Bien qu'il s'agisse d'une technique d'assemblage très répandue, le brasage présente plusieurs inconvénients qui peuvent affecter la qualité, l'efficacité et le coût du processus.Ces inconvénients varient en fonction du type de méthode de brasage utilisée, comme le brasage sous vide ou le brasage manuel.Les principaux problèmes sont la réduction de la dureté des matériaux, les exigences techniques et de processus élevées, la consommation d'énergie, les longs délais de traitement et les défis liés à l'oxydation et aux résidus de flux.Il est essentiel de comprendre ces inconvénients pour quiconque envisage le brasage comme méthode d'assemblage, car ils peuvent avoir un impact sur les performances du produit final et sur l'ensemble du processus de production.
Explication des points clés :
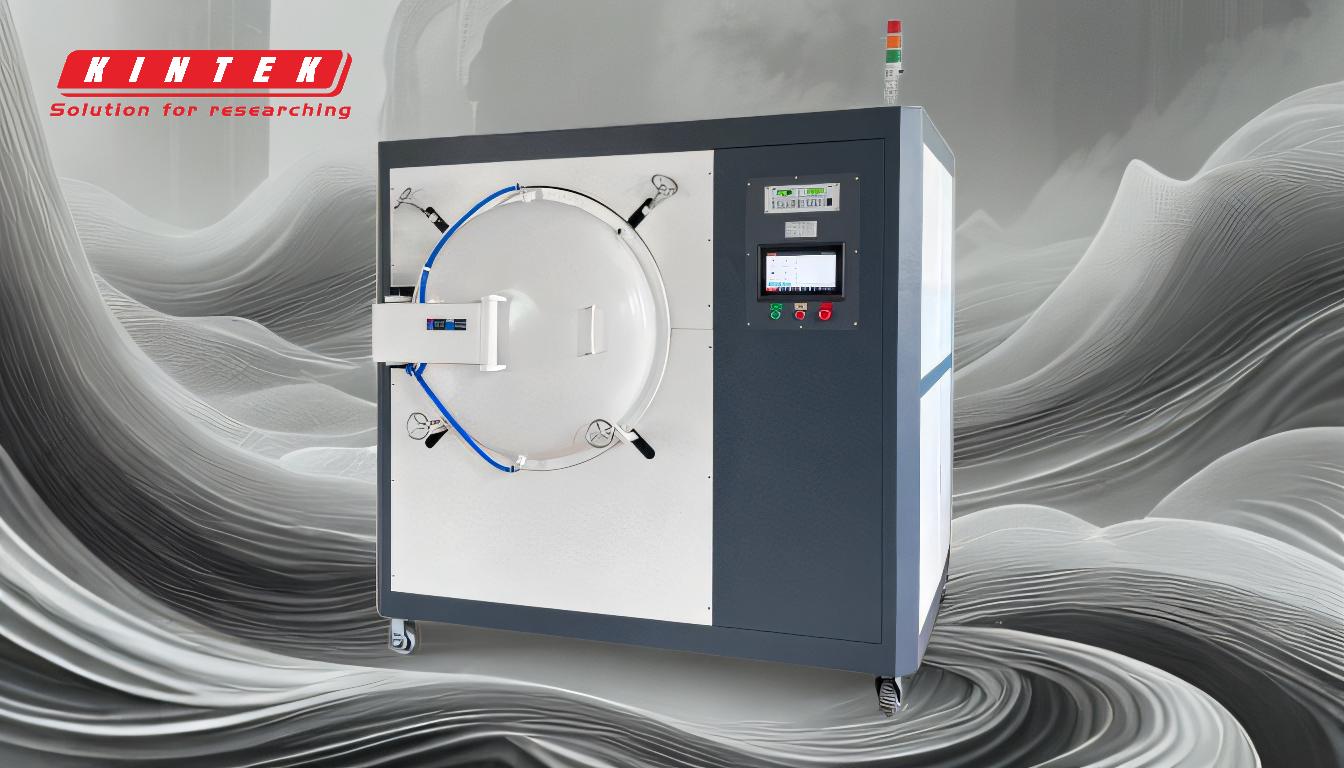
-
Réduction de la dureté du matériau après un soudage à haute température:
- Dans le brasage sous vide, les températures élevées requises pour faire fondre le matériau d'apport peuvent entraîner une réduction de la dureté du métal de base.Ceci est particulièrement problématique pour les matériaux dont l'intégrité structurelle ou la résistance à l'usure dépendent de leur dureté.Le ramollissement du matériau peut compromettre la résistance et la durabilité de l'assemblage, ce qui le rend moins adapté aux applications soumises à de fortes contraintes.
