Introduction aux fours sous vide pour le molybdène
Les fours sous vide au molybdènesont essentiels dans les applications à haute température, car ils tirent parti des propriétés uniques du molybdène pour exceller dans des environnements exigeants. Ces systèmes avancés sont non seulement essentiels pour le frittage sous atmosphère à haute température, mais aussi pour le frittage sous vide de divers matériaux, ce qui démontre leur polyvalence et leur rôle essentiel dans les processus industriels modernes. Cet article se penche sur les caractéristiques complexes, la construction et les applications des fours à vide au molybdène, et donne un aperçu de leurs systèmes de contrôle avancés et de leurs stratégies de maintenance, essentiels pour garantir des performances optimales et une longue durée de vie.
Principales caractéristiques et objectifs des fours sous vide au molybdène
Les fours à vide pour le molybdène sont des équipements spécialisés conçus pour le traitement à haute température dans un environnement contrôlé et sous vide. Ces fours sont particulièrement réputés pour leur utilisation dans le frittage sous atmosphère à haute température et le frittage sous vide de divers matériaux, notamment les céramiques, les métaux et les composites. Les propriétés uniques du molybdène, telles que son point de fusion élevé, son excellente conductivité thermique et sa résistance aux chocs thermiques, en font un matériau idéal pour les éléments chauffants de ces fours.
Stabilité à haute température et efficacité
L'une des principales caractéristiques des fours sous vide au molybdène est leur capacité à maintenir une stabilité à haute température. Le molybdène peut fonctionner à des températures allant jusqu'à 1700°C, ce qui est crucial pour des processus tels que le frittage où un contrôle précis de la température est essentiel. La conductivité thermique élevée du molybdène garantit un transfert de chaleur efficace, permettant un chauffage rapide et une distribution uniforme de la température dans la chambre du four. Cette efficacité est particulièrement importante dans les applications industrielles où le temps et les coûts énergétiques sont des facteurs significatifs.
Performance du vide et contrôle de la contamination
Les fours à vide au molybdène sont conçus pour fonctionner sous vide ou dans une atmosphère contrôlée, ce qui est essentiel pour éviter la contamination des matériaux traités. L'environnement sous vide élimine la présence d'oxygène et d'autres gaz qui pourraient réagir avec les matériaux à haute température, préservant ainsi leur pureté et leur intégrité. Cette caractéristique est particulièrement utile pour le traitement des matériaux de haute pureté et dans les applications où les niveaux de contamination à l'état de traces doivent être maintenus à un minimum.
Polyvalence des applications
La polyvalence des fours sous vide au molybdène s'étend à une large gamme d'applications au-delà du frittage. Il s'agit notamment du traitement thermique, du brasage, du recuit et du traitement de matériaux avancés tels que les céramiques transparentes et les composites à matrice métallique. Chacune de ces applications bénéficie du contrôle précis de la température et de l'environnement sans contamination fourni par le four.
Composants structurels et conception
La conception d'un four sous vide au molybdène intègre plusieurs composants clés qui garantissent sa fonctionnalité et son efficacité. Il s'agit notamment des éléments suivants
- Corps et couvercle du four: Construits en acier inoxydable de haute qualité, le corps et le couvercle du four sont conçus pour maintenir un vide élevé et sont souvent refroidis à l'eau pour supporter les températures élevées.
- Éléments chauffants: Fabriqués en molybdène de haute pureté, ces éléments sont essentiels pour atteindre et maintenir les températures requises.
- Écrans d'isolation: Ils sont utilisés pour minimiser les pertes de chaleur et assurer une distribution uniforme de la température dans la chambre du four.
- Système de vide: Composé de pompes, de vannes et de jauges, le système de vide est essentiel pour maintenir l'environnement sous vide et contrôler l'atmosphère à l'intérieur du four.
- Système de contrôle: Des systèmes de contrôle avancés, comprenant souvent des interfaces PLC et informatiques, permettent un contrôle précis des paramètres du four, garantissant la reproductibilité et la sécurité de l'opération.
Entretien et précautions
Si les fours à vide pour le molybdène offrent de nombreux avantages, ils nécessitent également un entretien et un fonctionnement soigneux pour garantir leur longévité et leurs performances. Le molybdène étant sensible à l'oxydation et à la contamination, les fours doivent être utilisés dans des conditions strictement contrôlées. Un entretien régulier, comprenant l'inspection et le remplacement des éléments chauffants et des joints, est essentiel pour prévenir les défaillances et garantir que le four fonctionne avec une efficacité maximale.
