Un réfractaire de four est un composant essentiel des fours industriels, conçu pour résister à des températures extrêmes et protéger la structure du four des effets corrosifs et thermiques des matériaux en fusion.Il agit comme un revêtement de travail, en interface directe avec l'aluminium en fusion ou d'autres matériaux à l'intérieur du four.Les réfractaires de four sont généralement fabriqués à partir de matériaux résistant aux températures élevées, tels que la fibre d'alumine de haute pureté, les briques réfractaires légères et le carbure de silicium (SiC).Ces matériaux assurent la durabilité, l'isolation thermique et l'efficacité énergétique, ce qui les rend essentiels pour maintenir des conditions de traitement cohérentes et empêcher les pertes de chaleur.Le revêtement réfractaire est souvent constitué de plusieurs couches afin d'améliorer les performances et la longévité.
Explication des points clés :
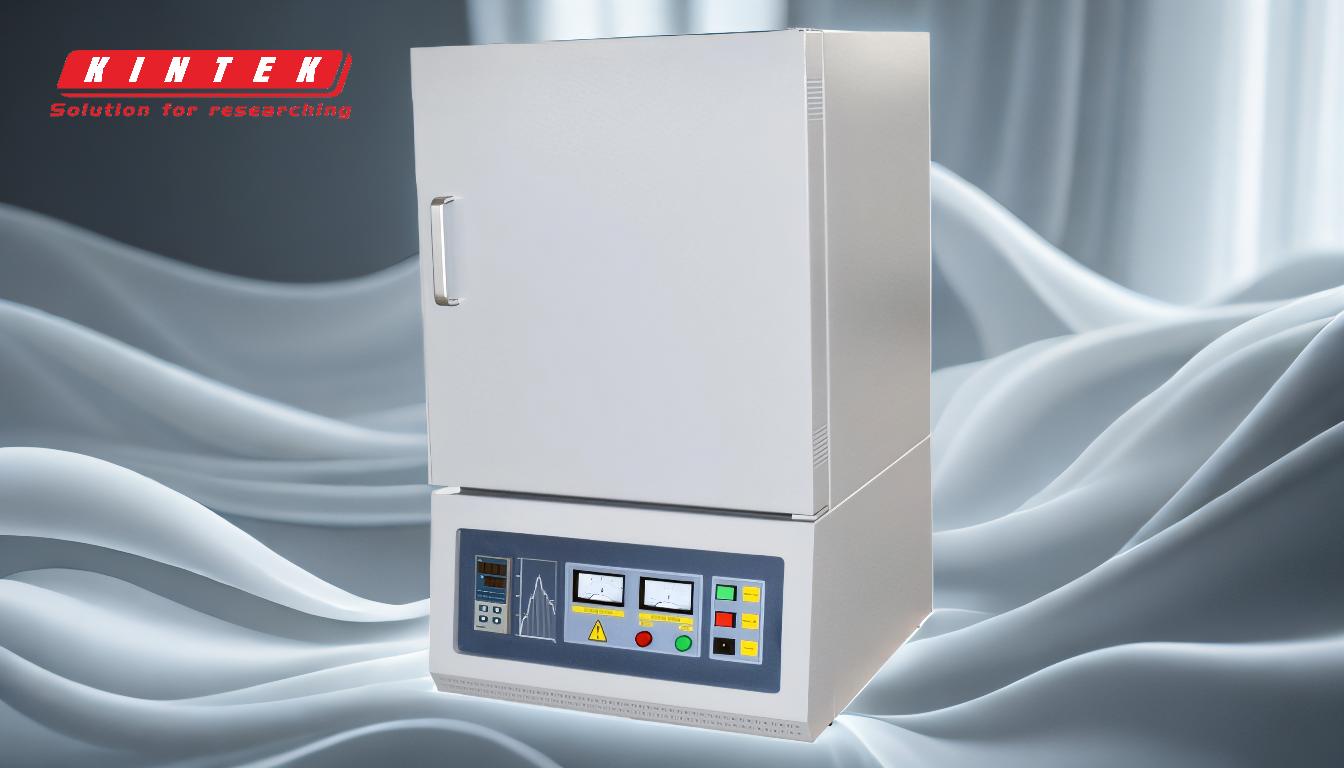
-
Définition et objectif des réfractaires de four:
- Un réfractaire de four est le revêtement céramique à l'intérieur d'un four qui interagit directement avec les matériaux en fusion, tels que l'aluminium.
