Introduction
Table des matières
- Introduction
- Vue d'ensemble de la compression isostatique à froid
- Types de pressage isostatique à froid
- Avantages du pressage isostatique à froid par rapport au pressage uniaxial sous pression
- Pressage isostatique à froid dans la production de composants de forme complexe
- Comparaison entre le pressage isostatique à froid et le moulage par injection pour la production de grands volumes
- Aperçu historique de l'utilisation de la NEF dans la fabrication de céramiques d'alumine
- Utilisation de la NEP dans la production d'isolateurs de bougies d'allumage
- Presses isostatiques à froid
- Pressage isostatique à froid
- QU'EST-CE QUE LE PRESSAGE ISOSTATIQUE À FROID ?
- Pressage isostatique à froid
- Processus de pressage isostatique à froid
- Avantages du pressage isostatique à froid pour les céramiques d'alumine
- Inconvénients du pressage isostatique à froid pour les céramiques
- Applications de la presse isostatique à froid
- Autres technologies de compression
- Conclusion
La compression isostatique à froid (CIP)est un procédé de fabrication largement utilisé dans diverses industries, notamment la céramique, la métallurgie et les produits pharmaceutiques. Il s'agit d'appliquer une pression égale dans toutes les directions à un matériau placé à l'intérieur d'un moule ou d'un sac flexible. Ce procédé permet d'obtenir une densité uniforme et de façonner des composants complexes aux géométries compliquées. Le CIP offre plusieurs avantages par rapport au pressage uniaxial traditionnel, comme la possibilité de former des formes plus complexes et la réduction des distorsions et des fissures grâce à l'emballage uniforme des particules. Dans cet article de blog, nous allons nous pencher sur l'application, les avantages et les limites du pressage isostatique à froid.
Vue d'ensemble de la compression isostatique à froid
Explication du pressage isostatique à froid
Le pressage isostatique à froid (CIP) est une technique de traitement des matériaux qui consiste à appliquer une pression égale dans toutes les directions à un matériau en poudre. Ce processus est utilisé pour comprimer la poudre en une masse solide, créant ainsi une pièce brute suffisamment résistante pour être manipulée et traitée ultérieurement.
Différence entre le pressage isostatique en sac humide et le pressage isostatique en sac sec
Une variante du pressage isostatique à froid est la technologie du sac humide. Dans ce procédé, la poudre est remplie dans un moule et scellée hermétiquement à l'extérieur de l'enceinte sous pression. Le moule est ensuite immergé dans un fluide à haute pression à l'intérieur de la cuve, et une pression isostatique est appliquée pour comprimer la poudre et lui donner une forme. La technologie des sacs humides est idéale pour la production de formes multiples et de petites ou grandes quantités.
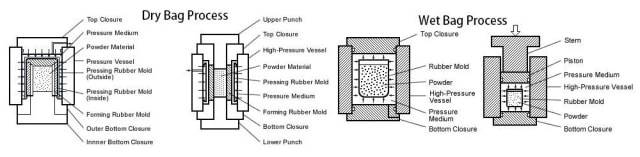
En revanche, le pressage isostatique en sac sec implique la création d'un moule intégré à l'intérieur de l'enceinte sous pression elle-même. La poudre est ajoutée au moule, celui-ci est scellé et une pression est appliquée pour comprimer la poudre. Ce procédé élimine la nécessité d'immerger le moule dans un fluide séparé, ce qui facilite l'automatisation.
Rôle de la qualité de la poudre et de la conception de l'outillage dans le processus
La qualité de la poudre utilisée pour le pressage isostatique à froid joue un rôle crucial dans le produit final. La poudre doit présenter une distribution granulométrique, une fluidité et une densité adéquates pour garantir une compression efficace et uniforme. En outre, la conception de l'outillage, y compris le moule ou le sac utilisé, doit être soigneusement étudiée pour répondre aux exigences spécifiques du matériau de la poudre et de la forme souhaitée.
Une conception adéquate de l'outillage et la qualité de la poudre sont essentielles pour obtenir la densité et la résistance souhaitées dans le produit final. Ceci est particulièrement important dans les industries telles que l'aérospatiale, l'automobile et le médical, où des composants fiables et de haute qualité sont cruciaux.
