Un four de type discontinu est un système de chauffage spécialisé conçu pour traiter des matériaux en lots discrets, ce qui le rend idéal pour les applications nécessitant un traitement thermique précis, des normes de salle blanche ou des atmosphères inertes. Ces fours traitent thermiquement les composants en augmentant la température de la pièce jusqu'à un maximum prédéterminé, en la maintenant pendant une durée donnée, puis en la refroidissant à une vitesse contrôlée. Ils sont particulièrement adaptés à la production de faibles volumes, aux pièces de grande taille ou complexes et aux procédés tels que la cémentation profonde. Les fours discontinus sont polyvalents, rentables et peuvent fonctionner avec ou sans atmosphère contrôlée, ce qui en fait un choix privilégié pour les industries qui ont besoin de solutions de traitement thermique sur mesure.
Explication des points clés :
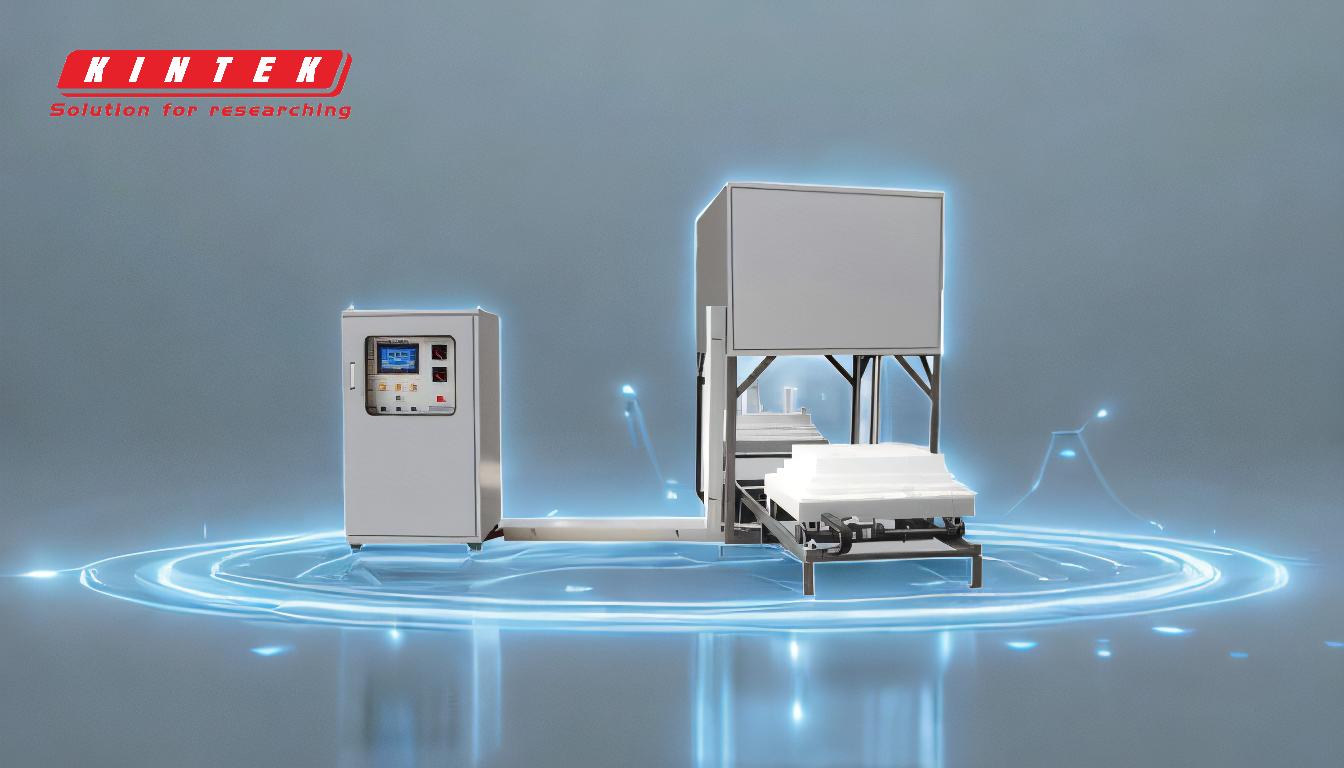
-
Définition et fonctionnement:
- Un four discontinu traite les matériaux par lots distincts, en chargeant et déchargeant la charge de travail comme une seule unité.
