Le frittage est une technique de fabrication qui permet de fusionner des matériaux en poudre en une masse solide à l'aide de la chaleur et de la pression, sans atteindre le point de fusion du matériau.Ce procédé est largement utilisé dans des industries telles que la métallurgie, la céramique et les plastiques pour créer des produits denses et durables.Les principales étapes consistent à préparer le matériau en poudre, à le comprimer pour lui donner la forme souhaitée et à le chauffer pour faciliter la diffusion atomique, qui lie les particules entre elles.Le frittage améliore les propriétés des matériaux telles que la résistance, la densité et l'intégrité structurelle, ce qui le rend essentiel pour la production de composants allant de l'acier aux céramiques de pointe.
Explication des points clés :
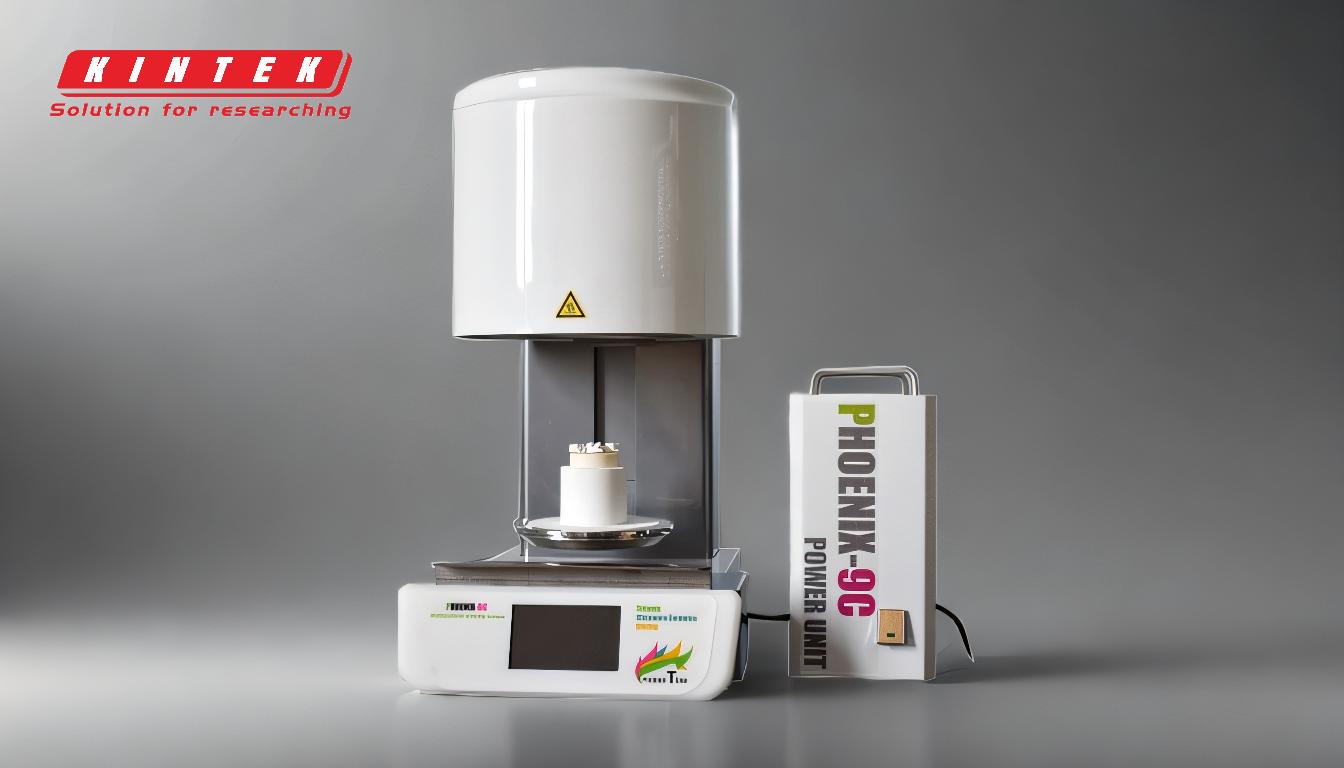
-
Définition et objectif du frittage
- Le frittage est un procédé qui permet de lier des matériaux en poudre en une masse solide grâce à la chaleur et à la pression, sans faire fondre le matériau.