En résumé, le pressage isostatique à froid est une technique polyvalente de traitement des matériaux qui permet de comprimer des matériaux en poudre pour en faire des pièces solides. Le choix entre la technologie des sacs humides et celle des sacs secs dépend des exigences de production spécifiques. En outre, la qualité de la poudre et la conception de l'outillage jouent un rôle important dans l'obtention des résultats souhaités pour le produit final.
Types de pressage isostatique à froid
Description détaillée de la technique du sac humide
Dans la technique de pressage isostatique à froid avec sac humide, la poudre est placée dans un moule et scellée hermétiquement à l'extérieur de l'enceinte sous pression. Le moule rempli est ensuite immergé dans un fluide sous pression à l'intérieur de l'enceinte sous pression. Une pression isostatique est appliquée à la surface externe du moule, comprimant la poudre en une masse solide.
Cette méthode n'est pas aussi répandue que l'autre type de pressage isostatique à froid, mais plus de 3 000 presses à sacs humides sont utilisées dans le monde. Les sacs humides sont disponibles en différentes tailles, allant de 50 mm à 2000 mm de diamètre.
Le traitement des matériaux à l'aide de la technologie des sacs humides peut durer de 5 à 30 minutes, ce qui en fait un processus relativement lent. Toutefois, l'utilisation de pompes à haut volume et de mécanismes de chargement améliorés peut contribuer à accélérer le processus.
Explication de la technique de pressage en sac sec
La technique de pressage en sac sec, quant à elle, implique la création d'un moule intégré à l'enceinte sous pression. Dans ce processus, la poudre est ajoutée au moule, qui est ensuite scellé. La pression est appliquée et la pièce obtenue est éjectée.
Comparé à la technique de la poche humide, le procédé de la poche sèche se prête à l'automatisation et convient au pressage de longues séries de produits compacts à des taux de production élevés. L'intégration du moule dans l'enceinte sous pression élimine l'étape d'immersion, ce qui en fait une méthode plus efficace.
Comparaison des applications des deux techniques
Le choix entre la technique du sac humide et celle du sac sec dépend des exigences spécifiques de l'application. La technique du sac humide est idéale pour la production de formes multiples et de petites à grandes quantités, ainsi que pour le pressage de produits de grande taille. Elle permet de créer des formes complexes et d'obtenir une densité verte élevée.
En revanche, le pressage à sec est plus adapté à l'automatisation et aux cadences de production élevées. Il s'intègre plus facilement dans le processus de fabrication et élimine l'étape de l'immersion, ce qui se traduit par des temps de production plus courts.
En résumé, les techniques de pressage en sac humide et en sac sec ont toutes deux leurs avantages et sont utilisées dans différentes applications. Le choix entre les deux dépend de facteurs tels que la forme souhaitée, la quantité de production et le niveau d'automatisation requis.
Avantages du pressage isostatique à froid par rapport au pressage uniaxial sous pression
Possibilité de réaliser des formes plus complexes
Le pressage isostatique à froid (CIP) offre l'avantage de pouvoir former des formes plus complexes que le pressage uniaxial. Avec le CIP, la pression est appliquée uniformément sur toute la surface du moule, ce qui permet de compacter des formes complexes et détaillées. Cette technique est particulièrement avantageuse pour la fabrication de composants aux géométries ou conceptions complexes qu'il serait difficile de réaliser avec le pressage uniaxial.

Réduction des distorsions et des fissures grâce à l'uniformisation des particules
L'un des principaux avantages du pressage isostatique à froid par rapport au pressage uniaxial sous pression est la réduction des distorsions et des fissures dans le produit final. Dans le CIP, la pression est appliquée de manière uniforme, ce qui entraîne un tassement plus uniforme des particules et une réduction des gradients de pression. Il en résulte une distribution plus homogène de la densité et une réduction de la probabilité de distorsions et de fissures dans le composant fini. Cet avantage est particulièrement important lorsqu'il s'agit de pièces de forme complexe.
D'un point de vue technique, le CIP permet d'obtenir une densité plus élevée et plus uniforme à une pression de compactage donnée, ce qui le rend particulièrement adapté aux poudres fragiles ou fines. En outre, l'absence de frottement entre les parois de la matrice élimine les problèmes liés à l'élimination du lubrifiant et permet d'obtenir des densités de pressage plus élevées.
