Les fours rotatifs, bien que polyvalents et efficaces pour divers procédés industriels, présentent plusieurs inconvénients qui peuvent avoir une incidence sur leur efficacité, leur sécurité et leur rentabilité globale.Les principaux problèmes sont les suivants : coûts d'investissement et d'exploitation élevés, faible efficacité de la conversion thermique, mauvais contrôle de la température, risques pour la sécurité, préoccupations environnementales et difficultés liées à la maintenance et à la manipulation des matériaux.Ces inconvénients peuvent entraîner une baisse de la qualité des produits, une complexité opérationnelle accrue et une plus grande attention de la part des autorités réglementaires.
Explication des principaux points :
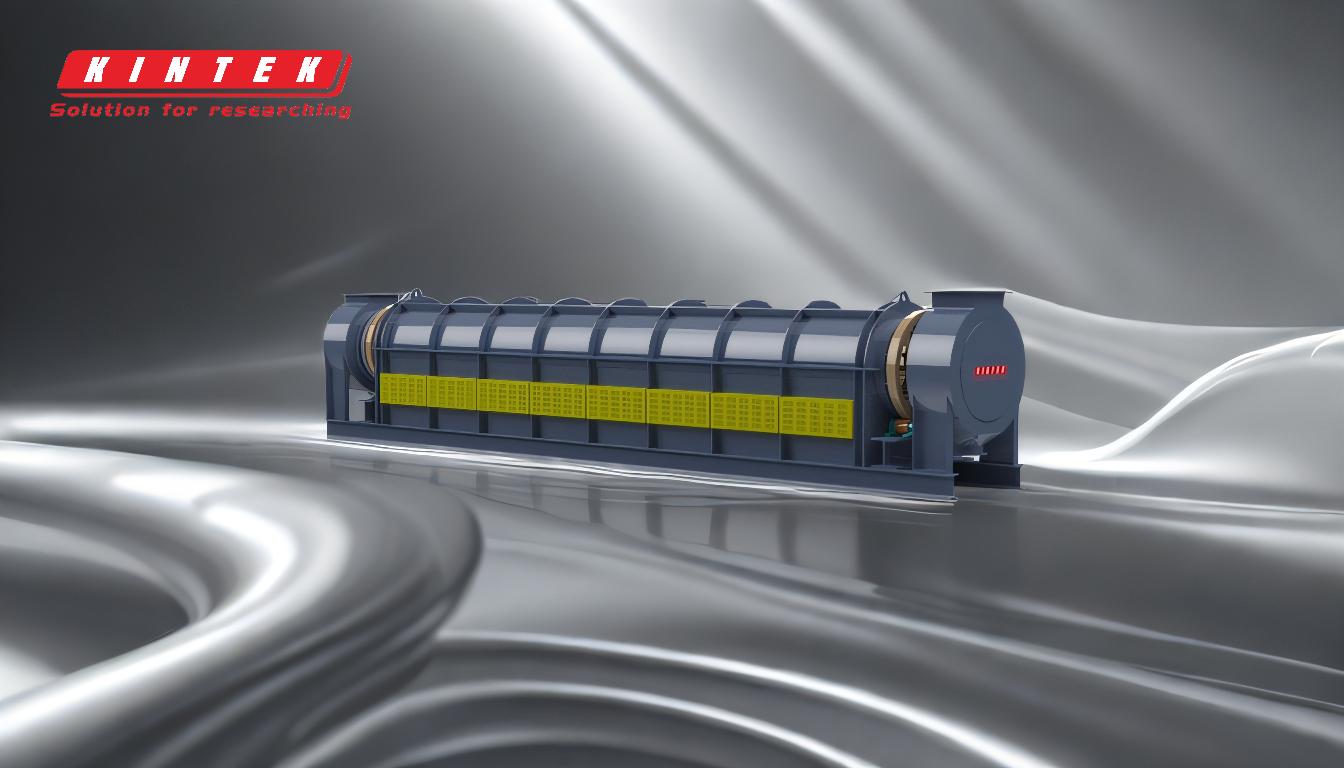
-
Des coûts d'investissement et d'exploitation élevés:
- Coûts en capital:Les fours rotatifs nécessitent un investissement initial important en raison de leur conception complexe et de la nécessité d'utiliser des matériaux de haute qualité pour résister aux températures extrêmes et aux contraintes mécaniques.
- Coûts d'exploitation:Les coûts d'exploitation d'un four rotatif sont également élevés, notamment la consommation d'énergie, l'entretien et la nécessité de disposer d'un personnel qualifié pour faire fonctionner et entretenir l'équipement.
