Les fours à induction sans noyau, bien qu'ils offrent des avantages tels qu'un contrôle précis de la température, une distribution uniforme de la chaleur et une flexibilité dans les changements d'alliage, présentent des inconvénients notables.Les principaux inconvénients sont un rendement énergétique réduit (environ 75 %) par rapport aux fours à noyau, qui peuvent atteindre un rendement de 98 %.En outre, les changements fréquents d'alliage peuvent accélérer l'usure du revêtement réfractaire, réduisant ainsi sa durée de vie.L'absence d'un noyau concentrateur de flux dans les fours sans noyau contribue également à leur faible efficacité.Ces facteurs font que les fours à induction sans noyau sont moins adaptés aux opérations à haut débit ou aux environnements exigeant une production continue avec un minimum de temps d'arrêt.
Explication des points clés :
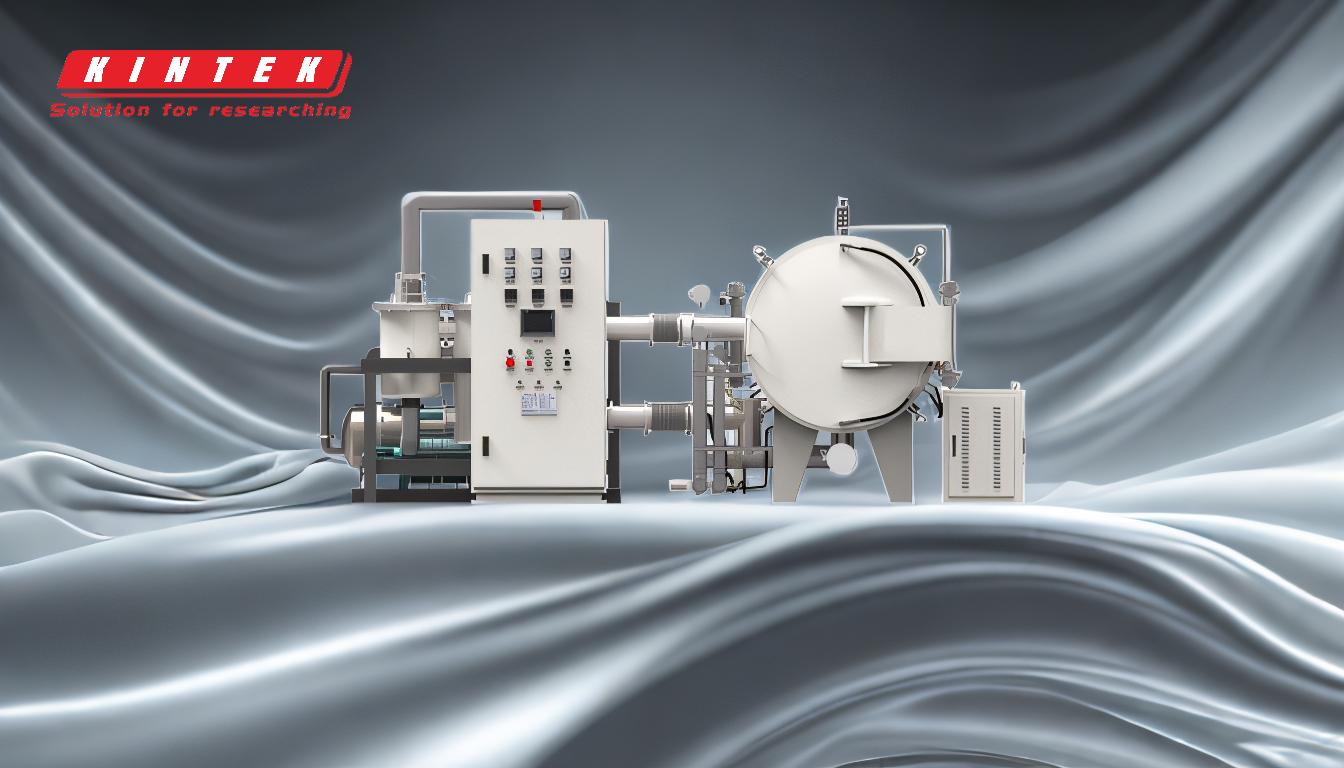
-
Efficacité énergétique réduite
- Les fours à induction sans noyau fonctionnent avec un rendement énergétique d'environ 75 %, ce qui est nettement inférieur aux fours à noyau, qui peuvent atteindre un rendement de 98 %.
