Les fours à résistance et les fours à induction sont tous deux largement utilisés dans les processus industriels de chauffage et de fusion, mais ils diffèrent considérablement dans leurs principes de fonctionnement, leur efficacité et leurs applications.Les fours à résistance s'appuient sur des éléments chauffants externes pour générer de la chaleur, qui est ensuite transférée au matériau, tandis que les fours à induction génèrent de la chaleur directement à l'intérieur du matériau en utilisant l'induction électromagnétique.Cette différence fondamentale entraîne des variations dans l'efficacité énergétique, les niveaux de contamination et les capacités opérationnelles.Les principales différences sont expliquées en détail ci-dessous.
Explication des principaux points :
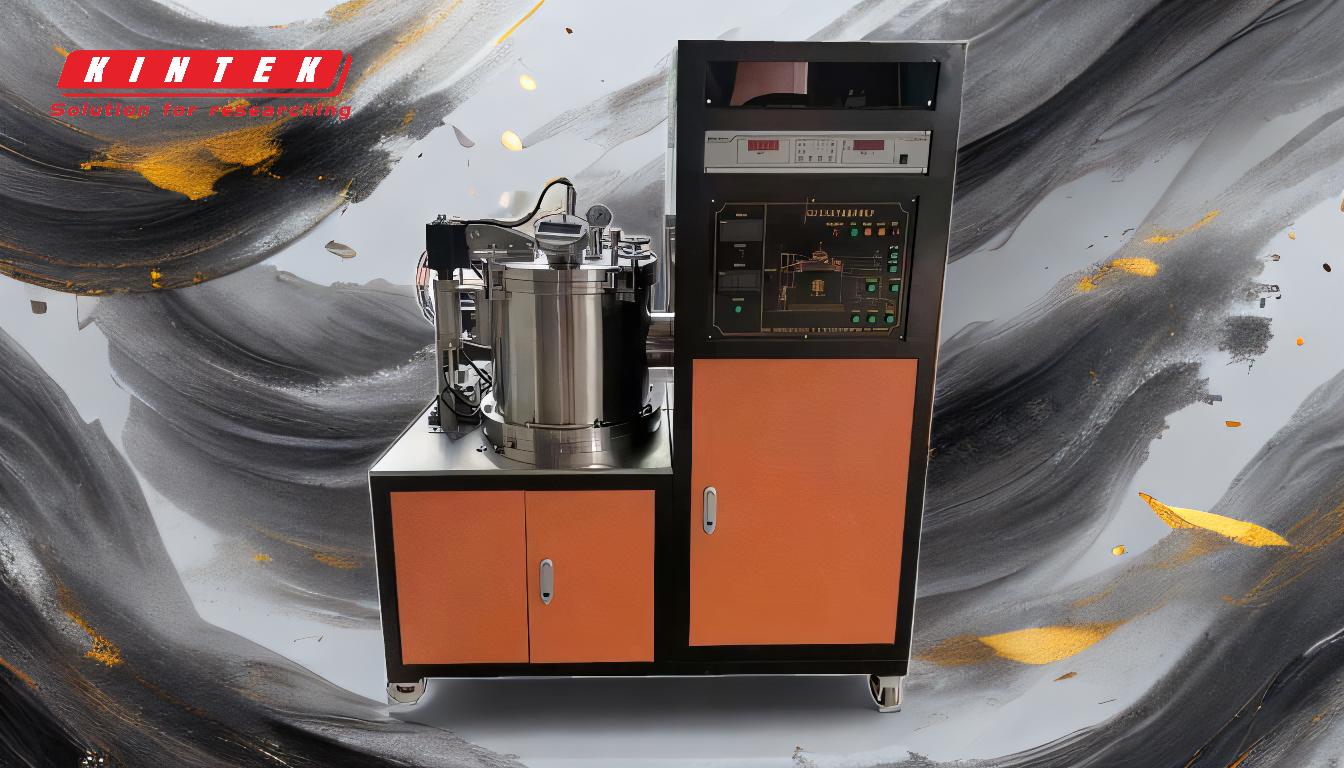
-
Mécanisme de chauffage:
-
Four à résistance:
- Utilise des éléments chauffants externes (par exemple, des éléments réfractaires ou des bobines) pour générer de la chaleur.
- La chaleur est transférée au matériau par conduction, convection ou radiation.
- Convient aux processus nécessitant un chauffage uniforme, mais la source de chaleur est externe au matériau.
-
Four à induction:
- Génère de la chaleur directement à l'intérieur du matériau grâce à l'induction électromagnétique.
- Le courant alternatif crée un champ magnétique alternatif, induisant des courants de Foucault dans le matériau, qui produisent de la chaleur en raison de la résistance.
- Il garantit un chauffage uniforme et minimise la contamination puisqu'il n'y a pas de source de chaleur externe.
-
Four à résistance:
-
Efficacité et consommation d'énergie:
-
Four à résistance:
- Moins efficace sur le plan énergétique en raison de la perte de chaleur lors du transfert de la source externe au matériau.
- Il faut plus d'énergie pour maintenir des températures élevées, en particulier dans les opérations à grande échelle.
-
Four à induction:
- Plus efficace sur le plan énergétique car la chaleur est générée directement dans le matériau, ce qui réduit les pertes de chaleur.
- Les vitesses de chauffage sont plus rapides et l'efficacité thermique plus élevée, ce qui en fait la solution idéale pour les applications à haute température.
