offrant une approche unique du frittage grâce à l'utilisation d'un courant continu pulsé tout ou rien pour la génération du plasma. Ce guide complet se penche sur les subtilités de la technologie SPS, en explorant ses composants tels que le dispositif de pression axiale, l'électrode de poinçonnage refroidie à l'eau et la chambre à vide. En comprenant les principales caractéristiques et les applications polyvalentes du frittage par plasma étincelant, nous pouvons comprendre comment cette technologie révolutionne le frittage rapide, efficace et de haute qualité de divers matériaux, des métaux et des céramiques aux nanomatériaux et aux composites.
Principales caractéristiques des fours de frittage par plasma étincelant
Les fours de frittage par plasma étincelant (SPS) ont révolutionné le domaine de la science des matériaux grâce à leurs capacités uniques et à leurs temps de traitement rapides. Ces fours utilisent un courant continu pulsé élevé pour chauffer et fritter des poudres compactes, offrant ainsi plusieurs avantages distincts par rapport aux méthodes de frittage traditionnelles. Nous examinons ici les principales caractéristiques des fours SPS, notamment le frittage rapide, le frittage de purification et d'activation, le frittage à grains fins, le frittage à large gamme de températures, le frittage de contrôle de la densité et le frittage à gradient de température.
Frittage rapide
L'un des principaux avantages des fours SPS est leur capacité à réaliser un frittage rapide. La vitesse de chauffage peut dépasser 500°C/min, ce qui est nettement plus rapide que les méthodes traditionnelles telles que le pressage à chaud, le pressage isostatique à chaud (HIP) et le frittage sans pression. Cette vitesse de chauffage rapide permet des temps de frittage beaucoup plus courts, réduisant souvent le processus de plusieurs heures à quelques minutes seulement. Les taux de chauffage et de refroidissement rapides minimisent également les processus de grossissement et aident à maintenir les nanostructures intrinsèques du matériau après la densification complète.
Frittage de purification et d'activation
Les fours SPS offrent un processus unique de frittage de purification et d'activation. Le courant continu pulsé élevé induit un effet de purification de la surface des particules, qui élimine les gaz adsorbés et les films d'oxyde. Ce processus de purification, combiné à l'effet d'activation de la surface des particules, permet le frittage de matériaux traditionnellement difficiles à fritter. Cette caractéristique est particulièrement avantageuse pour les matériaux exigeant une grande pureté ou pour ceux qui sont sensibles aux contaminants de surface.
Frittage à grains fins
L'élévation rapide de la température dans les fours SPS inhibe la croissance des grains, ce qui permet de réguler la microstructure et de préparer des corps frittés à grains fins. Cette caractéristique fait de la SPS une excellente méthode pour préparer des matériaux nanocristallins. En contrôlant les paramètres de frittage, les chercheurs peuvent obtenir la taille de grain et la microstructure souhaitées, ce qui est essentiel pour optimiser les propriétés mécaniques, électriques et thermiques du matériau.
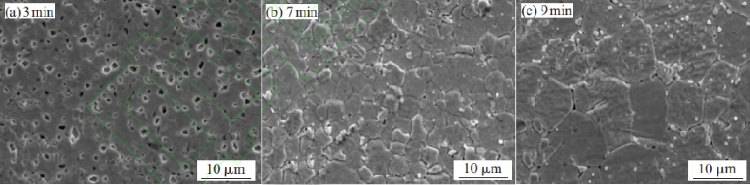
Frittage à large gamme de températures
Les fours SPS peuvent fonctionner sur une large gamme de températures, depuis les basses températures jusqu'à 2300°C. Cette large gamme de températures rend les fours SPS polyvalents pour le frittage d'une grande variété de matériaux, y compris les céramiques, les métaux et les composites. La capacité à atteindre rapidement et efficacement des températures élevées est particulièrement utile pour les matériaux qui nécessitent un traitement à haute température pour obtenir une densification complète et des propriétés optimales.
Frittage avec contrôle de la densité
Une autre caractéristique notable des fours SPS est leur capacité à contrôler la densité du corps fritté. Des corps poreux aux corps frittés entièrement denses, les fours SPS offrent un contrôle flexible de la densité. Ce contrôle s'effectue en ajustant les paramètres de frittage, tels que la force appliquée, la course du piston et le courant. Le contrôle précis de la densité est essentiel pour adapter les propriétés du matériau à des applications spécifiques, telles que l'aérospatiale, l'automobile et les industries médicales.
