Un four de calcination est un four industriel spécialisé conçu pour le processus de calcination, qui consiste à chauffer des matériaux à des températures élevées pour chasser l'humidité, éliminer les composants volatils ou induire des changements chimiques tels que l'oxydation.Ce processus est essentiel dans des industries telles que la production de ciment, où le carbonate de calcium est décomposé en oxyde de calcium et en dioxyde de carbone.Les fours de calcination sont dotés de caractéristiques telles que l'uniformité des températures élevées, des commandes programmables et des conceptions à haut rendement énergétique pour garantir un fonctionnement précis et efficace.Ils sont largement utilisés dans des applications allant de la fabrication du ciment à la purification des matériaux et au traitement chimique.
Explication des points clés :
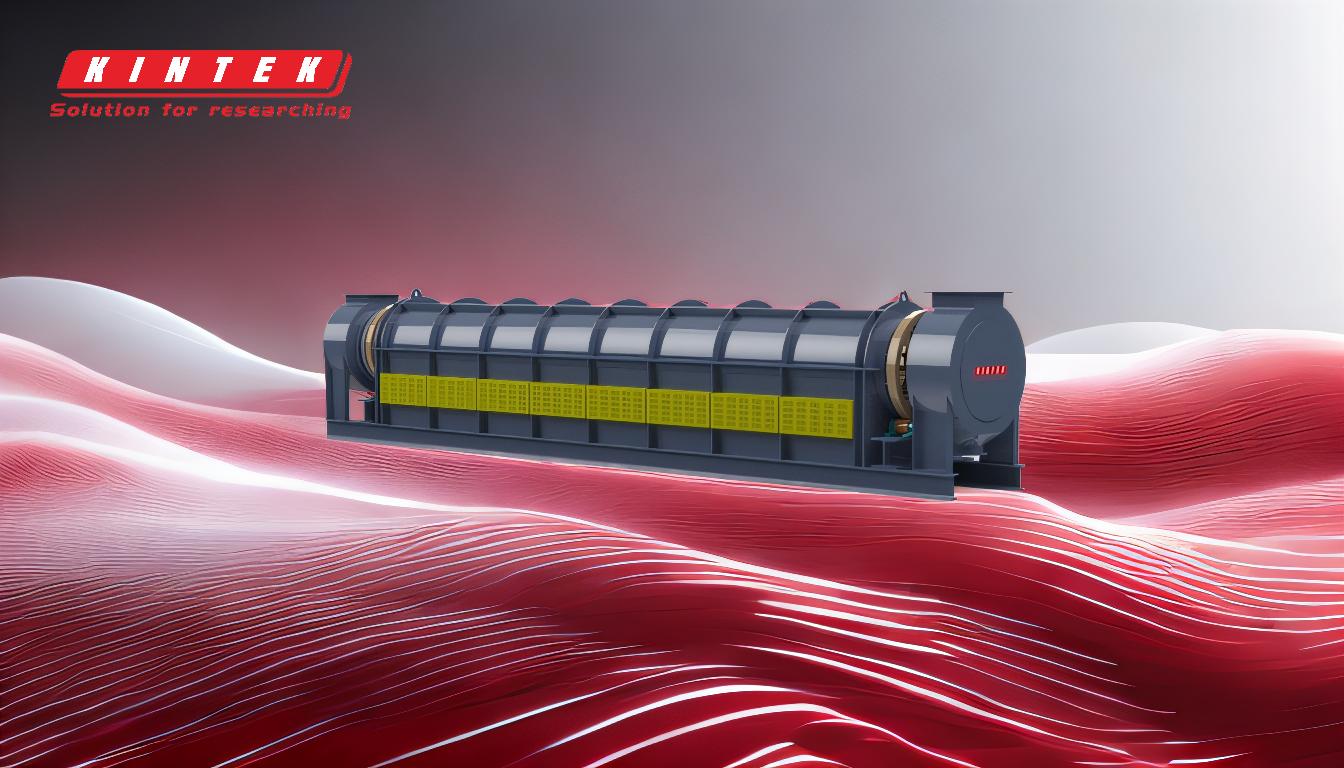
-
Définition et objectif d'un four de calcination:
- Un four de calcination est un four industriel utilisé pour le processus de calcination, qui consiste à chauffer des matériaux à des températures élevées pour obtenir des transformations chimiques ou physiques spécifiques.