De plus, le CIP offre l'avantage d'un retrait plus régulier pendant le frittage en raison de la densité uniforme à l'état vert. Ceci est essentiel pour maintenir un bon contrôle de la forme et obtenir des propriétés uniformes dans le produit final. En outre, le CIP ne nécessite pas de liant en cire comme le pressage uniaxial sous pression, ce qui élimine le besoin d'opérations de déparaffinage.
En résumé, les avantages du pressage isostatique à froid par rapport au pressage uniaxial sous pression comprennent la capacité de former des formes plus complexes et la réduction des distorsions et des fissures grâce à l'emballage uniforme des particules. Ces avantages font du pressage isostatique à froid une méthode privilégiée pour la fabrication de composants à géométrie complexe et pour l'obtention de produits homogènes de haute qualité.
Pressage isostatique à froid dans la production de composants de forme complexe
Comparaison entre le pressage isostatique à froid et le moulage par injection pour la production de grands volumes
Lorsque des composants de forme complexe sont requis, au-delà des capacités de forme du pressage uniaxial sous pression, et qu'un grand volume de production est nécessaire, le CIP et le moulage par injection sont les deux principales options utilisées. La CIP a été la première méthode de haute technologie mentionnée dans la littérature pour la fabrication de céramiques d'alumine, par Daubenmeyer en 1934. En effet, les isolateurs de bougies d'allumage constituent probablement le plus grand volume de production de composants céramiques fabriqués par NEP dans le monde. Une proportion importante des 3 milliards d'isolateurs de bougies d'allumage fabriqués chaque année est traitée par NEP. Comme pour le pressage uniaxial sous pression, la matière première du CIP est généralement de l'alumine de Bayer simplement broyée, de l'alumine de Bayer broyée et séchée par pulvérisation ou, dans de rares cas, des nanopoudres SolGel de haute technologie séchées par pulvérisation. Toutefois, en général, le CIP n'est pas aussi répandu dans l'industrie que le moulage par injection. Elle n'est généralement utilisée que lorsque des formes très complexes sont requises et que le moulage par injection n'est pas pratique pour une raison ou une autre.
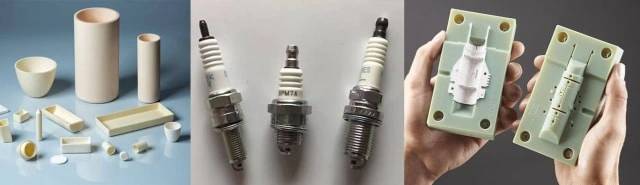
Aperçu historique de l'utilisation du CIP dans la fabrication des céramiques d'alumine
Le pressage isostatique à froid (CIP) est une technologie de production de pièces métalliques et céramiques à base de poudre et de forme presque nette. Le pressage isostatique à froid est couramment utilisé pour le traitement des céramiques, mais pas aussi largement pour les métaux. Des développements récents en matière de capacité de traitement et de métallurgie des poudres ont toutefois permis à la CIP d'être de plus en plus utilisée dans la fabrication de pièces métalliques de haute performance. Des avantages tels que le traitement à l'état solide, la microstructure uniforme, la complexité des formes, le faible coût de l'outillage et l'évolutivité du procédé ont fait de la NEP une voie de traitement viable pour les métaux. En outre, la possibilité de produire des pièces de forme presque nette avec un minimum de déchets de matériaux a rendu le procédé plus largement acceptable dans des applications de niche, telles que l'aérospatiale et l'automobile.
Utilisation de la CIP dans la production d'isolateurs de bougies d'allumage
Depuis des décennies, le pressage isostatique à froid (CIP) est utilisé avec succès par des fabricants du monde entier. La CIP est utilisée pour consolider les poudres métalliques et céramiques afin d'obtenir une pièce "verte" qui peut être traitée ultérieurement, par exemple par laminage, usinage ou frittage.
Avec des pressions typiques de 1 035 à 4 138 bars (15 000 à 60 000 psi) et une température ambiante allant jusqu'à 93°C (200°F), le CIP permet d'atteindre 95% de la densité théorique pour les céramiques.
Les applications courantes de la compression isostatique à froid comprennent la consolidation des poudres céramiques, la compression du graphite, des réfractaires et des isolateurs électriques, ainsi que d'autres céramiques fines destinées à des applications dentaires et médicales.