Frittage à gradient de température
Les fours SPS peuvent créer un gradient de température à l'intérieur du moule, ce qui permet le frittage simultané de matériaux ayant des points de fusion différents. Cette caractéristique est particulièrement utile pour la préparation de matériaux à gradient fonctionnel (FGM), où différentes couches ou régions du matériau nécessitent des conditions de traitement différentes. La possibilité de créer un gradient de température (des centaines de °C/mm) à l'intérieur du moule permet de produire des matériaux complexes, multicouches, avec des propriétés et des fonctionnalités adaptées.
En conclusion, les fours SPS offrent une gamme de caractéristiques avancées qui en font un outil puissant dans le domaine de la science des matériaux. Leur capacité à réaliser un frittage rapide, un frittage de purification et d'activation, un frittage à grain fin, un frittage à température étendue, un frittage de contrôle de la densité et un frittage à gradient de température les rend polyvalents et efficaces pour un large éventail d'applications. La recherche et le développement dans ce domaine continuant à progresser, les fours SPS sont appelés à jouer un rôle de plus en plus important dans la production de matériaux de haute performance.
Polyvalence dans le traitement des matériaux avec le frittage par plasma étincelant
Le frittage par plasma étincelant (SPS) est une technique très efficace et polyvalente utilisée pour le frittage d'une large gamme de matériaux, notamment les métaux, les céramiques, les nanomatériaux et les matériaux composites. Cette méthode s'appuie sur des impulsions de courant continu pour générer un plasma d'étincelles entre les particules, ce qui facilite les processus de chauffage et de densification rapides. La technologie SPS est réputée pour sa capacité à préparer des matériaux de haute qualité avec des avantages significatifs par rapport aux méthodes de frittage traditionnelles.
Large champ d'application de la SPS
Nanomatériaux
La technologie SPS est particulièrement efficace pour la préparation des nanomatériaux. Les méthodes de frittage traditionnelles ont souvent du mal à maintenir la taille des grains à l'échelle du nanomètre et à atteindre une densité complète. La technologie SPS, avec son chauffage rapide et ses temps de synthèse courts, supprime efficacement le grossissement des grains. Ce processus rapide permet également de conserver les défauts et les sous-structures dans la poudre, ce qui peut être bénéfique pour la synthèse de matériaux métastables et de nanomatériaux.
Matériaux fonctionnels à gradient
Les matériaux fonctionnels à gradient (FGM) sont des composites présentant un gradient de distribution dans une certaine direction, nécessitant souvent des températures de frittage différentes pour chaque couche. Les méthodes traditionnelles telles que le dépôt chimique en phase vapeur (CVD) et le dépôt physique en phase vapeur (PVD) sont coûteuses et difficiles à mettre en œuvre pour la production industrielle. La technologie SPS permet de surmonter ces difficultés en permettant le frittage de matériaux présentant des gradients de résistance à la chaleur, de résistance à l'usure, de dureté, de conductivité et de porosité, avec la possibilité de traiter plusieurs couches.
Matériaux électromagnétiques
La technologie SPS est également utilisée pour produire divers matériaux électromagnétiques, notamment des éléments de conversion thermoélectrique et des matériaux utilisés dans le domaine de l'électronique, tels que les matériaux supraconducteurs, les matériaux magnétiques, les matériaux diélectriques et bien d'autres encore. Ces matériaux sont essentiels pour des applications allant du stockage de l'énergie à l'ingénierie biomédicale.
Composés intermétalliques
Les composés intermétalliques, connus pour leur fragilité et leur point de fusion élevé, nécessitent des procédés de préparation spécialisés. La SPS offre une méthode efficace pour préparer ces composés en utilisant l'auto-échauffement et l'activation de surface entre les particules, ce qui permet un frittage rapide et à basse température.
Céramiques et cermets à haute densité et à grain fin
Le procédé SPS raccourcit considérablement les temps de frittage et réduit les températures en exploitant la chaleur générée à l'intérieur de chaque particule de poudre et les espaces entre elles. Cela fait de la SPS une excellente méthode pour préparer des céramiques et des cermets à haute densité et à grain fin, qui sont essentiels pour diverses applications industrielles.