-
Exigences élevées en matière de processus et difficultés techniques:
- Le brasage, en particulier le brasage sous vide, exige un contrôle précis de la température, de l'atmosphère et de la mise en place du matériau d'apport.Cela nécessite un équipement spécialisé et des opérateurs qualifiés, ce qui augmente la complexité et le coût du processus.La nécessité d'un environnement contrôlé, tel qu'une atmosphère sous vide ou sous gaz inerte, ajoute aux défis techniques et limite l'accessibilité du procédé pour les petites entreprises.
-
Consommation d'énergie élevée:
- Le processus de brasage, en particulier le brasage sous vide, consomme une quantité importante d'énergie en raison de la nécessité de températures élevées et d'environnements contrôlés.Cela augmente non seulement les coûts d'exploitation, mais a également des répercussions sur l'environnement, ce qui le rend moins durable que d'autres méthodes d'assemblage.
-
Temps de traitement long:
- Le brasage nécessite souvent des cycles de chauffage et de refroidissement prolongés pour assurer la formation correcte des joints et éviter les contraintes thermiques.Cela peut entraîner des temps de production plus longs, réduisant le rendement et l'efficacité.Dans les secteurs où le temps est un facteur critique, cela peut constituer un inconvénient important.
-
Coûts élevés de nettoyage et de protection de l'environnement:
- Avant le brasage, les matériaux doivent souvent être soigneusement nettoyés pour éliminer les oxydes, les huiles et autres contaminants susceptibles de nuire à la qualité du joint.En outre, l'utilisation de flux dans certains procédés de brasage peut laisser des résidus qui nécessitent un nettoyage après le brasage.Ces étapes augmentent le coût global et la complexité du processus, et l'élimination des produits de nettoyage et des résidus de flux peut avoir des conséquences sur l'environnement.
-
Surchauffe et affaiblissement du métal de base dans le brasage manuel:
- Lorsque le brasage est effectué manuellement avec un chalumeau dans un environnement ouvert, il y a un risque de surchauffe du métal de base.Cela peut entraîner un affaiblissement et une oxydation localisés, ce qui donne un joint à la fois plus faible mécaniquement et moins attrayant visuellement.Le chauffage inégal peut également entraîner une déformation ou un gauchissement des composants.
-
Résidus d'oxydation et de flux:
- Dans le cas du brasage à l'air libre, l'oxydation du métal de base est un problème courant, qui peut affaiblir le joint et réduire sa qualité esthétique.Pour prévenir l'oxydation, on utilise souvent des flux, mais ceux-ci peuvent laisser des résidus difficiles à éliminer et provoquer des vides dans le joint.Ces vides peuvent agir comme des concentrateurs de contraintes, réduisant encore la résistance du joint.
En résumé, si le brasage offre plusieurs avantages, tels que la possibilité d'assembler des matériaux différents et de créer des joints solides et étanches, il présente également des inconvénients importants.Ceux-ci comprennent le ramollissement des matériaux, des exigences techniques et énergétiques élevées, des temps de traitement longs et des problèmes liés à l'oxydation et aux résidus de flux.Il est essentiel de comprendre ces inconvénients pour décider en connaissance de cause si le brasage est la bonne méthode d'assemblage pour une application donnée.
Tableau récapitulatif :
Inconvénient | Description |
---|---|
Dureté réduite des matériaux | Les températures élevées du brasage sous vide ramollissent le métal de base, ce qui réduit sa résistance. |
Exigences élevées en matière de processus | Nécessite un contrôle précis de la température, un équipement spécialisé et une main-d'œuvre qualifiée. |
Forte consommation d'énergie | Une consommation d'énergie importante augmente les coûts et l'impact sur l'environnement. |
Longue durée de traitement | Les cycles de chauffage et de refroidissement prolongés réduisent l'efficacité de la production. |
Coûts de nettoyage et coûts environnementaux élevés | Le nettoyage avant et après le brasage augmente la complexité et les coûts. |
Surchauffe dans le brasage manuel | Le brasage manuel au chalumeau risque d'affaiblir et de déformer le métal de base. |
Oxydation et résidus de flux | Le brasage à l'air libre provoque l'oxydation ; les résidus de flux affaiblissent les joints. |
Vous avez besoin d'aide pour déterminer si le brasage convient à votre application ? Contactez nos experts dès aujourd'hui pour des conseils sur mesure !