La porosité dans la métallurgie des poudres est un facteur critique qui affecte les propriétés mécaniques et les performances du produit final.Il est possible de réduire la porosité en optimisant plusieurs paramètres clés au cours du processus de fabrication.Il s'agit notamment d'augmenter la pression de compactage, la température de frittage et le temps de frittage, ce qui permet de réduire la porosité apparente et d'augmenter la densité apparente.En outre, le contrôle de la taille des particules est crucial, car les particules plus grosses ont tendance à augmenter la porosité.En gérant soigneusement ces facteurs, les fabricants peuvent produire des composants de haute densité, à faible porosité et aux propriétés mécaniques améliorées.
Explication des points clés :
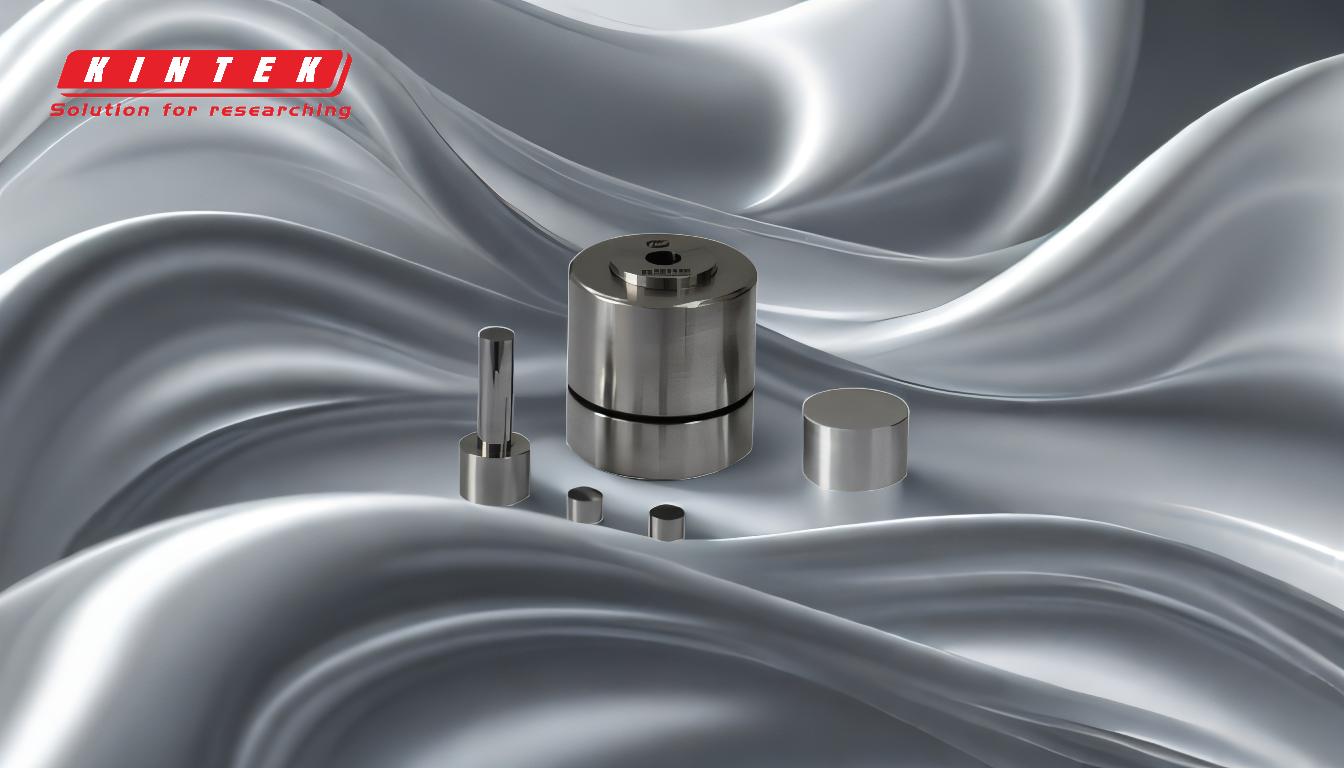
-
Augmenter la pression de compactage:
- Impact:Une pression de compactage plus élevée réduit les espaces entre les particules de poudre, ce qui permet d'obtenir un produit compact plus dense et moins poreux.
- Mécanisme:Lorsque la pression est appliquée pendant la phase de compactage, les particules sont rapprochées les unes des autres, ce qui minimise les vides et augmente la densité apparente du compact vert.
