Table des matières
Introduction aux fours de fusion sous vide
Les fours de fusion à induction sous vide se sont imposés comme une technologie révolutionnaire dans le traitement des métaux, répondant aux exigences uniques des matériaux avancés. Ces fours fonctionnent sous vide, ce qui permet un contrôle précis de la température, l'élimination des gaz et la prévention de l'oxydation, avec pour résultat des alliages de haute pureté et de haute performance. Les fours de fusion par induction sous vide ont révolutionné la production d'alliages de haute qualité aux propriétés exceptionnelles, ce qui en fait des outils indispensables à la fabrication et à la recherche de pointe.
Composants d'un four de fusion par induction sous vide
Un four de fusion par induction sous vide est un équipement polyvalent dans le domaine de la métallurgie, capable de fondre une large gamme de métaux et d'alliages, y compris les superalliages, l'aluminium, l'acier inoxydable et bien d'autres encore. Son fonctionnement repose sur l'induction électromagnétique sous vide, ce qui empêche la contamination des métaux fondus par des gaz réactifs tels que l'oxygène, l'azote et l'hydrogène.
Les principaux composants d'un four de fusion par induction sous vide sont les suivants :
-
Le corps du four : Le corps du four abrite les autres composants et fournit un environnement étanche pour le fonctionnement sous vide. Il est généralement fabriqué à partir de matériaux durables capables de résister à des températures élevées et de maintenir l'intégrité du vide.
-
Alimentation électrique à moyenne fréquence : Cette unité fournit l'énergie électrique nécessaire à la génération du champ magnétique pour le chauffage par induction. Elle se compose d'une source d'énergie, de transformateurs et d'un circuit de commande pour réguler la puissance de sortie.
-
Système de vide : Le système à vide est chargé de créer et de maintenir le vide dans la chambre du four. Il comprend une pompe à vide, des jauges à vide et des vannes pour contrôler le niveau de vide. La pompe à vide élimine l'air et les autres gaz de la chambre, ce qui permet d'obtenir les conditions de vide nécessaires à la fusion.
-
Système de refroidissement : Le système de refroidissement empêche la surchauffe des composants du four, en particulier la bobine d'induction et le creuset. Il utilise généralement une combinaison de canaux refroidis à l'eau et de ventilateurs pour dissiper efficacement la chaleur.
-
Système de commande électrique : Ce système surveille et contrôle le fonctionnement du four, notamment la température, le niveau de vide et la puissance absorbée. Il garantit que le four fonctionne selon des paramètres sûrs et efficaces.
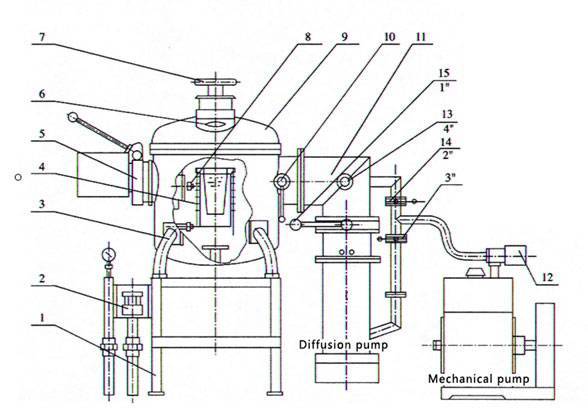
Outre ces composants essentiels, les fours de fusion par induction sous vide peuvent également être équipés de composants auxiliaires en fonction des exigences spécifiques du processus. Il peut s'agir des éléments suivants
- Chariot de transmission pour faciliter le déplacement du four
- Mécanismes d'ouverture et de fermeture de la porte du four
- Cuve de coulée centrifuge pour la coulée du métal en fusion
- Fenêtre d'observation pour contrôler le processus de fusion
- un système de filtrage des gaz pour éliminer les impuretés dans l'environnement sous vide.
La configuration et la sélection des composants d'un four de fusion par induction sous vide varient en fonction de l'application spécifique et des matériaux à fondre. En examinant attentivement les exigences du processus de fusion, il est possible d'optimiser les performances du four et d'obtenir les résultats souhaités.
Fonctionnement d'un four de fusion par induction sous vide
La fusion par induction sous vide est une technique de fusion spécialisée qui consiste à chauffer et à fondre le métal sous vide. Ce procédé présente plusieurs avantages, notamment l'élimination des impuretés, un contrôle précis de la température et la possibilité de fondre une large gamme de métaux.
Le four de fusion par induction sous vide se compose de plusieurs éléments clés :
- La chambre à vide : Cette chambre hermétique abrite la bobine d'induction et le creuset.
