Un four à induction à noyau direct, bien que très efficace et adapté aux opérations à haut rendement, présente plusieurs inconvénients importants.Ceux-ci comprennent la nécessité d'un entretien continu de la boucle métallique, l'impossibilité d'affiner les matériaux de charge, et l'obligation pour les matériaux de charge d'être exempts d'oxydes et d'une composition connue.En outre, le four est rarement autorisé à refroidir, ce qui peut compliquer les opérations et la maintenance.Ces facteurs le rendent moins flexible pour les opérations nécessitant des changements fréquents d'alliage ou celles impliquant des matériaux de composition variable.
Explication des points clés :
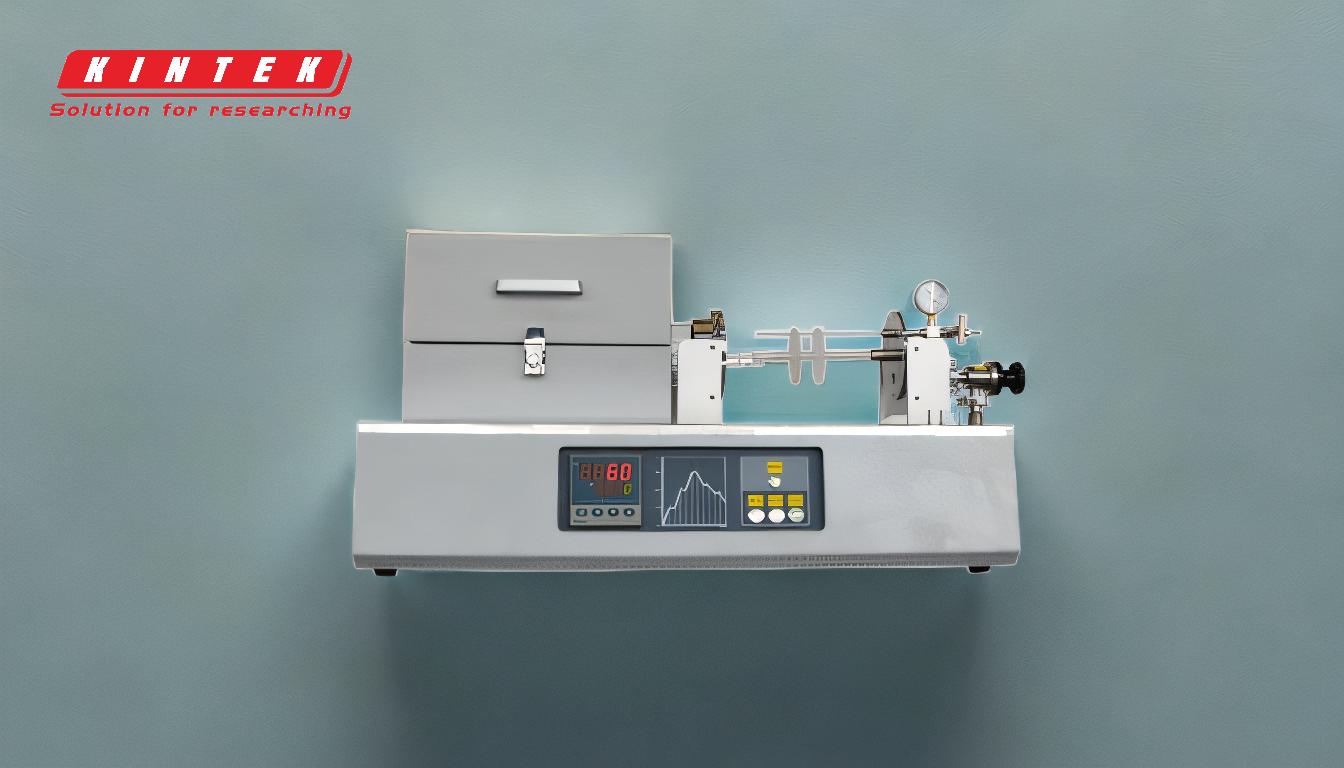
-
Entretien continu de la boucle métallique:
- Le four à induction à noyau direct nécessite un entretien permanent pour garantir que la boucle métallique reste intacte et fonctionnelle.Cet entretien permanent peut nécessiter une main-d'œuvre importante et entraîner une augmentation des coûts d'exploitation au fil du temps.