En conclusion, les fours à vide en molybdène sont des outils indispensables pour le traitement à haute température, car ils offrent une stabilité à haute température, un transfert de chaleur efficace et un environnement sans contamination. Leur polyvalence et leur précision en font un élément clé de l'avancement de la science des matériaux et des technologies de traitement industriel.
Construction et composition des fours à vide au molybdène
Les fours à vide pour le molybdène sont des équipements sophistiqués conçus pour des applications à haute température sous vide ou dans des atmosphères contrôlées. Ces fours sont essentiels pour des processus tels que le frittage, le traitement thermique et le brasage, où le maintien d'un environnement parfait est essentiel. La construction de ces fours fait appel à plusieurs composants clés, chacun étant conçu pour fonctionner parfaitement dans des conditions extrêmes.
Composants structurels
Corps et couvercle du four : Le corps du four est généralement fabriqué en acier inoxydable, connu pour sa résistance à la corrosion et à la déformation à haute température. Les enveloppes intérieure et extérieure sont souvent en acier inoxydable 304, la surface extérieure étant polie miroir pour améliorer la durabilité et l'esthétique. Le couvercle, qui est amovible, comprend un mécanisme de refroidissement à l'eau dans sa partie centrale pour éviter la surchauffe et assurer l'étanchéité de la fermeture.
Fond et système de vide : Le fond du four, semblable au couvercle, comprend un système de refroidissement par eau et des orifices pour les électrodes, les thermocouples et d'autres instruments de contrôle. Le système de vide fait partie intégrante du fonctionnement du four et se compose d'une combinaison de pompes à vide, de vannes et de jauges. Ces composants travaillent ensemble pour atteindre et maintenir les niveaux de vide nécessaires, essentiels pour empêcher l'oxydation et la contamination des matériaux traités.
Éléments chauffants et écran isolant : Le cœur du four réside dans ses éléments chauffants, souvent fabriqués en molybdène de haute pureté. Le molybdène est choisi pour son excellente résistance aux températures élevées et sa capacité à maintenir l'intégrité structurelle jusqu'à 1700°C. Les éléments chauffants sont conçus pour fonctionner à des densités de puissance élevées, ce qui garantit un chauffage rapide et uniforme. L'écran isolant, généralement fabriqué à partir de matériaux tels que le tungstène et l'acier inoxydable, permet de maintenir la température à l'intérieur du four et de réduire les pertes de chaleur.
Considérations opérationnelles
Systèmes de manutention et de contrôle : Les fours à vide pour le molybdène sont équipés de systèmes de contrôle avancés qui permettent une gestion précise de la température et un contrôle du processus. Ces systèmes peuvent être automatisés, à l'aide d'interfaces PLC et d'écrans tactiles, ce qui permet aux opérateurs de surveiller et d'ajuster les paramètres en temps réel. L'intégration d'un contrôle informatisé permet non seulement d'améliorer l'efficacité, mais aussi de garantir la répétabilité et la sécurité des procédés à haute température.
Refroidissement et sécurité : Compte tenu des températures de fonctionnement élevées, les systèmes de refroidissement sont cruciaux pour la longévité des composants du four. Des enveloppes refroidies à l'eau autour du corps, du couvercle et du fond du four permettent de dissiper la chaleur et d'éviter les dommages structurels. Des dispositifs de sécurité tels que des soupapes de décharge et des fonctions d'arrêt d'urgence sont également intégrés pour protéger à la fois l'équipement et les opérateurs.
Applications et avantages
Les fours sous vide au molybdène sont des outils polyvalents, utilisés dans diverses industries, notamment la métallurgie, la céramique et l'électronique. Leur capacité à fonctionner sous vide ou sous atmosphère contrôlée les rend idéaux pour les procédés qui exigent une grande pureté et une contamination minimale. L'utilisation d'éléments chauffants en molybdène garantit un chauffage efficace et fiable, ce qui contribue à la qualité globale et à la cohérence des produits finis.
