Le revêtement neutre d'un four à induction est un composant essentiel conçu pour protéger la structure du four et améliorer ses performances.Il est constitué de matériaux réfractaires capables de supporter des températures extrêmes et de résister aux réactions chimiques avec les métaux en fusion.Ce revêtement sert de barrière entre le métal en fusion et la structure extérieure du four, comme la bobine d'induction, ce qui garantit la longévité et l'efficacité du four.Il isole également le métal en fusion, empêchant toute contamination et préservant l'intégrité du métal en cours de fusion.Le revêtement neutre est essentiel au fonctionnement sûr et efficace des fours à induction, ce qui en fait un élément clé pour les acheteurs d'équipements et de consommables.
Explication des points clés :
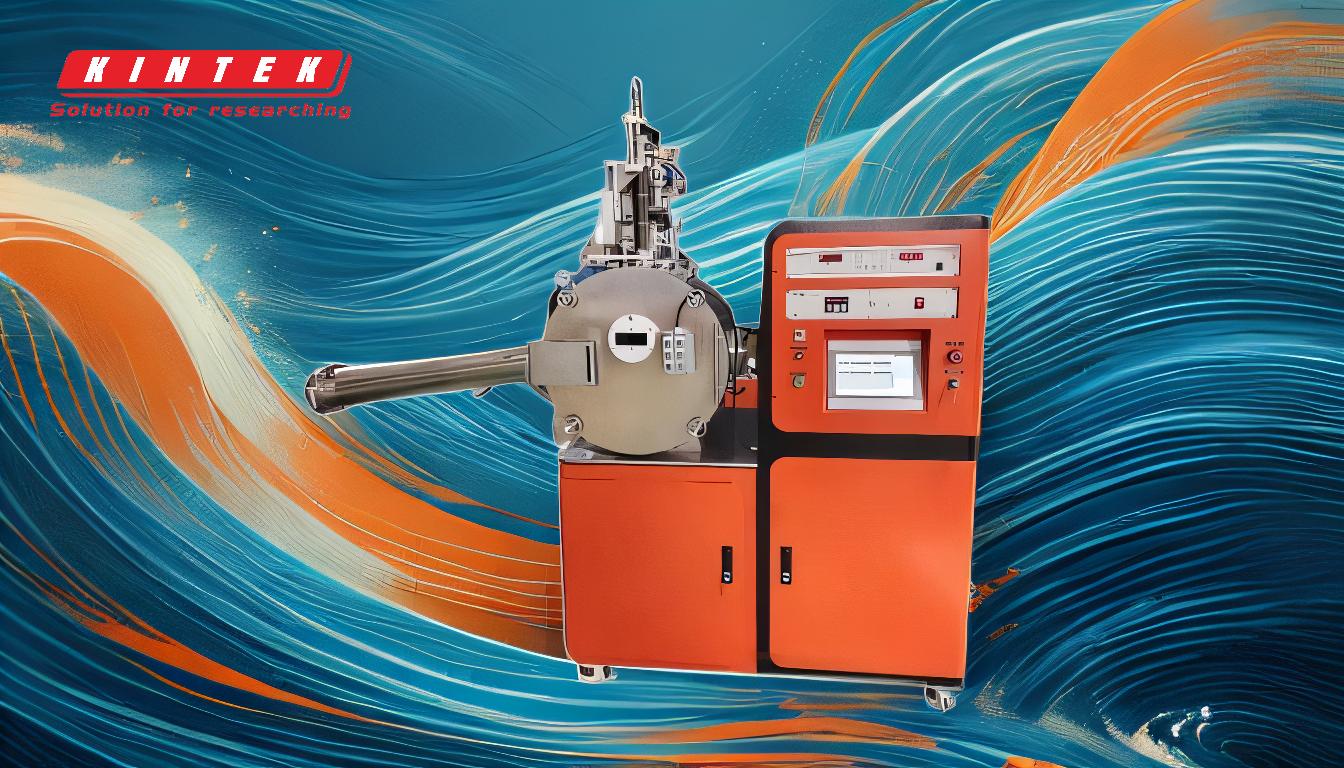
-
Définition et objectif du revêtement neutre :
- Le revêtement neutre est une couche protectrice à l'intérieur du four à induction, fabriquée à partir de matériaux réfractaires.