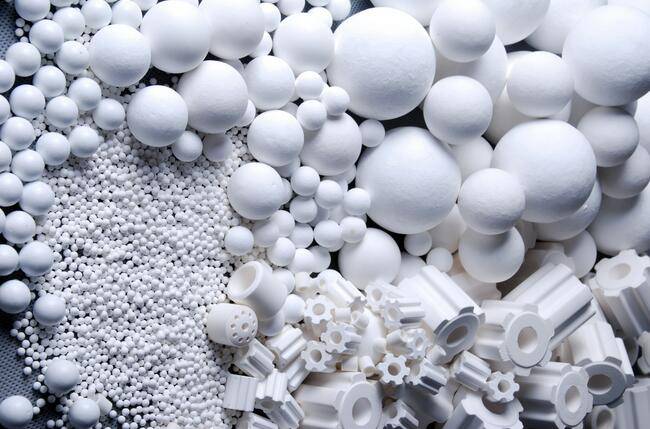
Avantages de la SPS
- Temps de cycle plus courts : La technologie SPS réduit considérablement les cycles de frittage, qui passent de plusieurs heures ou jours à quelques minutes seulement, améliorant ainsi la productivité et les capacités de développement rapide des matériaux.
- Températures de frittage plus basses : Elle permet de fritter à des températures plus basses que les procédés conventionnels, ce qui est particulièrement avantageux pour les matériaux sensibles à la chaleur.
- Contrôle de processus de haute précision : Le procédé SPS permet un contrôle précis des paramètres de frittage tels que la température et la pression, ce qui garantit des résultats optimaux et permet de créer des chimies uniques qui ne sont pas réalisables avec les méthodes conventionnelles.
- Polyvalence : Elle permet de densifier une large gamme de matériaux, depuis les métaux à faible point de fusion jusqu'aux céramiques à ultra-haute température, et même de lier des matériaux dissemblables nécessitant des distributions de température non uniformes.
Applications de la technologie SPS
La technologie SPS trouve des applications dans divers domaines, notamment
- Stockage d'énergie : Batteries lithium-ion à haute capacité et autres matériaux de stockage d'énergie avancés.
- Ingénierie biomédicale : Céramiques poreuses pour l'administration de médicaments et les échafaudages pour l'ingénierie tissulaire.
- Céramiques avancées : Supraconducteurs à haute température et céramiques piézoélectriques à haute performance.
- Intermétalliques : Alliages avancés aux propriétés mécaniques, thermiques et électriques améliorées.
- Composites : Céramiques et métaux renforcés aux propriétés mécaniques améliorées.
En conclusion, le frittage par plasma étincelant s'impose comme une méthode très polyvalente et efficace pour le frittage de divers matériaux, offrant des avantages significatifs en termes de contrôle des processus, d'efficacité énergétique et de capacité à produire des matériaux de haute qualité pour un large éventail d'applications.
Facilité d'utilisation et caractéristiques de sécurité des fours SPS
Les fours de frittage par plasma à étincelles (SPS) sont réputés pour leur facilité d'utilisation et leurs caractéristiques de sécurité robustes, ce qui en fait un choix privilégié pour diverses applications industrielles. Ces fours sont conçus en mettant l'accent sur des interfaces conviviales et des mécanismes de sécurité complets afin de garantir des opérations efficaces et sûres.
Conception et systèmes de contrôle conviviaux
Les fours SPS sont équipés de systèmes de contrôle de pointe qui améliorent la facilité d'utilisation. Une caractéristique notable est l'intégration d'interfaces à écran tactile et d'automates programmables (PLC) pour le contrôle central. Cette configuration permet aux opérateurs de surveiller et d'ajuster facilement les paramètres du four, ce qui réduit la complexité de l'opération et le risque d'erreur humaine. Le système PLC Allen-Bradley, par exemple, est connu pour sa facilité de programmation et de modification, ce qui simplifie encore la gestion des opérations du four.
L'armoire de commande de ces fours est conçue pour abriter toutes les commandes électriques dans une armoire NEMA 12 standard, ce qui garantit la conformité aux normes de sécurité telles que NFPA 70. Cette commande centralisée renforce non seulement la sécurité, mais facilite également l'entretien et le dépannage. L'intégration d'un interrupteur électrique principal de verrouillage ajoute une couche supplémentaire de sécurité en empêchant les opérations non autorisées ou accidentelles.
Mécanismes de sécurité avancés
La sécurité est une préoccupation majeure dans le fonctionnement des fours SPS, et ces systèmes sont équipés de plusieurs niveaux de protection. Les principaux dispositifs de sécurité comprennent des alarmes de dysfonctionnement en cas de surchauffe et de surpression, qui alertent les opérateurs des risques potentiels en temps réel. En outre, des systèmes mécaniques automatiques de protection contre la pression sont en place pour se prémunir contre les problèmes liés à la pression, afin de garantir l'intégrité du four et des matériaux traités.