En conclusion, la construction et la composition des fours à vide en molybdène sont méticuleusement conçues pour répondre aux exigences des applications à haute température et à haute pureté. Chaque composant, du corps du four aux éléments chauffants, joue un rôle essentiel dans le fonctionnement efficace et sûr du four, ce qui en fait un outil indispensable dans les environnements de fabrication et de recherche de pointe.
Systèmes de contrôle des fours à vide au molybdène
Les fours à vide au molybdène font partie intégrante du traitement à haute température et de la synthèse des matériaux, et utilisent des systèmes de contrôle avancés pour garantir la précision et l'efficacité. Ces systèmes de contrôle, qui comprennent des systèmes de contrôle automatique par ordinateur et des systèmes d'automates programmables (PLC), sont essentiels à la gestion de processus complexes et au maintien d'un fonctionnement optimal des fours.
Systèmes de contrôle automatique par ordinateur
Les systèmes de commande automatique par ordinateur des fours à vide de molybdène sont conçus pour gérer des fonctions de commande logique complexes, la surveillance continue des paramètres du procédé et la gestion des données. Ces systèmes utilisent du matériel et des logiciels informatiques dédiés pour superviser des opérations telles que les taux de refusion, le contrôle de l'écart entre les arcs et l'acquisition de données. Un PC d'interface opérateur (OIP) sert d'interface principale entre l'opérateur et le processus du four, fournissant une visualisation du processus en temps réel, des ajustements de paramètres et une gestion des recettes. L'OIP peut également être équipé d'une interface réseau Ethernet pour un transfert transparent des données vers d'autres ordinateurs en réseau, ce qui améliore l'intégration du système et l'accessibilité des données.
Contrôleurs logiques programmables (PLC)
Les automates programmables ont révolutionné le contrôle des fours sous vide en remplaçant les systèmes traditionnels à relais par des commandes numériques plus fiables et plus efficaces. Introduits à l'origine pour simplifier la gestion de plusieurs instruments de contrôle, les automates programmables sont aujourd'hui indispensables dans les systèmes modernes de fours sous vide. Ils réduisent l'intervention de l'opérateur, garantissent une qualité constante du produit et minimisent les temps d'arrêt du four. Dans les fours sous vide de molybdène contemporains, les API sont généralement intégrés à des interfaces à écran tactile, ce qui permet aux opérateurs de charger et de décharger le four, de sélectionner des recettes de processus et de lancer des opérations d'une simple pression sur un bouton.
Caractéristiques et avantages des systèmes de contrôle
L'intégration de systèmes de contrôle avancés dans les fours à vide de molybdène offre plusieurs avantages clés :
-
Précision et cohérence: Les systèmes de contrôle avancés permettent des ajustements précis des paramètres du four, garantissant une distribution uniforme de la chaleur et des résultats de traitement cohérents. Cette précision est cruciale pour les applications de grande valeur où les propriétés des matériaux doivent être étroitement contrôlées.
-
Efficacité énergétique: Les systèmes de contrôle modernes optimisent l'utilisation de l'énergie en ajustant dynamiquement les cycles de chauffage et les taux de refroidissement sur la base de données en temps réel. Cela permet non seulement de réduire les coûts d'exploitation, mais aussi de minimiser l'impact sur l'environnement.
-
Surveillance et contrôle à distance: Avec la possibilité de fonctionner à distance, ces systèmes améliorent la flexibilité et la sécurité de l'exploitation. L'accès à distance permet une surveillance et des ajustements en temps réel, ce qui réduit le besoin de personnel sur place pendant les phases critiques de l'exploitation.
-
Gestion et analyse des données: Les systèmes de contrôle avancés facilitent l'enregistrement et l'analyse de données complètes, ce qui est essentiel pour l'amélioration des processus et le respect des normes de qualité. Les données historiques peuvent être utilisées pour affiner les processus et résoudre les problèmes de manière proactive.
-
Sécurité renforcée: Les systèmes de contrôle automatisés comprennent des protocoles de sécurité qui évitent les erreurs de l'opérateur et protègent contre les dysfonctionnements de l'équipement. Cela est particulièrement important dans les environnements à haute température et sous vide, où les risques de sécurité sont élevés.
