Un four rotatif, également connu sous le nom de four rotatif , est un équipement polyvalent et efficace utilisé dans diverses applications industrielles et de recherche. Sa fonction principale est de chauffer uniformément les matériaux tout en assurant une exposition constante à l'atmosphère, ce qui améliore la diffusion des gaz, réduit la consommation de gaz et améliore l'efficacité du traitement thermique. La capacité du four à pivoter et à s'incliner permet une manipulation et un placement précis des matériaux, ce qui le rend adapté aux processus tels que le frittage, le recuit, les réactions chimiques et la préparation des revêtements. Son chauffage uniforme, sa large applicabilité et son contrôle précis de la température le rendent indispensable dans des industries telles que la métallurgie, la science des matériaux, l'électronique et le traitement chimique.
Points clés expliqués :
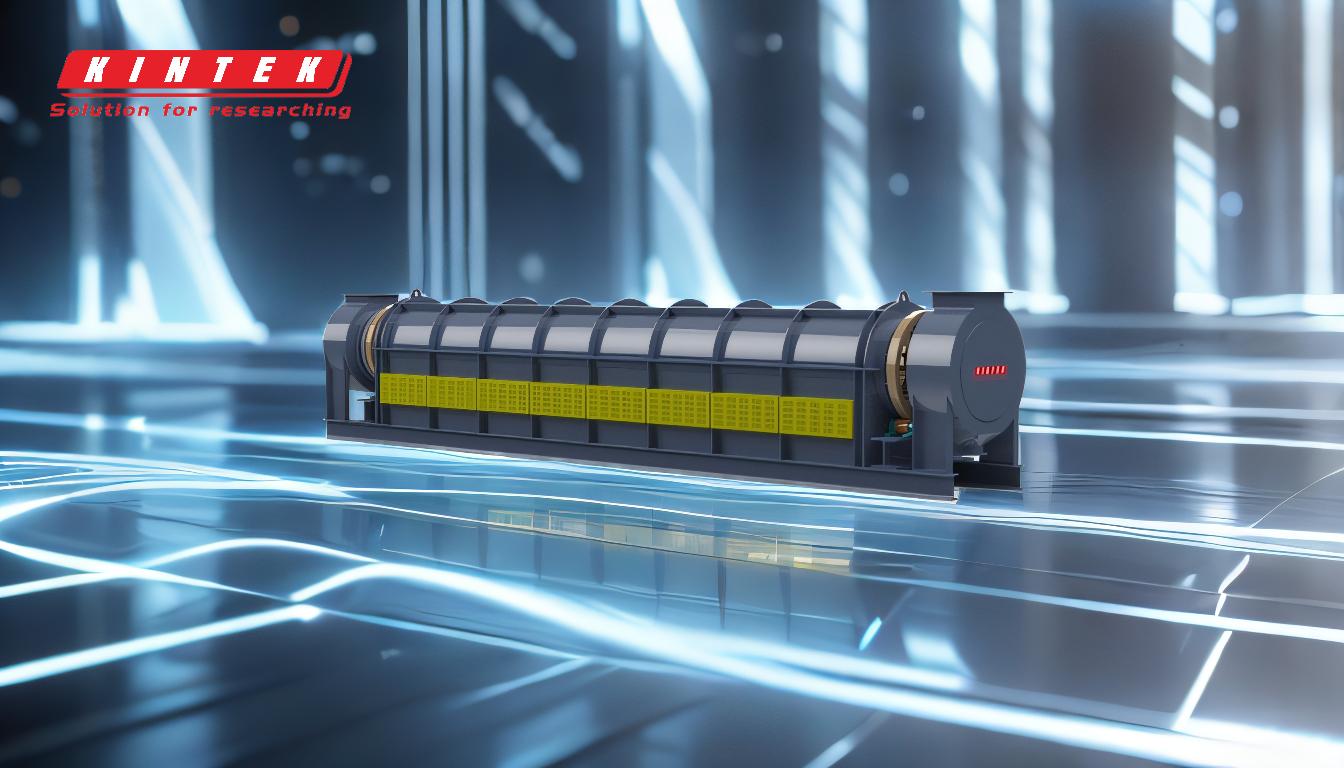
-
Chauffage et mélange de matériaux uniformes
- Le mouvement de rotation du four rotatif garantit que les matériaux sont entièrement mélangés, réduisant ainsi les gradients de température et améliorant les effets du traitement thermique.