La technologie s'étend à de nouvelles applications telles que le pressage de cibles de pulvérisation, les revêtements de pièces de soupapes dans un moteur pour minimiser l'usure des culasses, les télécommunications, l'électronique, l'aérospatiale et l'automobile.
Presses isostatiques à froid
Les presses isostatiques à froid (CIP) d'EPSI sont utilisées pour produire des composants en poudre métallique non frittés ou compactés à l'aide de colorants verts lors d'une étape préliminaire de densification avant le laminage, l'usinage ou le frittage. Nos systèmes CIP sont utilisés par des entreprises du monde entier pour produire efficacement des composants sans défaut pour les industries aérospatiale, militaire, industrielle et médicale. Les leaders technologiques du monde entier savent que nos presses isostatiques à froid sont conçues de manière à ce que les pièces puissent être facilement retirées avec une résistance à l'état vert suffisante pour une manipulation et un frittage ultérieurs.
Pressage isostatique à froid
Le pressage isostatique à froid présente l'avantage de produire des pièces pour lesquelles le coût initial élevé des matrices de pressage ne se justifie pas ou lorsque des pièces compactes très grandes ou complexes sont nécessaires. Diverses poudres peuvent être pressées isostatiquement à l'échelle commerciale, notamment des métaux, des céramiques, des plastiques et des composites. Les pressions requises pour le compactage vont de moins de 5 000 psi à plus de 100 000 psi (34,5 à 690 MPa). Les poudres sont compactées dans des moules en élastomère, soit par voie humide, soit par voie sèche.
Les capacités des matériaux sont importantes à prendre en compte lors du choix des services de pressage isostatique à froid. Les alliages d'aluminium et de magnésium, les carbures et les outils de coupe, le carbone et le graphite, les céramiques et les composites ne sont que quelques-uns des matériaux et composants produits par le CIP. Certains services de pressage isostatique à froid sont spécialisés dans les revêtements et les dépôts par pulvérisation thermique, les alliages de cuivre, le diamant et les matériaux semblables au diamant. D'autres travaillent avec des matériaux électroniques ou électriques, des explosifs ou des produits pyrotechniques, ou encore des matériaux spécialisés et exclusifs.
QU'EST-CE QUE LE PRESSAGE ISOSTATIQUE À FROID ?
Le pressage isostatique à froid (CIP) est un procédé utilisé pour façonner et compacter des poudres en composants de tailles et de formes variées. Dans le cas du pressage isostatique à froid en sac humide, le matériau est préformé puis scellé dans un sac souple ou un moule. La poche est placée dans un fluide hydraulique (par exemple, de l'huile ou de l'eau) dans un récipient sous pression. Le fluide est soumis à une pression, généralement comprise entre 10 000 et 60 000 psi, qui est répartie uniformément sur le matériau. Cette méthode permet de réduire les déformations, d'améliorer la précision et de réduire le risque d'emprisonnement d'air et de vides. Elle est largement utilisée dans la production de composants pour des applications médicales, aérospatiales et automobiles.
Le contrôle dimensionnel est moins important avec le CIP qu'avec le pressage uniaxial. Pour reprendre l'exemple ci-dessus, si vous avez besoin d'un diamètre de 5 mm exactement, vous devrez procéder à des essais, des erreurs et des calculs dans votre moule et votre procédure de remplissage pour y parvenir. Mais une fois cette étape franchie, il s'agit d'un processus très reproductible qui offre des avantages indéniables. Il permet notamment de presser des pastilles à très long rapport d'aspect. Les bougies d'allumage sont un exemple d'article courant qui est pressé isostatiquement à froid à l'échelle industrielle.
Pressage isostatique à froid
Le pressage isostatique à froid (CIP) s'effectue à température ambiante et utilise un moule fabriqué à partir d'un matériau élastomère tel que l'uréthane, le caoutchouc ou le chlorure de polyvinyle. Le fluide utilisé pour le pressage isostatique à froid est généralement de l'huile ou de l'eau. La pression du fluide pendant l'opération est généralement comprise entre 60 000 livres/po2 (400 MPa) et 150 000 livres/po2 (1000 MPa). Ce procédé de fabrication présente l'inconvénient d'une faible précision géométrique en raison de la souplesse du moule. La poudre est d'abord compactée à une densité très uniforme par pressage isostatique à froid. Ensuite, le compact vert est généralement fritté de manière conventionnelle pour produire la pièce souhaitée.
