Les fours à arc électrique sont largement utilisés dans la production d'acier en raison de leur efficacité, de leur flexibilité et de leur capacité à recycler la ferraille. Cependant, ils présentent également plusieurs inconvénients qui peuvent avoir une incidence sur leur fonctionnement, leur coût et la qualité du produit final. Les principaux inconvénients sont une consommation d'énergie élevée, la difficulté de contrôler la composition chimique lorsqu'on utilise 100 % de la ferraille, les risques de contamination, les défis opérationnels et les limites de la production d'alliages. Ces facteurs doivent être soigneusement pris en compte lors de l'évaluation de l'adéquation des fours électriques à des applications sidérurgiques spécifiques.
Explication des points clés :
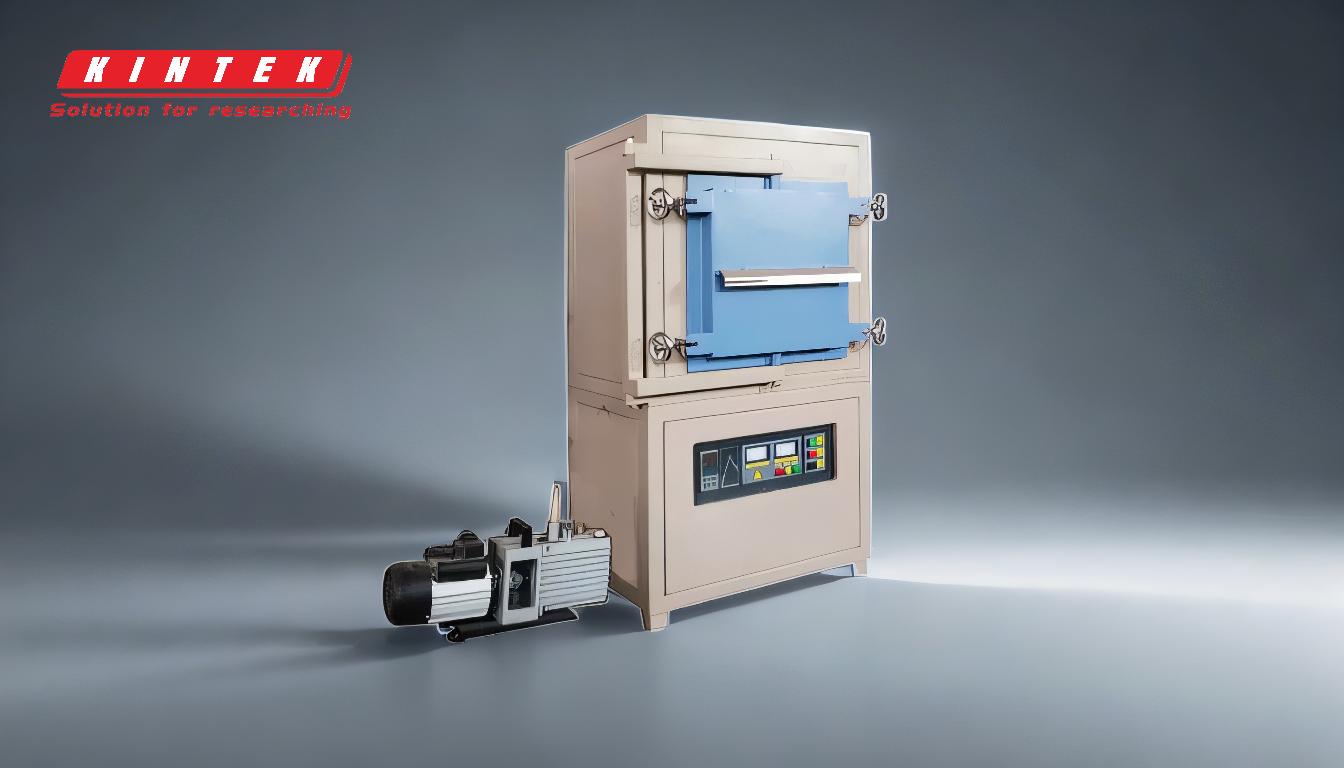
-
Consommation d'énergie élevée
- Le fonctionnement des fours électriques à arc nécessite une quantité importante d'énergie électrique, ce qui peut peser sur les réseaux électriques locaux et augmenter les coûts d'exploitation.
