Le processus de recuit, bien que largement utilisé en métallurgie et en science des matériaux pour améliorer les propriétés des métaux et des alliages, présente plusieurs limites.Il s'agit notamment des contraintes liées au contrôle de la température, des exigences de temps, des défis spécifiques aux matériaux, de la consommation d'énergie et du potentiel d'oxydation de la surface.En outre, le processus ne permet pas toujours d'obtenir les propriétés souhaitées du matériau en raison de la complexité de la microstructure ou d'une mauvaise sélection des paramètres.Il est essentiel de comprendre ces limites pour optimiser le processus de recuit et garantir les résultats souhaités pour des applications spécifiques.
Explication des points clés :
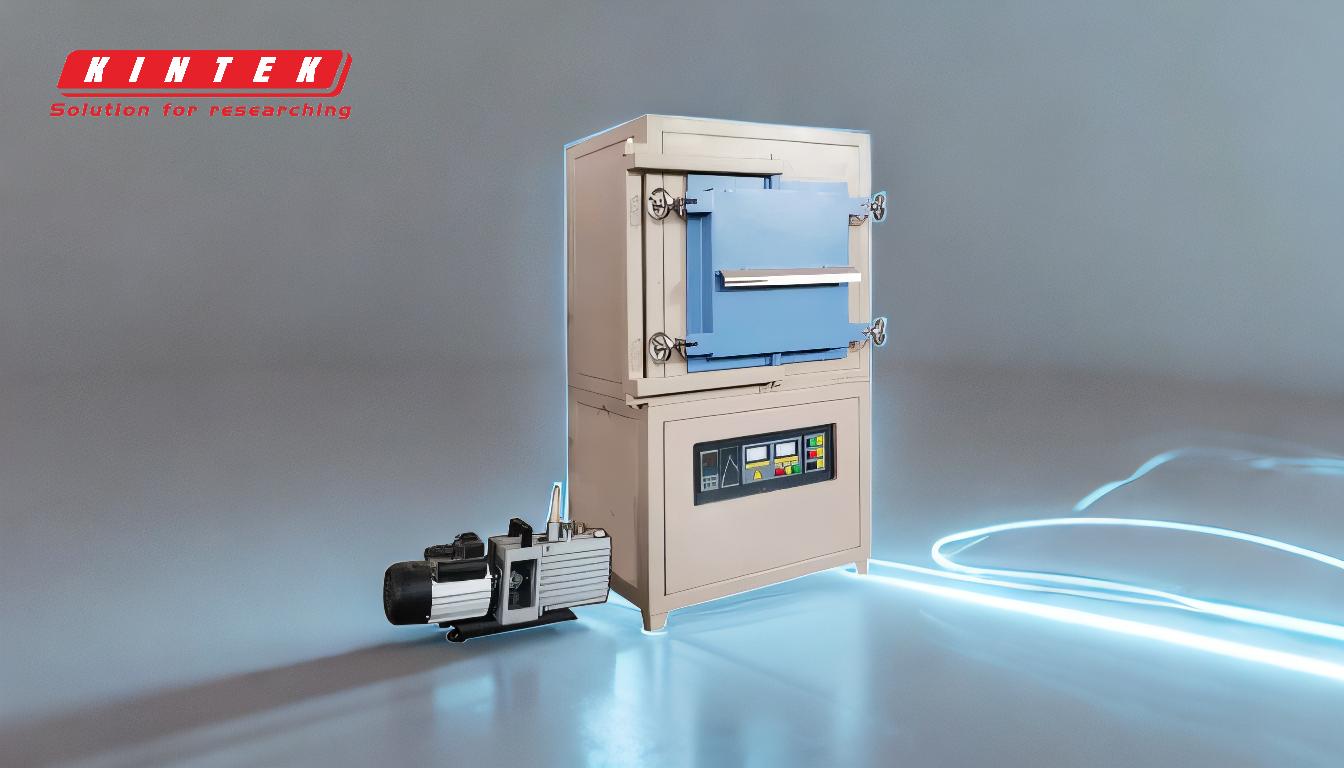
-
Défis en matière de contrôle de la température:
- Exigences de précision:Le recuit nécessite un contrôle précis de la température pour obtenir les propriétés souhaitées du matériau.De légers écarts peuvent entraîner une recristallisation incomplète ou des problèmes de croissance des grains.
- Limites de l'équipement:Tous les fours ne sont pas en mesure de maintenir des températures uniformes sur des pièces complexes ou de grande taille, ce qui entraîne des résultats irréguliers.
- Sensibilité des matériaux:Certains matériaux, tels que les aciers à haute teneur en carbone ou certains alliages, ont des plages de température étroites pour un recuit efficace, ce qui rend le processus plus difficile.