- Son objectif principal est de protéger la structure du four de la chaleur extrême, de la corrosion chimique et des chocs thermiques, afin d'assurer un fonctionnement efficace et sûr du four.
-
Matériaux utilisés dans les réfractaires de four:
- Fibre d'alumine de haute pureté:Ce matériau est formé sous vide et utilisé pour sa capacité à supporter des températures élevées, à fournir une excellente isolation et à résister aux chocs thermiques.
- Briques réfractaires légères:Ces briques sont utilisées pour leur durabilité et leurs propriétés isolantes, réduisant les pertes de chaleur et la consommation d'énergie.
- Carbure de silicium (SiC):Le SiC est utilisé dans les barres chauffantes et les revêtements réfractaires en raison de sa résistance élevée, de sa conductivité thermique et de sa résistance à l'usure et à la corrosion.
-
Construction et conception des réfractaires de four:
- Les réfractaires des fours sont souvent construits en utilisant une conception d'isolation multicouche, combinant des matériaux tels que la fibre céramique d'alumine légère et des panneaux d'isolation de haute qualité.
- Cette approche multicouche améliore l'isolation thermique, réduit les pertes de chaleur et garantit que le four fonctionne avec une efficacité énergétique optimale.
- La conception évite les composants en amiante, ce qui la rend plus sûre et plus respectueuse de l'environnement.
-
Caractéristiques de performance:
- Température de service élevée:Les matériaux réfractaires sont conçus pour fonctionner à des températures extrêmement élevées sans se dégrader.
- Isolation thermique:Les matériaux utilisés offrent une excellente isolation, minimisant les pertes de chaleur et améliorant l'efficacité énergétique.
- Durabilité:Les revêtements réfractaires sont résistants à la fissuration, à la scorification et aux chocs thermiques, ce qui garantit une longue durée de vie et des performances constantes.
-
Applications dans différents types de fours:
- Fours de maintien et de fusion:Les revêtements réfractaires de ces fours sont essentiels pour maintenir la température et l'intégrité des métaux en fusion.
- Fours de frittage:Les fibres d'alumine de haute pureté et les briques en matériaux Morgan sont couramment utilisées dans les fours de frittage pour leur durabilité et leur efficacité dans les environnements à haute température.
- Fours à moufle:Ces fours utilisent de l'alumine très résistante ou des briques réfractaires isolantes pour garantir des conditions de traitement précises et uniformes.
-
Avantages des matériaux réfractaires modernes:
- Efficacité énergétique:L'utilisation de matériaux réfractaires avancés réduit les pertes de chaleur, ce qui permet de réduire la consommation d'énergie.
- Sécurité environnementale:Les réfractaires modernes sont exempts d'amiante, ce qui les rend plus sûrs pour les opérateurs et l'environnement.
- Rapid Heating and Cooling:Les matériaux tels que la fibre d'alumine de haute pureté permettent aux fours de chauffer et de refroidir rapidement, ce qui améliore l'efficacité opérationnelle.
-
Caractéristiques structurelles des corps de four:
- Les corps des fours sont souvent construits avec des coquilles en acier inoxydable, qui sont polies comme des miroirs pour des raisons de durabilité et d'esthétique.
- La conception comprend divers composants fonctionnels tels que les trous d'électrode, les trous d'aspiration, les trous d'aération, les trous de thermocouple et les trous d'observation, tous fabriqués en acier inoxydable pour la solidité et la résistance à la corrosion.
En comprenant ces points clés, les acheteurs d'équipements et de consommables peuvent prendre des décisions éclairées quant au choix des matériaux réfractaires et des conceptions adaptés à leurs applications de fours spécifiques, garantissant ainsi des performances, une efficacité énergétique et une longévité optimales.
Tableau récapitulatif :
Aspect | Détails |
---|---|
Objectif | Protège la structure du four de la chaleur extrême, de la corrosion et des chocs thermiques. |
Matériaux | Fibre d'alumine de haute pureté, briques réfractaires légères, carbure de silicium. |
Conception | Isolation multicouche pour une efficacité thermique et une durabilité accrues. |
Performances | Température de service élevée, excellente isolation et longue durée de vie. |
Applications | Fours de maintien, de fusion, de frittage et à moufle. |
Avantages | Efficacité énergétique, sécurité environnementale, chauffage/refroidissement rapide. |
Optimisez les performances de votre four avec les bons matériaux réfractaires. contactez nos experts dès aujourd'hui !