Les fours continus, bien qu'efficaces pour la production à grande échelle, présentent plusieurs inconvénients qui peuvent nuire à leur adéquation à certaines applications.Ils sont plus complexes et plus coûteux que les fours discontinus et nécessitent une maintenance fréquente et des connaissances spécialisées.Leur fonctionnement à température constante limite la flexibilité, ce qui les rend inadaptés aux processus nécessitant des températures et des durées variées.En outre, ils s'adaptent moins bien aux petits lots ou aux géométries complexes, consomment plus d'énergie en fonctionnement continu et ne sont pas toujours idéaux pour fondre de grandes quantités de métal.Ces facteurs rendent les fours continus moins polyvalents et plus gourmands en ressources que les autres types de fours.
Explication des points clés :
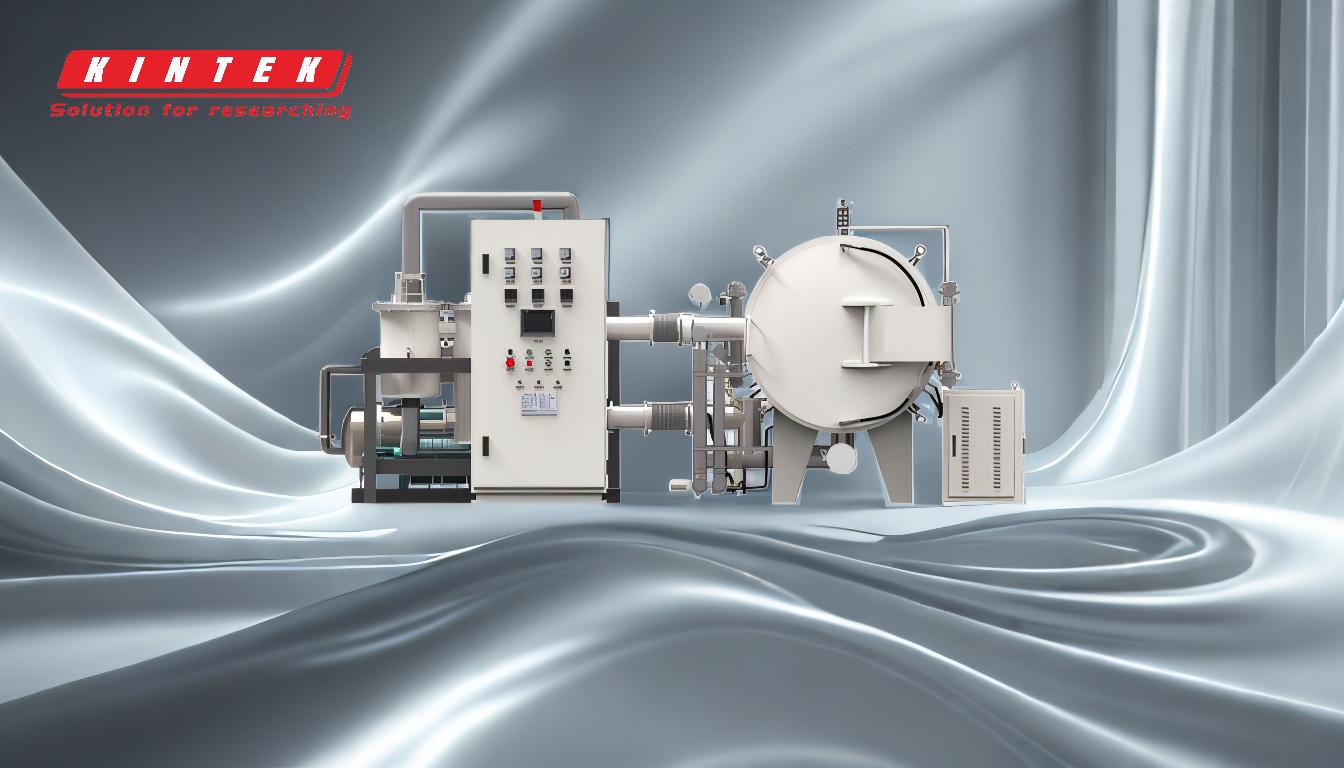
-
Complexité et coût accrus:
- Les fours continus sont plus complexes dans leur conception et leur fonctionnement que les fours discontinus.Cette complexité se traduit par des coûts initiaux et des dépenses permanentes plus élevés.
