La cémentation est un processus de traitement thermique qui introduit du carbone dans la surface de l'acier à faible teneur en carbone afin d'améliorer sa dureté et sa résistance à l'usure.Il existe cinq méthodes principales de cémentation, chacune ayant ses propres caractéristiques, avantages et applications.Il s'agit de la cémentation en caisse, de la cémentation au gaz, de la cémentation liquide, de la cémentation sous vide et de la cémentation au plasma.Chaque technique varie en fonction du milieu utilisé pour introduire le carbone, de l'équipement requis et des résultats spécifiques obtenus.Il est essentiel de comprendre ces méthodes pour choisir la technique la plus appropriée en fonction des propriétés souhaitées de l'acier et des exigences spécifiques de l'application.
Explication des points clés :
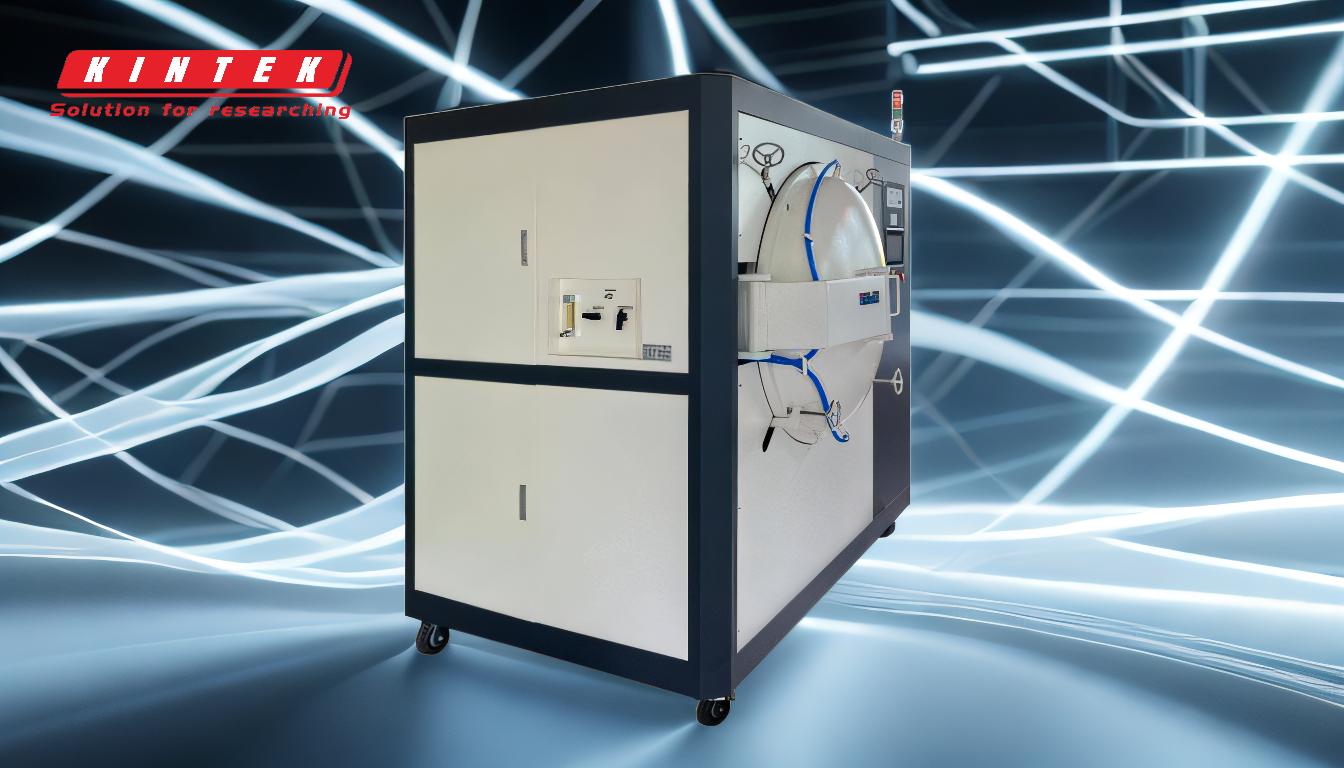
-
La cémentation en caisse
- Procédé:Dans la cémentation en caisse, les pièces d'acier sont placées dans un conteneur contenant un matériau riche en carbone, tel que du charbon de bois ou du coke.Le conteneur est ensuite chauffé dans un four à une température comprise entre 900°C et 950°C, ce qui permet au carbone de se diffuser dans la surface de l'acier.
- Les avantages:Cette méthode est rentable et convient aux grands lots de pièces.Elle permet d'obtenir une grande profondeur de cémentation, ce qui est bénéfique pour les pièces nécessitant une grande résistance à l'usure.
- Inconvénients:Le processus prend du temps et le potentiel de carbone est difficile à contrôler avec précision.En outre, les pièces peuvent nécessiter un nettoyage supplémentaire après le processus en raison du matériau d'emballage riche en carbone.