- Il est utilisé pour créer des produits denses, solides et durables dans des industries telles que la métallurgie, la céramique et les plastiques.
- L'objectif principal est de réduire la porosité et d'augmenter l'intégrité structurelle en fusionnant les particules au niveau atomique.
-
Principales étapes du processus de frittage
-
Préparation du matériau en poudre:
- La matière première est broyée en une fine poudre et mélangée à des agents de couplage ou à des liants si nécessaire.
- Cette étape garantit l'uniformité et la consistance du produit final.
-
Compression:
- La poudre est pressée dans la forme souhaitée à l'aide de moules ou d'outils à haute pression.
- Cette étape permet de créer un "compact vert", c'est-à-dire une structure peu adhérente prête à être frittée.
-
Chauffage et consolidation:
- Le compact vert est chauffé dans un four à une température inférieure au point de fusion du matériau.
- La chaleur facilite la diffusion des atomes, ce qui permet aux particules de se lier et de se densifier.
-
Refroidissement et solidification:
- Après le frittage, le matériau est refroidi pour se solidifier en une masse unifiée et dense.
-
Préparation du matériau en poudre:
-
Types de frittage
-
Frittage à l'état solide:
- Les particules se lient par diffusion atomique sans phase liquide.
- Couramment utilisé pour les métaux et les céramiques.
-
Frittage en phase liquide (LPS):
- Une petite quantité de phase liquide est introduite pour accélérer la liaison des particules.
- Souvent utilisé pour les matériaux ayant un point de fusion élevé ou des formes complexes.
-
Frittage à l'état solide:
-
Applications du frittage
-
Métallurgie:
- Utilisé pour produire de l'acier, du fer et d'autres composants métalliques à usage industriel.
- Exemple :Le minerai de fer fritté est utilisé dans les hauts fourneaux pour produire de l'acier.
-
La céramique:
- Crée des produits céramiques solides et résistants à la chaleur, tels que des carreaux, des isolateurs et des outils de coupe.
-
Plastiques:
- Produit des composants en plastique durables avec des propriétés mécaniques améliorées.
-
Métallurgie:
-
Avantages du frittage
-
Propriétés améliorées des matériaux:
- Augmente la densité, la résistance et la durabilité du produit final.
-
Rentable:
- Réduit les déchets de matériaux et la consommation d'énergie par rapport aux procédés de fusion.
-
Polyvalence:
- Peut être utilisé pour une large gamme de matériaux et de formes complexes.
-
Propriétés améliorées des matériaux:
-
Défis et considérations
-
Contrôle de la température:
- Le contrôle précis des taux de chauffage et de refroidissement est essentiel pour éviter les défauts.
-
Gestion de la porosité:
- Bien que le frittage réduise la porosité, certains pores résiduels peuvent subsister et affecter les performances du matériau.
-
Sélection des matériaux:
- Tous les matériaux ne se prêtent pas au frittage ; certains peuvent nécessiter des liants ou des additifs supplémentaires.
-
Contrôle de la température:
-
Mise en œuvre industrielle
-
Equipement:
- Les fours, les presses et les moules sont essentiels au processus de frittage.
-
Optimisation du processus:
- Les paramètres tels que la température, la pression et le temps de frittage doivent être soigneusement contrôlés pour obtenir des résultats optimaux.
-
Equipement:
En comprenant le processus de frittage, les fabricants peuvent produire des matériaux et des composants de haute qualité adaptés à des besoins industriels spécifiques.Cette méthode offre un équilibre entre l'efficacité, la rentabilité et la polyvalence, ce qui en fait une pierre angulaire de la fabrication moderne.
Tableau récapitulatif :
Aspect | Détails |
---|---|
Définition | Lier des matériaux pulvérulents en une masse solide à l'aide de la chaleur et de la pression. |
Étapes clés |
1.Préparation de la matière en poudre
2.Compression 3.Chauffage 4.Refroidissement |
Types de frittage | Frittage à l'état solide, frittage en phase liquide (LPS) |
Applications | Métallurgie, céramique, plastiques |
Avantages | Résistance accrue, rentabilité, polyvalence |
Défis | Contrôle de la température, gestion de la porosité, sélection des matériaux |
Prêt à optimiser votre production de matériaux ? Contactez nous dès aujourd'hui pour en savoir plus sur les solutions de frittage !