Les fours de fusion à induction sont largement utilisés dans la métallurgie pour leur efficacité, leur précision et leur polyvalence.La fréquence d'un four de fusion à induction joue un rôle essentiel dans la détermination de ses performances, de sa profondeur de chauffe et de l'adéquation de son application.Les fréquences élevées permettent d'obtenir des couches de chauffe plus fines et un contrôle précis du processus de chauffe, ce qui les rend idéales pour les applications nécessitant une régulation fine de la température.À l'inverse, les fréquences plus basses conviennent mieux à une pénétration plus profonde et à des opérations à plus grande échelle.Le choix de la fréquence dépend des exigences spécifiques du processus de fusion, telles que le type de matériau, la profondeur de chauffe souhaitée et l'échelle de production.
Explication des points clés :
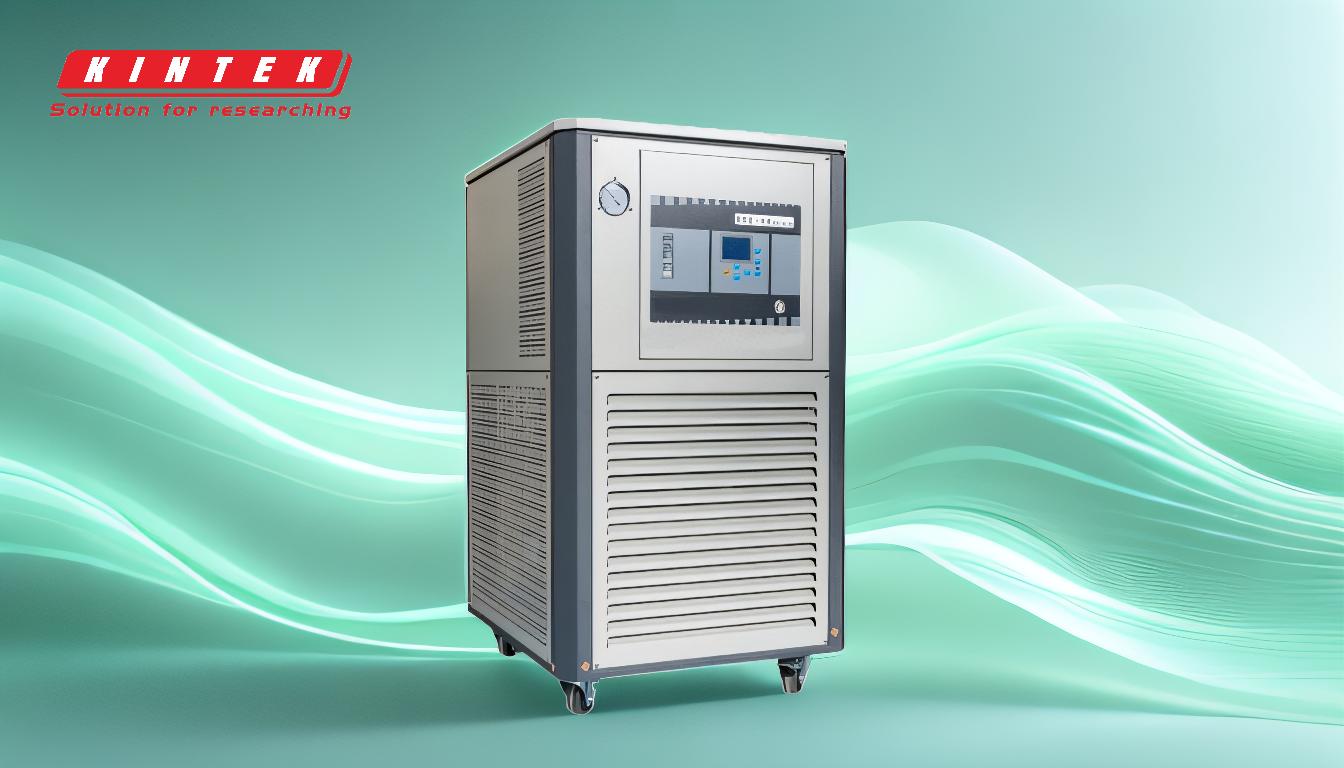
-
Fréquence et profondeur de chauffe:
- La fréquence d'un four de fusion à induction affecte directement la profondeur de chauffage du matériau.Des fréquences plus élevées permettent d'obtenir une couche chauffante plus fine, ce qui est idéal pour les processus nécessitant un contrôle précis de la température, tels que le durcissement de la surface ou la fusion à petite échelle.Les fréquences plus basses, en revanche, permettent une pénétration plus profonde, ce qui les rend adaptées aux pièces plus grandes ou aux applications de fusion en vrac.