- Le four est scellé pendant le fonctionnement, ce qui garantit qu'aucun contaminant extérieur ne pénètre dans le four. Il convient donc aux applications en salle blanche et en atmosphère inerte.
-
Traitement thermique:
- Le four chauffe à partir de la température ambiante jusqu'à une température maximale spécifiée, à une vitesse contrôlée.
- Il maintient la température cible pendant une durée déterminée avant de refroidir à une vitesse prédéterminée.
- Ce processus garantit un traitement thermique cohérent et précis pour chaque lot.
-
Polyvalence des applications:
- Les fours discontinus gèrent des charges de travail variables, y compris des différences de poids, de taille, de qualité de matériau et d'exigences en matière de traitement thermique.
- Ils sont idéaux pour la production de faibles volumes, les pièces complexes ou de grande taille et les procédés spécialisés tels que la cémentation profonde.
-
Types de fours discontinus:
- Les types les plus courants sont les fours à caisson, les fours à fond ouvrant, les fours à trempe intégrale, les fours à cuvette et les fours à vide.
- Chaque type est conçu pour des applications spécifiques, telles que le détensionnement, la trempe ou le recuit.
-
Plage de température et capacité:
- Les fours discontinus fonctionnent généralement entre 1200℉ et 2500℉, accueillant une large gamme de métaux et d'alliages.
- Ils peuvent traiter des pièces d'une largeur allant jusqu'à 24 pouces, ce qui les rend adaptés aux composants de grande taille ou volumineux.
-
Options d'atmosphère contrôlée:
- Les fours discontinus peuvent fonctionner avec ou sans atmosphère contrôlée, ce qui offre une certaine souplesse pour répondre aux différents besoins en matière de traitement thermique.
- Les fours à vide et à atmosphère protectrice sont des variantes courantes, garantissant une oxydation ou une contamination minimale pendant le traitement.
-
Rentabilité:
- Comparés aux fours continus, les fours discontinus sont généralement moins chers, ce qui en fait un choix pratique pour les opérations à petite échelle ou les applications spécialisées.
-
Avantages par rapport aux fours continus:
- Les fours discontinus sont mieux adaptés à la production de faibles volumes et aux pièces complexes ou de grande taille qui sont difficiles à traiter dans les systèmes continus.
- Ils offrent une plus grande flexibilité dans le traitement de divers matériaux et exigences en matière de traitement thermique.
En comprenant ces points clés, les acheteurs d'équipements et de consommables peuvent décider en toute connaissance de cause si un four discontinu répond à leurs besoins spécifiques en matière de traitement thermique.
Tableau récapitulatif :
Caractéristiques | Description |
---|---|
Fonctionnement | Traite les matériaux en lots discrets avec un fonctionnement scellé et sans contamination. |
Traitement thermique | Chauffe, maintient et refroidit les matériaux à des vitesses contrôlées pour des résultats constants. |
Applications | Idéal pour la production de faibles volumes, les grandes pièces et les procédés tels que la cémentation. |
Types de fours | Fours à caisson, à fond ouvrant, à trempe intégrale, à fosse et à vide. |
Plage de température | Fonctionne entre 1200℉ et 2500℉, convient à divers métaux et alliages. |
Options d'atmosphère | Peut fonctionner avec ou sans atmosphère contrôlée (par exemple, vide, gaz inerte). |
Rentabilité | Plus abordable que les fours continus pour les applications spécialisées. |
Prêt à améliorer votre processus de traitement thermique ? Contactez nous dès aujourd'hui pour trouver le four discontinu idéal pour vos besoins !