Applications et tendances futures
Les fours à vide de molybdène équipés de systèmes de contrôle avancés sont utilisés dans diverses applications à haute température, notamment pour le frittage, le traitement thermique et la synthèse de matériaux. Au fur et à mesure que la technologie progresse, les tendances futures en matière de systèmes de contrôle se concentreront probablement sur une intégration plus poussée de l'intelligence artificielle et des algorithmes d'apprentissage automatique afin de prévoir et d'optimiser les performances du four, d'améliorer la maintenance prédictive et d'accroître l'efficacité globale du processus.
En conclusion, les systèmes de contrôle avancés des fours à vide de molybdène représentent un bond en avant significatif en termes de précision, d'efficacité et de sécurité. Ces systèmes sont essentiels pour répondre aux exigences rigoureuses du traitement moderne à haute température et de la synthèse des matériaux, garantissant que les fours sous vide à molybdène restent à l'avant-garde des technologies de fabrication avancées.
Propriétés des matériaux et performances des éléments chauffants en molybdène
Le molybdène, métal réfractaire connu pour sa résistance aux températures élevées et son excellente conductivité électrique, est largement utilisé dans divers éléments chauffants dans l'industrie et les laboratoires. Sa capacité à maintenir l'intégrité structurelle et les performances à des températures extrêmes en fait un choix privilégié pour les applications exigeant durabilité et fiabilité.
Propriétés matérielles du molybdène
Le molybdène présente plusieurs propriétés clés qui le rendent adapté aux éléments chauffants :
- Point de fusion élevé: Le molybdène a un point de fusion d'environ 2623°C (4753°F), ce qui est nettement plus élevé que de nombreux autres métaux. Ce point de fusion élevé permet aux éléments chauffants en molybdène de fonctionner à des températures allant jusqu'à 1700°C (3100°F) sans défaillance structurelle.
- Bonne conductivité électrique: Le molybdène est un très bon conducteur d'électricité, ce qui est essentiel pour une production de chaleur efficace dans les éléments chauffants.
- Résistance au fluage: À haute température, le molybdène présente une déformation minimale dans le temps, connue sous le nom de résistance au fluage. Cette propriété garantit que les éléments chauffants conservent leur forme et leurs performances en cas d'exposition prolongée à des températures élevées.
- Faible dilatation thermique: Le molybdène a un coefficient de dilatation thermique relativement faible, ce qui permet de réduire les contraintes et les déformations lors des cycles de chauffage et de refroidissement rapides.
Performance dans les environnements à haute température
Dans les environnements à haute température, les éléments chauffants en molybdène présentent des performances exceptionnelles :
- Résistance à l'oxydation: Le molybdène forme une couche protectrice de trioxyde de molybdène (MoO3) lorsqu'il est exposé à des températures élevées dans des atmosphères oxydantes. Cette couche empêche l'oxydation et prolonge la durée de vie des éléments chauffants.
- Résistance et durabilité: Malgré son fonctionnement à haute température, le molybdène conserve sa résistance et ne devient pas cassant à moins d'être exposé à des températures supérieures à 1700°C (3100°F). Cela permet aux éléments chauffants de résister aux contraintes mécaniques et aux chocs thermiques.
- Distribution efficace de la chaleur: La bonne conductivité thermique du molybdène assure une distribution uniforme de la chaleur, ce qui est essentiel pour un chauffage homogène dans les fours industriels et de laboratoire.
Effets d'alliage sur le molybdène
L'alliage du molybdène avec d'autres éléments améliore ses propriétés et élargit son champ d'action :
- Alliage TZM: L'ajout de titane et de zirconium au molybdène forme l'alliage TZM, qui présente une résistance accrue, une température de recristallisation plus élevée et une meilleure résistance au fluage. Le TZM peut fonctionner à des températures d'éléments allant jusqu'à 1400°C (2552°F).
- Molybdène lanthané (MoLa): L'incorporation de trioxyde de lanthane dans le molybdène permet d'obtenir une fine structure de grains en "fibres empilées" qui améliore considérablement la résistance à la recristallisation et au gauchissement à haute température. Le MoLa peut être utilisé à des températures d'éléments allant jusqu'à 2000°C (3632°F).
- Disiliciure de molybdène (MoSi2): Ce composé offre une faible résistivité, des caractéristiques de résistance-température positives et une excellente résistance à l'oxydation à haute température. Les éléments chauffants en MoSi2 peuvent fonctionner avec des charges en watts très élevées et maintenir des performances constantes tout au long de leur durée de vie.