Les fours sont également dotés de fonctions de verrouillage qui empêchent les opérations dans des conditions dangereuses. Par exemple, des dispositifs de verrouillage sont utilisés pour désactiver le four en cas de pénurie d'électricité ou d'eau, de pression insuffisante ou de surchauffe. Ces verrouillages sont essentiels pour prévenir les accidents et protéger à la fois l'équipement et les opérateurs.
Les capacités de commande à distance constituent un autre élément de sécurité important, car elles permettent de diagnostiquer les dysfonctionnements et de mettre à jour les programmes à distance. Cela permet non seulement d'améliorer l'efficacité de la maintenance, mais aussi de réduire le risque d'exposition des techniciens à des conditions dangereuses.
Intégration du thermocouple
Un contrôle précis de la température est essentiel dans les processus de frittage, et les fours SPS utilisent des thermocouples de haute qualité, tels que le type "S" et le type "K", pour une surveillance et un contrôle précis de la température. Ces thermocouples sont intégrés à des panneaux de vérins appropriés pour la surveillance et le contrôle du travail, ce qui garantit que le processus de frittage reste dans des plages de température sûres et optimales.
Conclusion
En résumé, la facilité d'utilisation et les caractéristiques de sécurité des fours SPS sont conçues pour offrir une expérience de frittage transparente et sûre. Avec des systèmes de commande conviviaux, des mécanismes de sécurité avancés et un contrôle précis de la température, ces fours sont idéaux pour une large gamme d'applications dans le traitement des métaux, des céramiques, des nanomatériaux, etc. L'intégration de technologies modernes et de protocoles de sécurité robustes permet aux opérateurs de travailler efficacement tout en minimisant les risques.
Systèmes de contrôle et de surveillance avancés dans les SPS
Les systèmes avancés de contrôle et de surveillance font partie intégrante du processus de frittage par plasma étincelant (SPS), permettant une régulation précise de la température, de la pression et du courant, ainsi que l'acquisition de données complètes pour suivre et analyser les paramètres de frittage. Ces systèmes sont essentiels pour garantir la qualité et la reproductibilité des matériaux frittés.
Contrôle automatisé du programme
Le processus SPS commence par le chargement d'une quantité connue d'échantillon de poudre séchée et broyée dans une matrice cylindrique doublée d'une feuille de graphite, qui facilite le retrait du compact fritté. La matrice est ensuite placée à l'intérieur de la chambre SPS et le profil temps-température spécifique requis pour l'expérience est défini. L'atmosphère à l'intérieur de la chambre est maintenue selon les besoins, qu'il s'agisse de vide, d'argon ou d'autres environnements contrôlés. La puissance est réglée au maximum en mode automatique et la charge requise est appliquée à la matrice. La position de l'axe z est réglée sur zéro et la minuterie est activée avant d'appuyer sur SINTER pour lancer le processus de frittage.
Pour mesurer la température, SPS utilise deux types d'instruments : des thermocouples pour les températures de frittage inférieures à 1000°C et des pyromètres pour les températures supérieures à 1000°C. Une impulsion de courant continu élevé passe entre des électrodes en graphite et une pression axiale est appliquée simultanément dès le début du cycle de frittage. L'échantillon est chauffé par effet Joule et par étincelles entre les particules, ce qui accélère instantanément le transfert de chaleur et de masse. Après le frittage, l'alimentation est coupée et l'échantillon est laissé à refroidir.
Systèmes de contrôle informatisés
Le système de contrôle des SPS est généralement informatisé et comprend un système de contrôle automatique PLC à écran plat tactile qui permet de passer manuellement en mode automatique. Le logiciel du système de contrôle est développé en interne et offre une interface conviviale avec une surveillance en temps réel des conditions du four. Le système est stable et fiable, avec une réponse rapide et de fortes capacités anti-interférences. Le logiciel affiche un écran de simulation en couleur, intégrant l'affichage de la température et le contrôle de la soupape à vide pour un fonctionnement intuitif.
L'appareil peut adopter différentes courbes pour l'analyse, telles que les courbes de température, de puissance, de vide, de température de l'eau, de pression de l'air et de temps de frittage. Ces courbes constituent un moyen convivial d'analyser le processus de frittage sur la base de données historiques. Le système peut générer automatiquement des fichiers Excel via l'interface USB pour une analyse plus approfondie.
La méthode de contrôle de la température utilise un thermocouple pour les températures allant jusqu'à 1700°C, les instruments infrarouges prenant le relais pour les températures supérieures à 1700°C. Le système prend en charge diverses interfaces de communication telles que RS232, RS422, CAN, LAN et USB, ce qui facilite la mise en réseau avec d'autres équipements. L'interface de contrôle du logiciel est visualisée, affichant dynamiquement le flux de travail pour plus de commodité et d'intuitivité. La mise à jour du logiciel est gratuite à vie.
