Le recuit est un processus de traitement thermique utilisé pour modifier les propriétés physiques et mécaniques des métaux, les rendant plus ductiles et moins cassants.Le processus consiste à chauffer le métal à une température spécifique, à le maintenir à cette température pendant une période déterminée, puis à le laisser refroidir lentement.Les principaux éléments nécessaires au recuit sont un dispositif de chauffage (tel qu'un four), un contrôle précis de la température et un environnement de refroidissement contrôlé.Le processus est divisé en trois étapes :La récupération, la recristallisation et la croissance des grains, chacune d'entre elles se produisant à des températures spécifiques.Le recuit peut être effectué sur différents métaux, notamment l'acier, l'aluminium, le laiton et le cuivre, à l'aide d'équipements spécialisés tels que les fours à chambre, les fours à atmosphère et les fours à vide.
Explication des principaux points :
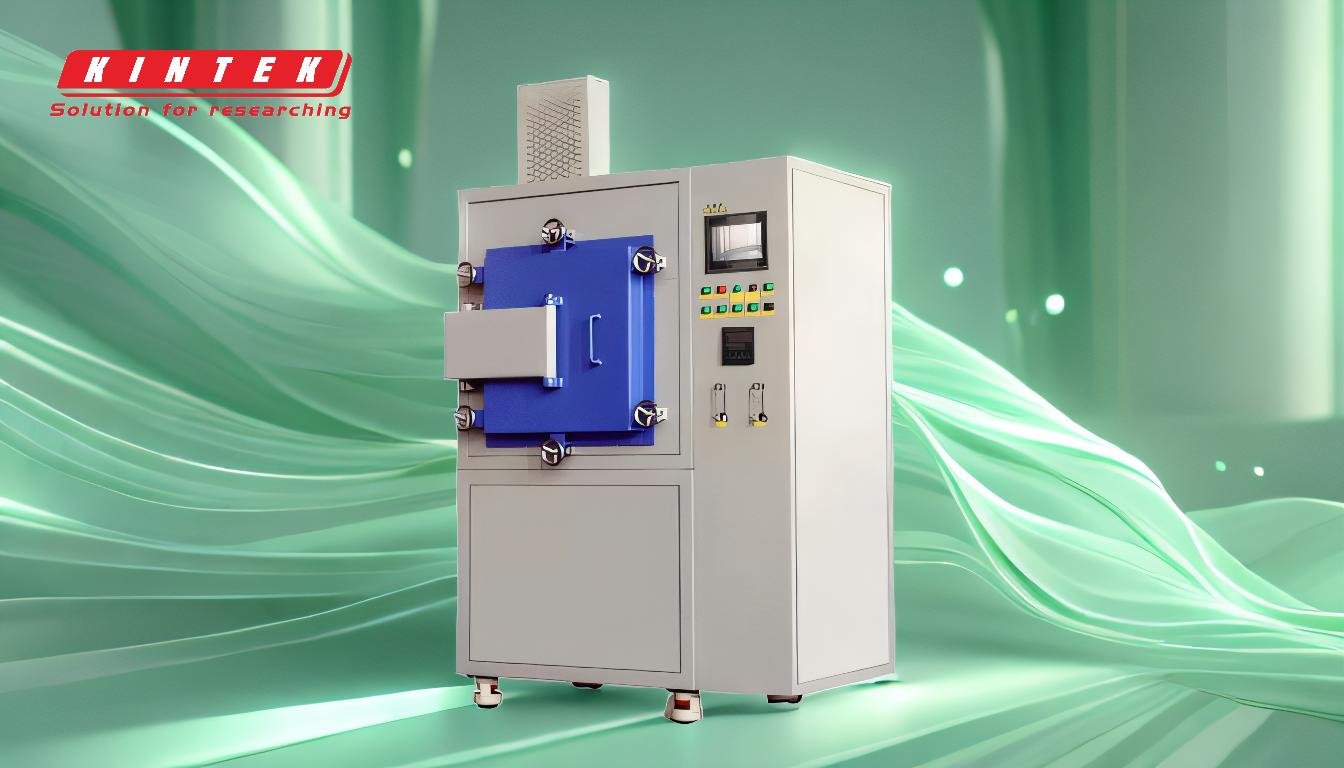
-
Dispositif de chauffage (four):
- Le four est le principal équipement nécessaire au recuit.Il doit être capable d'atteindre et de maintenir des températures élevées, généralement comprises entre 700 °C et 900 °C, bien que certains fours puissent dépasser 1000 °C.
