La "meilleure" méthode de traitement thermique dépend entièrement du résultat souhaité pour le matériau, comme la dureté, la ductilité, l'usinabilité ou le relâchement des contraintes. Le recuit est idéal pour adoucir les métaux, améliorer l'usinabilité et soulager les contraintes internes. La trempe est utilisée pour refroidir rapidement les métaux, ce qui augmente leur dureté mais les rend souvent cassants. Le revenu réduit la fragilité après la trempe tout en maintenant la dureté. La normalisation affine la structure du grain et améliore les propriétés mécaniques. La cémentation améliore la dureté superficielle tout en conservant la ductilité du noyau. Chaque méthode a des objectifs spécifiques et le choix dépend de l'application prévue du matériau et des propriétés requises.
Explication des points clés :
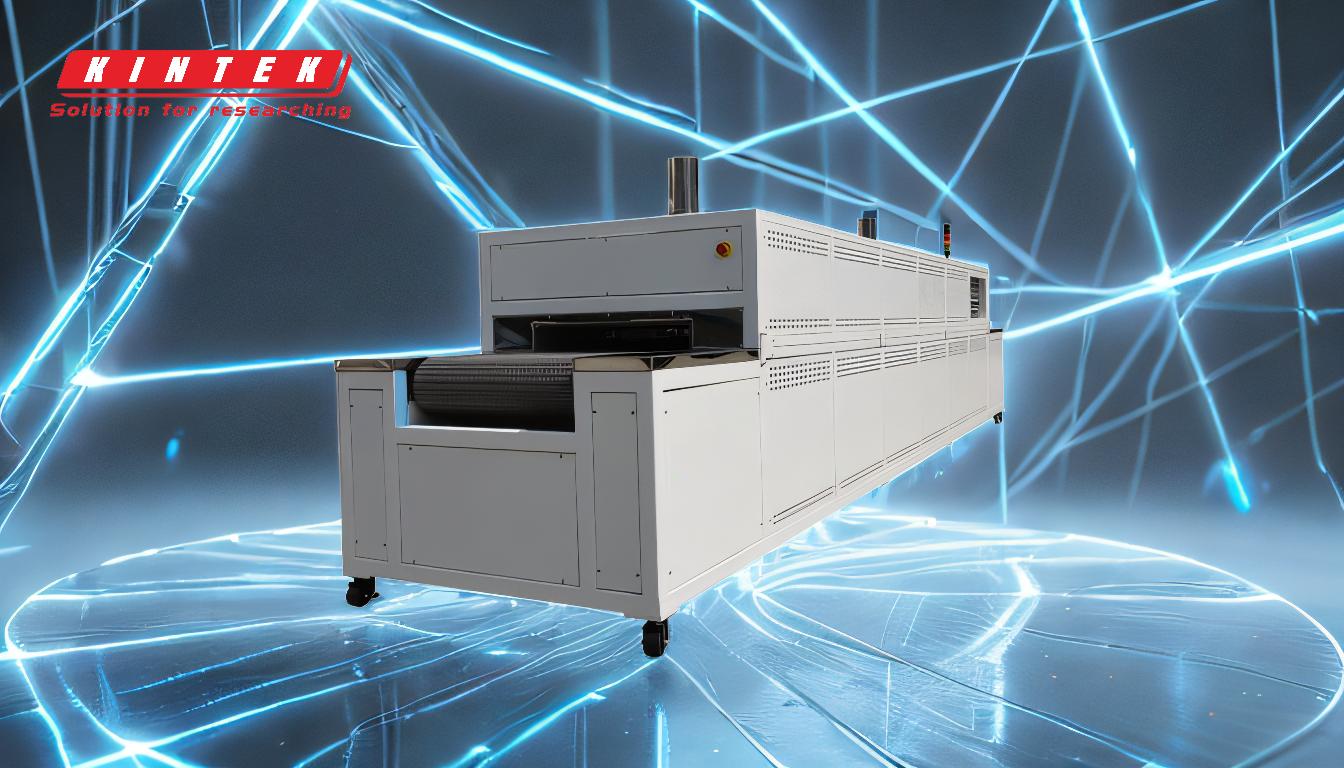
-
Le recuit:
- Objectif: Ramollir les métaux, améliorer l'usinabilité et soulager les tensions internes.
- Procédé : Le recuit est un procédé qui permet d'assouplir les métaux.: Les métaux sont chauffés puis progressivement refroidis.
- Résultat: Une structure uniforme et plus souple, idéale pour les matériaux qui doivent être travaillés ultérieurement.
- Applications: Utilisé dans les processus de fabrication où la ductilité et une dureté réduite sont requises.
-
Trempe:
- Objectif: Augmente la dureté et la résistance.
- Procédé: Refroidissement rapide des métaux chauffés, souvent dans l'eau, l'huile ou l'air.
- Résultat: Matériau dur mais cassant.
- Applications: Convient aux outils et aux composants nécessitant une dureté de surface élevée.
-
Revenu:
- Objectif: Réduit la fragilité tout en maintenant la dureté.
- Procédé: Chauffer les métaux trempés à une température plus basse, puis les refroidir.
- Résultat: Amélioration de la ténacité et de la ductilité.
- Applications: Utilisé dans les outils et les composants structurels pour équilibrer la dureté et la durabilité.
-
Normalisation:
- Objectif: Affine la structure du grain et améliore les propriétés mécaniques.
- Procédé: Chauffer les métaux à haute température et les refroidir à l'air.