- Considérations pratiques:Si une pression plus élevée est bénéfique, elle doit être mise en balance avec le risque d'endommager la matrice ou de provoquer une répartition inégale de la densité dans la pièce.
-
Optimisation de la température et de la durée du frittage:
- Impact:Des températures de frittage plus élevées et des temps de frittage plus longs favorisent une meilleure liaison et diffusion des particules, réduisant la porosité et augmentant la densité.
- Mécanisme:Le frittage consiste à chauffer la poudre compactée en dessous de son point de fusion, ce qui permet aux atomes de se diffuser à travers les limites des particules, ce qui ferme les pores et renforce le matériau.
- Considérations pratiques:Une température ou une durée excessive peut entraîner la croissance ou la distorsion des grains, d'où la nécessité d'une optimisation minutieuse.
-
Contrôle de la taille des particules:
- Impact:Les particules de plus petite taille ont généralement une porosité plus faible car elles se tassent plus efficacement, laissant moins de vides.
- Mécanisme:Les particules fines ont un rapport surface/volume plus élevé, ce qui améliore le frittage et la liaison.Les particules plus grosses, en revanche, créent plus d'espaces et augmentent la porosité.
- Considérations pratiques:Si les particules plus petites sont préférables, elles peuvent aussi augmenter le risque d'agglomération, qui doit être géré pendant le traitement.
-
Méthodes de production des poudres:
- Impact:La méthode utilisée pour produire des poudres métalliques influe sur leur taille, leur forme et leur distribution, ce qui a une incidence sur la porosité.
- Mécanisme:Les techniques telles que l'atomisation produisent des poudres de taille contrôlée, qui peuvent être adaptées pour minimiser la porosité.Le concassage et le broyage peuvent produire des particules de forme irrégulière qui se tassent moins efficacement.
- Considérations pratiques:Le choix de la méthode de production de poudre appropriée est essentiel pour obtenir les caractéristiques souhaitées des particules et minimiser la porosité.
-
Sélection des matériaux:
- Impact:Le choix du matériau de base (par exemple, base de cuivre ou base de fer) peut influencer la porosité en raison des différences de forme et de taille des particules et de leur comportement lors du frittage.
- Mécanisme:Certains matériaux se frittent plus facilement que d'autres, ce qui permet une meilleure densification et une moindre porosité.
- Considérations pratiques:Le choix du matériau doit correspondre à l'application prévue et aux propriétés mécaniques souhaitées.
En tenant compte de ces facteurs clés, les fabricants peuvent réduire efficacement la porosité dans la métallurgie des poudres, ce qui permet d'obtenir des composants plus résistants, plus durables et plus performants.
Tableau récapitulatif :
Facteur clé | Impact | Mécanisme | Considérations pratiques |
---|---|---|---|
Augmentation de la pression de compactage | Réduit les écarts entre les particules, ce qui permet d'obtenir des compacts plus denses et moins poreux. | La pression rapproche les particules, minimise les vides et augmente la densité en vrac. | Équilibrer la pression pour éviter d'endommager la matrice ou d'obtenir une répartition inégale de la densité. |
Optimiser la température et la durée du frittage | Favorise la liaison des particules, réduit la porosité et améliore la densité. | Le chauffage en dessous du point de fusion permet la diffusion des atomes, la fermeture des pores et le renforcement du matériau. | Évitez les températures et les durées excessives afin d'empêcher la croissance du grain ou la distorsion. |
Contrôle de la taille des particules | Les petites particules se tassent efficacement, ce qui réduit la porosité. | Les particules fines ont un rapport surface/volume plus élevé, ce qui améliore le frittage et l'adhérence. | Gérer les risques d'agglomération avec des particules plus petites. |
Méthodes de production des poudres | Influence la taille, la forme et la distribution des particules, ainsi que la porosité. | L'atomisation produit des gammes de tailles contrôlées ; l'écrasement/le broyage peut créer des particules irrégulières. | Choisir la bonne méthode pour obtenir les caractéristiques souhaitées des particules. |
Sélection des matériaux | Le matériau de base influe sur la porosité en raison de différences dans le comportement de frittage. | Certains matériaux se frittent plus facilement, ce qui entraîne une meilleure densification et une porosité plus faible. | Alignez le choix du matériau sur l'application et les propriétés mécaniques souhaitées. |
Prêt à optimiser votre processus de métallurgie des poudres ? Contactez nos experts dès aujourd'hui pour des solutions sur mesure !