Contrôleurs et acquisition de données
Comme pour les autres chambres d'essais, SPS propose différents choix de contrôleurs, allant de systèmes entièrement manuels à des systèmes entièrement automatisés. Les contrôleurs automatisés permettent aux utilisateurs de définir les paramètres du processus et, au fur et à mesure que la procédure se déroule, le système procède à des ajustements de pression, de température et d'autres facteurs programmés. Ces systèmes de contrôle sont configurables à l'aide d'un logiciel personnalisable et d'une variété de méthodes de collecte de données. Le choix du contrôleur est déterminé par la criticité de l'application et la taille de la chambre à vide. Les petites chambres peuvent n'avoir besoin que d'une simple jauge pour contrôler le pompage et la pression, tandis que les chambres plus grandes peuvent nécessiter un système plus agressif et plus sophistiqué.
Composants de la machine de frittage
La machine SPS est assistée par plusieurs composants, notamment une presse uniaxiale, des électrodes de poinçonnage, une chambre à vide, une atmosphère contrôlée, un générateur d'impulsions CC et des unités de mesure de la position, de la température et de la pression. Le contrôle de la température de frittage s'effectue par le réglage de paramètres tels que le temps de maintien, le taux de rampe, la durée de l'impulsion, le courant et la tension de l'impulsion. La décharge d'impulsions CC génère un plasma d'étincelles, une pression d'impact d'étincelles, un chauffage par effet Joule et un effet de diffusion du champ électrique. Dans le cas de la SPS, le frittage est assisté par la tension d'impulsion continue tout ou rien, ce qui est différent du pressage à chaud conventionnel. L'application de la pression favorise l'écoulement plastique du matériau, et le flux de courant continu pulsé à travers les particules est illustré par des diagrammes détaillés.
En conclusion, les systèmes avancés de contrôle et de surveillance des SPS sont essentiels pour obtenir des résultats de frittage précis et reproductibles. Ces systèmes permettent des ajustements en temps réel et l'acquisition de données complètes, garantissant la qualité et la cohérence des matériaux frittés. Grâce à l'intégration de commandes informatisées, de logiciels personnalisables et de méthodes avancées de collecte de données, la technologie SPS continue de repousser les limites de la science et de l'ingénierie des matériaux.
Applications du frittage par plasma étincelant en science des matériaux
Le frittage par étincelage (SPS) est une technique de frittage polyvalente et avancée qui a révolutionné le domaine de la science des matériaux. En combinant une pression uniaxiale, un courant continu pulsé et un chauffage rapide, le SPS permet la synthèse d'un large éventail de matériaux aux propriétés et structures uniques. Cette section examine les multiples applications de la technologie SPS, notamment le frittage, l'assemblage, le formage, la modification de la surface et la synthèse de matériaux tels que les électrolytes solides et les matériaux électriques thermiques.
Frittage de matériaux avancés
La technologie SPS est particulièrement réputée pour sa capacité à fritter efficacement des matériaux à point de fusion élevé et des nanomatériaux. Les taux de chauffage rapides (jusqu'à 1000°C/min) et les temps de traitement courts inhérents à la SPS permettent de maintenir la nanostructure des poudres, empêchant la croissance des grains et préservant les propriétés inhérentes aux particules de taille nanométrique. Cela fait de la SPS une méthode idéale pour produire des céramiques et des cermets à haute densité et à grain fin. Par exemple, le nitrure de titane, un matériau connu pour ses mauvaises propriétés de frittage et sa fragilité, peut être densifié à des niveaux élevés à l'aide de la SPS, atteignant des densités proches des valeurs théoriques sous des pressions de 1 à 5 GPa.
Assemblage et formage
Outre le frittage, la technologie SPS est également utilisée pour assembler des matériaux dissemblables et former des formes complexes. Le courant continu appliqué pendant le processus non seulement chauffe le matériau, mais renforce également la liaison par diffusion entre les particules, facilitant ainsi l'assemblage de matériaux traditionnellement difficiles à lier, tels que les céramiques aux métaux. Cette capacité est particulièrement utile dans les secteurs de l'aérospatiale et de l'automobile, où la demande de composites légers et très résistants est élevée.