-
Les principaux objectifs de la calcination sont les suivants
- Chasser l'humidité absorbée (déshydratation).
- Éliminer les composants volatils tels que le dioxyde de carbone ou le dioxyde de soufre.
- Oxydation d'une partie ou de la totalité du matériau.
-
Applications principales:
- Production de ciment:L'utilisation la plus courante des fours de calcination est la fabrication du ciment, où le carbonate de calcium (calcaire) est chauffé pour produire de l'oxyde de calcium (chaux) et du dioxyde de carbone.
- Purification des matériaux:La calcination est utilisée pour purifier les matériaux en éliminant les impuretés ou les composants volatils.
- Traitement chimique:Il est utilisé dans des processus tels que l'oxydation ou la décomposition pour modifier la composition chimique des matériaux.
-
Principales caractéristiques des fours de calcination:
- Uniformité à haute température:Les éléments chauffants sont positionnés sur tous les côtés de la chambre pour assurer une distribution uniforme de la chaleur, ce qui est essentiel pour obtenir des résultats constants.
- Commandes programmables:Les fours de calcination modernes sont souvent équipés de segments programmables (par exemple, 16 ou 30 segments) pour un contrôle précis des taux de chauffage et des profils de température.
- Efficacité énergétique:De nombreux fours utilisent une isolation en fibre céramique et des enveloppes en acier à double couche avec des ventilateurs de refroidissement pour minimiser la consommation d'énergie et assurer la sécurité de l'opérateur en maintenant les températures de surface à un niveau bas.
- Caractéristiques de sécurité:Des caractéristiques telles que le contrôle automatique de la température et les systèmes de refroidissement garantissent un fonctionnement sûr, même à des températures élevées.
-
Comparaison avec d'autres fours:
- Fours de frittage:Les fours de frittage sont également utilisés pour les processus à haute température, mais ils se concentrent sur la liaison des particules entre elles plutôt que sur l'élimination des composants volatils.
- Fours de carbonisation:Ces fours sont conçus pour convertir les matières organiques en carbone, souvent en mettant l'accent sur l'efficacité énergétique et l'absence de fumée, contrairement aux fours de calcination, qui se concentrent sur les transformations chimiques.
-
Importance industrielle:
- Les fours de calcination jouent un rôle essentiel dans des industries telles que la construction (production de ciment), la métallurgie (purification des métaux) et la fabrication de produits chimiques (décomposition des matériaux).
- Leur capacité à contrôler avec précision la température et les taux de chauffage les rend indispensables pour les processus exigeant des niveaux élevés de précision et de répétabilité.
-
Considérations relatives à la conception et au fonctionnement:
- Compatibilité des matériaux:La conception du four doit tenir compte des matériaux spécifiques traités, afin de garantir la compatibilité avec les températures élevées et les réactions chimiques.
- Plage de température:Les fours de calcination fonctionnent généralement à des températures allant jusqu'à 1200°C, certains modèles pouvant atteindre des températures encore plus élevées en fonction de l'application.
- Contrôle de la vitesse de chauffe:Un contrôle précis des taux de chauffage est essentiel pour obtenir les changements chimiques ou physiques souhaités sans endommager le matériau.
En comprenant ces points clés, un acheteur peut évaluer l'adéquation d'un four de calcination à ses besoins spécifiques, garantissant ainsi des performances et une efficacité optimales dans ses processus industriels.
Tableau récapitulatif :
Aspect | Détails |
---|---|
Objectif | Chauffer des matériaux à des températures élevées pour les déshydrater, les oxyder ou les décomposer. |
Applications principales | Production de ciment, purification des matériaux, traitement chimique. |
Caractéristiques principales | Uniformité à haute température, commandes programmables, efficacité énergétique, caractéristiques de sécurité. |
Plage de température | Jusqu'à 1200°C ou plus, selon l'application. |
Comparaison | Diffère des fours de frittage et de carbonisation par son objectif et son fonctionnement. |
Importance industrielle | Vital pour les industries de la construction, de la métallurgie et de la fabrication de produits chimiques. |
Prêt à améliorer vos processus industriels avec un four de calcination ? Contactez nous dès aujourd'hui pour trouver la solution idéale à vos besoins !