Processus de pressage isostatique à froid
Explication du procédé CIP
Le pressage isostatique à froid (CIP) est une méthode de traitement des matériaux qui consiste à compacter des poudres en les enfermant dans un moule en élastomère. Le moule est fabriqué à partir de matériaux tels que l'uréthane, le caoutchouc ou le chlorure de polyvinyle, qui présentent une faible résistance à la déformation. Une pression liquide est ensuite appliquée uniformément sur le moule pour le comprimer. Ce processus est basé sur la loi de Pascal, qui stipule que la pression appliquée dans un fluide fermé est transmise dans toutes les directions sans changement de magnitude.
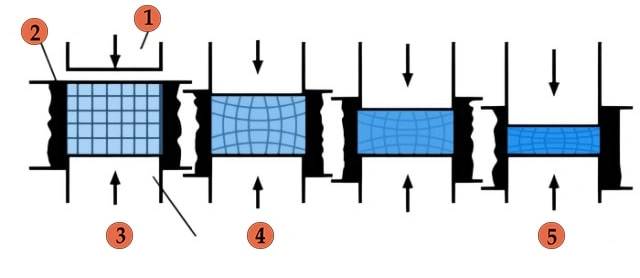
La CIP peut être utilisée pour divers matériaux tels que les plastiques, le graphite, la métallurgie en poudre, les céramiques et les cibles de pulvérisation. Il est généralement utilisé pour obtenir une pièce "brute" suffisamment résistante pour être manipulée et traitée, qui peut ensuite être frittée pour atteindre sa résistance finale.
Automatisation du procédé CIP
Le procédé CIP peut être automatisé à l'aide d'un équipement spécialisé. Le matériau à traiter est scellé dans un moule en élastomère et placé dans une chambre de pression. Un liquide, tel que de l'eau ou de l'huile, est pompé dans la chambre et le moule est uniformément soumis à une pression élevée de tous les côtés. Cette automatisation garantit une application cohérente et précise de la pression, ce qui permet d'obtenir des produits finis de grande qualité.
L'automatisation du processus de NEP offre plusieurs avantages. Elle améliore l'efficacité en réduisant le travail manuel et en augmentant les taux de production. Elle garantit également une application cohérente de la pression, ce qui améliore la qualité et la fiabilité globales des produits finis. En outre, l'automatisation permet de mieux contrôler et surveiller les paramètres du processus, ce qui conduit à une meilleure optimisation du processus et à des économies.
Cycles de pressurisation et de dépressurisation dans le NEP
Le procédé CIP implique des cycles de pressurisation et de dépressurisation pour obtenir le compactage souhaité des poudres. Pendant le cycle de pressurisation, le milieu liquide est pompé dans la chambre de pression, appliquant une pression uniforme au moule en élastomère. Cette pression compacte les poudres et forme un solide très compact.
Une fois le compactage souhaité obtenu, le cycle de dépressurisation commence. La pression dans la chambre est progressivement relâchée, ce qui permet au moule de se détendre et au matériau compacté d'être retiré. Ce cycle garantit que le matériau compacté peut être facilement extrait du moule sans déformation ni dommage.
Les cycles de pressurisation et de dépressurisation sont soigneusement contrôlés pour obtenir la densité et la résistance souhaitées du matériau compacté. Les paramètres, tels que l'amplitude de la pression, la durée et la vitesse de changement, peuvent être ajustés en fonction des exigences spécifiques du matériau traité.
En conclusion, le pressage isostatique à froid (CIP) est une méthode polyvalente de compactage des poudres et de mise en forme des matériaux. En enfermant les poudres dans un moule en élastomère et en appliquant une pression uniforme, le CIP peut produire des solides très compacts pour diverses applications. L'automatisation du processus de CIP offre une efficacité et un contrôle accrus, tandis que les cycles de pressurisation et de dépressurisation garantissent la densité et la résistance souhaitées du matériau compacté.
Avantages du pressage isostatique à froid pour les céramiques d'alumine
Comparaison entre le pressage isostatique à froid et le pressage uniaxial sous pression et d'autres méthodes de formage des céramiques
Le pressage isostatique à froid (CIP) est une technologie à base de poudre, proche de la forme nette, pour la production de composants métalliques et céramiques. Le CIP est couramment utilisé pour le traitement des céramiques, mais pas aussi largement pour les métaux. Des développements récents en matière de capacité de traitement et de métallurgie des poudres ont toutefois permis à la CIP d'être de plus en plus utilisée dans la fabrication de pièces métalliques de haute performance. Des avantages tels que le traitement à l'état solide, l'uniformité de la microstructure, la complexité des formes, le faible coût de l'outillage et l'évolutivité du procédé ont fait de la CIP une voie de traitement viable pour les métaux.