Applications des éléments chauffants en molybdène
Les éléments chauffants en molybdène sont largement utilisés dans diverses applications, notamment dans les domaines suivants
- Fours à vide: En raison de sa résistance à l'oxydation et de son point de fusion élevé, le molybdène est idéal pour les fours à vide utilisés dans les processus de traitement thermique tels que la trempe et le brasage.
- Fours industriels et de laboratoire: La capacité du molybdène à résister à des températures élevées et à une distribution uniforme de la chaleur le rend adapté à une large gamme de fours industriels et de laboratoire.
- Environnements d'oxydation à haute température: La formation d'une couche d'oxyde protectrice sur les éléments chauffants en molybdène assure leur longévité et leur fiabilité dans les atmosphères oxydantes à haute température.
En conclusion, le molybdène et ses alliages sont des matériaux essentiels pour les éléments chauffants en raison de leurs performances exceptionnelles à haute température, de leur résistance et de leur durabilité. Grâce à une sélection et à un alliage minutieux, ces matériaux peuvent être adaptés pour répondre aux exigences spécifiques de diverses applications industrielles et de laboratoire, garantissant ainsi des processus de chauffage efficaces et fiables.
Maintenance et performances à long terme des fours à vide au molybdène
Le maintien des performances à long terme des fours à vide au molybdène est crucial pour assurer un fonctionnement cohérent et fiable. Ces fours sont conçus pour fonctionner dans des conditions extrêmes, et un entretien adéquat peut prévenir des problèmes tels que le durcissement, l'effondrement et la perte de résistance des éléments chauffants à haute température. Voici des directives détaillées pour vous aider à préserver l'intégrité et l'efficacité de votre four sous vide au molybdène.
Entretien des éléments chauffants
Les éléments chauffants en molybdène sont des composants essentiels des fours sous vide. Ils doivent être entretenus avec soin pour éviter tout dommage et garantir leur longévité. Après chaque utilisation, inspectez les éléments chauffants pour détecter tout signe de dommage. Vérifiez que les connexions sont bien serrées afin d'éviter tout problème électrique. Si un élément chauffant est endommagé, il peut être possible de le réparer. Les éléments en molybdène peuvent généralement être réparés jusqu'à trois fois par bande d'éléments, mais cela nécessite des précautions particulières en raison de la fragilité du molybdène et de la libération potentielle de vapeurs toxiques de dioxyde de molybdène au cours du processus de réparation.
Conditionnement des nouveaux éléments chauffants
Les nouveaux éléments chauffants en molybdène doivent être conditionnés pour améliorer leurs performances et leur longévité. Il s'agit de chauffer le four vide à 1550°C et de le maintenir à cette température pendant une heure. Ce processus permet d'appliquer une fine couche de verre protectrice sur les éléments, ce qui peut empêcher une dégradation prématurée. Si le four doit fonctionner pendant de longues périodes à des températures inférieures à 800°C, reconditionnez les surfaces en utilisant la procédure de cuisson initiale afin de préserver leur intégrité.
Contrôle de la vitesse de chauffe
La vitesse de chauffage est un facteur critique pour le maintien de l'intégrité structurelle des éléments chauffants. Un chauffage rapide peut entraîner une dilatation thermique et une déformation de l'écran thermique. Il est recommandé d'utiliser une vitesse de chauffage lente, en particulier dans la phase de haute température. Par exemple, la réduction de la vitesse de rampe pour des températures de 100 à 200°C en dessous de la température nominale maximale du four à 60-100°C par heure peut éviter des contraintes excessives sur les éléments chauffants.
Contrôles du vide et des fuites
Avant de lancer le processus de chauffage, il est essentiel de vérifier le taux de fuite du vide et le degré de vide final. Il est essentiel de garantir un environnement de vide adéquat pour le bon fonctionnement du four. Lorsque l'équipement n'est pas utilisé, il doit être stocké sous vide. Si le four contient des substances volatiles, il doit être séché pour éviter toute contamination et tout dommage potentiel aux éléments chauffants.