-
Contraintes de temps:
- Longs délais de traitement:Le recuit nécessite souvent des cycles de chauffage et de refroidissement prolongés, ce qui peut être long et inefficace pour une production en grande quantité.
- Sensibilité à la vitesse de refroidissement:Des vitesses de refroidissement lentes sont nécessaires pour certains matériaux afin d'éviter les contraintes internes, mais cela peut allonger les temps de traitement.
-
Limites propres aux matériaux:
- Microstructures non uniformes:Les matériaux dont la composition est hétérogène ou qui ont subi des traitements antérieurs peuvent ne pas réagir uniformément au recuit.
- Questions relatives à la croissance des grains:Un recuit excessif peut entraîner une croissance excessive du grain, réduisant la résistance et la ténacité du matériau.
- Applicabilité limitée:Certains matériaux, tels que les composites non métalliques ou les céramiques, ne bénéficient pas d'un recuit significatif.
-
Consommation d'énergie:
- Besoins énergétiques élevés:Le maintien de températures élevées pendant de longues périodes consomme beaucoup d'énergie, ce qui rend le processus coûteux et moins respectueux de l'environnement.
- Inefficacité du traitement par lots:Le recuit par lots, bien que courant, est moins efficace sur le plan énergétique que les procédés de recuit en continu.
-
Oxydation de surface et décarburation:
- Risques d'oxydation:L'exposition à des températures élevées en présence d'oxygène peut entraîner une oxydation de la surface, dégradant ainsi la qualité du matériau.
- Décarburation:Dans les aciers, un chauffage prolongé peut entraîner une perte de carbone à la surface, ce qui réduit la dureté et la résistance à l'usure.
-
Complexité du processus et compétences requises:
- Optimisation des paramètres:Le choix de la température, de la durée et de la vitesse de refroidissement correctes pour le recuit requiert de l'expertise et de l'expérimentation.
- Traitements post-cuisson:Des procédés supplémentaires, tels que la trempe ou le revenu, peuvent être nécessaires pour obtenir les propriétés souhaitées, ce qui ajoute à la complexité.
-
Contraintes économiques et pratiques:
- Coût de l'équipement:Les fours de recuit et les systèmes de contrôle de la température de haute qualité peuvent être coûteux à l'achat et à l'entretien.
- Exigences en matière d'espace:Les opérations de recuit à grande échelle nécessitent un espace important, ce qui n'est pas toujours possible dans les petites installations.
-
Résultats incohérents:
- Variabilité de la réponse des matériaux:Même avec des paramètres contrôlés, des variations dans la composition des matériaux ou dans le traitement préalable peuvent conduire à des résultats incohérents.
- Erreur humaine:Le contrôle manuel des processus de recuit augmente le risque d'erreurs, telles que des réglages de température ou de temps incorrects.
-
Amélioration limitée pour certaines propriétés:
- Compromis entre dureté et résistance:Le recuit réduit souvent la dureté et la résistance pour améliorer la ductilité, ce qui n'est pas forcément souhaitable pour toutes les applications.
- Impact limité sur les défauts:Si le recuit peut réduire les contraintes internes, il n'élimine pas nécessairement tous les défauts, tels que les vides ou les inclusions.
-
Préoccupations en matière d'environnement et de sécurité:
- Chaleur et émissions:Les processus à haute température génèrent de la chaleur et des émissions, ce qui nécessite une ventilation et des mesures de sécurité appropriées.
- Sécurité des travailleurs:La manipulation de matériaux chauds et l'utilisation d'équipements à haute température présentent des risques pour la sécurité.
En comprenant ces limites, les fabricants et les ingénieurs peuvent mieux concevoir les processus de recuit, sélectionner les matériaux appropriés et mettre en œuvre des traitements complémentaires pour obtenir des résultats optimaux.
Tableau récapitulatif :
Catégorie de limitation | Principaux défis |
---|---|
Contrôle de la température | Exigences de précision, limitations de l'équipement, sensibilité des matériaux |
Contraintes de temps | Temps de traitement longs, sensibilité à la vitesse de refroidissement |
Problèmes spécifiques aux matériaux | Microstructures non uniformes, croissance du grain, applicabilité limitée |
Consommation d'énergie | Besoins énergétiques élevés, inefficacité dans le traitement par lots |
Oxydation de surface | Risques d'oxydation, décarburation des aciers |
Complexité du processus | Optimisation des paramètres, traitements post-cuisson |
Contraintes économiques | Coût de l'équipement, espace nécessaire |
Résultats incohérents | Variabilité de la réponse des matériaux, erreur humaine |
Amélioration limitée des propriétés | Compromis dureté-résistance, élimination limitée des défauts |
Préoccupations environnementales | Chaleur et émissions, risques pour la sécurité des travailleurs |
Besoin d'aide pour optimiser votre processus de recuit ? Contactez nos experts dès aujourd'hui pour des solutions sur mesure !