Le type de four utilisé pour fondre le métal brut dépend de l'application spécifique, de l'échelle et du débit souhaité.Pour la fusion industrielle des métaux, les fours les plus courants sont les suivants les fours à arc électrique et fours de fusion par induction .Les fours à arc électrique utilisent un arc électrique pour générer une chaleur intense, ce qui les rend adaptés à la fusion à grande échelle de métaux tels que l'acier.Les fours à induction, quant à eux, utilisent l'induction électromagnétique pour chauffer et faire fondre les métaux. Ils offrent un contrôle précis de la température et une grande efficacité, ce qui les rend idéaux pour les applications spécialisées ou à petite échelle.Ces deux types de fours sont largement utilisés dans l'industrie en raison de leur capacité à supporter des températures élevées et de grands volumes de métal brut.
Explication des principaux points :
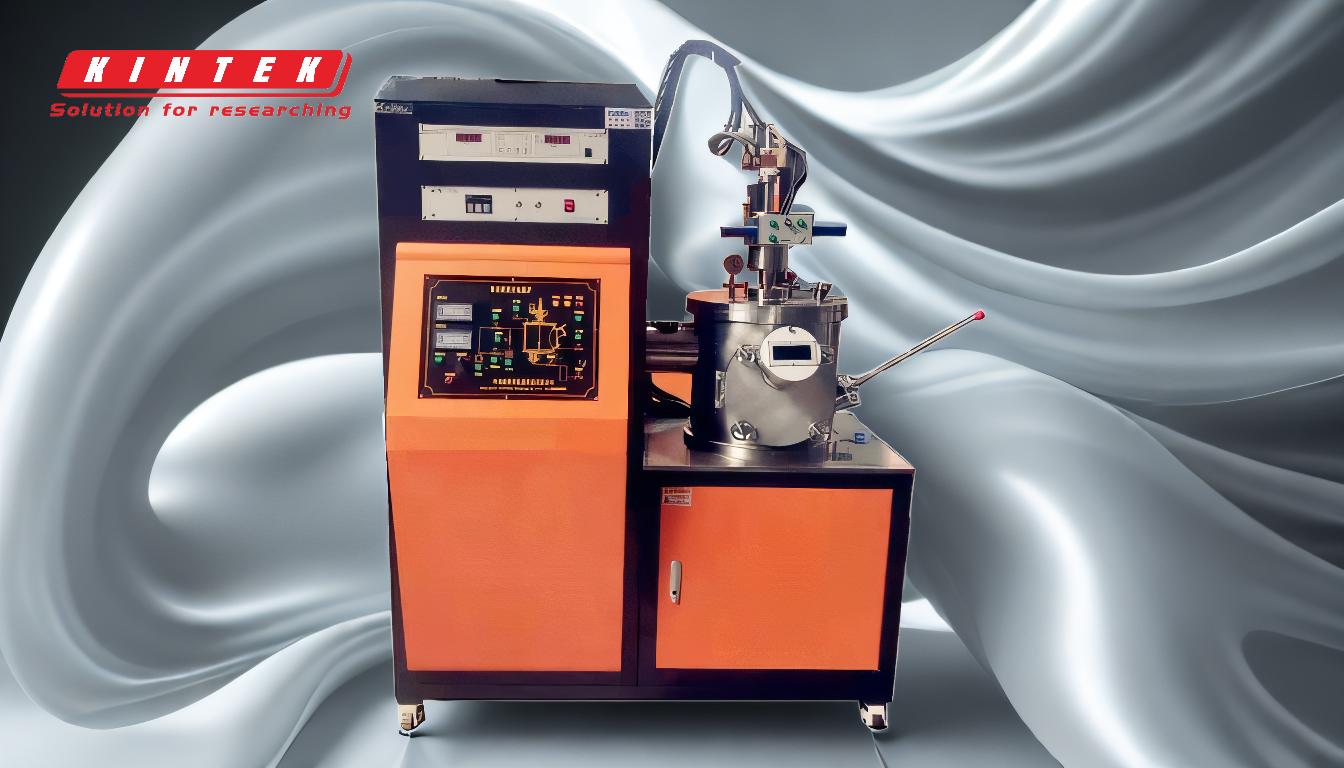
-
Les fours à arc électrique (FÉA) :
- Comment ils fonctionnent : Les fours à arc électrique génèrent de la chaleur grâce à un arc électrique formé entre les électrodes et le métal.Cet arc produit des températures suffisamment élevées pour faire fondre les métaux bruts tels que l'acier, le fer et les alliages.
- Applications : Les fours électriques à arc sont couramment utilisés dans les installations industrielles à grande échelle, en particulier dans la production d'acier.Ils sont appréciés pour leur capacité à recycler efficacement la ferraille.
-
Avantages :
- Débit élevé et capacité à traiter de gros volumes.
- Possibilité d'utiliser de la ferraille recyclée comme matière première.