Manipulation des produits et contrôle des impuretés
Lors de la manipulation des produits, veillez à ne pas les faire tomber sur la surface des éléments chauffants en molybdène, car cela pourrait les endommager. Les produits contenant des éléments en fer dont le point de fusion est plus bas ne doivent pas se volatiliser sur la bande de molybdène dans le four, car cela peut entraîner une fusion au fil du temps. Tenez fermement les produits avec les deux mains ou utilisez des objets mécaniques pour éviter les chutes accidentelles. En outre, contrôlez strictement la teneur en impuretés des produits afin d'éviter la contamination des éléments chauffants.
Connexions électriques et systèmes de refroidissement
La connexion électrique aux éléments chauffants s'effectue généralement par l'intermédiaire d'une traversée refroidie à l'eau. Cette connexion étanche contient le conducteur qui achemine le courant vers l'élément chauffant. Les traversées sont disponibles en différentes intensités, y compris des modèles à haute capacité. Le refroidissement par eau empêche la surchauffe et il est essentiel d'utiliser un système de refroidissement en boucle fermée, mis à la terre, avec des liquides de refroidissement non conducteurs tels que l'eau déionisée ou l'éthylène glycol. Les conduites de refroidissement doivent être fabriquées dans des matériaux non conducteurs, tels que des tubes en polypropylène, afin d'éviter que le liquide de refroidissement ne s'intègre au circuit.
Conception d'éléments chauffants résistants
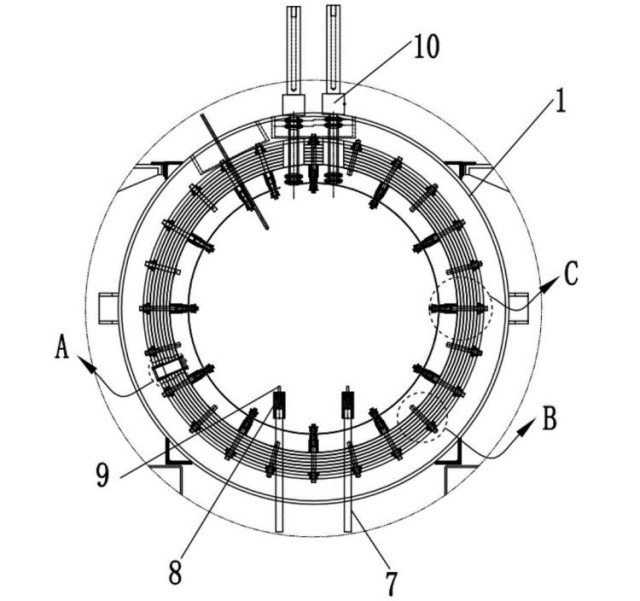
Pour s'assurer que le fil chauffant du four à vide conserve la résistance nécessaire à des températures élevées et évite le durcissement, l'effondrement ou l'affaissement, la taille de construction du fil chauffant doit être soigneusement conçue. Il faut notamment utiliser un fil de résistance en spirale et prêter attention au diamètre de courbure, au pas et au diamètre médian de l'élément chauffant. Le corps chauffant doit être fixé contre le revêtement isolant du four à vide, avec 95 pièces de céramique placées dans le revêtement isolant pour fournir un espace de dilatation approprié. Pendant l'utilisation, positionnez les éléments chauffants de manière appropriée, généralement à des intervalles de 100 à 200 mm, et accrochez-les solidement pour éviter que le fil de résistance ne reste à plat. En outre, évitez tout contact direct entre les fils du four afin de prévenir les courts-circuits, généralement en utilisant des feuilles d'isolation.
En suivant ces directives complètes de maintenance et de conception, vous pouvez garantir les performances et la fiabilité à long terme de votre four sous vide à molybdène, en prolongeant sa durée de vie et en maintenant une efficacité opérationnelle optimale.
Applications des fours sous vide au molybdène dans l'industrie
Les fours sous vide au molybdène jouent un rôle crucial dans divers secteurs industriels en raison de leur capacité à fonctionner à des températures élevées et dans des conditions de vide, assurant un contrôle précis du processus de chauffage sans oxydation ni contamination. Cette section explore les diverses applications des fours sous vide au molybdène dans des industries telles que la céramique, la métallurgie, l'électronique et les traitements de matériaux spéciaux.
