La calcination n'est généralement pas effectuée dans un haut fourneau.Elle est plutôt réalisée dans des fours spécialisés tels que les fours à réverbère ou les fours rotatifs, qui sont conçus pour fournir des conditions de chauffage contrôlées en dessous du point de fusion de la matière.La calcination consiste à chauffer des matériaux en l'absence ou en présence limitée d'air afin d'induire une décomposition thermique, d'éliminer les substances volatiles ou de provoquer des transitions de phase.Alors que le grillage à petite échelle, qui nécessite un minimum d'oxygène, peut avoir lieu dans un haut fourneau, la calcination est distincte et nécessite généralement un équipement différent.Le haut fourneau est plus communément associé aux processus de fusion, où des températures élevées et des réactions chimiques spécifiques sont utilisées pour extraire les métaux des minerais.
Explication des points clés :
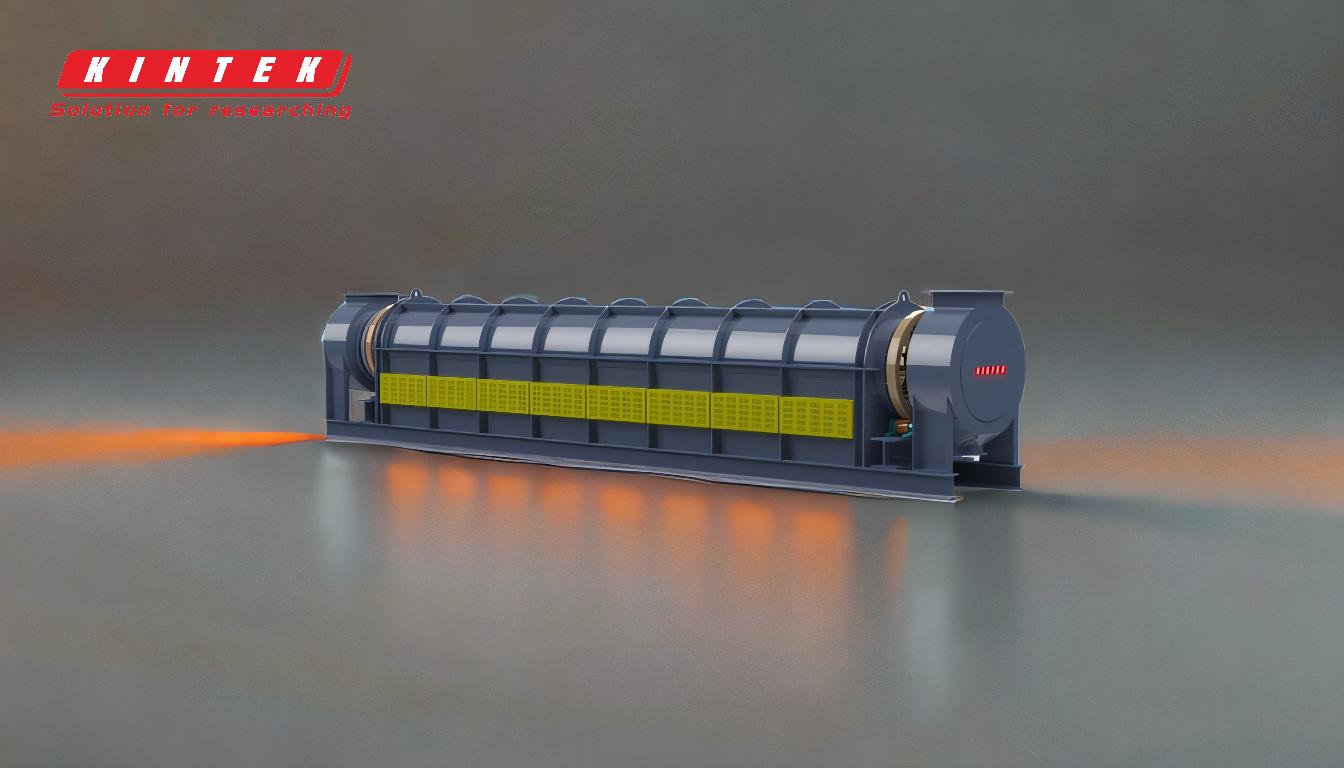
-
Définition de la calcination:
- La calcination est un processus de traitement thermique qui consiste à chauffer des matériaux solides, tels que des minerais, en dessous de leur point de fusion en l'absence ou en présence limitée d'air ou d'oxygène.Ce processus induit une décomposition thermique, élimine les fractions volatiles ou provoque des transitions de phase.