- Ce chauffage uniforme est essentiel pour des processus tels que le frittage, où une répartition constante de la température est nécessaire pour obtenir les propriétés souhaitées du matériau, telles que la densité, la résistance et la résistance à la corrosion.
-
Mécanisme flexible d'inclinaison et de rotation
- Le four peut s'incliner entre 0 et 30 degrés et tourner à 360 degrés, permettant aux opérateurs d'ajuster la position du matériau en fonction des besoins expérimentaux ou opérationnels.
- Cette flexibilité améliore la manipulation des matériaux et l'efficacité opérationnelle, facilitant ainsi le placement et le traitement précis des matériaux.
-
Amélioration de la diffusion des gaz et de l’efficacité du traitement thermique
- Le mouvement continu des matériaux dans le four garantit que toute la surface est exposée à l’atmosphère, améliorant ainsi la diffusion des gaz et réduisant la consommation de gaz.
- Cette fonctionnalité est particulièrement bénéfique pour les processus tels que l’oxydation, la réduction et les réactions chimiques, où une exposition constante aux gaz réactifs est essentielle.
-
Large gamme d'applications
- Les fours rotatifs sont utilisés pour fritter des céramiques et des poudres métalliques, préparer des revêtements, conduire des réactions chimiques et effectuer un traitement thermique et un recuit de matériaux métalliques.
- Ils sont également utilisés dans des réactions d'oxydation et de réduction à haute température, ainsi que pour la calcination de matériaux granulaires ou en poudre à des températures allant jusqu'à 1 100 ℃.
-
Contrôle précis de la température
- Équipés de systèmes de contrôle informatique avancés, les fours rotatifs assurent une régulation précise de la température, garantissant un chauffage de haute qualité et des résultats de produits cohérents.
- Cette précision est cruciale pour des applications telles que la préparation de catalyseurs et la synthèse de matériaux, où la stabilité de la température a un impact direct sur les propriétés du produit final.
-
Homogénéité améliorée des produits
- Le profil de température constant maintenu dans les fours rotatifs améliore l’uniformité du produit, ce qui est essentiel pour obtenir les caractéristiques souhaitées des matériaux dans les environnements industriels et de recherche.
- Cette homogénéité est particulièrement importante dans des processus tels que la préparation des revêtements et la synthèse chimique, où même de légères variations peuvent affecter les performances.
-
Composants clés et caractéristiques de conception
- Les principaux composants d'un four rotatif comprennent le corps du four, le revêtement du four, l'engrenage d'entraînement et la source de chaleur interne.
- Ces composants fonctionnent ensemble pour garantir un transfert de chaleur efficace, une durabilité et une fiabilité opérationnelle, rendant le four adapté aux environnements industriels exigeants.
En résumé, le four rotatif est un outil hautement adaptable et efficace pour une large gamme d’applications de traitement thermique. Sa capacité à fournir un chauffage uniforme, un contrôle précis de la température et une exposition constante des matériaux le rend inestimable dans les industries nécessitant une modification et une préparation des matériaux de haute qualité.
Tableau récapitulatif :
Fonctionnalité | Avantages |
---|---|
Chauffage et mélange uniformes | Réduit les gradients de température, améliore les effets du traitement thermique |
Inclinaison et rotation flexibles | Améliore la manipulation des matériaux et le placement précis |
Diffusion des gaz améliorée | Assure une exposition constante à l’atmosphère, réduit la consommation de gaz |
Large gamme d'applications | Convient au frittage, au recuit, aux réactions chimiques et à la préparation de revêtements |
Contrôle précis de la température | Garantit un chauffage de haute qualité et des résultats de produits cohérents |
Homogénéité améliorée des produits | Améliore l'uniformité du matériau pour de meilleures performances |
Conception et composants durables | Garantit la fiabilité et l’efficacité dans les environnements industriels exigeants |
Prêt à améliorer le traitement de vos matériaux ? Contactez-nous aujourd'hui pour trouver le four rotatif parfait pour vos besoins !