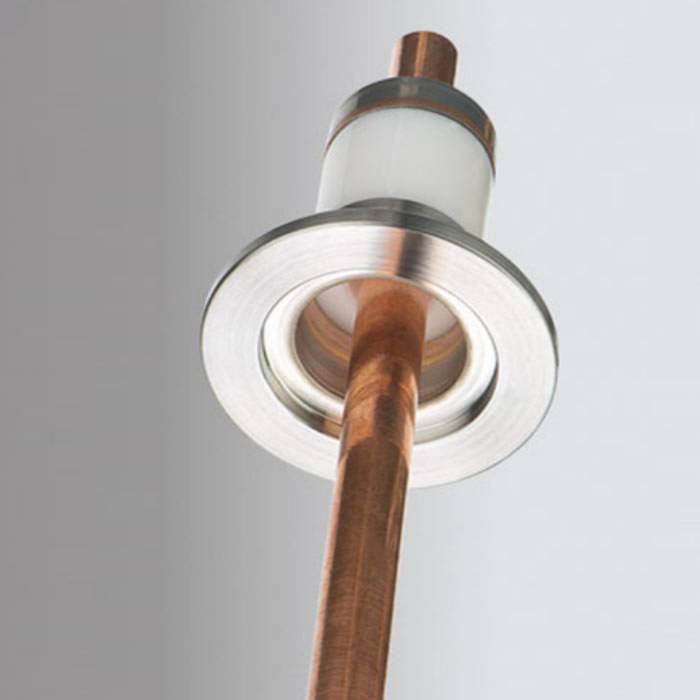
Modification de surface
La technologie SPS peut également être utilisée pour la modification des surfaces, en améliorant les propriétés de surface des matériaux sans affecter leurs caractéristiques globales. En contrôlant la densité du courant et la pression, des couches de surface spécifiques peuvent être adaptées pour obtenir les propriétés souhaitées, telles qu'une dureté accrue, une résistance à l'usure ou à la corrosion. Cette application est particulièrement bénéfique pour les matériaux d'outillage et les composants exposés à des environnements difficiles.
Synthèse de matériaux fonctionnels
L'une des applications les plus importantes de la technologie SPS est la synthèse de matériaux fonctionnels, notamment les électrolytes solides et les matériaux électriques thermiques. Les électrolytes solides, essentiels pour les applications dans les batteries à l'état solide et les piles à combustible, exigent un degré élevé de densification et de pureté. Les SPS facilitent la synthèse de ces matériaux avec une ségrégation minimale des joints de grains et une excellente conductivité ionique. De même, les matériaux thermiques électriques, utilisés dans diverses applications de chauffage, peuvent être synthétisés avec une conductivité thermique et une résistivité électrique contrôlées grâce à des paramètres de traitement SPS précis.
Importance industrielle et perspectives d'avenir
L'importance industrielle de la technologie SPS réside dans sa capacité à produire des matériaux de haute performance avec une consommation d'énergie réduite et des temps de traitement plus courts. Cette technologie est particulièrement adaptée à la production de nanomatériaux, d'alliages amorphes en vrac et de matériaux fonctionnels à gradient, qui sont difficiles à synthétiser à l'aide des méthodes traditionnelles. Alors que la recherche se poursuit pour découvrir de nouvelles applications et optimiser les paramètres de traitement, le SPS est appelé à jouer un rôle crucial dans l'avenir de la science des matériaux, en favorisant les progrès dans diverses industries de haute technologie.
En conclusion, le frittage par plasma étincelant s'impose comme une technologie de transformation de la science des matériaux, offrant un large éventail d'applications allant du frittage et de l'assemblage à la modification des surfaces et à la synthèse de matériaux fonctionnels avancés. Sa capacité à traiter les matériaux avec une grande efficacité et une grande précision en fait un outil indispensable pour les chercheurs et les praticiens industriels.
Défis et considérations liés à l'utilisation de la technologie SPS
La technologie du frittage par plasma étincelant (SPS) a révolutionné le domaine de la science des matériaux en permettant la synthèse de matériaux avancés aux propriétés uniques. Cependant, la mise en œuvre du SPS s'accompagne de son propre ensemble de défis et de considérations qui doivent être pris en compte pour obtenir des résultats de frittage optimaux. Cette section aborde les aspects critiques de la sélection et de la maintenance des moules, ainsi que les considérations plus générales pour des opérations SPS efficaces.
Sélection et entretien des moules
Le choix du matériau du moule est un facteur essentiel de la technologie SPS. Traditionnellement, le graphite est le matériau préféré en raison de sa résistance aux températures élevées, de son excellente conductivité électrique et thermique et de sa stabilité chimique. Cependant, les moules en graphite présentent des limites telles qu'une faible résistance mécanique, une courte durée de vie et une contamination potentielle des matériaux frittés. Ces problèmes nécessitent l'exploration d'autres matériaux de moulage.
