Le dépôt physique en phase vapeur (PVD) est une technique très efficace pour protéger les produits métalliques contre la corrosion.Elle consiste à déposer un revêtement mince, durable et résistant à la corrosion sur un substrat dans des conditions de vide.Les revêtements PVD améliorent la durée de vie, la durabilité et les performances des matériaux en améliorant des propriétés telles que la résistance à l'usure, la résistance à l'oxydation et la dureté.Contrairement à d'autres méthodes de revêtement telles que la galvanoplastie ou le dépôt chimique en phase vapeur (CVD), le dépôt en phase vapeur utilise des matériaux à l'état solide, ce qui le rend plus respectueux de l'environnement et lui permet de produire des revêtements présentant une meilleure tolérance à la corrosion.Cette technique est largement utilisée dans des secteurs tels que l'aérospatiale, le biomédical, la fabrication de semi-conducteurs et les revêtements décoratifs, où la résistance à la corrosion et la longévité des matériaux sont essentielles.
Explication des principaux points :
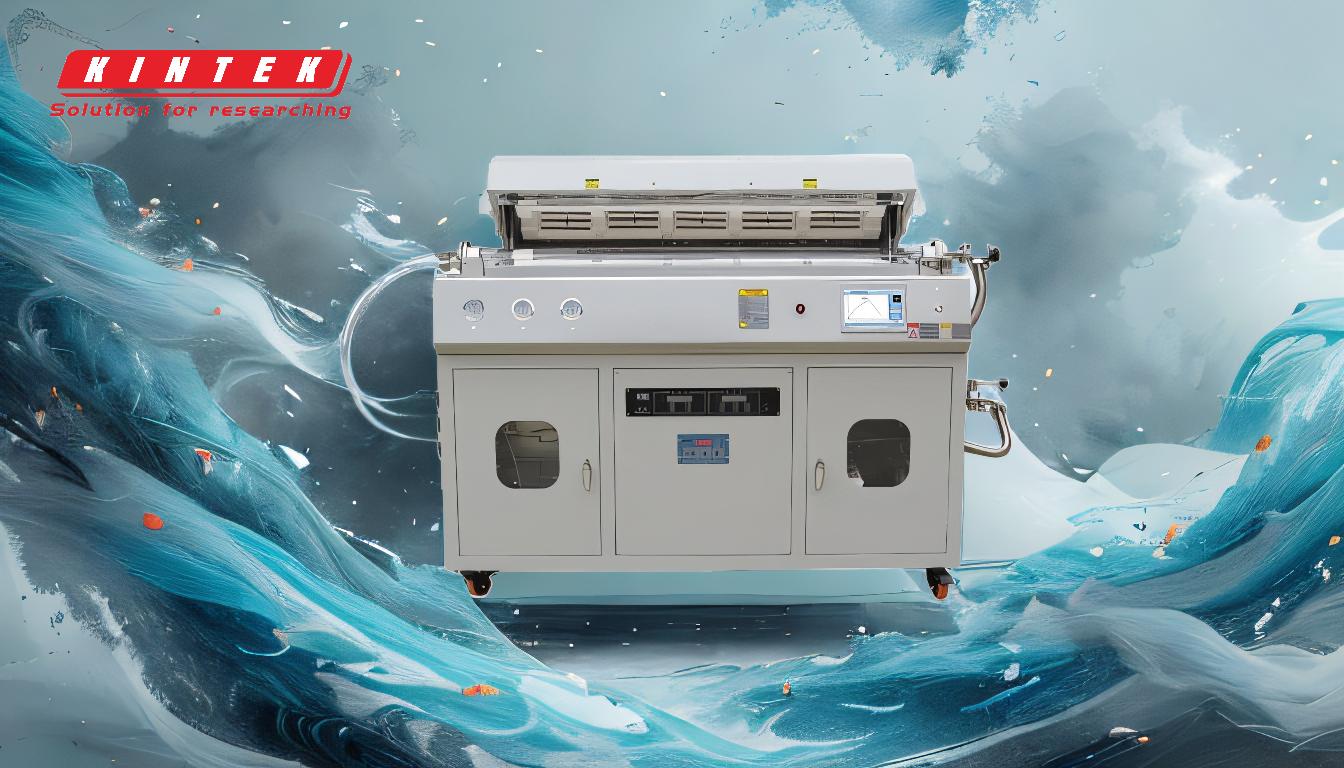
-
Qu'est-ce que le dépôt en phase vapeur (PVD) ?
- Le dépôt physique en phase vapeur (PVD) est un procédé de revêtement sous vide dans lequel des matériaux à l'état solide sont vaporisés et déposés sur un substrat pour former une fine couche protectrice.
- Il est utilisé pour améliorer les propriétés des matériaux, notamment la résistance à la corrosion, la résistance à l'usure, la résistance à l'oxydation et la dureté.
- Contrairement au dépôt chimique en phase vapeur (CVD), qui utilise des précurseurs gazeux, le dépôt en phase vapeur s'appuie sur des matériaux solides, ce qui le rend plus respectueux de l'environnement et plus polyvalent.
-
Comment le dépôt en phase vapeur (PVD) assure-t-il la protection contre la corrosion ?
- Les revêtements PVD créent une barrière entre le matériau du substrat et l'environnement extérieur, empêchant tout contact direct avec des agents corrosifs tels que l'humidité, les produits chimiques ou l'oxygène.
- Les revêtements sont très denses et uniformes, ce qui garantit une couverture complète et un minimum de défauts susceptibles de déclencher la corrosion.