- Le four doit fournir un chauffage uniforme afin que le métal atteigne la température souhaitée dans l'ensemble de sa structure.
- Les types de fours utilisés comprennent les fours à chambre, les fours à atmosphère et les fours à vide, chacun étant adapté à des matériaux et à des exigences de recuit spécifiques.
-
Contrôle de la température:
- Le contrôle précis de la température est essentiel pendant le recuit.Le métal doit être chauffé à une température où sa structure cristalline devient fluide tout en restant solide.
- Cette température varie en fonction du type de métal recuit.Par exemple, l'acier nécessite généralement des températures plus élevées que l'aluminium ou le cuivre.
- Le maintien d'une température correcte garantit que les défauts du matériau peuvent se réparer d'eux-mêmes, ce qui permet d'améliorer les propriétés du matériau.
-
Étapes du recuit:
- Récupération:Au cours de cette étape, le métal est chauffé à une température qui réduit les contraintes internes sans modifier la structure du grain.Cette étape prépare le métal aux phases suivantes.
- Recristallisation:Le métal est chauffé au-dessus de sa température de recristallisation, ce qui permet à de nouveaux grains de se former sans les contraintes préexistantes.Cette étape permet d'obtenir un matériau plus souple et plus ductile.
- Croissance du grain:Si le métal est maintenu trop longtemps à la température de recuit, les grains peuvent grossir, ce qui peut affecter les propriétés mécaniques du matériau.Un refroidissement contrôlé permet d'éviter une croissance excessive des grains.
-
Processus de refroidissement:
- Une fois que le métal a été maintenu à la température de recuit, il doit être refroidi lentement jusqu'à la température ambiante.Un refroidissement rapide peut réintroduire des tensions et annuler les avantages du recuit.
- La vitesse de refroidissement est soigneusement contrôlée pour assurer la formation d'une structure cristalline ductile, qui améliore la maniabilité du métal et réduit sa fragilité.
-
Matériaux adaptés au recuit:
- Si l'acier et l'acier allié sont couramment recuits, d'autres métaux tels que l'aluminium, le laiton et le cuivre bénéficient également de ce processus.
- Chaque métal a une plage de température de recuit et une vitesse de refroidissement spécifiques, qui doivent être respectées pour obtenir des résultats optimaux.
-
Variations de l'équipement:
- Fours à chambre:Ils sont polyvalents et peuvent traiter une large gamme de matériaux et de tailles.Ils conviennent au traitement par lots.
- Fours à atmosphère:Ces fours contrôlent l'environnement autour du métal, empêchant l'oxydation ou d'autres réactions chimiques pendant le recuit.Ils sont idéaux pour les matériaux sensibles aux conditions atmosphériques.
- Fours à vide:Utilisés pour les matériaux de haute pureté ou ceux qui nécessitent un environnement sans oxygène.Les fours à vide sont essentiels pour le recuit des métaux qui réagissent avec l'air à des températures élevées.
-
Applications et avantages:
- Le recuit est utilisé pour améliorer l'usinabilité, la ductilité et la ténacité des métaux.
- Il est couramment appliqué dans des industries telles que l'automobile, l'aérospatiale et la fabrication, où les composants métalliques doivent résister à la contrainte et à la déformation.
- Le processus améliore également la conductivité électrique de métaux tels que le cuivre, ce qui le rend précieux dans les applications électriques et électroniques.
En comprenant ces points clés, un acheteur d'équipement ou de consommables peut prendre des décisions éclairées sur le type de four et de procédé de recuit requis pour des matériaux et des applications spécifiques.
Tableau récapitulatif :
Aspect clé | Détails |
---|---|
Dispositif de chauffage | Four (chambre, atmosphère, vide) capable de chauffer uniformément à 700-1000 °C |
Contrôle de la température | Chauffage précis à des températures de recuit spécifiques au métal |
Étapes du recuit | Récupération, recristallisation, croissance des grains |
Processus de refroidissement | Refroidissement lent jusqu'à la température ambiante pour éviter la réintroduction de contraintes. |
Matériaux | Acier, aluminium, laiton, cuivre |
Variantes d'équipement | Fours à chambre, à atmosphère et à vide pour des besoins spécifiques |
Applications | Industrie automobile, aérospatiale, manufacturière et électrique |
Prêt à optimiser les propriétés de vos métaux grâce au recuit ? Contactez nos experts dès aujourd'hui pour des solutions sur mesure !