La consommation d'électricité d'un four à induction, en particulier pour la fusion de l'acier, est un facteur critique pour l'efficacité opérationnelle et la gestion des coûts.En moyenne, un four à induction consomme environ 625 kWh par tonne d'acier fondu.Ce chiffre peut varier en fonction de facteurs tels que la conception du four, les conditions d'exploitation et le type de technologie d'induction utilisée, par exemple un four à induction à four à induction IGBT .La compréhension de ces variables permet d'optimiser l'utilisation de l'énergie et de réduire les coûts opérationnels.
Explication des points clés :
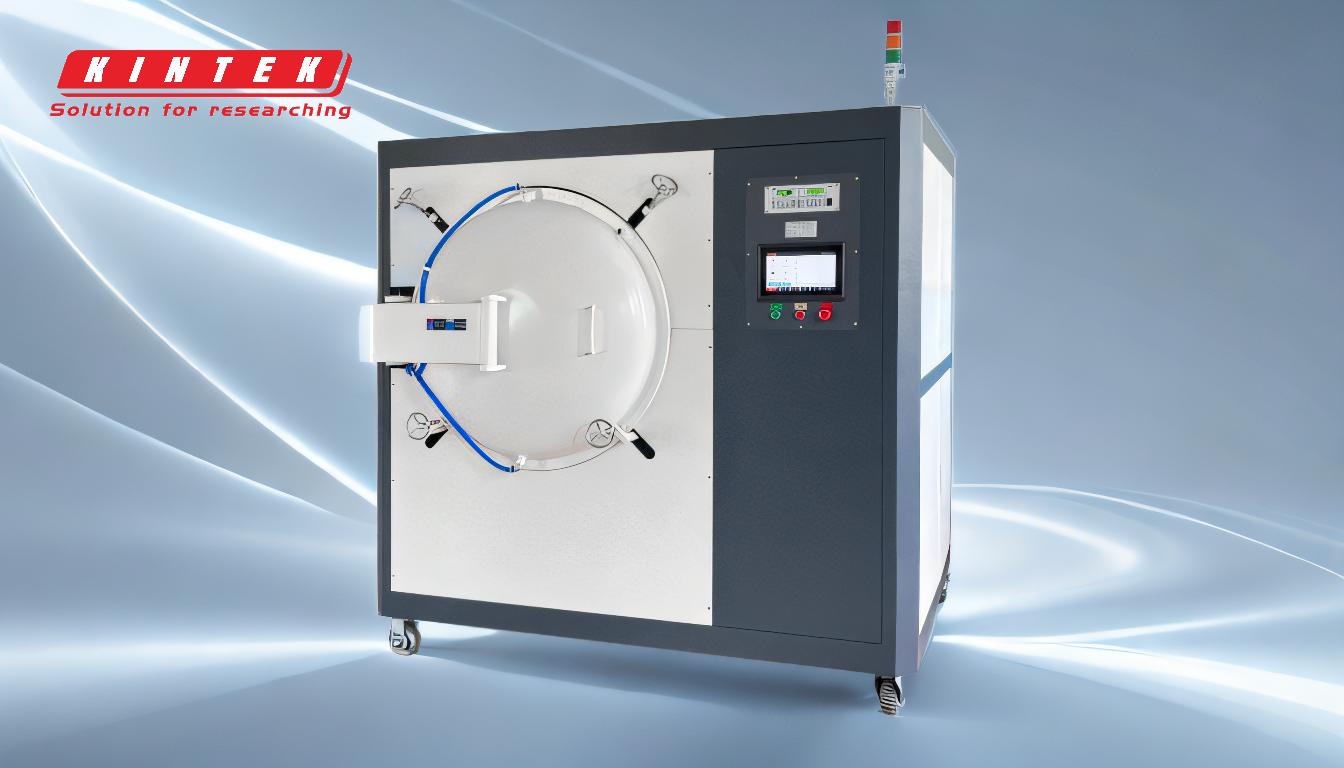
-
Consommation électrique standard:
- La consommation électrique standard d'un four à induction pour l'acier est de 625 kWh/tonne .Il s'agit d'une référence en matière d'efficacité énergétique dans les opérations de fusion de l'acier.
- Ce chiffre est basé sur des fours bien conçus et correctement exploités, garantissant un gaspillage d'énergie minimal.
-
Facteurs influençant la consommation d'électricité:
- Conception du four:L'efficacité de la conception du four, y compris la configuration du serpentin et l'isolation, joue un rôle important dans la consommation d'énergie.
- Conditions de fonctionnement:Des facteurs tels que la vitesse de fusion, la qualité du matériau de charge et le contrôle de la température ont un impact sur la consommation d'énergie.Par exemple, des taux de fusion plus élevés peuvent augmenter la consommation d'énergie.
- Technologie de l'induction:Technologies avancées telles que fours à induction IGBT offrent une plus grande efficacité et un contrôle précis de la puissance, ce qui permet de réduire la consommation d'énergie globale par rapport aux anciens systèmes à base de SCR.
-
Importance de l'efficacité énergétique:
- La réduction de la consommation d'électricité diminue directement les coûts d'exploitation et améliore la durabilité du processus de fusion.
- Les fours à haut rendement énergétique contribuent également à réduire les émissions de gaz à effet de serre, conformément aux réglementations environnementales.
-
Stratégies d'optimisation:
- Entretien régulier:Un bon entretien du four permet de réduire les pertes d'énergie dues à l'usure.
- Préparation correcte de la charge:L'utilisation de matériaux de charge propres et de taille appropriée réduit le temps de fusion et la consommation d'énergie.
- Systèmes de contrôle avancés:Mise en œuvre de systèmes de contrôle modernes dans les fours à induction IGBT permet une gestion précise de l'énergie, ce qui améliore encore l'efficacité.
-
Comparaison avec d'autres types de fours:
- Les fours à induction consomment généralement moins d'énergie que les fours à arc traditionnels, en particulier pour les opérations à petite échelle.
- L'utilisation de fours à induction fours à induction IGBT améliorent encore cet avantage grâce à leur efficacité supérieure et à leur capacité de chauffage plus rapide.
En se concentrant sur ces points clés, les opérateurs peuvent mieux comprendre et gérer la consommation d'électricité des fours à induction, garantissant ainsi des opérations rentables et durables.
Tableau récapitulatif :
Aspect clé | Détails |
---|---|
Consommation standard | 625 kWh/tonne d'acier fondu (référence en matière d'efficacité énergétique) |
Facteurs influençant l'utilisation |
- Conception du four (serpentin, isolation)
- Conditions de fonctionnement (taux de fusion, qualité de la charge) - Technologie d'induction (par exemple, IGBT) |
Stratégies d'optimisation |
- Entretien régulier
- Préparation correcte de la charge - Systèmes de contrôle avancés |
Comparaison avec les fours à arc | Réduction de la consommation d'énergie, en particulier avec les fours à induction IGBT |
Découvrez comment optimiser l'efficacité énergétique de votre four à induction. contactez nos experts dès aujourd'hui !