Les fours réfractaires sont construits à l'aide d'une variété de matériaux conçus pour résister à des températures extrêmes et fournir une isolation thermique.Le choix des matériaux dépend de l'application spécifique, des exigences du processus et des caractéristiques de performance souhaitées.Les matériaux courants comprennent les briques réfractaires, les fibres céramiques, les matériaux à base d'alumine, le carbure de silicium (SiC) et les matériaux moulés spécialisés.Ces matériaux sont souvent disposés en plusieurs couches afin d'optimiser l'isolation, de réduire les pertes de chaleur et de garantir la durabilité.Par exemple, des fibres céramiques d'alumine légères, des panneaux isolants de haute qualité et des barres chauffantes en SiC sont fréquemment utilisés dans les fours modernes.La sélection des matériaux réfractaires est adaptée aux conditions de fonctionnement du four, telles que les plages de température et les environnements chimiques, afin de garantir l'efficacité et la longévité.
Explication des points clés :
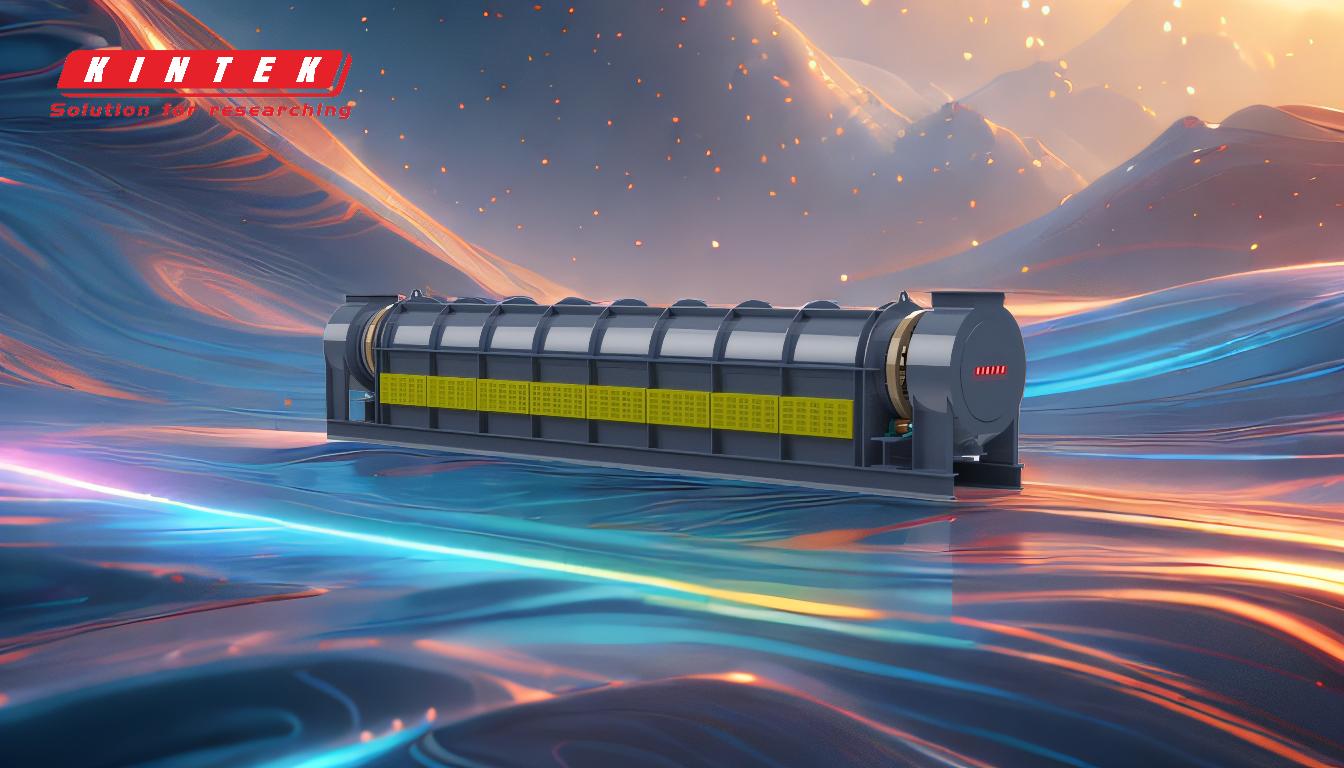
-
Briques réfractaires et fibres céramiques
- Les briques réfractaires sont l'un des matériaux réfractaires les plus couramment utilisés dans les fours en raison de leur capacité à conserver leur résistance à des températures élevées (supérieures à 1000°F).Elles sont souvent fabriquées à partir de matériaux tels que l'alumine ou la magnésite, en fonction de l'application du four.