Industrie de la céramique
Dans l'industrie de la céramique, les fours sous vide en molybdène sont essentiels pour produire des céramiques denses de haute qualité aux propriétés uniformes. Ces fours permettent le frittage de céramiques avancées à des températures allant jusqu'à 2400°C, ce qui est crucial pour obtenir les propriétés mécaniques, électriques et thermiques souhaitées. L'environnement sous vide empêche l'oxydation des poudres céramiques, ce qui permet d'obtenir des produits d'une pureté et d'une performance accrues. Les applications comprennent la production de céramiques techniques utilisées dans l'électronique, l'aérospatiale et les appareils médicaux.
Métallurgie
Le secteur de la métallurgie utilise largement les fours à vide au molybdène pour la fusion et le traitement thermique des métaux. Ces fours sont idéaux pour traiter les métaux réfractaires comme le tungstène, le molybdène et le tantale, qui nécessitent des points de fusion élevés et résistent à l'oxydation. La fusion sous vide permet d'éliminer les impuretés volatiles et les gaz, ce qui permet d'obtenir des métaux d'une pureté et de propriétés mécaniques supérieures. En outre, ces fours sont utilisés pour le traitement thermique des aciers à haute résistance, des aciers inoxydables et des aciers à outils afin d'obtenir la dureté, la ténacité et la résistance à l'usure souhaitées.
L'électronique
Dans l'industrie électronique, les fours à vide au molybdène sont utilisés pour la production de dispositifs à semi-conducteurs et de circuits intégrés. Les fours sont utilisés pour des processus tels que le frittage, le recuit et la diffusion, qui nécessitent un contrôle précis de la température et un environnement sans contamination. Les capacités à haute température des fours au molybdène permettent le traitement de matériaux avancés tels que le carbure de silicium et le nitrure de gallium, qui sont essentiels pour les dispositifs électroniques de la prochaine génération.
Traitements de matériaux spéciaux
Les fours à vide au molybdène sont également utilisés pour des traitements de matériaux spécialisés dans diverses industries. Il s'agit notamment des traitements suivants
- Le brasage et la soudure: Les fours à vide offrent un environnement idéal pour les opérations de brasage et de soudure, garantissant des joints de haute qualité avec une oxydation et une porosité minimales. Ces opérations sont particulièrement importantes dans les secteurs de l'aérospatiale et de l'automobile, où la fiabilité et les performances sont essentielles.
- Traitement du combustible nucléaire: Les fours à molybdène sont utilisés pour la fabrication de pastilles de combustible nucléaire, garantissant une pureté et une densité élevées. L'environnement sous vide permet d'éliminer les impuretés et les gaz volatils, ce qui est essentiel pour la sécurité et les performances nucléaires.
- Fusion du verre: Dans l'industrie du verre, les fours à vide en molybdène sont utilisés pour fondre des verres de haute pureté et créer des céramiques techniques. Les températures élevées et l'atmosphère contrôlée permettent de produire des verres spéciaux aux propriétés optiques et mécaniques uniques.
Avantages des fours à vide au molybdène
L'utilisation de fours sous vide au molybdène présente plusieurs avantages, notamment
- Capacités à haute température: Les éléments chauffants en molybdène peuvent supporter des températures allant jusqu'à 2400°C, ce qui les rend adaptés au traitement de matériaux à haute température.
- Atmosphère contrôlée: L'environnement sous vide empêche l'oxydation et la contamination, ce qui garantit des produits de haute qualité aux propriétés constantes.
- Efficacité énergétique: Les fours à vide sont conçus pour être efficaces sur le plan énergétique, ce qui réduit les coûts d'exploitation et l'impact sur l'environnement.
- Polyvalence: Les fours sous vide au molybdène peuvent être configurés pour diverses applications, ce qui en fait un outil polyvalent dans de nombreuses industries.
En conclusion, les fours sous vide au molybdène sont indispensables à l'industrie moderne, car ils permettent de produire des matériaux et des composants de haute qualité avec un contrôle précis et une contamination minimale. Leurs applications couvrent la céramique, la métallurgie, l'électronique et les traitements de matériaux spéciaux, soulignant leur rôle essentiel dans l'avancement des processus technologiques et industriels.