-
Four à résistance:
-
Température et densité de puissance:
-
Four à résistance:
- Fonctionne à des densités de puissance inférieures à celles des fours à induction.
- Convient aux applications nécessitant des températures modérées (par exemple, recuit, trempe).
-
Four à induction:
- Capable de fonctionner à des températures et des densités de puissance plus élevées.
- Il peut atteindre des températures de forgeage allant jusqu'à 1250°C et des températures de fusion allant jusqu'à 1650°C, ce qui le rend adapté à la fusion et au traitement à haute température.
-
Four à résistance:
-
Contamination et pureté:
-
Four à résistance:
- Risque de contamination plus élevé en raison de l'utilisation d'éléments chauffants externes, qui peuvent introduire des impuretés.
- Nécessite une sélection minutieuse des éléments chauffants et des revêtements de four pour minimiser la contamination.
-
Four à induction:
- Contamination minimale car la chaleur est générée à l'intérieur du matériau lui-même.
- Idéal pour les applications nécessitant des matériaux de haute pureté, comme dans les industries des semi-conducteurs ou de l'aérospatiale.
-
Four à résistance:
-
Contrôle et automatisation:
-
Four à résistance:
- S'appuie généralement sur des systèmes de contrôle manuels ou semi-automatiques.
- Limité par la complexité du maintien d'un chauffage uniforme sur de grands volumes.
-
Four à induction:
- Équipé de systèmes de contrôle avancés, y compris le balayage automatique des fréquences, le contrôle de la puissance constante et des mécanismes de protection complets.
- Il offre un contrôle précis de la température et un fonctionnement souple, réduisant ainsi la nécessité d'une intervention manuelle.
-
Four à résistance:
-
Applications:
-
Four à résistance:
- Couramment utilisé pour les processus de traitement thermique tels que le recuit, la trempe et le revenu.
- Il convient au traitement par lots de matériaux qui ne nécessitent pas de températures extrêmement élevées.
-
Four à induction:
- Largement utilisé dans les applications de fusion et de forgeage, en particulier pour les métaux tels que l'acier, l'aluminium et le cuivre.
- Préféré pour les processus continus et les opérations à haute température où l'efficacité et la pureté sont essentielles.
-
Four à résistance:
-
Conception et entretien:
-
Four à résistance:
- Conception plus simple avec moins de composants, ce qui rend l'entretien relativement aisé.
- Toutefois, les éléments chauffants peuvent nécessiter un remplacement fréquent en raison de l'usure.
-
Four à induction:
- Conception plus complexe avec des composants tels que des inductances, des condensateurs et des systèmes de contrôle.
- Nécessite des considérations de conception minutieuses, telles que la disposition des culasses et l'espacement des inductances, afin de garantir des performances optimales.
- La maintenance est plus facile pour les modèles avancés dotés de circuits intégrés et de composants modulaires.
-
Four à résistance:
-
Adéquation des matériaux:
-
Four à résistance:
- Convient à une large gamme de matériaux, y compris les matériaux non métalliques et magnétiques.
- Limité par la capacité du matériau à absorber la chaleur d'une source externe.
-
Four à induction:
- Convient le mieux aux matériaux conducteurs, en particulier les métaux.
- Des problèmes se posent avec les matériaux non magnétiques tels que l'aluminium, qui nécessitent des inducteurs spécialisés pour garantir un chauffage efficace.
-
Four à résistance:
En résumé, les fours à résistance et les fours à induction servent des objectifs différents en fonction de leurs mécanismes de chauffage, de leur efficacité et de leurs applications.Les fours à résistance sont mieux adaptés aux processus à température modérée et aux opérations par lots, tandis que les fours à induction excellent dans les processus à haute température, à haute pureté et continus.Le choix entre les deux dépend des exigences spécifiques de l'application, notamment la température, le type de matériau et l'efficacité souhaitée.
Tableau récapitulatif :
Aspect | Four à résistance | Four à induction |
---|---|---|
Mécanisme de chauffage | Les éléments chauffants externes transfèrent la chaleur par conduction, convection ou radiation. | La chaleur est générée directement à l'intérieur du matériau par induction électromagnétique. |
Efficacité | Moins efficace sur le plan énergétique en raison de la perte de chaleur pendant le transfert. | Plus efficace sur le plan énergétique grâce à des vitesses de chauffage plus rapides et à une réduction des pertes de chaleur. |
Plage de température | Convient pour les températures modérées (par exemple, recuit, trempe). | Capable de températures élevées (jusqu'à 1650°C) pour la fusion et le forgeage. |
Risque de contamination | Risque plus élevé en raison des éléments chauffants externes. | Contamination minimale, idéale pour les applications de haute pureté. |
Systèmes de contrôle | Systèmes de contrôle manuels ou semi-automatiques. | Automatisation avancée avec contrôle précis de la température et mécanismes de protection. |
Applications | Procédés de traitement thermique (par exemple, recuit, trempe). | Fusion, forgeage et opérations à haute température pour des métaux tels que l'acier et l'aluminium. |
Conception et entretien | Conception plus simple, mais les éléments chauffants peuvent nécessiter des remplacements fréquents. | Conception complexe mais entretien plus facile pour les modèles avancés. |
Adaptation aux matériaux | Convient aux matériaux non métalliques et magnétiques. | Meilleur pour les matériaux conducteurs, en particulier les métaux. |
Vous avez besoin d'aide pour choisir le four adapté à votre application ? Contactez nos experts dès aujourd'hui pour des conseils personnalisés !