- Bobine d'induction : Cette bobine génère des champs électromagnétiques qui induisent des courants de Foucault dans le métal, ce qui le fait chauffer et fondre.
- Creuset : Ce récipient contient le métal pendant le processus de fusion.
- Système de vide : Ce système évacue l'air de la chambre, créant ainsi un vide.
- Système de refroidissement : Ce système fait circuler de l'eau dans le four pour éviter la surchauffe.
Le fonctionnement d'un four de fusion par induction sous vide comprend les étapes suivantes :
- Chargement du four : Le métal à fondre est placé dans le creuset.
- Évacuation de la chambre : Le système de vide est activé pour éliminer l'air de la chambre.
- Mise sous tension : La bobine d'induction est alimentée en électricité, ce qui génère des champs électromagnétiques qui chauffent le métal.
- Fusion du métal : Le métal fond progressivement et forme un bain de fusion.
- Affinage du métal : Les impuretés sont éliminées du métal fondu par des réactions chimiques, la dissociation, la flottation et la volatilisation.
- Ajustement de la chimie : La composition du métal en fusion est ajustée en ajoutant des éléments d'alliage ou en éliminant les impuretés.
- Couler le métal : Lorsque la composition et la température souhaitées sont atteintes, le métal en fusion est versé dans un moule ou un creuset.
La fusion par induction sous vide est une technique de fusion polyvalente et efficace qui est utilisée pour un large éventail d'applications, notamment :
- Production de métaux de haute pureté : La fusion par induction sous vide permet de produire des métaux présentant des niveaux d'impuretés extrêmement faibles.
- Fusion de métaux réactifs : Les métaux réactifs à l'oxygène ou à d'autres gaz peuvent être fondus sous vide pour éviter toute contamination.
- Production d'alliages : La fusion par induction sous vide peut être utilisée pour produire des alliages ayant des compositions et des propriétés précises.
- Recyclage des métaux : La fusion par induction sous vide peut être utilisée pour recycler les métaux et éliminer les impuretés.
Avantages des fours de fusion par induction sous vide
Les fours de fusion par induction sous vide (VIM) offrent une multitude d'avantages, ce qui en fait un choix idéal pour diverses applications dans l'industrie métallurgique. Ces fours fonctionnent sous vide, ce qui permet de contrôler avec précision les processus de fusion et de solidification, et d'obtenir ainsi des matériaux de haute qualité aux propriétés adaptées. Examinons les principaux avantages des fours VIM :
Pureté et qualité élevées
L'un des principaux avantages des fours VIM est leur capacité à produire des matériaux d'une grande pureté et d'une grande qualité. L'environnement sous vide élimine le risque de contamination par l'oxygène, l'azote et les autres gaz présents dans l'atmosphère. Il en résulte une fusion plus propre et plus homogène, exempte d'inclusions et d'impuretés nocives susceptibles d'avoir un impact sur les propriétés mécaniques du matériau.
Atmosphère contrôlée
Dans la chambre à vide, l'atmosphère est étroitement contrôlée. Seuls des gaz spécifiques sont introduits à des pressions précises. Ce niveau de contrôle permet de maîtriser la composition chimique du matériau fondu et toute réactivité. L'oxydation ou les réactions indésirables avec les gaz ambiants sont évitées, ce qui garantit la pureté et la qualité du produit final.
Fusion et refroidissement rapides
Les fours VIM permettent des taux de fusion et de refroidissement rapides grâce à l'absence de résistance de l'air et à l'utilisation du chauffage par induction. Ce processus de chauffage et de refroidissement rapide permet d'affiner la structure des grains, d'améliorer les propriétés mécaniques et d'accroître l'homogénéité du matériau.
Consommation d'énergie réduite
Les fours VIM sont très économes en énergie. L'environnement sous vide minimise la perte de chaleur par convection et radiation, ce qui permet une utilisation plus efficace de l'énergie. En outre, les cycles de fusion et de refroidissement rapides réduisent le temps de traitement global, ce qui diminue encore la consommation d'énergie.
Évolutivité
Les fours VIM peuvent être conçus et dimensionnés pour s'adapter à différentes capacités et exigences de production. Cette flexibilité permet de les utiliser aussi bien pour la recherche à petite échelle que pour la production industrielle à grande échelle. Les petits fours peuvent être utilisés pour des expériences à l'échelle du laboratoire et des études pilotes, tandis que les fours plus grands peuvent gérer une production en grande quantité pour des applications commerciales.