Tendances et innovations futures dans la technologie des fours sous vide au molybdène
Le domaine de la technologie des fours sous vide au molybdène s'apprête à connaître des avancées et des innovations significatives qui amélioreront l'efficacité et élargiront les applications dans diverses industries. La demande de matériaux de haute qualité et de procédés de traitement thermique précis augmentant, le développement de fours sous vide au molybdène avancés devient crucial.
Amélioration de l'efficacité
L'un des principaux objectifs de l'évolution de la technologie des fours sous vide au molybdène est l'amélioration de l'efficacité opérationnelle. Les innovations en matière d'éléments chauffants, de matériaux d'isolation et de systèmes de contrôle devraient permettre de réduire la consommation d'énergie et d'améliorer l'uniformité de la température. Par exemple, l'intégration de matériaux d'isolation avancés tels que les fibres céramiques et l'isolation multicouche peut réduire considérablement les pertes de chaleur, améliorant ainsi l'efficacité énergétique globale du four.
En outre, le développement de systèmes de contrôle intelligents qui utilisent des algorithmes d'intelligence artificielle et d'apprentissage automatique peut optimiser les cycles de chauffage, prévoir les besoins de maintenance et ajuster les paramètres opérationnels en temps réel. Ces systèmes peuvent analyser de grandes quantités de données collectées par des capteurs à l'intérieur du four afin de garantir des performances optimales et des temps d'arrêt minimaux.
Nouvelles applications
La polyvalence des fours à vide au molybdène ouvre de nouvelles voies pour des applications dans des domaines émergents tels que la fabrication additive, les céramiques avancées et le traitement des semi-conducteurs. La capacité à contrôler l'atmosphère et la température avec une grande précision rend ces fours idéaux pour le traitement des matériaux avancés qui nécessitent des conditions environnementales spécifiques.
Dans le domaine de la fabrication additive, les fours à vide au molybdène peuvent être utilisés pour le post-traitement des pièces métalliques, afin de s'assurer qu'elles sont exemptes d'impuretés et qu'elles présentent les propriétés mécaniques souhaitées. De même, dans la production de céramiques avancées, ces fours peuvent faciliter le frittage de formes et de compositions complexes qui ne sont pas possibles avec les méthodes conventionnelles.
Innovations en matière de matériaux
Le développement de nouveaux alliages et composites de molybdène est un autre domaine d'innovation. En incorporant des éléments tels que le titane, le zirconium et les métaux des terres rares, les chercheurs créent des alliages de molybdène dont la résistance à haute température, la résistance à la corrosion et la conductivité thermique sont améliorées. Ces matériaux avancés peuvent étendre la plage de température opérationnelle des éléments chauffants en molybdène et améliorer leur durabilité.
En outre, l'utilisation de la nanotechnologie dans la production d'éléments chauffants en molybdène peut conduire à des améliorations significatives de leurs performances. Les revêtements nanostructurés peuvent améliorer l'émissivité des éléments, ce qui permet un transfert de chaleur plus efficace et une réduction de la consommation d'énergie.
Considérations environnementales
Les réglementations environnementales devenant plus strictes, la conception des fours à vide au molybdène évolue également pour minimiser leur empreinte écologique. Des innovations dans la conception des fours qui réduisent la production de déchets et améliorent les capacités de recyclage sont à l'étude. En outre, la mise au point de fours à haut rendement énergétique, conformes aux normes internationales de consommation d'énergie, devient une priorité pour les fabricants.
Conclusion
L'avenir desfour sous vide au molybdène est prometteur, avec de nombreuses innovations à l'horizon qui permettront d'améliorer l'efficacité et d'étendre les applications. En s'appuyant sur les progrès de la science des matériaux, des systèmes de contrôle et de la durabilité environnementale, l'industrie est prête à répondre à la demande croissante de matériaux de haute qualité et d'ingénierie de précision. À mesure que ces technologies continueront d'évoluer, elles joueront un rôle crucial dans le façonnement de l'avenir de diverses industries, de l'aérospatiale à l'automobile en passant par l'électronique et les soins de santé.
CONTACTEZ-NOUS POUR UNE CONSULTATION GRATUITE
Les produits et services de KINTEK LAB SOLUTION ont été reconnus par des clients du monde entier. Notre personnel se fera un plaisir de répondre à toute demande que vous pourriez avoir. Contactez-nous pour une consultation gratuite et parlez à un spécialiste produit pour trouver la solution la plus adaptée aux besoins de votre application !