L'objectif premier d'un four à induction est de fondre efficacement et proprement des métaux, tels que la ferraille, la fonte brute, l'aluminium, le cuivre et les métaux précieux, en un métal fondu de haute qualité avec un contrôle précis de la composition, de la température et de la pureté.Ce processus implique la fusion de matières premières solides, l'ajustement des compositions chimiques, l'élimination des éléments nocifs et la garantie que le métal fondu est adapté à la coulée.Les fours à induction sont appréciés pour leur efficacité énergétique, leur respect de l'environnement et leur capacité à produire un métal fondu homogène avec une contamination minimale.Ils sont largement utilisés dans les fonderies pour produire des pièces moulées d'une qualité et d'une régularité supérieures.
Explication des points clés :
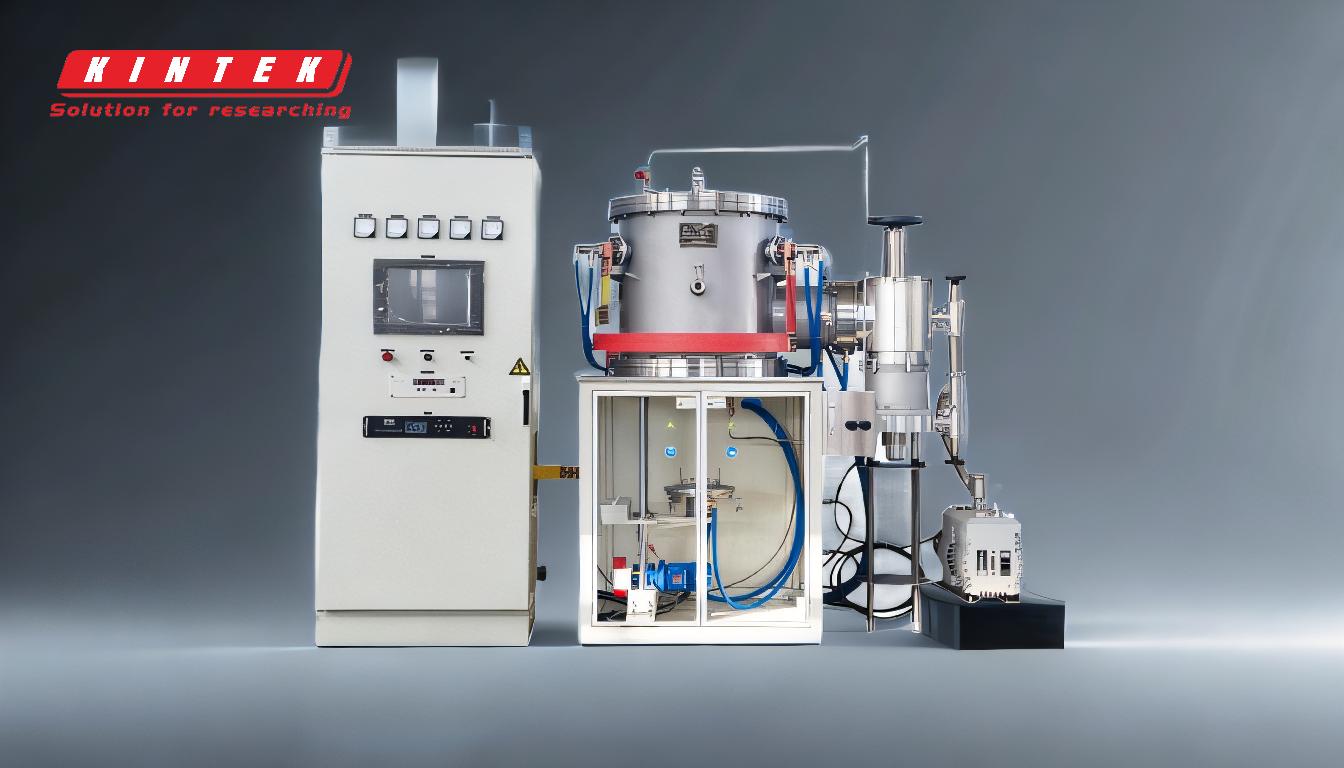
-
Fusion efficace des métaux:
- Les fours à induction sont conçus pour faire fondre des matières premières solides telles que la ferraille, la fonte brute, l'aluminium et d'autres métaux.Ce résultat est obtenu grâce à l'induction électromagnétique, qui génère de la chaleur directement à l'intérieur du métal, ce qui garantit un chauffage rapide et uniforme.