- Résultat: Structure de grain uniforme et résistance accrue.
- Applications: Courant dans la fabrication de l'acier pour préparer les matériaux à un traitement ultérieur.
-
Cémentation:
- Objectif: Augmenter la dureté de la surface tout en conservant un noyau ductile.
- Le procédé: Ajout de carbone ou d'azote à la couche superficielle du métal.
- Résultat: L'extérieur est dur et l'intérieur est résistant.
- Applications: Idéal pour les engrenages, les arbres et autres composants nécessitant une résistance à l'usure.
-
Transformation martensitique:
- Objet: Permet d'obtenir une dureté et une résistance élevées.
- Processus: Refroidissement rapide pour former de la martensite, une microstructure dure.
- Résultat : La martensite est une microstructure dure.: Matériau extrêmement dur mais cassant.
- Applications: Utilisé dans des applications à haute résistance comme les couteaux et les outils de coupe.
-
La cémentation:
- Objectif: Augmenter la dureté de la surface en ajoutant du carbone.
- Procédé: Chauffage des métaux dans un environnement riche en carbone.
- Résultat: Surface durcie avec un noyau plus mou.
- Applications: Convient aux composants nécessitant une résistance à l'usure.
-
Réduction des contraintes:
- Objectif: Réduit les contraintes résiduelles dans les métaux.
- Procédé: Chauffer les métaux à une température modérée et les refroidir lentement.
- Résultat: Amélioration de la stabilité dimensionnelle et réduction du risque de fissuration.
- Applications: Utilisé dans les pièces soudées ou usinées pour éviter les déformations.
-
Recuit brillant:
- Objectif: Minimise l'oxydation pendant le recuit.
- Procédé: Chauffage des métaux dans une atmosphère protectrice (hydrogène, azote ou argon).
- Résultat: Surface propre et exempte d'oxydation.
- Applications: Utilisé pour l'acier inoxydable et d'autres matériaux nécessitant une finition impeccable.
-
Frittage:
- Objectif: Lier des poudres métalliques en une structure solide.
- Le procédé: Chauffer les métaux juste en dessous de leur point de fusion dans une atmosphère protectrice.
- Résultat: Des composants denses et solides.
- Applications: Courant dans la métallurgie des poudres pour créer des formes complexes.
En conclusion, la "meilleure" méthode de traitement thermique dépend des exigences spécifiques du matériau et de l'usage auquel il est destiné. Par exemple, le recuit est le meilleur moyen d'adoucir et de réduire les contraintes, tandis que la trempe et le revenu sont idéaux pour obtenir une dureté et une ténacité élevées. Il est essentiel de comprendre les propriétés et les processus de chaque méthode pour sélectionner le traitement thermique approprié à une application donnée.
Tableau récapitulatif :
Méthode | Objectif | Procédé | Résultat | Applications |
---|---|---|---|---|
Recuit | Ramollit les métaux, améliore l'usinabilité, soulage les tensions internes. | Les métaux sont chauffés et progressivement refroidis | Structure uniforme et plus souple | Procédés de fabrication nécessitant de la ductilité et une dureté réduite |
Trempe | Augmente la dureté et la résistance | Refroidissement rapide des métaux chauffés (eau, huile ou air) | Matériau dur mais cassant | Outils et composants nécessitant une dureté de surface élevée |
Revenu | Réduit la fragilité tout en maintenant la dureté | Chauffage des métaux trempés à une température plus basse et refroidissement | Amélioration de la ténacité et de la ductilité | Outils et composants structurels équilibrant la dureté et la durabilité |
Normalisation | Affine la structure du grain, améliore les propriétés mécaniques | Chauffage des métaux à une température élevée et refroidissement à l'air | Structure uniforme du grain et résistance accrue | Fabrication de l'acier en vue d'un traitement ultérieur |
Cémentation | Augmente la dureté de la surface tout en conservant un noyau ductile | Ajout de carbone ou d'azote à la couche superficielle | Extérieur dur avec intérieur résistant | Engrenages, arbres et composants nécessitant une résistance à l'usure |
Transformation martensitique | Permet d'obtenir une dureté et une résistance élevées | Refroidissement rapide pour former de la martensite | Matériau extrêmement dur mais cassant | Applications à haute résistance comme les couteaux et les outils de coupe |
Carburation | Augmente la dureté de la surface en ajoutant du carbone | Chauffage des métaux dans un environnement riche en carbone | Surface durcie avec un noyau plus mou | Composants nécessitant une résistance à l'usure |
Réduction des contraintes | Réduit les contraintes résiduelles dans les métaux | Chauffage des métaux à une température modérée et refroidissement lent | Amélioration de la stabilité dimensionnelle et réduction du risque de fissuration | Pièces soudées ou usinées pour éviter les déformations |
Recuit brillant | Minimise l'oxydation pendant le recuit | Chauffage des métaux dans une atmosphère protectrice (hydrogène, azote ou argon) | Surface propre et exempte d'oxydation | Acier inoxydable et matériaux nécessitant une finition impeccable |
Frittage | Liaison de poudres métalliques en une structure solide | Chauffage des métaux juste en dessous de leur point de fusion dans une atmosphère protectrice | Composants denses et solides | La métallurgie des poudres permet de créer des formes complexes. |
Vous avez besoin d'aide pour choisir la méthode de traitement thermique adaptée à vos matériaux ? Contactez nos experts dès aujourd'hui pour des solutions sur mesure !