Avantages pour l'environnement
Les fours VIM présentent certains avantages pour l'environnement. L'environnement sous vide élimine le besoin d'agents fondants, ce qui réduit la production de déchets dangereux. En outre, l'absence de pollution de l'air et des scories pendant le processus de fusion contribue à une opération plus propre et plus respectueuse de l'environnement.
En conclusion, les fours de fusion par induction sous vide offrent de nombreux avantages pour la production de métaux et d'alliages purs et de haute qualité. L'environnement sous vide, l'atmosphère contrôlée, les vitesses de fusion et de refroidissement rapides, la consommation d'énergie réduite, l'évolutivité et les avantages environnementaux font des fours VIM un choix privilégié dans l'industrie métallurgique.
Applications des fours de fusion par induction sous vide
Les fours de fusion par induction sous vide (VIM) sont des outils polyvalents utilisés dans diverses industries, notamment l'aérospatiale, la médecine et l'automobile. Leur fonction principale consiste à traiter des alliages spécialisés, tels que les superalliages, les alliages de titane et les aciers inoxydables, pour lesquels des performances matérielles exceptionnelles sont primordiales.
Industrie aérospatiale
Les fours VIM jouent un rôle crucial dans l'industrie aérospatiale, où la production de composants de haute performance pour les avions, les missiles et les satellites exige l'utilisation d'alliages spécialisés. Ces fours permettent la fusion et le moulage précis de superalliages et d'aciers à haute résistance, dont beaucoup nécessitent un traitement sous vide en raison de la présence d'éléments réactifs tels que le titane, le niobium et l'aluminium.
Industrie médicale
Dans le domaine médical, les fours VIM sont utilisés pour produire des implants et des instruments chirurgicaux de haute qualité. La capacité à contrôler précisément le processus de fusion garantit la production d'alliages d'une pureté et de propriétés mécaniques optimales, qui sont essentielles pour assurer la sécurité et l'efficacité des dispositifs médicaux.
Industrie automobile
L'industrie automobile utilise les fours VIM pour fabriquer des composants de haute performance tels que des engrenages, des roulements et des pièces de moteur. Ces fours facilitent la production d'alliages présentant une dureté, une résistance à l'usure et une résistance à la fatigue accrues, qui sont cruciales pour la durabilité et la fiabilité des composants automobiles.
Autres applications
Au-delà de ces industries primaires, les fours VIM trouvent également des applications dans l'industrie nucléaire pour la fusion et le moulage de l'uranium métal faiblement enrichi en barres de combustible. Ils sont également utilisés dans la production de métaux tels que le titane et l'aluminium.
Avantages des fours VIM
L'utilisation de fours VIM présente plusieurs avantages par rapport aux techniques de fusion traditionnelles :
- Contrôle précis de la température : Les fours VIM permettent un contrôle précis de la température, ce qui est essentiel pour fondre et couler des alliages aux propriétés spécifiques.
- Environnement sous vide : L'environnement sous vide empêche la contamination du métal en fusion et garantit la production d'alliages d'une grande pureté.
- Amélioration des propriétés des matériaux : La combinaison d'un contrôle précis de la température et d'un environnement sous vide permet d'obtenir des alliages aux propriétés mécaniques améliorées, telles que la solidité, la ténacité et la résistance à la corrosion.
- Efficacité énergétique : Les fours VIM fonctionnent à des températures et des pressions plus basses que les techniques de fusion traditionnelles, ce qui permet de réaliser des économies d'énergie.
Conclusion
Les fours de fusion par induction sous vide sont des outils indispensables dans diverses industries, permettant la production d'alliages de haute performance aux propriétés matérielles exceptionnelles. Leur polyvalence et leur capacité à contrôler précisément le processus de fusion les rendent idéaux pour les applications où la qualité et la fiabilité sont primordiales.
Conclusion
Les fours de fusion par induction sous vide ont transformé le traitement des métaux, permettant la production d'alliages de haute pureté aux propriétés exceptionnelles. Leur capacité à contrôler les conditions de vide, à prévenir la contamination et à assurer une régulation précise de la température en fait des outils indispensables à la fabrication et à la recherche de pointe. En libérant le potentiel des matériaux spécialisés, les fours de fusion sous vide continuent à stimuler l'innovation et à repousser les limites de la science des matériaux.
CONTACTEZ-NOUS POUR UNE CONSULTATION GRATUITE
Les produits et services de KINTEK LAB SOLUTION ont été reconnus par des clients du monde entier. Notre personnel se fera un plaisir de répondre à toute demande que vous pourriez avoir. Contactez-nous pour une consultation gratuite et parlez à un spécialiste produit pour trouver la solution la plus adaptée aux besoins de votre application !