- Flexibilité dans la production d'une large gamme de nuances d'acier.
-
Limites :
- Consommation d'énergie élevée.
- Nécessite une infrastructure et une maintenance importantes.
-
Fours de fusion à induction :
- Comment ils fonctionnent : Les fours à induction utilisent l'induction électromagnétique pour générer de la chaleur dans le métal lui-même.Une bobine transportant un courant alternatif crée un champ magnétique, induisant des courants de Foucault dans le métal, ce qui le chauffe et le fait fondre.
- Applications : Ces fours sont idéaux pour les opérations à petite échelle, la fusion de précision et les applications spécialisées telles que les fonderies et les laboratoires.
-
Avantages :
- Contrôle précis de la température, ce qui est essentiel pour l'alliage et l'affinage.
- Efficacité énergétique et respect de l'environnement, avec un minimum d'émissions.
- Conception compacte, ce qui permet de les utiliser dans des installations plus petites.
-
Limites :
- Capacité limitée par rapport aux fours à arc électrique, ce qui les rend moins adaptés à la production industrielle à grande échelle.
- Coût initial plus élevé en raison de la complexité du système électromagnétique.
-
Comparaison des fours à arc électrique et des fours à induction :
- Échelle : Les fours à arc électrique sont mieux adaptés aux opérations industrielles à grande échelle, tandis que les fours à induction sont idéaux pour les applications spécialisées ou à petite échelle.
- Efficacité énergétique : Les fours à induction sont généralement plus efficaces sur le plan énergétique, mais les fours électriques à arc ont l'avantage de traiter des volumes plus importants.
- Flexibilité des matériaux : Les deux types de fours peuvent traiter une grande variété de métaux, mais les fours électriques à arc sont particulièrement efficaces pour l'acier et le fer, tandis que les fours à induction excellent avec les métaux non ferreux comme l'aluminium et le cuivre.
- Coût : Les fours à induction ont des coûts initiaux plus élevés mais des coûts opérationnels plus faibles, alors que les fours électriques à arc nécessitent une infrastructure et une maintenance importantes.
-
Autres types de fours (informations contextuelles) :
- Bien que l'accent soit mis sur les fours de fusion, il convient de noter les autres types de fours mentionnés dans les références, tels que les fours à tambour rotatif , fours à sole roulante et les fours à dalles à poussoir .Ils sont généralement utilisés pour le frittage et le traitement thermique plutôt que pour la fusion.
- Les fours à bande sont utilisés pour les processus à basse température et ne conviennent pas aux températures élevées requises pour la fusion des métaux.
- Les fours continus Les fours continus (par exemple, les fours à plaques poussantes) sont courants dans la métallurgie des poudres et les applications industrielles à haut rendement, mais ne sont généralement pas utilisés pour fondre le métal brut.
-
Facteurs influençant le choix du four :
- Volume de production : Les opérations à grande échelle privilégient les fours à arc électrique, tandis que les opérations plus petites ou spécialisées peuvent opter pour des fours à induction.
- Type de matériau : Le type de métal à fondre (ferreux ou non ferreux) influence le choix du four.
- Efficacité énergétique et impact sur l'environnement : Les fours à induction sont plus efficaces sur le plan énergétique et produisent moins d'émissions, ce qui en fait un choix privilégié pour les entreprises soucieuses de l'environnement.
- Exigences de précision : Les fours à induction offrent un meilleur contrôle de la température, ce qui est crucial pour les applications nécessitant un alliage ou un affinage précis.
En résumé, le choix du four pour la fusion du métal brut dépend des exigences spécifiques de l'opération, notamment de l'échelle, du type de matériau et du débit souhaité.Les fours à arc électrique sont utilisés pour la fusion industrielle des métaux à grande échelle, tandis que les fours à induction sont préférés pour les applications plus petites, précises ou spécialisées.Les deux types de fours jouent un rôle essentiel dans le traitement moderne des métaux, chacun ayant ses avantages et ses limites.
Tableau récapitulatif :
Caractéristiques | Four à arc électrique (EAF) | Four à induction |
---|---|---|
Échelle | Opérations industrielles à grande échelle | Applications à plus petite échelle ou spécialisées |
Efficacité énergétique | Consommation d'énergie élevée | Efficacité énergétique |
Flexibilité des matériaux | Idéal pour l'acier et le fer | Excellent pour les métaux non ferreux |
Coût | Coûts d'infrastructure et de maintenance élevés | Coût initial plus élevé, coûts d'exploitation plus faibles |
Contrôle de la température | Moins précis | Très précis |
Applications | Production d'acier, recyclage de la ferraille | Fonderies, laboratoires, fusion de précision |
Vous avez besoin d'aide pour choisir le four adapté à vos besoins en matière de fusion des métaux ? Contactez nos experts dès aujourd'hui pour des conseils personnalisés !