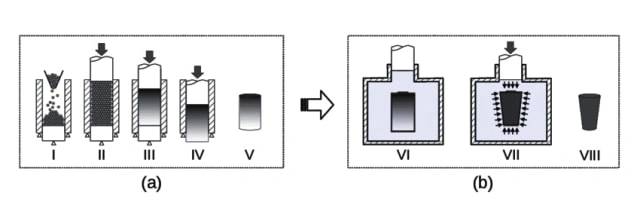
Voici quelques-uns des principaux avantages du CIP pour les céramiques d'alumine par rapport au pressage uniaxial sous pression :
-
Des formes plus complexes sont possibles : Le CIP permet de produire des formes plus complexes que le pressage uniaxial. En effet, le CIP utilise des moules flexibles qui peuvent s'adapter à des conceptions et des formes complexes.
-
Gradients de pression fortement réduits : La CIP réduit considérablement les gradients de pression de pressage, ce qui permet de minimiser les déformations et les fissures au cours du processus de formage. Cela garantit que les composants céramiques finaux présentent une précision dimensionnelle et une intégrité structurelle accrues.
Avantages du NEP pour les pièces complexes produites en petites séries
Le NEP offre plusieurs avantages pour la production de pièces complexes en petites séries. Ces avantages sont les suivants
-
Faible coût du moule : Le procédé CIP nécessite un coût de moule peu élevé, ce qui le rend idéal pour la production de pièces complexes en petites séries. Contrairement à d'autres méthodes de formage de la céramique, le CIP ne nécessite pas de moules coûteux, ce qui contribue à réduire les coûts de fabrication.
-
Pas de coût de moule pour l'après-PCI : Outre le faible coût des moules, le procédé CIP élimine également le besoin de moules pour les procédés post-CIP. Cela réduit encore les coûts de production et permet une plus grande flexibilité dans la fabrication de pièces complexes.
-
Pas de limitation de taille : La NEP n'a pas de limites de taille, à l'exception des limites de la chambre de pressage. Il convient donc à la production de pièces de très grande taille, en particulier celles qui présentent des formes complexes. En fait, des pièces pesant plus d'une tonne ont été produites avec succès grâce au procédé CIP.
-
Des cycles de traitement courts : La NEP a des cycles de traitement courts car elle ne nécessite pas de séchage ou de combustion du liant. Cela signifie que les composants céramiques formés peuvent être frittés plus rapidement qu'avec d'autres méthodes, ce qui accroît l'efficacité de la production.
Si la NEP offre de nombreux avantages pour les céramiques d'alumine, il est important de noter certaines de ses limites. Il s'agit notamment d'un contrôle dimensionnel limité, d'une complexité de forme inférieure à celle du moulage par injection de poudre (MIP) et de la nécessité d'utiliser des poudres ayant une excellente fluidité.
Dans l'ensemble, le pressage isostatique à froid est une méthode polyvalente et rentable pour produire des céramiques d'alumine de formes complexes et en petites séries. Ses avantages en termes de complexité des formes, de réduction des gradients de pression, de faible coût des moules et de rapidité de traitement en font un choix populaire dans diverses industries telles que l'automobile, l'aérospatiale et les télécommunications.
Inconvénients de la presse isostatique à froid pour les céramiques
Difficultés liées au contrôle des dimensions et à la complexité des formes
Le pressage isostatique à froid (CIP) est un procédé de compactage des poudres utilisé pour obtenir des pièces prêtes à être frittées. Cependant, le contrôle des dimensions et la complexité des formes posent certains problèmes lors de l'utilisation du CIP pour les céramiques.
La précision moindre des surfaces pressées adjacentes à la poche souple par rapport au pressage mécanique ou à l'extrusion nécessite souvent un usinage ultérieur. Cela signifie que des étapes supplémentaires peuvent être nécessaires pour obtenir les dimensions et la forme souhaitées des pièces en céramique.