- Son objectif principal est de contenir le métal en fusion, de l'isoler de la structure extérieure du four et de protéger le corps du four pendant son fonctionnement.
- Il garantit le fonctionnement efficace et sûr du four en empêchant les réactions chimiques et les dommages thermiques.
-
Matériaux utilisés dans le revêtement neutre :
- Les matériaux réfractaires sont choisis pour leur capacité à supporter des températures élevées et à résister aux réactions chimiques avec les métaux en fusion.
- Les matériaux courants comprennent l'alumine, la silice et la magnésie, qui sont sélectionnés en fonction du type de métal fondu et des conditions de fonctionnement du four.
-
Rôle dans la protection de la structure du four :
- Le revêtement agit comme une barrière entre le métal en fusion et la bobine d'induction, empêchant tout contact direct et tout dommage potentiel.
- Il protège également le corps du four des contraintes thermiques et de l'usure mécanique, prolongeant ainsi la durée de vie du four.
-
Importance du maintien de l'intégrité du métal :
- En isolant le métal en fusion, le revêtement neutre empêche la contamination par des éléments extérieurs, ce qui garantit la pureté et la qualité du métal fondu.
- Cette caractéristique est particulièrement importante dans les applications exigeant des compositions d'alliage précises, notamment dans les secteurs de l'aérospatiale et de l'automobile.
-
Impact sur les performances du four :
- Un revêtement neutre bien entretenu garantit un transfert de chaleur efficace et une fusion uniforme de la charge métallique.
- Il minimise les pertes de chaleur et réduit la consommation d'énergie, contribuant ainsi à la rentabilité globale de l'exploitation du four.
-
Considérations pour les acheteurs :
- Lors du choix d'un revêtement neutre, les acheteurs doivent tenir compte du type de métal à fondre, de la température de fonctionnement et de la fréquence d'utilisation du four.
- Le choix du matériau réfractaire doit s'aligner sur les exigences spécifiques de l'application afin de garantir des performances et une durabilité optimales.
-
Entretien et remplacement :
- L'inspection et l'entretien réguliers du revêtement neutre sont essentiels pour éviter les fissures, l'érosion et d'autres formes d'usure.
- Le remplacement opportun du revêtement est nécessaire pour éviter les arrêts du four et garantir des performances constantes.
En résumé, le revêtement neutre d'un four à induction est un composant vital qui garantit le fonctionnement sûr, efficace et fiable du four.Il protège la structure du four, maintient l'intégrité du métal fondu et contribue aux performances globales du four.Pour les acheteurs d'équipements et de consommables, il est essentiel de comprendre le rôle et l'importance du revêtement neutre pour prendre des décisions éclairées et optimiser les opérations du four.
Tableau récapitulatif :
Aspect clé | Détails |
---|---|
Objectif | Protège la structure du four, isole le métal en fusion, assure la sécurité des opérations. |
Matériaux | Alumine, silice, magnésie - choisis pour leur résistance aux hautes températures. |
Rôle dans la protection | Agit comme une barrière, prévient les contraintes thermiques et l'usure mécanique. |
Intégrité du métal | Empêche la contamination, garantit la pureté et la qualité du métal fondu. |
Impact sur les performances | Améliore le transfert de chaleur, réduit la consommation d'énergie et améliore l'efficacité. |
Considérations relatives à l'achat | Adapter les matériaux réfractaires au type de métal, à la température et à la fréquence d'utilisation. |
L'entretien | Inspection régulière et remplacement en temps voulu pour éviter les temps d'arrêt. |
Veillez à ce que votre four à induction fonctionne de manière optimale. contactez nos experts dès aujourd'hui pour en savoir plus sur les revêtements neutres !