- Le processus est plus rapide et plus économe en énergie que les méthodes de fusion traditionnelles, telles que les cubilots ou les fours à gaz.
-
Contrôle précis de la composition et de la température:
- Les fours à induction permettent d'ajuster avec précision la composition chimique du métal en fusion.Par exemple, des éléments comme le silicium et le carbone peuvent être ajustés avec précision pour répondre à des exigences spécifiques.
- La température du métal en fusion est étroitement contrôlée, ce qui permet d'atteindre l'état optimal pour la coulée et le moulage.Cette précision permet de minimiser les défauts du produit final.
-
Purification et élimination des éléments nocifs:
- Le four facilite l'élimination des éléments nocifs tels que le soufre et le phosphore, qui peuvent dégrader la qualité du métal.Ce processus de purification garantit que le métal fondu a une faible teneur en gaz et une qualité d'inclusion élevée.
- Le brassage électromagnétique des fours à induction crée un mélange homogène, ce qui améliore encore la pureté et la consistance du métal fondu.
-
Efficacité énergétique et avantages environnementaux:
- Les fours à induction sont connus pour leur faible consommation d'énergie et leur impact minimal sur l'environnement.Ils produisent moins de bruit, de fumée, de gaz, de poussière et de résidus que les méthodes de fusion traditionnelles.
- L'absence de combustion ou d'arcs électriques rend le processus plus propre et plus sûr, ce qui réduit la pollution et améliore les conditions de travail des opérateurs.
-
Qualité de coulée supérieure:
- Le processus de fusion contrôlée garantit que le métal en fusion présente une faible différence de température entre le noyau et la surface, ce qui permet de produire des pièces moulées de haute qualité présentant moins de défauts.
- La possibilité de fonctionner à la fois dans des conditions atmosphériques et sous vide réduit encore la contamination, ce qui rend les fours à induction idéaux pour la production de métaux de haute pureté.
-
Polyvalence des applications:
- Les fours à induction sont utilisés dans les fonderies pour faire fondre une large gamme de métaux, notamment le fer, l'acier, le cuivre, l'aluminium et les métaux précieux.Une fois fondu, le métal est versé dans des moules pour créer des pièces coulées.
- La souplesse de manipulation de différents métaux et la capacité à produire des résultats cohérents font des fours à induction un choix privilégié dans les industries métallurgiques modernes.
-
Rentabilité et avantages opérationnels:
- Le processus de chauffage et de fusion rapide réduit le temps et les coûts de production.Les fours à induction minimisent également les pertes de matériaux dues à l'oxydation et à la décarburation, ce qui permet d'économiser sur les coûts des matières premières et des matrices.
- L'amélioration de l'environnement de travail et la réduction des besoins de maintenance contribuent également à la réduction des coûts et à l'efficacité opérationnelle.
En résumé, l'objectif d'un four à induction est de fournir une méthode propre, efficace et contrôlée pour fondre les métaux, en garantissant un métal fondu de haute qualité avec une composition et une température précises.Cela en fait un outil indispensable dans les fonderies modernes et les industries métallurgiques.
Tableau récapitulatif :
Caractéristique principale | Description |
---|---|
Fusion efficace | Chauffage rapide et uniforme par induction électromagnétique pour une fusion plus rapide. |
Contrôle précis | Ajuster la composition chimique et la température pour obtenir des résultats de coulée optimaux. |
Purification | Élimine les éléments nocifs tels que le soufre et le phosphore pour obtenir un métal de grande pureté. |
Efficacité énergétique | Faible consommation d'énergie et impact minimal sur l'environnement. |
Qualité de coulée supérieure | Produit des pièces coulées de haute qualité avec un minimum de défauts et de contamination. |
Polyvalence | Fusion d'une large gamme de métaux, y compris l'acier, l'aluminium et les métaux précieux. |
Rentabilité | Réduit le temps de production, les pertes de matériaux et les coûts d'exploitation. |
Découvrez comment un four à induction peut transformer votre processus d'usinage des métaux. contactez-nous dès aujourd'hui pour obtenir des conseils d'experts !