Le traitement thermique du molybdène est un processus essentiel pour améliorer ses propriétés mécaniques, telles que la résistance, la ductilité et la résistance aux températures élevées. Le molybdène, étant un métal réfractaire, nécessite une manipulation prudente lors du traitement thermique pour éviter la fragilité et la fissuration. Le processus implique généralement un recuit pour soulager les contraintes internes et améliorer l'usinabilité, ainsi qu'un refroidissement contrôlé pour maintenir son intégrité structurelle. Les bateaux en molybdène, souvent utilisés dans les applications à haute température, bénéficient de ces traitements pour garantir durabilité et performances dans des environnements exigeants tels que les opérations de four, le frittage et le traitement des terres rares.
Points clés expliqués :
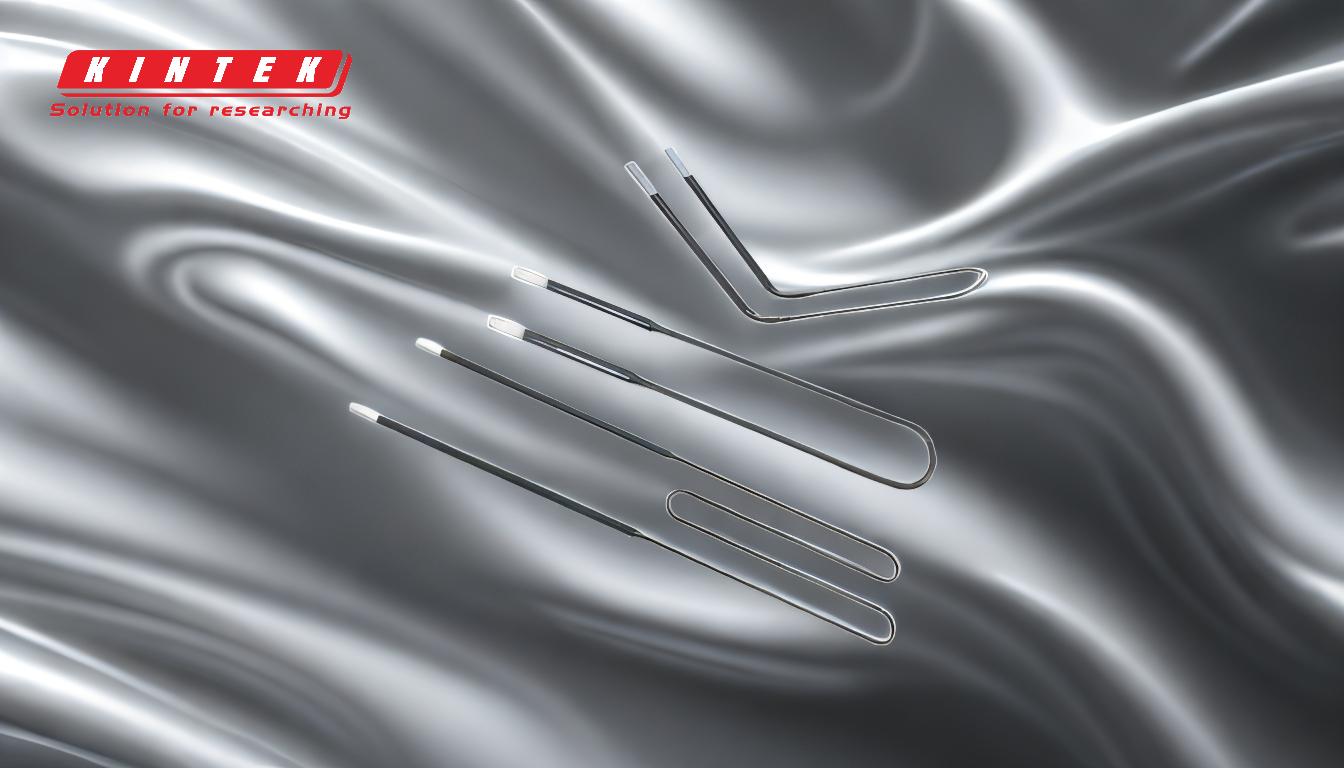
-
Propriétés du Molybdène:
- Le molybdène est un métal réfractaire connu pour son point de fusion élevé (2623°C), son excellente conductivité thermique et sa résistance à la corrosion et à l'usure.