- La dépendance à l'égard de l'électricité rend les FEA vulnérables aux pannes ou aux fluctuations de courant, qui peuvent perturber la production et entraîner des temps d'arrêt.
- Une forte consommation d'énergie contribue également à l'augmentation de l'empreinte carbone si l'électricité est produite à partir de sources non renouvelables.
-
Difficulté à contrôler la composition chimique
- Si les fours électriques à arc offrent une certaine souplesse dans le contrôle de la composition chimique de l'acier, cela devient difficile lorsque l'on utilise 100 % de ferraille.
- La ferraille contient souvent des impuretés ou des éléments d'alliage inconnus, ce qui peut entraîner des incohérences dans le produit final.
- L'obtention d'une composition chimique précise nécessite un contrôle et des ajustements minutieux, ce qui peut accroître la complexité et le coût.
-
Risque de contamination
- Dans les FÉA à électrodes non autoconsommatrices, le métal en fusion peut être contaminé par le matériau de l'électrode, bien que cela soit généralement localisé et rare.
- La contamination peut affecter la qualité et les propriétés de l'acier, le rendant impropre à certaines applications de haute précision.
-
Défis opérationnels
- Les fours à arc non autoconsommateurs sont souvent confrontés à des problèmes de stabilité, ce qui rend leur fonctionnement difficile, en particulier dans des conditions de vide.
- Le processus nécessite la formation d'un bain de fusion avant le dégazage, ce qui augmente la complexité et le temps nécessaire à la production.
- Les temps de prise à prise (le temps entre deux lots successifs) varient généralement de 50 à 80 minutes, en fonction de la puissance du transformateur et de la taille de la cuve, ce qui peut limiter le débit.
-
Limites de la production d'alliages
- Les fours électriques à arc non autoconsommateurs sont généralement limités à la production d'alliages à petite échelle, la taille des lots allant de quelques dizaines à quelques centaines de grammes.
- Il est difficile de contrôler la proportion de la composition de l'alliage et d'obtenir des résultats cohérents.
- Cette limitation rend les fours électriques moins adaptés aux applications nécessitant de grandes quantités d'alliages de haute précision.
-
Considérations économiques et environnementales
- Bien que les FEA soient plus efficaces sur le plan énergétique que les hauts fourneaux, leur consommation élevée d'électricité peut annuler une partie de ces économies, en particulier dans les régions où l'électricité est chère ou peu fiable.
- La dépendance à l'égard de la ferraille, bien que bénéfique pour l'environnement, peut également introduire une variabilité dans la qualité des matières premières, ce qui peut être source d'inefficacité.
En résumé, si les fours électriques à arc présentent des avantages significatifs en termes d'efficacité, de flexibilité et de respect de l'environnement, ils posent également plusieurs problèmes. Il s'agit notamment de la consommation élevée d'énergie, de la difficulté à contrôler la composition chimique, des risques de contamination, de la complexité des opérations et des limites de la production d'alliages. Ces facteurs doivent être soigneusement pesés lorsqu'il s'agit de décider d'utiliser des fours électriques à arc pour des besoins spécifiques en matière de fabrication d'acier.
Tableau récapitulatif :
Inconvénient | Détails clés |
---|---|
Consommation d'énergie élevée | - Les réseaux locaux sont mis à rude épreuve, les coûts augmentent et l'empreinte carbone s'alourdit. |
Contrôle de la composition chimique | - Difficile avec 100 % de déchets ; les impuretés entraînent des incohérences et des coûts plus élevés. |
Risques de contamination | - Le métal en fusion peut être contaminé par le matériau de l'électrode, ce qui nuit à la qualité. |
Défis opérationnels | - Problèmes de stabilité, processus de dégazage complexe et temps d'écoulement plus longs. |
Limites de la production d'alliages | - Limité à la production à petite échelle ; difficulté à obtenir une composition d'alliage cohérente. |
Impact économique et environnemental | - Les coûts élevés de l'électricité et la variabilité de la qualité de la ferraille peuvent annuler les avantages de l'efficacité. |
Vous envisagez d'utiliser des fours à arc électrique pour vos besoins en matière de fabrication d'acier ? Contactez nos experts dès aujourd'hui pour discuter des meilleures solutions pour vos opérations !