Des avancées récentes ont conduit au développement d'autres matériaux de moulage tels que le carbure cémenté, les céramiques conductrices et le graphite à fibres de carbone. Chacun de ces matériaux présente des avantages uniques, mais aussi des difficultés. Par exemple, les moules en carbure cémenté sont plus résistants mais peuvent être sujets à des déformations à haute température. Les céramiques conductrices offrent un équilibre de propriétés mais sont souvent coûteuses. Les moules en fibre de carbone et graphite combinent les avantages du graphite avec des propriétés mécaniques améliorées, mais nécessitent une manipulation soigneuse pour éviter les dommages.
Le maintien de l'intégrité du moule est essentiel pour obtenir des résultats de frittage constants. L'inspection régulière et le remplacement des moules usés sont essentiels pour éviter les incohérences dans le processus de frittage. En outre, un nettoyage et un conditionnement adéquats des moules entre deux utilisations peuvent prolonger leur durée de vie et maintenir la qualité des matériaux frittés.
Obtenir des résultats de frittage optimaux
Pour obtenir des résultats de frittage optimaux, plusieurs éléments doivent être pris en compte. Il s'agit notamment de la sélection des paramètres de frittage appropriés, du contrôle de l'environnement de frittage et de la compréhension du mécanisme de frittage.
Paramètres de frittage
Les paramètres de frittage, tels que la température, la pression et le temps de séjour, jouent un rôle essentiel dans la détermination des propriétés finales du matériau fritté. Les vitesses de chauffage et de refroidissement rapides obtenues avec la SPS peuvent conduire à des microstructures non équilibrées, ce qui peut être avantageux pour obtenir des propriétés de matériaux uniques. Toutefois, ces vitesses doivent être soigneusement contrôlées pour éviter une croissance excessive des grains ou d'autres défauts.
Environnement de frittage
L'environnement de frittage, y compris l'atmosphère et les gradients de température, peut influencer de manière significative le processus de frittage. Le contrôle de l'atmosphère permet d'éviter l'oxydation et d'autres réactions chimiques susceptibles de dégrader le matériau. Les gradients de température à l'intérieur du moule peuvent entraîner une densification non uniforme, ce qui nécessite une conception et une optimisation minutieuses de l'installation de frittage.
Comprendre le mécanisme de frittage
Le mécanisme de frittage dans les SPS implique la génération d'un plasma d'étincelles entre les particules, ce qui facilite un chauffage et une densification rapides. Toutefois, les mécanismes exacts qui régissent ce processus ne sont pas encore totalement compris et font l'objet de recherches permanentes. Les simulations par éléments finis sont devenues un outil précieux pour l'étude du processus de frittage, car elles permettent de mieux comprendre les distributions de température et de champ électrique à l'intérieur du matériau.
Orientations futures
L'amélioration continue de la technologie SPS nécessite une recherche et un développement permanents. Les principaux domaines d'exploration future comprennent le développement de nouveaux matériaux de moulage aux propriétés améliorées, l'optimisation des paramètres de frittage grâce à des techniques de simulation avancées, et une compréhension plus approfondie du mécanisme de frittage.
En conclusion, si la technologie SPS offre des avantages significatifs pour la synthèse de matériaux avancés, elle présente également plusieurs défis et considérations qui doivent être pris en compte pour obtenir des résultats optimaux. En sélectionnant et en entretenant soigneusement les moules, en contrôlant les paramètres de frittage et en approfondissant notre compréhension du mécanisme de frittage, nous pouvons continuer à repousser les limites de ce qui est possible avec la technologie SPS.
Tendances et innovations futures dans la technologie SPS
La technologie du frittage par plasma étincelant (SPS), connue pour ses capacités de frittage rapide, a été un point focal dans le domaine de la science des matériaux en raison de sa capacité à produire des matériaux de haute qualité avec des propriétés uniques. Alors que la recherche continue d'évoluer, plusieurs tendances et innovations émergent, promettant d'améliorer l'efficacité, d'élargir les applications et d'améliorer la sécurité de la technologie SPS.