- Il est largement utilisé dans les applications à haute température, comme dans les fours sous vide, où il peut résister à des températures allant jusqu'à 1 700 °C sans dégradation significative.
- Sa ductilité et sa résistance le rendent adapté au formage de composants tels que bateaux en molybdène , qui sont utilisés dans des industries telles que le traitement des terres rares et le frittage du combustible nucléaire.
-
Objectifs du traitement thermique:
- L'objectif principal du traitement thermique du molybdène est de soulager les contraintes internes induites lors des processus de fabrication tels que la découpe, le pliage et le soudage.
- Le traitement thermique améliore l'usinabilité, la ductilité et les performances mécaniques globales, garantissant que le matériau peut résister à des environnements à haute température et à fortes contraintes.
-
Processus de recuit:
- Le recuit est le traitement thermique le plus courant pour le molybdène. Il s'agit de chauffer le matériau à une température spécifique (généralement entre 800°C et 1 200°C) et de le maintenir pendant une période définie pour permettre la recristallisation et la relaxation des contraintes.
- Un refroidissement contrôlé est essentiel après le recuit pour éviter la formation de phases fragiles et maintenir la ductilité du matériau.
-
Applications dans des environnements à haute température:
- Les nacelles en molybdène sont souvent utilisées dans les fours pour des processus tels que le frittage, où elles sont exposées à des températures extrêmes. Un traitement thermique approprié garantit leur stabilité dimensionnelle et leur longévité.
- Dans des industries comme la métallurgie, le verre et la céramique, les composants en molybdène doivent conserver leur intégrité structurelle dans des conditions continues de haute température.
-
Les défis du traitement thermique:
- Le molybdène devient cassant à des températures supérieures à 1 700°C, le traitement thermique doit donc être soigneusement contrôlé pour éviter de dépasser ce seuil.
- Un refroidissement rapide ou un chauffage inégal peuvent entraîner des fissures ou des déformations, ce qui compromet les performances du matériau.
-
Comparaison avec d'autres matériaux:
- Contrairement au tungstène, qui est plus dur et plus cassant, le molybdène offre une meilleure ductilité et une plus grande facilité de fabrication, ce qui le rend plus adapté aux formes complexes comme les bateaux et les fils.
- La résistance du molybdène aux taches et à la corrosion lors des processus de fusion en fait un matériau privilégié dans l'industrie du verre.
-
Pertinence industrielle:
- Les bateaux en molybdène et d'autres composants sont essentiels dans des applications telles que le frittage de condensateurs déchargés, le traitement du combustible nucléaire et la production d'éléments de terres rares.
- La capacité du matériau à résister à des températures élevées et à des environnements corrosifs garantit son utilisation généralisée dans les processus industriels avancés.
En comprenant les processus de traitement thermique et les propriétés du molybdène, les fabricants peuvent optimiser les performances des bateaux en molybdène et d'autres composants, en garantissant qu'ils répondent aux exigences rigoureuses des applications à haute température.
Tableau récapitulatif :
Aspect | Détails |
---|---|
Propriétés | Point de fusion élevé (2623°C), conductivité thermique, résistance à la corrosion |
Objectifs du traitement thermique | Soulage les contraintes internes, améliore l'usinabilité et améliore la ductilité |
Processus de recuit | Chauffer entre 800°C et 1 200°C, maintenir pour la recristallisation et contrôler le refroidissement |
Applications | Exploitation des fours, frittage, traitement des terres rares et combustible nucléaire |
Défis | Éviter la fragilité au-dessus de 1 700 °C, éviter les fissures lors d'un refroidissement rapide |
Comparaison avec le tungstène | Meilleure ductilité, fabrication plus facile et résistance aux taches |
Améliorez les performances de vos composants en molybdène : contactez nos experts dès aujourd'hui pour des solutions de traitement thermique sur mesure !