- L'absence de noyau concentrateur de flux dans les fours sans noyau entraîne des pertes d'énergie, car le champ magnétique est moins efficacement concentré sur la charge métallique.
- Cette efficacité moindre se traduit par une consommation d'énergie et des coûts d'exploitation plus élevés, ce qui rend les fours sans noyau moins économiques pour les applications à haut rendement ou à forte consommation d'énergie.
-
Usure du revêtement réfractaire
- Les changements fréquents d'alliage, une pratique courante dans les fours sans noyau, peuvent accélérer la dégradation du revêtement réfractaire.
- Le revêtement réfractaire est exposé à des cycles thermiques et à des réactions chimiques avec différents alliages, ce qui entraîne des fissures, une érosion et une réduction de la durée de vie.
- Le remplacement du revêtement réfractaire est coûteux et prend du temps, ce qui augmente les dépenses de maintenance et les temps d'arrêt.
-
Adaptation limitée aux opérations en continu
- Les fours à induction sans noyau sont conçus pour être flexibles, ce qui leur permet d'être arrêtés et démarrés à froid, ce qui est avantageux pour les changements d'alliage.
- Toutefois, cette conception les rend moins adaptés aux opérations continues et à forte production, où le maintien d'un bain de métal en fusion constant est essentiel.
- Les fours à noyau, en revanche, sont mieux adaptés à ces applications en raison de leur efficacité supérieure et de leur capacité à fonctionner en continu.
-
Consommation d'énergie plus élevée
- L'efficacité plus faible des fours sans noyau signifie qu'il faut plus d'énergie pour obtenir les mêmes résultats de fusion que les fours à noyau.
- Cette demande accrue d'énergie peut entraîner une augmentation des coûts d'exploitation, en particulier dans les régions où l'électricité est chère.
- Pour les entreprises qui cherchent à minimiser leurs dépenses énergétiques, les fours sans noyau ne sont peut-être pas l'option la plus rentable.
-
Dépendance à l'égard du système de refroidissement
- Les fours à induction sans noyau s'appuient sur des bobines de cuivre refroidies à l'eau pour éviter la surchauffe pendant le fonctionnement.
- Le système de refroidissement ajoute de la complexité à la conception du four et nécessite un entretien régulier pour garantir son bon fonctionnement.
- Toute défaillance du système de refroidissement peut entraîner l'endommagement des bobines ou l'arrêt du four, ce qui perturbe la production.
-
Limites opérationnelles
- Si les fours sans noyau offrent une certaine souplesse en termes de changement d'alliage et de gamme de fréquences (50 Hz à 10 kHz), ils sont moins efficaces à des fréquences plus basses.
- Les fours à noyaux, plus efficaces, conviennent mieux aux applications nécessitant des performances constantes sur une large gamme de fréquences.
En résumé, si les fours à induction sans noyau offrent un excellent contrôle de la température et de la chimie des métaux, leur rendement énergétique réduit, leur susceptibilité à l'usure du revêtement réfractaire et leur consommation d'énergie plus élevée les rendent moins idéaux pour les opérations à haut débit ou en continu.Ces inconvénients doivent être soigneusement pris en compte lors de la sélection d'un four pour des applications industrielles spécifiques.
Tableau récapitulatif :
Inconvénient | Description |
---|---|
Efficacité énergétique réduite | Le rendement est d'environ 75 % contre 98 % dans les fours à noyau, ce qui se traduit par une consommation d'énergie plus élevée. |
Usure du revêtement réfractaire | Les changements fréquents d'alliage accélèrent la dégradation du revêtement, augmentant les coûts de maintenance et les temps d'arrêt. |
Limité pour une utilisation continue | Moins adapté aux opérations à haut débit ou en continu en raison des limitations de conception. |
Consommation d'énergie plus élevée | Une efficacité moindre augmente les coûts d'exploitation, en particulier dans les régions où l'électricité est chère. |
Dépendance à l'égard du système de refroidissement | Dépend des serpentins refroidis à l'eau, ce qui ajoute à la complexité et aux besoins de maintenance. |
Limites opérationnelles | Moins efficaces à des fréquences plus basses, les fours à noyau sont plus adaptés à des performances constantes. |
Vous avez besoin d'aide pour choisir le bon appareil de chauffage pour vos besoins ? Contactez nos experts dès aujourd'hui !