-
Manque de capacité de raffinage:
- Contrairement à d'autres types de fours, le four à induction à noyau direct n'a pas la capacité d'affiner les matériaux de charge.Cela signifie que les matériaux utilisés doivent déjà être exempts d'oxydes et avoir une composition connue, ce qui limite les types de matériaux pouvant être traités.
-
Oxydation et perte d'éléments d'alliage:
- Au cours du processus de fusion, certains éléments d'alliage peuvent être perdus en raison de l'oxydation.Il est alors nécessaire d'ajouter à nouveau ces éléments à la matière fondue, ce qui peut compliquer le processus et augmenter les coûts des matériaux.
-
Impossibilité de refroidir:
- Le four est rarement refroidi, ce qui peut compliquer les opérations et la maintenance.Ce fonctionnement continu peut entraîner l'usure des composants du four, ce qui risque de réduire la durée de vie globale de l'équipement.
-
Flexibilité limitée pour les changements d'alliage:
- Le four à induction à noyau direct n'est pas bien adapté aux opérations qui nécessitent des changements fréquents d'alliage.Ce manque de flexibilité peut constituer un inconvénient important pour les installations qui doivent traiter une variété de matériaux de compositions différentes.
-
Coûts initiaux et opérationnels élevés:
- Bien que le four soit efficace, les coûts d'installation et d'entretien peuvent être élevés.Cela comprend le coût de l'entretien de la boucle métallique et la nécessité de disposer de matériaux de charge de haute qualité et exempts d'oxyde.
-
Complexité du fonctionnement:
- L'exigence d'un fonctionnement continu et la nécessité d'un contrôle précis des matériaux de charge peuvent rendre le fonctionnement d'un four à induction à noyau direct plus complexe que celui d'autres types de fours.
En résumé, si le four à induction à noyau direct offre un rendement élevé et convient aux opérations à haut débit, ses inconvénients, notamment la nécessité d'une maintenance continue, le manque de capacité d'affinage et la flexibilité limitée pour les changements d'alliage, le rendent moins idéal pour certaines applications.Ces facteurs doivent être soigneusement pris en compte lors de la sélection d'un four pour des besoins industriels spécifiques.
Tableau récapitulatif :
Inconvénients | Explication |
---|---|
Entretien continu de la boucle métallique | Nécessite un entretien permanent, ce qui augmente les coûts de main-d'œuvre et d'exploitation. |
Manque de capacité d'affinage | Impossibilité d'affiner les matériaux de la charge ; les matériaux doivent être exempts d'oxyde et de composition connue. |
Oxydation et perte d'éléments d'alliage | Les éléments d'alliage peuvent s'oxyder, ce qui nécessite un nouvel ajout et augmente les coûts des matériaux. |
Impossibilité de refroidir | Le refroidissement est rarement autorisé, ce qui complique les opérations et la maintenance. |
Flexibilité limitée pour les changements d'alliage | Pas idéal pour les changements fréquents d'alliage ou les matériaux dont la composition varie. |
Coûts initiaux et opérationnels élevés | Coûts d'installation et de maintenance élevés, notamment en ce qui concerne l'entretien des boucles métalliques et la qualité des matériaux. |
Complexité d'exploitation | Le fonctionnement en continu et le contrôle précis des matériaux rendent l'exploitation plus complexe. |
Vous envisagez d'utiliser un four pour vos activités ? Contactez nos experts dès aujourd'hui pour trouver la solution la mieux adaptée à vos besoins !