-
Équipement typique pour la calcination:
- La calcination est généralement réalisée dans des équipements spécialisés tels que fours à réverbère ou fours rotatifs .Ces fours sont conçus pour fournir des conditions de chauffage contrôlées et conviennent aux procédés nécessitant une régulation précise de la température.
- Les fours à réverbère, par exemple, ont une forme horizontale en "S" et peuvent fonctionner avec ou sans oxygène, en fonction des exigences spécifiques du procédé.
-
Haut fourneau et calcination:
- A Haut fourneau est principalement utilisé pour la fusion La fusion est un processus qui implique des températures élevées et des réactions chimiques pour extraire les métaux des minerais.Il n'est généralement pas utilisé pour la calcination.
- Si la torréfaction à petite échelle (un processus similaire à la calcination mais nécessitant un minimum d'oxygène) peut avoir lieu dans un haut-fourneau, la calcination elle-même est distincte et nécessite généralement un équipement différent.
-
Objectif de la calcination:
- Le but premier de la calcination est d'éliminer les impuretés volatiles ou d'induire une dissociation chimique dans les matériaux.Par exemple, dans la production de chaux à partir de calcaire, la calcination chasse le dioxyde de carbone, laissant la chaux sous forme de poudre.
-
Exemples de calcination:
- Un exemple classique de calcination est la conversion du calcaire (CaCO₃). calcaire (CaCO₃) à chaux (CaO) .Lorsque le calcaire est chauffé, il subit une décomposition thermique qui libère du dioxyde de carbone (CO₂) et forme de la chaux.
- D'autres matériaux, tels que la dolomie et la magnésite, sont également calcinés pour obtenir des propriétés chimiques ou physiques spécifiques.
-
Fours rotatifs pour la calcination:
- Les fours rotatifs sont couramment utilisés pour la calcination, en particulier pour les matériaux dont la taille des particules est inférieure ou égale à 60 mm.Ces fours assurent un chauffage uniforme et sont efficaces pour produire des produits de haute qualité et homogènes.
-
Contraste avec la torréfaction:
- Le grillage est un processus similaire, mais il consiste généralement à chauffer les minerais en présence d'un excès d'air ou d'oxygène.Il est souvent utilisé pour oxyder les minerais sulfurés, alors que la calcination se concentre sur la décomposition thermique ou l'élimination des substances volatiles.
-
Principales différences entre les procédés de calcination et de haut fourneau:
- La calcination est un processus de décomposition thermique qui se produit en dessous du point de fusion de la matière, tandis que les procédés de haut fourneau impliquent une fusion qui se produit à des températures beaucoup plus élevées et implique souvent une réduction chimique.
- La calcination est généralement effectuée dans des fours à réverbère ou fours rotatifs tandis que les hauts fourneaux sont utilisés pour production de fer et d'autres processus d'extraction de métaux.
En résumé, la calcination n'est pas effectuée dans un haut fourneau.Elle est réalisée dans un équipement spécialisé conçu pour un chauffage et une décomposition thermique contrôlés.Le haut fourneau est réservé à la fusion et à d'autres processus à haute température, ce qui le rend inadapté aux exigences précises de la calcination.
Tableau récapitulatif :
Point clé | Détails |
---|---|
Définition de la calcination | Décomposition thermique en dessous du point de fusion, souvent en l'absence d'air ou d'oxygène. |
Équipement typique | Fours à réverbère, fours rotatifs. |
Utilisation des hauts fourneaux | Principalement pour la fusion, pas pour la calcination. |
Objectif de la calcination | Éliminer les impuretés volatiles ou induire une dissociation chimique. |
Exemple | Conversion du calcaire (CaCO₃) en chaux (CaO). |
Fours rotatifs | Idéal pour le chauffage uniforme de matériaux ≤60 mm. |
Contraste avec la torréfaction | La torréfaction utilise un excès d'air ; la calcination se concentre sur la décomposition thermique. |
Vous avez besoin d'un four adapté à votre processus de calcination ? Contactez nos experts dès aujourd'hui pour trouver la solution idéale !