-
Puissance et efficacité:
- Des fréquences de fonctionnement plus élevées permettent d'appliquer une plus grande puissance dans des fours plus petits, ce qui améliore l'efficacité et réduit la consommation d'énergie.Ceci est particulièrement bénéfique pour les applications de haute précision qui nécessitent un chauffage uniforme et une fusion rapide.
-
Effet d'agitation magnétique:
- Le champ magnétique à moyenne fréquence des fours à induction crée un effet de brassage magnétique qui améliore l'uniformité de la composition du métal en fusion et facilite l'élimination de l'écume.Cette caractéristique est cruciale pour la production de métaux de haute qualité aux propriétés constantes.
-
Applications basées sur la fréquence:
-
Les fours de fusion à induction sont utilisés dans une variété d'applications, y compris :
- Fours à haute fréquence:Idéal pour un chauffage précis, tel que le chauffage de rotors de moteurs, la diathermie de moules et la fusion de métaux à petite échelle.
- Fours à moyenne fréquence:Convient aux opérations à grande échelle telles que le forgeage, le chauffage de tubes d'acier et la fusion de métaux en vrac.
- Fours à induction sous vide:Utilisé pour la fusion de métaux précieux et réactifs tels que les alliages de titane, où un environnement sous vide empêche les réactions chimiques et garantit une grande pureté.
-
Les fours de fusion à induction sont utilisés dans une variété d'applications, y compris :
-
Avantages opérationnels:
-
Les fours de fusion à induction offrent de nombreux avantages opérationnels, notamment
- Fusion rapide:Les hautes fréquences permettent une augmentation rapide de la température, réduisant ainsi le temps de fusion.
- Efficacité énergétique:Moins de pertes de chaleur et moins d'impact sur l'environnement par rapport aux fours traditionnels.
- L'automatisation:Facile à automatiser, réduisant les coûts de main-d'œuvre et améliorant la cohérence.
- La flexibilité:Permet de changer facilement les corps des fours pour répondre aux différentes exigences de fusion.
-
Les fours de fusion à induction offrent de nombreux avantages opérationnels, notamment
-
Caractéristiques techniques:
-
Les fours à induction modernes sont dotés de caractéristiques avancées, telles que
- Conversion de fréquence IGBT:Assure une régulation précise de la puissance et une protection complète contre les surintensités, les surchauffes et autres défauts.
- Fonctions d'affichage:Les systèmes de surveillance en temps réel du courant, de la tension et de la durée permettent d'optimiser les processus.
- Conception compacte:Le volume ultra réduit et la construction légère rendent le four portable et peu encombrant.
-
Les fours à induction modernes sont dotés de caractéristiques avancées, telles que
-
Avantages environnementaux et économiques:
- Les fours de fusion à induction sont respectueux de l'environnement, car ils produisent moins de pollution et consomment moins d'énergie que les méthodes traditionnelles.Leur rentabilité et leur capacité à produire des métaux de haute qualité en font un choix privilégié dans la métallurgie moderne.
En conclusion, la fréquence d'un four de fusion par induction est un facteur essentiel qui détermine sa profondeur de chauffe, son efficacité et son adéquation à des applications spécifiques.En comprenant la relation entre la fréquence et les performances, les utilisateurs peuvent sélectionner le four adapté à leurs besoins, garantissant ainsi des résultats optimaux en termes de qualité, de rapidité et de rentabilité.
Tableau récapitulatif :
Aspect | Fréquence élevée | Fréquence moyenne | Basse fréquence |
---|---|---|---|
Profondeur de chauffe | Couche mince, contrôle précis | Profondeur modérée | Pénétration profonde |
Applications | Fusion à petite échelle, durcissement de surface | Forgeage, chauffage de tubes d'acier | Fusion en vrac, pièces de grande taille |
Puissance et efficacité | Puissance élevée dans les petits fours, économie d'énergie | Puissance et efficacité équilibrées | Convient aux opérations à grande échelle |
Agitation magnétique | Limité | Améliore l'uniformité, facilite l'élimination de l'écume | Limité |
Avantages opérationnels | Fusion rapide, automatisation, flexibilité | Rentabilité, résultats constants | Idéal pour les processus à grande échelle et en grande quantité |
Vous êtes prêt à choisir le four de fusion par induction adapté à vos besoins ? Contactez nos experts dès aujourd'hui pour un accompagnement personnalisé !