- Les fibres céramiques, telles que les fibres à base d'alumine, sont légères et offrent une excellente isolation thermique.Elles sont souvent utilisées dans des conceptions multicouches pour réduire les pertes de chaleur et améliorer l'efficacité énergétique.
-
Matériaux à base d'alumine
- Les fibres d'alumine de haute pureté et les fibres céramiques d'alumine sont largement utilisées dans les revêtements de four en raison de leur température de service élevée, de leur résistance rapide à la chaleur et au froid et de leurs excellentes propriétés d'isolation thermique.
- Des plaques d'alumine légères ou des plaques creuses d'oxyde d'aluminium sont également utilisées pour minimiser la capacité de stockage de la chaleur et améliorer l'efficacité thermique.
-
Carbure de silicium (SiC)
- Le SiC est un matériau très résistant utilisé dans les éléments chauffants (par exemple, les barres chauffantes en SiC) et les revêtements réfractaires.Il offre une excellente conductivité thermique, une résistance aux chocs thermiques et une durabilité dans les environnements à haute température.
- Le SiC est souvent utilisé dans les fours à moufle et autres fours spécialisés où un chauffage uniforme et un contrôle précis de la température sont nécessaires.
-
Isolation multicouche
- Les fours modernes utilisent souvent une combinaison de matériaux dans une conception d'isolation multicouche.Par exemple, des fibres céramiques légères sont associées à des panneaux isolants de haute qualité pour créer un revêtement robuste et économe en énergie.
- Cette conception garantit une faible perte de chaleur, une réduction de la consommation d'énergie et une amélioration des performances.
-
Matériaux moulés réfractaires spécialisés
- Les fours rotatifs et autres fours à haute performance peuvent utiliser des bétons réfractaires, qui sont des mélanges de matériaux réfractaires combinés à des liants.Ces bétons sont appliqués comme revêtements pour fournir une isolation thermique supérieure, réduire la température de la peau du four et améliorer la durabilité.
-
Sélection des matériaux en fonction de l'application
-
Le choix des matériaux réfractaires dépend fortement de l'application spécifique du four et des conditions d'exploitation.Par exemple :
- Les briques d'alumine à faible teneur en fer ou de magnésium-spinel sont utilisées dans les fours de réduction du minerai de fer.
- Les briques de magnésite sont préférées dans les fours à ciment en raison de leur résistance aux températures élevées et à la corrosion chimique.
- L'épaisseur, les propriétés physiques et la composition chimique des matériaux réfractaires sont adaptées aux exigences du processus.
-
Le choix des matériaux réfractaires dépend fortement de l'application spécifique du four et des conditions d'exploitation.Par exemple :
-
Composants sans amiante
- Les matériaux réfractaires modernes sont conçus pour être exempts d'amiante, ce qui garantit la sécurité et le respect des réglementations environnementales.Des matériaux tels que les fibres céramiques d'alumine et les panneaux d'isolation sont utilisés comme alternatives.
-
Composants structurels
- Alors que les matériaux réfractaires constituent le revêtement, les composants structurels du four (par exemple, la coque extérieure) sont généralement fabriqués en acier au carbone pour les fours à combustion directe ou en alliages résistants à la chaleur pour les fours à combustion indirecte.Ces matériaux assurent l'intégrité structurelle et le soutien du revêtement réfractaire.
En sélectionnant et en combinant soigneusement ces matériaux, les fours réfractaires atteignent des performances, une efficacité énergétique et une durabilité optimales, adaptées aux besoins spécifiques de l'application.
Tableau récapitulatif :
Matériel | Propriétés principales | Applications courantes |
---|---|---|
Briques réfractaires | Haute résistance à >1000°F, à base d'alumine ou de magnésite | Revêtements généraux de fours, environnements à haute température |
Fibres céramiques | Légèreté, excellente isolation thermique, efficacité énergétique | Conceptions d'isolation multicouches, réduisant les pertes de chaleur |
À base d'alumine | Température de service élevée, résistance rapide à la chaleur et au froid, isolation supérieure | Revêtements de four, plaques légères pour l'efficacité thermique |
Carbure de silicium (SiC) | Conductivité thermique élevée, résistance aux chocs thermiques, durabilité | Éléments chauffants, fours à moufle, fours spécialisés |
Matériaux moulés réfractaires | Isolation supérieure, réduction de la température de peau du four, durabilité accrue | Fours rotatifs, fours à haute performance |
Sans amiante | Sans amiante, sûr, conforme aux réglementations environnementales | Revêtements de four modernes, panneaux d'isolation |
Composants structurels | Acier au carbone ou alliages résistants à la chaleur pour l'intégrité structurelle | Enveloppe extérieure des fours à combustion directe/indirecte |
Vous avez besoin d'aide pour sélectionner les matériaux réfractaires adaptés à votre four ? Contactez nos experts dès aujourd'hui pour des solutions sur mesure !