-
Carburage au gaz
- Procédé:La cémentation au gaz consiste à chauffer les pièces d'acier dans un four avec une atmosphère gazeuse riche en carbone, généralement un mélange de méthane, de propane ou de gaz naturel.La température est maintenue entre 850°C et 950°C, ce qui permet au carbone de se diffuser dans la surface de l'acier.
- Les avantages:Cette méthode permet de mieux contrôler le potentiel de carbone et la profondeur de la cémentation par rapport à la cémentation en caisse.Elle est également plus rapide et plus efficace, ce qui la rend adaptée à la production en grande quantité.
- Inconvénients:L'équipement requis pour la cémentation au gaz est plus complexe et plus coûteux.En outre, le processus exige un contrôle minutieux de la composition du gaz pour garantir des résultats constants.
-
Carburation liquide
- Procédé:La cémentation liquide, également appelée cémentation en bain de sel, consiste à immerger les pièces d'acier dans un bain de sel fondu contenant des composés riches en carbone, tels que le cyanure de sodium ou le cyanure de potassium.La température est généralement maintenue entre 850°C et 950°C.
- Les avantages:Cette méthode permet un chauffage rapide et uniforme, ce qui se traduit par une profondeur de cémentation et une concentration de carbone constantes.Elle convient également aux pièces petites et complexes.
- Inconvénients:L'utilisation de sels à base de cyanure pose des problèmes d'environnement et de sécurité.En outre, les pièces doivent être soigneusement nettoyées après le processus afin d'éliminer les sels résiduels.
-
La cémentation sous vide
- Procédé:La cémentation sous vide est réalisée dans un four sous vide, où les pièces d'acier sont chauffées à des températures comprises entre 900°C et 1050°C dans un environnement à basse pression.Un gaz riche en carbone, tel que le méthane ou le propane, est introduit dans le four pour faciliter la diffusion du carbone.
- Avantages:Cette méthode offre un excellent contrôle du potentiel de carbone et de la profondeur de cémentation, ce qui permet d'obtenir des résultats cohérents et de haute qualité.Elle élimine également le risque d'oxydation et de décarburation, car le processus se déroule sous vide.
- Inconvénients:L'équipement nécessaire à la cémentation sous vide est coûteux et le processus est plus lent que les autres méthodes.Elle est généralement utilisée pour les composants de grande valeur pour lesquels la précision et la qualité sont essentielles.
-
Carburation au plasma
- Procédé:La cémentation par plasma, également connue sous le nom de cémentation ionique, consiste à placer les pièces d'acier dans une chambre à vide et à introduire un gaz riche en carbone, tel que le méthane.Un plasma est généré par l'application d'un champ électrique à haute tension, qui ionise le gaz et accélère les ions carbone vers la surface de l'acier.
- Les avantages:Cette méthode permet un contrôle précis du potentiel de carbone et de la profondeur de la cémentation, ce qui se traduit par une cémentation uniforme et de haute qualité.Elle est également plus rapide et plus économe en énergie que les méthodes traditionnelles.
- Inconvénients:L'équipement requis pour la cémentation au plasma est complexe et coûteux.En outre, le procédé est limité aux pièces de petite et moyenne taille en raison des contraintes de taille de la chambre à vide.
En conclusion, le choix de la méthode de cémentation dépend de plusieurs facteurs, notamment les propriétés souhaitées de l'acier, la taille et la complexité des pièces, le volume de production et les considérations de coût.Chaque méthode présente des avantages et des limites qui lui sont propres. Il est donc essentiel de sélectionner la technique la plus appropriée en fonction des exigences spécifiques de l'application.
Tableau récapitulatif :
Méthode | Aperçu du processus | Avantages et inconvénients | Inconvénients |
---|---|---|---|
Carburation en batterie | Pièces en acier emballées avec un matériau riche en carbone, chauffées à 900-950°C. | Rentable, grande profondeur de cémentation. | Prend du temps, contrôle difficile du carbone. |
Carburage au gaz | Acier chauffé dans une atmosphère de gaz riche en carbone (850-950°C). | Meilleur contrôle du carbone, plus rapide pour les grands volumes. | Équipement coûteux, nécessite une surveillance des gaz. |
Carburation liquide | Acier immergé dans un bain de sel fondu avec des composés de carbone (850-950°C). | Chauffage rapide et uniforme, idéal pour les petites pièces. | Préoccupations en matière d'environnement et de sécurité, post-nettoyage. |
Carburation sous vide | Acier chauffé dans un four sous vide avec un gaz riche en carbone (900-1050°C). | Contrôle précis, pas de risque d'oxydation. | Processus coûteux et plus lent. |
Carburation au plasma | Acier dans une chambre à vide avec un gaz riche en carbone ionisé (plasma). | Efficacité énergétique, résultats uniformes. | Équipement complexe, limité aux pièces petites/moyennes. |
Vous avez besoin d'aide pour choisir la méthode de cémentation adaptée à votre application ? Contactez nos experts dès aujourd'hui !