Industrialisation et production de masse
L'une des tendances les plus significatives de la technologie des SPS est sa transition vers l'industrialisation. Par rapport aux méthodes de frittage traditionnelles, les SPS offrent des avantages substantiels en termes d'économies d'énergie et de temps, d'efficacité accrue de la production et de contrôle supérieur des performances du produit. Des pays comme le Japon ont déjà réalisé des applications industrielles de la technologie SPS, principalement dans la production de matériaux magnétiques, d'alliages durs et de matériaux fonctionnels à gradient. Par exemple, Ohta Seiki, au Japon, a réussi à mettre en œuvre la production de masse de matériaux superdurs 100 % WC à l'aide de la technologie SPS, fournissant plus de 40 fabricants dans le monde. En revanche, dans d'autres régions, comme la Chine, la technologie SPS reste largement au stade de la recherche en laboratoire, se concentrant sur la préparation et la recherche de procédés pour de nouveaux matériaux.
Diversification des formes frittées
Actuellement, la technologie SPS est limitée à la production d'échantillons cylindriques simples en raison des contraintes du mécanisme de frittage et des moules en graphite. Cependant, la tendance est de plus en plus au développement de la technologie SPS pour créer des formes et des structures plus complexes. Cette avancée élargirait considérablement les possibilités d'application des SPS dans divers secteurs de l'ingénierie, en permettant la production de composants complexes qui sont actuellement impossibles à réaliser.
Synthèse et connexion des matériaux
La technologie SPS n'est pas seulement utilisée pour le frittage de matériaux en vrac, mais aussi pour la synthèse de poudres, en particulier celles qui sont difficiles à obtenir par des méthodes conventionnelles. Par exemple, la technologie SPS a été utilisée pour synthétiser de la poudre de ZrC à ultra-haute température, avec une grande pureté et une granulométrie fine d'environ 100 nm. En outre, la SPS est étudiée pour la connexion des matériaux (soudage), y compris les joints céramique-céramique et céramique-métal. La possibilité de relier des matériaux sans couche intermédiaire, grâce à l'auto-diffusion renforcée par le champ électrique de la SPS, ouvre de nouvelles perspectives pour la création de structures composites robustes et durables.
Optimisation des performances des moules de frittage
Le graphite, bien que couramment utilisé dans les SPS en raison de sa résistance aux températures élevées et de son excellente conductivité électrique et thermique, présente des limites telles qu'une faible résistance et une contamination potentielle des matériaux frittés. La tendance est à la mise au point de nouveaux matériaux de moulage offrant une plus grande résistance, une meilleure réutilisation et une contamination réduite. Des matériaux tels que les moules en carbure cémenté, les moules en céramique conductrice et les moules en fibre de carbone graphite font l'objet de recherches, bien que des problèmes tels que la déformation à haute température et les coûts élevés persistent.
Progrès en matière de simulation et de modélisation
Il est essentiel de comprendre le processus complexe de frittage des résines de polystyrène pour optimiser ses paramètres et prédire ses résultats. La simulation par éléments finis s'est révélée être un outil précieux à cet égard, permettant aux chercheurs d'analyser les distributions de température et de champ électrique pendant le frittage. Des logiciels comme ABAQUS, MATLAB et MSC.MARC sont utilisés pour simuler le processus de frittage, ce qui permet de mieux comprendre l'impact des différents paramètres et de faciliter l'orientation théorique de la production.
Caractéristiques de sécurité améliorées
Alors que la technologie SPS continue d'évoluer, l'accent est mis de plus en plus sur l'amélioration de ses caractéristiques de sécurité. Il s'agit notamment de mettre au point des protocoles d'exploitation plus sûrs, d'améliorer la fiabilité des équipements SPS et de veiller à ce que la technologie puisse être utilisée dans un plus grand nombre d'environnements sans compromettre la sécurité.
En conclusion, l'avenir de latechnologie SPSest prometteur grâce à la recherche et au développement continus visant à améliorer l'efficacité, à élargir les applications des matériaux et à renforcer les caractéristiques de sécurité. Ces avancées devraient révolutionner le domaine de la science des matériaux, en permettant la production de matériaux et de composants de haute performance qui n'étaient pas accessibles auparavant. Au fur et à mesure que la technologie SPS continue à mûrir, elle jouera sans aucun doute un rôle essentiel dans l'avenir de la fabrication et de l'innovation en matière de matériaux.
CONTACTEZ-NOUS POUR UNE CONSULTATION GRATUITE
Les produits et services de KINTEK LAB SOLUTION ont été reconnus par des clients du monde entier. Notre personnel se fera un plaisir de répondre à toute demande que vous pourriez avoir. Contactez-nous pour une consultation gratuite et parlez à un spécialiste produit pour trouver la solution la plus adaptée aux besoins de votre application !