Exigences relatives aux poudres utilisées dans le NEP
L'un des inconvénients du pressage isostatique à froid est qu'une poudre séchée par pulvérisation relativement coûteuse est normalement nécessaire pour les presses à sacs secs entièrement automatiques. Cela peut augmenter le coût global du processus, car il faut utiliser des poudres spécialisées.
En outre, les taux de production du CIP sont inférieurs à ceux de l'extrusion ou du compactage par filière. Cela signifie que le procédé peut ne pas être aussi efficace en termes de production en volume.
En résumé, si le pressage isostatique à froid offre des avantages tels que la possibilité de produire des compacts complexes ou de grande taille et l'utilisation d'une grande variété de poudres, il présente également certains inconvénients. Il s'agit notamment des difficultés liées au contrôle des dimensions et à la complexité des formes, ainsi que des exigences en matière de poudres spécialisées et des taux de production inférieurs à ceux d'autres méthodes de formage.
Applications du pressage isostatique à froid
Utilisation courante du pressage isostatique à froid dans la production de masse de céramiques de pointe
Le pressage isostatique à froid (CIP) est une technologie à base de poudre, proche de la forme nette, couramment utilisée pour le traitement des céramiques. Elle présente l'avantage de pouvoir produire des pièces lorsque le coût initial élevé des matrices de pressage ne se justifie pas ou lorsque des pièces compactes très grandes ou complexes sont nécessaires.

Diverses poudres peuvent être pressées isostatiquement à l'échelle commerciale, notamment les métaux, les céramiques, les plastiques et les composites. Les pressions requises pour le compactage vont de moins de 5 000 psi à plus de 100 000 psi. Les poudres sont compactées dans des moules en élastomère, soit par voie humide, soit par voie sèche.
Le CIP a été largement utilisé pour la consolidation de poudres céramiques, de graphite, de matériaux réfractaires, d'isolateurs électriques et pour la compression de céramiques avancées. Des matériaux tels que le nitrure de silicium, le carbure de silicium, le nitrure de bore, le carbure de bore, le borure de titane et le spinelle peuvent être traités par NEP.
La technologie s'étend à de nouvelles applications telles que la compression de cibles de pulvérisation, le revêtement de composants de soupapes utilisés pour réduire l'usure des cylindres dans les moteurs, et diverses applications dans les télécommunications, l'électronique, l'aérospatiale et l'industrie automobile.
Exemples de composants produits par CIP
Le procédé CIP est couramment utilisé pour la consolidation de poudres céramiques, la compression de graphite, de réfractaires et d'isolateurs électriques, ainsi que d'autres céramiques fines pour des applications dentaires et médicales. Il est également utilisé pour le pressage de cibles de pulvérisation, le revêtement de pièces de soupapes dans les moteurs afin de minimiser l'usure des culasses, et dans diverses applications dans les télécommunications, l'électronique, l'aérospatiale et l'industrie automobile.
Les équipements de NEP sont utilisés pour comprimer les coûts de production et sont essentiels pour fabriquer des produits finis à partir de matières premières. Le processus consiste à confiner des poudres dans un moule en élastomère, à placer le moule dans une chambre de pression, à pomper un milieu liquide et à soumettre uniformément le moule à une pression élevée de tous les côtés. Le CIP peut être utilisé avec des poudres métallurgiques, des carbures cémentés, des matériaux réfractaires, du graphite, des céramiques, des plastiques et d'autres matériaux.
Il est important de tenir compte des capacités des matériaux lors du choix des services de pressage isostatique à froid. Les alliages d'aluminium et de magnésium, les carbures et les outils de coupe, le carbone et le graphite, les céramiques, les composites et d'autres matériaux peuvent être produits par CIP. Certains services de pressage isostatique à froid se spécialisent dans les revêtements et les dépôts par projection thermique, les alliages de cuivre, le diamant et les matériaux semblables au diamant, les matériaux électroniques ou électriques, les explosifs ou la pyrotechnie, ou encore les matériaux spécialisés et propriétaires.
Le pressage isostatique à froid s'effectue à température ambiante et utilise un moule fabriqué à partir d'un matériau élastomère tel que l'uréthane, le caoutchouc ou le chlorure de polyvinyle. Le fluide utilisé pour le pressage isostatique à froid est généralement de l'huile ou de l'eau, et la pression du fluide pendant l'opération est généralement comprise entre 60 000 lb/po2 et 150 000 lb/po2. L'inconvénient de ce procédé de fabrication est la faible précision géométrique due à la souplesse du moule.