-
Faible efficacité de conversion de la chaleur:
- Questions d'efficacité:Les fours rotatifs traditionnels ont une efficacité de conversion de la chaleur de seulement 30 à 70 %, ce qui signifie qu'une part importante de l'énergie utilisée est gaspillée.
- Impact sur les opérations:Cette inefficacité entraîne une augmentation de la consommation de carburant et des coûts d'exploitation, ce qui rend le processus moins économique.
-
Mauvais contrôle de la température:
- Défis en matière de contrôle:Il est difficile de maintenir un contrôle précis de la température dans un four rotatif, ce qui peut entraîner une qualité irrégulière du produit.
- Rendement du produit:Un mauvais contrôle de la température peut entraîner un faible rendement du produit et des variations de couleur, ce qui affecte la qualité globale et la qualité marchande du produit final.
-
Risques pour la sécurité:
- Risques liés à l'électricité et au gaz:Les fours rotatifs présentent des risques importants pour la sécurité, notamment des fuites électriques, des chocs électriques et des incendies dus à des fuites de gaz.
- Sécurité opérationnelle:Ces risques nécessitent des mesures de sécurité strictes et des inspections régulières pour éviter les accidents, ce qui accroît la complexité et le coût des opérations.
-
Préoccupations environnementales:
- Pollution:Les fours rotatifs peuvent être à l'origine d'une importante pollution de l'environnement, notamment par les poussières et les effluents gazeux qui doivent être traités.
- Conformité réglementaire:En raison de leur impact sur l'environnement, les fours rotatifs sont soumis à des réglementations strictes en matière d'environnement et de sécurité, ce qui peut entraîner une augmentation des coûts de mise en conformité et des difficultés d'exploitation.
-
Questions relatives à l'entretien et à la durée de vie:
- Intensité de l'entretien:Les fours rotatifs nécessitent une maintenance fréquente et intensive en raison des conditions de fonctionnement difficiles, ce qui entraîne une forte intensité de main-d'œuvre et des procédures de maintenance difficiles.
- Durée de vie:La durée de vie des fours rotatifs peut être relativement courte, ce qui nécessite des remplacements fréquents ou des révisions majeures, qui peuvent être coûteux et perturbateurs.
-
Défis en matière de manutention:
- Questions relatives à la culbute:Tous les matériaux ne sont pas bien brassés dans un four rotatif, ce qui entraîne un mauvais mélange et de grandes variations de température.
- Réduction de l'efficacité:Ces problèmes de manutention peuvent réduire l'efficacité globale du four et affecter la qualité et l'homogénéité du produit final.
-
Problèmes d'installation et d'alignement:
- Erreurs d'installation:Une mauvaise installation peut endommager des composants essentiels tels que les roues, les pneus et l'enveloppe du tambour.
- Garantie et remise en état:Les erreurs d'installation peuvent entraîner des travaux de reprise ou l'annulation de garanties, ce qui augmente le coût global et la complexité de l'exploitation d'un four rotatif.
En résumé, si les fours rotatifs présentent plusieurs avantages, leurs inconvénients - coûts élevés, inefficacité, problèmes de sécurité et d'environnement - en font un choix difficile pour certaines applications.Les utilisateurs potentiels doivent soigneusement peser ces inconvénients par rapport aux avantages afin de déterminer si un four rotatif est la bonne solution pour leurs besoins.
Tableau récapitulatif :
Désavantages | Questions clés |
---|---|
Coûts d'investissement et d'exploitation élevés | Investissement initial important et coûts permanents de l'énergie, de la maintenance et de la main-d'œuvre |
Faible efficacité de la conversion de la chaleur | 30%-70% d'efficacité, entraînant un gaspillage d'énergie et des coûts d'exploitation plus élevés |
Mauvais contrôle de la température | Qualité irrégulière du produit, faible rendement et variations de couleur |
Risques pour la sécurité | Fuites électriques, chocs électriques et incendies dus à des fuites de gaz |
Préoccupations environnementales | Pollution par les poussières et les effluents gazeux, respect strict de la réglementation |
Problèmes de maintenance et de durée de vie | Maintenance fréquente et intensive et durée de vie courte |
Défis liés à la manutention des matériaux | Mauvais mélange, variations de température et efficacité réduite |
Problèmes d'installation et d'alignement | Endommagement des composants, reprise des travaux et annulation des garanties |
Vous avez besoin d'aide pour déterminer si un four rotatif convient à votre application ? Contactez nos experts dès aujourd'hui pour des conseils et des solutions sur mesure !