- Les mécanismes complexes requis pour un fonctionnement continu, tels que les systèmes de convoyage et les contrôles de température, contribuent à l'augmentation des coûts.
-
Besoins de maintenance fréquents:
- En raison de leur fonctionnement continu, ces fours subissent une usure plus importante, ce qui nécessite une maintenance plus fréquente.
- La nécessité de disposer de connaissances et de ressources spécialisées pour l'entretien augmente les coûts d'exploitation et peut entraîner des temps d'arrêt si elle n'est pas correctement gérée.
-
Flexibilité limitée de la température:
- Les fours continus fonctionnent à une température constante, qui ne peut pas être facilement ajustée.Cette rigidité signifie que tous les éléments traités doivent être chauffés à la même température.
- Cette limitation peut constituer un inconvénient important pour les processus qui nécessitent une gamme de températures ou des durées de traitement thermique variables.
-
Manque de flexibilité pour les petits lots et les géométries complexes:
- Les fours continus sont conçus pour une production uniforme à grande échelle et s'adaptent moins bien aux petits lots ou aux articles de forme complexe.
- La nécessité d'une vitesse et d'une température constantes rend difficile l'adaptation aux variations de taille ou de géométrie des produits.
-
Consommation d'énergie plus élevée:
- Le fonctionnement continu de ces fours entraîne une plus grande consommation d'énergie, en particulier pendant les périodes de faible production ou lorsqu'ils tournent au ralenti.
- Cette consommation accrue d'énergie peut se traduire par des coûts d'exploitation plus élevés et une empreinte environnementale plus importante.
-
Inadaptation à la fusion de métaux à grande échelle:
- Les fours continus, en particulier les fours à résistance, mettent plus de temps à atteindre les températures nécessaires à la fusion des métaux.
- Ils sont souvent inadaptés à la fusion de grandes quantités de métal, ce qui les rend moins efficaces pour certaines applications minières ou industrielles à grande échelle.
-
Connaissances et ressources spécialisées:
- Le fonctionnement et l'entretien des fours continus nécessitent des connaissances et des ressources spécialisées, ce qui peut constituer un obstacle pour les petites entreprises ou celles qui n'ont pas accès à du personnel spécialisé.
- Cette exigence peut entraîner une augmentation des coûts de formation et le recours à des experts externes pour le dépannage et les réparations.
En résumé, si les fours continus offrent des avantages en termes d'efficacité et de débit pour la production à grande échelle, leurs inconvénients en termes de coût, de maintenance, de flexibilité et de consommation d'énergie les rendent moins adaptés à certaines applications.Il est essentiel de comprendre ces limites pour prendre des décisions éclairées lors de la sélection d'un type de four pour des procédés industriels spécifiques.
Tableau récapitulatif :
Inconvénient | Description |
---|---|
Complexité et coût plus élevés | Conception et fonctionnement plus complexes, entraînant des coûts initiaux et permanents plus élevés. |
Maintenance fréquente | Le fonctionnement en continu nécessite davantage de maintenance, ce qui augmente les temps d'arrêt. |
Flexibilité limitée de la température | Fonctionne à une température constante, inadaptée à des besoins de traitement thermique variés. |
Manque de flexibilité pour les petits lots | Moins adaptable aux petits lots ou aux géométries complexes. |
Consommation d'énergie plus élevée | Le fonctionnement en continu entraîne une augmentation de la consommation d'énergie et des coûts d'exploitation. |
Inadapté à la fusion des métaux | N'est pas idéal pour fondre de grandes quantités de métal, en particulier dans les types de résistance. |
Connaissances spécialisées requises | L'utilisation et l'entretien de l'appareil nécessitent l'intervention d'un personnel spécialisé, ce qui augmente les coûts de formation. |
Vous avez besoin d'aide pour choisir le four le mieux adapté à vos besoins ? Contactez nos experts dès aujourd'hui pour des solutions sur mesure !