- Les matériaux couramment utilisés dans le procédé PVD pour la protection contre la corrosion comprennent le nitrure de titane (TiN), le nitrure de chrome (CrN) et les revêtements à base d'aluminium, qui sont intrinsèquement résistants à l'oxydation et aux attaques chimiques.
-
Avantages du dépôt en phase vapeur pour la protection contre la corrosion :
- Tolérance supérieure à la corrosion : Les revêtements PVD offrent une meilleure résistance à la corrosion que les méthodes traditionnelles telles que la galvanoplastie, ce qui les rend idéaux pour les environnements difficiles.
- Durabilité : Les revêtements sont extrêmement durs et résistants à l'usure, ce qui garantit une protection à long terme, même en cas de contraintes mécaniques.
- Avantages pour l'environnement : Le dépôt en phase vapeur est un procédé propre qui produit peu de déchets et ne fait pas appel à des produits chimiques dangereux, contrairement à la galvanoplastie.
- Polyvalence : Le dépôt en phase vapeur peut être appliqué à une large gamme de matériaux, y compris les métaux, les céramiques et les polymères, ce qui le rend adapté à diverses applications.
-
Applications du dépôt en phase vapeur dans la protection contre la corrosion :
- Industrie aérospatiale : Les revêtements PVD sont utilisés sur les composants des avions pour les protéger contre la corrosion causée par l'exposition à des températures extrêmes, à l'humidité et à l'eau salée.
- Domaine biomédical : Les implants et les outils chirurgicaux sont revêtus de PVD pour prévenir la corrosion et améliorer la biocompatibilité.
- Outils de coupe : Les outils revêtus de PVD (par exemple, le nitrure de titane) présentent une résistance accrue à l'usure et à la corrosion, ce qui prolonge leur durée de vie dans les applications de travail des métaux.
- Revêtements décoratifs : La bijouterie et l'horlogerie utilisent les revêtements PVD pour assurer à la fois l'esthétique et la résistance à la corrosion.
- Appareils à semi-conducteurs : Le dépôt en phase vapeur est utilisé pour déposer des couches résistantes à la corrosion sur les composants semi-conducteurs, ce qui garantit la fiabilité des applications électroniques.
-
Comparaison avec d'autres techniques de revêtement :
- Placage électrolytique : Le dépôt en phase vapeur offre une meilleure adhérence, une meilleure uniformité et une meilleure résistance à la corrosion que la galvanoplastie, qui peut produire des revêtements poreux sujets à la corrosion.
- Dépôt chimique en phase vapeur (CVD) : Le dépôt en phase vapeur (CVD) offre une excellente qualité de revêtement, mais il nécessite des températures élevées et des précurseurs gazeux, ce qui le rend moins adapté aux matériaux sensibles à la température.Le dépôt en phase vapeur (PVD), en revanche, fonctionne à des températures plus basses et utilise des matériaux solides, ce qui le rend plus polyvalent.
-
Processus de revêtement PVD :
- Environnement sous vide : Le processus se déroule dans une chambre à vide afin d'éviter toute contamination et de garantir des revêtements de haute qualité.
- Vaporisation : Le matériau de revêtement (cible) est vaporisé à l'aide de techniques telles que la pulvérisation cathodique, l'évaporation ou la vaporisation à l'arc.
- Dépôt : Le matériau vaporisé se condense sur le substrat, formant une couche fine et uniforme.
- Post-traitement : Certains revêtements PVD peuvent subir des traitements supplémentaires (par exemple, un recuit) pour améliorer encore leurs propriétés.
-
Matériaux utilisés dans les revêtements PVD pour la protection contre la corrosion :
- Nitrure de titane (TiN) : Il offre une excellente dureté et une résistance à la corrosion. Il est couramment utilisé dans les outils de coupe et les revêtements décoratifs.
- Nitrure de chrome (CrN) : Connu pour sa grande résistance à l'oxydation et sa durabilité, il est idéal pour les applications aérospatiales et biomédicales.
- Revêtements à base d'aluminium : Ils offrent une résistance supérieure à la corrosion et sont souvent utilisés dans les secteurs de la marine et de l'automobile.
-
Défis et considérations :
- Coût : L'équipement et les procédés PVD peuvent être coûteux, ce qui les rend moins adaptés aux applications à faible coût.
- Complexité : Le processus nécessite un contrôle précis de paramètres tels que la température, la pression et la vitesse de dépôt pour obtenir des résultats optimaux.
- Compatibilité du substrat : Tous les matériaux ne conviennent pas au revêtement PVD, et la préparation de la surface est essentielle pour garantir l'adhérence et les performances.
En tirant parti des avantages uniques du PVD, les industries peuvent améliorer de manière significative la résistance à la corrosion et la longévité de leurs produits, garantissant ainsi leur fiabilité et leur performance dans des environnements exigeants.
Tableau récapitulatif :
Aspect | Détails |
---|---|
Procédé | Revêtement sous vide à l'aide de matériaux à l'état solide |
Principaux avantages | Résistance supérieure à la corrosion, durabilité, respect de l'environnement |
Matériaux courants | Nitrure de titane (TiN), nitrure de chrome (CrN), revêtements à base d'aluminium |
Applications | Aérospatiale, biomédical, outils de coupe, revêtements décoratifs, semi-conducteurs |
Comparaison avec d'autres procédés | Meilleure adhérence et meilleure résistance à la corrosion que la galvanoplastie et le dépôt en phase vapeur (CVD) |
Défis | Coût élevé, complexité du processus, compatibilité des substrats |
Vous souhaitez améliorer la résistance à la corrosion de votre produit ? Contactez nous dès aujourd'hui pour en savoir plus sur les solutions PVD !