En résumé, le pressage isostatique à froid (CIP) est une technique précieuse pour la production en masse de céramiques avancées et d'autres matériaux. Elle offre des avantages tels que le traitement à l'état solide, une microstructure uniforme, la complexité des formes, un faible coût d'outillage et l'évolutivité du processus. La CIP est largement utilisée dans diverses industries et continue de s'étendre à de nouvelles applications.
Autres technologies de compression
Aperçu des autres technologies de compression
Dans le domaine du traitement des matériaux, il existe plusieurs techniques de compression puissantes. Deux d'entre elles, le pressage isostatique à froid (CIP) et le pressage isostatique à chaud (HIP), sont largement utilisées dans diverses industries. Bien que ces deux méthodes visent à améliorer les propriétés des matériaux, elles diffèrent par leurs conditions de fonctionnement et offrent des avantages uniques.
Introduction du compactage par ondes de choc comme alternative
Bien que le CIP et le HIP soient des techniques de compression efficaces, des technologies alternatives ont été développées pour répondre à des défis spécifiques. L'une d'entre elles est le compactage par ondes de choc, également connu sous le nom de compression par choc.
Le compactage par ondes de choc implique la génération d'une courte onde de choc à haute pression qui peut déformer gravement les particules ou même provoquer une fusion locale. Ce processus peut permettre au matériau de devenir totalement dense et compact sans croissance significative des grains. Les ondes de choc se caractérisent par des pressions très élevées, des températures moyennes, des temps de réaction très courts et des vitesses de déformation très élevées.
Diverses méthodes, telles que les canons à air et les ondes de choc explosives, qui étaient auparavant utilisées pour la compression de poudres de taille micrométrique, sont maintenant utilisées pour comprimer les nanopoudres. Ces technologies de compression alternatives, avec des temps de chauffage très courts, ont permis d'obtenir des matériaux entièrement denses et compacts sans grossissement des nanograins.
Un exemple de compactage par ondes de choc est l'utilisation d'un dispositif de compactage par ondes de choc planes équipé d'un pistolet à air. Ce dispositif génère une courte onde de choc à haute pression qui peut déformer les particules et atteindre une densité et un compactage complets. Ces technologies de compression alternatives offrent un moyen efficace de traiter les matériaux avec une croissance minimale des grains et des propriétés améliorées.
Dans l'industrie du caoutchouc, les presses à compression avancées sont utilisées pour une vulcanisation efficace du caoutchouc. En appliquant une force de pression contrôlée sur les matériaux en caoutchouc, ces machines testent les caractéristiques physiques des produits en caoutchouc, telles que la résistance, l'élasticité et la durabilité, garantissant qu'ils répondent aux normes ASTM et sont de haute qualité.
Dans l'ensemble, les technologies de compression alternatives telles que le compactage par ondes de choc offrent des solutions innovantes pour obtenir des matériaux entièrement denses et compacts aux propriétés améliorées. Ces technologies offrent des avantages uniques et peuvent être utilisées dans diverses industries pour améliorer les capacités de traitement des matériaux.
Conclusion
En conclusion, le pressage isostatique à froid (CIP)le pressage isostatique à froid (CIP) est une technique très polyvalente et efficace pour la fabrication de composants de forme complexe, en particulier dans la production de céramiques avancées. Contrairement au pressage uniaxial traditionnel, le CIP permet la formation de formes plus complexes et réduit le risque de distorsions et de fissures grâce à l'uniformité de l'empaquetage des particules. Bien que le contrôle des dimensions et les exigences en matière de poudre posent des problèmes, la NEP offre des avantages significatifs pour les petites séries et est largement utilisée dans la production de masse de céramiques de pointe. Le compactage par ondes de choc est une alternative au NEP qui mérite d'être envisagée pour certaines applications de compression.
CONTACTEZ-NOUS POUR UNE CONSULTATION GRATUITE
Les produits et services de KINTEK LAB SOLUTION ont été reconnus par des clients du monde entier. Notre personnel se fera un plaisir de répondre à toute demande que vous pourriez avoir. Contactez-nous pour une consultation gratuite et parlez à un spécialiste produit pour trouver la solution la plus adaptée aux besoins de votre application !